Research on Entrainment Behavior of Aluminum Alloy Castings in Low Pressure Die Casting Process Based on Flow-3D
With the development of automobile lightweight, aluminum alloy castings are more and more widely used in automobiles. Some thin-walled castings used in automobile bodies are mainly high-pressure casting, while some complex-structured castings such as wheel hubs, engine blocks and cylinder heads are mostly formed by low-pressure casting. Low-pressure casting has the characteristics of stable filling, controllable speed, and solidification under pressure to facilitate feeding. However, insufficient attention has been paid to the filling process of low-pressure casting. Recently, some researchers have found that if the pressurization speed in the low pressure casting process is too fast, the filling speed of the molten metal will exceed the critical filling speed value (0.5 m/s), which will cause entrainment and slag entrapment defects, and reduce the casting cost. Mechanical properties. During the filling process of low-pressure casting, the pressurization speed and the structure of the casting will have an impact on the entrainment defects. Therefore, this subject combines numerical simulation and experiment to compare three flat castings with different structures and different pressurization speeds. Research has been carried out to clarify the causes of entrainment defects and provide a reference for the process design of smooth filling of low pressure casting.
Test Method
Mainly investigate the influence of casting structure and pressurization speed on the filling process. Therefore, three simple models with different structures are designed, as shown in Figure 1. The size of the casting is 280 mm×150 mm×30 mm. The center positions of the three flat-plate castings have different heights of the waterfall structure. The drop heights are 0, 15 and 30 mm respectively. The influence of structure on the quality of castings.
Using Flow-3D software, three different models and different filling pressures were simulated. Apply the entrainment model in the software to analyze the entrainment volume during the filling process of different schemes. Save these three models as STL files and import them into Flow-3D. The casting mesh is divided into 5 million. The casting material is ZL101A, the pouring temperature is 700℃, and the alloy viscosity is 0.0019Pa• according to the software's own database. s, the mold material is H13 steel, and the preheating temperature is 250℃. For these three models, input the boosting speeds of 2000, 1200, 600 and 300Pa/s in sequence for simulation
According to the simulation results, the model with the largest and smallest entrainment volume is selected for trial production. The ZL101A is smelted in a gas furnace on site, and Al-10Sr and Al-5Ti-1B master alloys are used for modification and refinement. The parameter design of the process is consistent with the parameter setting of the simulation. In order to ensure the consistency of the aluminum alloy state, this experiment was completed in a crucible. The as-cast mechanical properties of the successfully produced castings are analyzed. 4 M6 tensile samples are taken for each casting. The sampling location is shown in Figure 2. Each model analyzes 6 castings, a total of 24 tensile samples, and the international tensile test is adopted. Standard DIN EN ISO 6892-1. Take samples with the lowest mechanical properties and use SEM for fracture analysis to analyze the root causes of reduced mechanical properties.
Take the V3.1 scheme as an example to observe the distribution of entrainment during the filling process, as shown in Figure 3. It can be seen that when the filling time is 2.9 s, the molten metal rises steadily; when the filling reaches 3.6 s, the molten metal enters the waterfall area, causing severe turbulence and serious entrainment; as the filling process continues The entrainment gas generated in the falling area will be randomly distributed into the casting as the molten metal rises.
The simulation results show the air volume distribution of different models after filling at different pressurization speeds. It can be seen that the air volume of model V1 is less, and the volume of air volume increases slightly as the pressurization speed increases. Regardless of whether the supercharging speed increases or not, the models V2 and V3 have different degrees of entrainment, and the distribution is different.
In order to clarify the impact of the boost speed and the falling structure on the volume of air volume, the volume of air volume of each scheme is quantitatively analyzed, and the volume of air volume of each scheme is derived from Flow-3D, as shown in Figure 5. It can be seen from the quantitative analysis results of the entrainment that when there is no falling structure, the amount of entrainment increases with the increase of the boosting speed; when there is a falling structure, the amount of entrainment does not change significantly with the increase of the boosting speed; the same kind of increase Under pressure speed, increase the height of the falling structure, and the volume of entrainment will increase significantly. Therefore, the falling structure in the casting is the primary factor affecting the volume of entrainment. When there is no falling structure, the pressurization speed will affect the volume of entrainment.
The Actual Castings Analysis Of Mechanical Properties And Dracture
For the V1 model and the V3 model, the same filling pressure speed of 300 Pa/s was used for production trial production. 12 pieces of each model were produced. It can be seen that the casting quality is good and the outline is clear. 6 of them are selected for tensile test bars Processing.
The tensile strength and elongation of the casting can be obtained through the tensile test, as shown in Figure 7. It can be seen that the tensile strength and elongation of castings without falling structure are relatively stable, the average tensile strength is 191MPa, and the average elongation can reach 5.3%; while the tensile strength and elongation of castings with 30 mm falling structure The elongation has some relatively low values. The average tensile strength is 178MPa, and the average elongation is only 3.8%. Select the sample with the tensile strength lower than 160MPa in the falling structure, and perform SEM analysis on the fracture, as shown in Figure 8. It can be seen that there are relatively large entrained scale defects on the surface of the fracture. Combined with the analysis of the simulation results, the main reason is that serious entrainment behavior is produced in the falling structure.
3 Conclusion
- During the filling process of low-pressure casting, the falling structure is the main cause of entrainment, and the volume of entrainment increases with the height of the falling structure.
- If there is a falling structure in the casting, turbulence will be generated, the oxide scale will fold, the formation of entrainment defects, and the mechanical properties of the casting will be greatly reduced.
Please keep the source and address of this article for reprinting:Research on Entrainment Behavior of Aluminum Alloy Castings in Low Pressure Die Casting Process Based on Flow-3D
Minghe Die Casting Company are dedicated to manufacture and provide quality and high performance Casting Parts(metal die casting parts range mainly include Thin-Wall Die Casting,Hot Chamber Die Casting,Cold Chamber Die Casting),Round Service(Die Casting Service,Cnc Machining,Mold Making,Surface Treatment).Any custom Aluminum die casting, magnesium or Zamak/zinc die casting and other castings requirements are welcome to contact us.
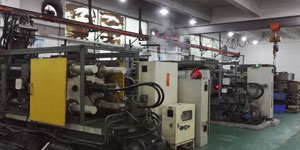
Under the control of ISO9001 and TS 16949,All processes are carried out through hundreds of advanced die casting machines, 5-axis machines, and other facilities, ranging from blasters to Ultra Sonic washing machines.Minghe not only has advanced equipment but also have professional team of experienced engineers,operators and inspectors to make the customer’s design come true.
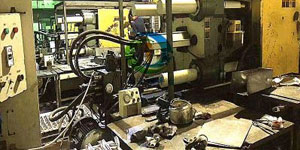
Contract manufacturer of die castings. Capabilities include cold chamber aluminum die casting parts from 0.15 lbs. to 6 lbs., quick change set up, and machining. Value-added services include polishing, vibrating, deburring, shot blasting, painting, plating, coating, assembly, and tooling. Materials worked with include alloys such as 360, 380, 383, and 413.
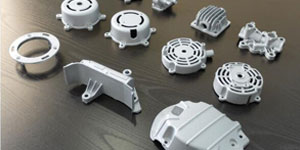
Zinc die casting design assistance/concurrent engineering services. Custom manufacturer of precision zinc die castings. Miniature castings, high pressure die castings, multi-slide mold castings, conventional mold castings, unit die and independent die castings and cavity sealed castings can be manufactured. Castings can be manufactured in lengths and widths up to 24 in. in +/-0.0005 in. tolerance.
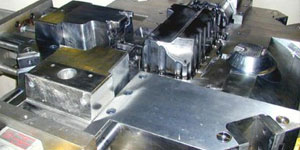
ISO 9001: 2015 certified manufacturer of die cast magnesium, Capabilities include high-pressure magnesium die casting up to 200 ton hot chamber & 3000 ton cold chamber, tooling design, polishing, molding, machining, powder & liquid painting, full QA with CMM capabilities, assembly, packaging & delivery.
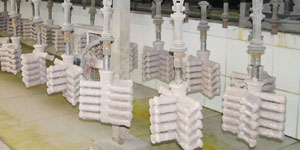
ITAF16949 certified. Additional Casting Service Include investment casting,sand casting,Gravity Casting, Lost Foam Casting,Centrifugal Casting,Vacuum Casting,Permanent Mold Casting,.Capabilities include EDI, engineering assistance, solid modeling and secondary processing.
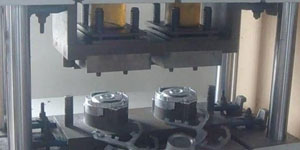
Casting Industries Parts Case Studies for: Cars, Bikes, Aircraft, Musical instruments, Watercraft, Optical devices, Sensors, Models, Electronic devices, Enclosures, Clocks, Machinery, Engines, Furniture, Jewelry, Jigs, Telecom, Lighting, Medical devices, Photographic devices, Robots, Sculptures, Sound equipment, Sporting equipment, Tooling, Toys and more.
What Can we help you do next?
∇ Go To Homepage For Die Casting China
→Casting Parts-Find out what we have done.
→Ralated Tips About Die Casting Services
By Minghe Die Casting Manufacturer |Categories: Helpful Articles |Material Tags: Aluminum Casting, Zinc Casting, Magnesium Casting, Titanium Casting, Stainless Steel Casting, Brass Casting,Bronze Casting,Casting Video,Company History,Aluminum Die Casting |Comments Off