Research On New Forged High Speed Steel Roll Material Quenching Process
Modern large-scale cold strip rolling mills have realized headless and semi-endless rolling. The requirements for the quality of the strips, such as the surface flatness and thickness difference of the cold-rolled strips, are getting higher and higher, and the quality requirements for the work rolls are getting higher and higher. The higher the price, the higher the requirements on the surface hardness and the depth of the hardened layer. The research on the material of cold-rolling work rolls has always been highly valued by the roll industry. From the initial bearing steel, it has gradually developed to 2%Cr, 3%Cr, and 5%Cr steel.
Its development is usually based on the continuous increase of chromium content. In recent years, semi-high-speed steel and high-speed steel roll materials have appeared, and there have been some reports on the study of their structure and carbides. The technicians of Tianjin Heavy Equipment Engineering Research Co., Ltd. studied the quenching process of a newly developed forged high-speed steel cold-rolled work roll material, and analyzed the effects of quenching temperature on the structure, grain size, retained austenite and hardness of the high-speed steel roll. The influence of, provides a theoretical and experimental basis for the development of high-end cold-rolled work rolls.
The new forged high-speed steel roll material used in the test was smelted in a 50kg vacuum induction furnace, and then forged at a high temperature into a 100mm×100mm×250mm blank, which was annealed at 700°C for 4h to obtain the original material for the test. The metallographic sample is a 15mm×15mm×15mm square, which is heated by a box-type resistance furnace at different temperatures and quenched by air cooling. 660RLD/T Rockwell hardness tester was used to detect hardness, X’perPro X-ray diffractometer was used to detect retained austenite, Axiovert200MAT optical microscope was used to detect structure and grain size, and QUANTA400 scanning electron microscope was used to observe carbides.
The as-cast structure of the new forged high-speed steel roll is lower bainite + ledeburite + a small amount of martensite + bar-shaped carbides + granular carbides, of which the large bar-shaped carbides are precipitated during the solidification of molten steel Primary carbides, granular carbides are secondary carbides precipitated from austenite during the cooling process, and the carbide content is 3.6%. research shows:
- The quenching temperature affects the dissolution of carbides. As the quenching temperature increases, the carbide content in the quenched structure of the high-speed steel roll gradually decreases. When the temperature rises to 1200 ℃, the granular carbide has basically dissolved
- Solution, only a small amount of massive carbide remains.
- As the quenching temperature increases, the grains of high-speed steel continue to grow. When the quenching temperature exceeds 1040°C, the grain growth trend is obvious, the quenching temperature exceeds 1160°C, the grain size reaches 4.5, and the grain coarsening is very serious.
- As the quenching temperature increases, the content of retained austenite continues to increase. When the quenching temperature is below 1080°C, the content of retained austenite increases more slowly, and then its content increases sharply. When the quenching temperature reaches 1160℃, the retained austenite content increases to 38%. Therefore, from the perspective of the control of retained austenite content, the quenching temperature should be lower than 1080 ℃.
- When quenching at 1040℃, the hardness reaches the peak value, up to 64.1HRC. At this time, the high-speed steel roll structure, grain size, and retained austenite content match the best.
- The quenching temperature of the new forged high-speed steel roll material should be selected between 1020~1080℃.
Please keep the source and address of this article for reprinting:Research On New Forged High Speed Steel Roll Material Quenching Process
Minghe Die Casting Company are dedicated to manufacture and provide quality and high performance Casting Parts(metal die casting parts range mainly include Thin-Wall Die Casting,Hot Chamber Die Casting,Cold Chamber Die Casting),Round Service(Die Casting Service,Cnc Machining,Mold Making,Surface Treatment).Any custom Aluminum die casting, magnesium or Zamak/zinc die casting and other castings requirements are welcome to contact us.
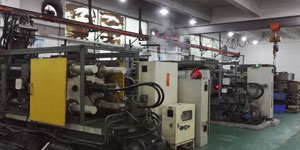
Under the control of ISO9001 and TS 16949,All processes are carried out through hundreds of advanced die casting machines, 5-axis machines, and other facilities, ranging from blasters to Ultra Sonic washing machines.Minghe not only has advanced equipment but also have professional team of experienced engineers,operators and inspectors to make the customer’s design come true.
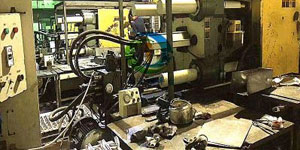
Contract manufacturer of die castings. Capabilities include cold chamber aluminum die casting parts from 0.15 lbs. to 6 lbs., quick change set up, and machining. Value-added services include polishing, vibrating, deburring, shot blasting, painting, plating, coating, assembly, and tooling. Materials worked with include alloys such as 360, 380, 383, and 413.
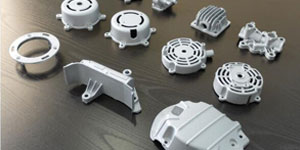
Zinc die casting design assistance/concurrent engineering services. Custom manufacturer of precision zinc die castings. Miniature castings, high pressure die castings, multi-slide mold castings, conventional mold castings, unit die and independent die castings and cavity sealed castings can be manufactured. Castings can be manufactured in lengths and widths up to 24 in. in +/-0.0005 in. tolerance.
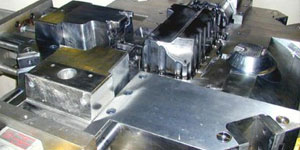
ISO 9001: 2015 certified manufacturer of die cast magnesium, Capabilities include high-pressure magnesium die casting up to 200 ton hot chamber & 3000 ton cold chamber, tooling design, polishing, molding, machining, powder & liquid painting, full QA with CMM capabilities, assembly, packaging & delivery.
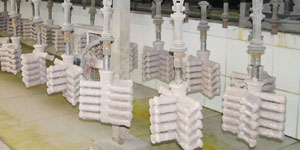
ITAF16949 certified. Additional Casting Service Include investment casting,sand casting,Gravity Casting, Lost Foam Casting,Centrifugal Casting,Vacuum Casting,Permanent Mold Casting,.Capabilities include EDI, engineering assistance, solid modeling and secondary processing.
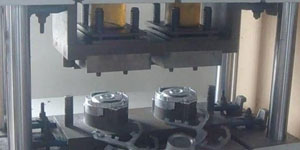
Casting Industries Parts Case Studies for: Cars, Bikes, Aircraft, Musical instruments, Watercraft, Optical devices, Sensors, Models, Electronic devices, Enclosures, Clocks, Machinery, Engines, Furniture, Jewelry, Jigs, Telecom, Lighting, Medical devices, Photographic devices, Robots, Sculptures, Sound equipment, Sporting equipment, Tooling, Toys and more.
What Can we help you do next?
∇ Go To Homepage For Die Casting China
→Casting Parts-Find out what we have done.
→Ralated Tips About Die Casting Services
By Minghe Die Casting Manufacturer |Categories: Helpful Articles |Material Tags: Aluminum Casting, Zinc Casting, Magnesium Casting, Titanium Casting, Stainless Steel Casting, Brass Casting,Bronze Casting,Casting Video,Company History,Aluminum Die Casting |Comments Off