Rare earth can effectively improve the toughness of cast steel
As we all know, adding an appropriate amount of rare earth elements to steel materials will have a significant impact on the structure and performance of the material. Usually the rare earth elements in steel are added in 0.05%~0.20%. Because the ratio of the atomic radii of rare earth to iron far exceeds 15%, and the difference in electronegativity between rare earth and iron is very large, these are not conducive to the formation of solid solution, so the solubility of rare earth in steel is very low. Most of the rare earth elements in steel exist in the form of rare earth compounds, mainly rare earth oxides and rare earth sulfides.
Xi’an Aeronautical Vocational and Technical College has carried out research on the effect of adding rare earth elements to cast steel on its structure and performance. They used ZG35CrMnSi cast steel as the test material, and the rare earth additive used was mixed rare earth. Considering that the test material contains a certain amount of sulfur And the loss when adding rare earth elements, the range of rare earth addition is 0.23%~0.38%, this addition refers to the total amount of rare earth added to molten steel during smelting. Compare the structure and performance of the two sets of samples with and without rare earth elements. Steel casting is smelted in an intermediate frequency induction furnace, and the casting is prepared by investment casting. Then the test piece is heated to 900°C+670°C for air cooling, and then heated to 890°C for quenching in oil; then 570~630°C fire.
The comparative test results show that rare earth has little effect on the strength of cast steel, but it has a significant effect on the toughness of cast steel. The impact toughness is increased by 43%, and the elongation rate is increased by 13.3%. Microstructure inspection shows that the tempered sorbite of the cast steel structure without rare earth elements is relatively coarse, and its grain size is about 5; among them, the gray lumps are MnS inclusions, which are not distributed on the entire inspected surface. In general, the morphology of MnS is mostly angular. The sample structure of the cast steel with rare earth elements is uniform and fine tempered sorbite, and the grain size is about 8-9. It shows that the structure of cast steel can be refined after adding rare earth elements.
In addition, after adding rare earth elements, the desulfurization effect of steel is not obvious, but it has a greater influence on the morphology of MnS. When the rare earth elements are not added, the MnS in the steel is in the shape of strips or blocks with edges and corners; after adding the rare earth elements, the sulfide is approximately spherical, and the distribution is relatively dispersed relative to the sample without the rare earth elements, but only in a few places You can see strip or block sulfide inclusions. On the fracture of the sample without rare earth elements, MnS is concentrated and dendritic. The fracture of the MnS inclusion area is mainly intergranular fracture, and intergranular secondary cracks can be seen locally.
In the samples with rare earth elements, the fracture is ductile transgranular fracture. Even in the area where sulfides are concentrated, the matrix metal is still ductile transgranular fracture. Cast steel added with rare earth elements eliminates dendritic sulfides and changes them into spherical or non-angular rods and massive rare earth sulfides, which is beneficial to the improvement of toughness.
Studies have pointed out that the principle of rare earth element refinement may be due to the following reasons:
(1) Sulfides and oxide inclusions formed by adding rare earth elements to steel can become non-spontaneous crystal nuclei of steel, which can refine equiaxed crystals and shorten columnar crystal regions.
(2) The solubility of rare earth elements in the solid phase is very small. Once the molten steel is solidified, the rare earths are enriched in the liquid phase at the front of the growing crystals, preventing the crystals from growing, thus making the grains refined.
(3) Rare earth elements tend to accumulate in the grain boundaries, reduce the interfacial tension of the alloy, and reduce the driving force for grain growth, thereby inhibiting the growth of austenite grains. Correspondingly, the flaky martensite formed by quenching is also smaller. .
Please keep the source and address of this article for reprinting: Rare earth can effectively improve the toughness of cast steel
Minghe Die Casting Company are dedicated to manufacture and provide quality and high performance Casting Parts(metal die casting parts range mainly include Thin-Wall Die Casting,Hot Chamber Die Casting,Cold Chamber Die Casting),Round Service(Die Casting Service,Cnc Machining,Mold Making,Surface Treatment).Any custom Aluminum die casting, magnesium or Zamak/zinc die casting and other castings requirements are welcome to contact us.
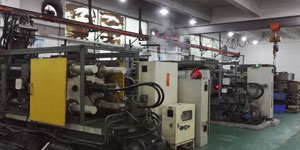
Under the control of ISO9001 and TS 16949,All processes are carried out through hundreds of advanced die casting machines, 5-axis machines, and other facilities, ranging from blasters to Ultra Sonic washing machines.Minghe not only has advanced equipment but also have professional team of experienced engineers,operators and inspectors to make the customer’s design come true.
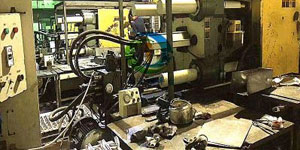
Contract manufacturer of die castings. Capabilities include cold chamber aluminum die casting parts from 0.15 lbs. to 6 lbs., quick change set up, and machining. Value-added services include polishing, vibrating, deburring, shot blasting, painting, plating, coating, assembly, and tooling. Materials worked with include alloys such as 360, 380, 383, and 413.
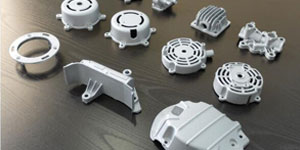
Zinc die casting design assistance/concurrent engineering services. Custom manufacturer of precision zinc die castings. Miniature castings, high pressure die castings, multi-slide mold castings, conventional mold castings, unit die and independent die castings and cavity sealed castings can be manufactured. Castings can be manufactured in lengths and widths up to 24 in. in +/-0.0005 in. tolerance.
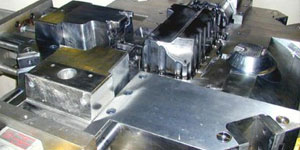
ISO 9001: 2015 certified manufacturer of die cast magnesium, Capabilities include high-pressure magnesium die casting up to 200 ton hot chamber & 3000 ton cold chamber, tooling design, polishing, molding, machining, powder & liquid painting, full QA with CMM capabilities, assembly, packaging & delivery.
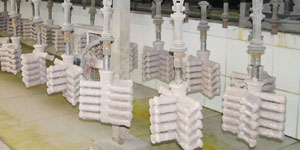
ITAF16949 certified. Additional Casting Service Include investment casting,sand casting,Gravity Casting, Lost Foam Casting,Centrifugal Casting,Vacuum Casting,Permanent Mold Casting,.Capabilities include EDI, engineering assistance, solid modeling and secondary processing.
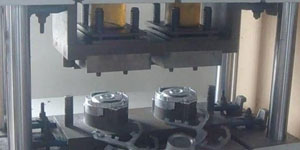
Casting Industries Parts Case Studies for: Cars, Bikes, Aircraft, Musical instruments, Watercraft, Optical devices, Sensors, Models, Electronic devices, Enclosures, Clocks, Machinery, Engines, Furniture, Jewelry, Jigs, Telecom, Lighting, Medical devices, Photographic devices, Robots, Sculptures, Sound equipment, Sporting equipment, Tooling, Toys and more.
What Can we help you do next?
∇ Go To Homepage For Die Casting China
→Casting Parts-Find out what we have done.
→Ralated Tips About Die Casting Services
By Minghe Die Casting Manufacturer |Categories: Helpful Articles |Material Tags: Aluminum Casting, Zinc Casting, Magnesium Casting, Titanium Casting, Stainless Steel Casting, Brass Casting,Bronze Casting,Casting Video,Company History,Aluminum Die Casting |Comments Off