Research Trends In Heat Treatment Of Heat Resistant Alloys And Superalloys
One of the most important issues for the development of 700 ℃ steam temperature A-USC generator sets is the development of heat-resistant alloys for turbine impellers. Some researchers have developed Ni-0.05C-18Cr-13Co-9Mo-1.3Al-1.4Ti-0.1Ta-0.3Nb alloy based on Inconel 617 as the basic material and improved the alloy composition, and trial-produced A large-scale forged impeller sample that simulates the impeller of a real machine. There are research reports on the material properties of different parts of the impeller sample.
Evaluated the casting alternative materials that can be applied to A-USC generator sets with a steam temperature of 700℃. Regarding the Ni-0.04C-26Cr-21Co-1Al-1.9Ti-1.8Nb alloy, trial-produced castings with 3-layer stepped wall thicknesses were made and the materials were evaluated. A research report introduced the influence of segregation on creep strength.
Ni-Fe-based superalloy is expected to be the material of turbine impellers for A-USC thermal power generation. However, in order to ensure the characteristics and manufacturability of turbine impellers, it is important to control trace elements. There are still many unclear points about the influence of trace elements in Ni-Fe-based superalloys parts for turbine impellers. Therefore, some researchers have investigated the influence of trace elements in terms of creep characteristics.
In the process of developing 700℃-class A-USC generator set, in order to apply different material welded impellers composed of Ni-based and Fe-based impellers into practice, the structural stability and mechanical properties of the impeller welded part at high temperature were proposed. Claim. Some researchers have produced a low-alloy steel/Inconel 617 welding material as the interface style of different Fe/Ni materials, and evaluated the effect of thermal aging on the microstructure change of the welding interface.
In order to reduce CO2 emissions, extensive research has been conducted on A-USC equipment. 23Cr-45Ni-7W alloy (ASTM UNS N06674) is a material that improves the creep strength by strengthening the precipitation of M23C6 and Laves phases. It can be used as an alternative material for A-USC's high-temperature steam tubes and boiler tubes. Some researchers evaluated the influence of the alloy's creep characteristics on the Laves phase precipitation behavior.
In order to develop A-USC generator sets with a steam temperature of 700℃, the possibility of using Ni-based heat-resistant alloys as boiler parts was studied, and it was pointed out that alloy 617, which is a precipitation-strengthened alloy, has relaxation in the process of high-temperature use. Cracks (SR cracks) and other related issues. On the other hand, the 23Cr-45Ni-7W alloy (ASME-CC2684), which does not use the phase as the precipitation strengthening phase, has a slightly lower creep rupture strength at 700°C than that of the alloy 617, while the 30Cr-50Ni-W alloy has not been precipitated. It is strengthened, but the creep rupture strength is higher than that of 23Cr-45Ni-7W alloy. Its ductility and SR crack resistance are good. It can be used for A-USC main steam pipe. A research report introduced the four types of structures, mechanical properties and creep characteristics of the plates and trial-produced large-diameter pipes.
At present, the energy problem has become a very important issue. In order to improve the efficiency of thermal power generation as the main power supply means, extensive research and development have been carried out on forged Ni-based alloys. For the stability of the Ni-based superalloy's strengthening phase, the phase structure, not only the precipitation behavior of the phase will have an important effect, but also the morphological change caused by the lattice mismatch between it and the parent phase. Have an important impact. However, the research on these microstructures is mainly the research on the cast Ni-based superalloys with high phase volume ratio, while the research on the cast alloys is very few. Therefore, some research reports have investigated the relationship between the change of the phase structure and the lattice misalignment in the forged Ni-based alloy.
Please keep the source and address of this article for reprinting: Research Trends In Heat Treatment Of Heat Resistant Alloys And Superalloys
Minghe Die Casting Company are dedicated to manufacture and provide quality and high performance Casting Parts(metal die casting parts range mainly include Thin-Wall Die Casting,Hot Chamber Die Casting,Cold Chamber Die Casting),Round Service(Die Casting Service,Cnc Machining,Mold Making,Surface Treatment).Any custom Aluminum die casting, magnesium or Zamak/zinc die casting and other castings requirements are welcome to contact us.
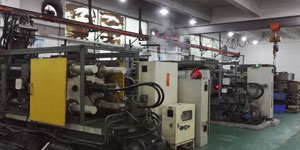
Under the control of ISO9001 and TS 16949,All processes are carried out through hundreds of advanced die casting machines, 5-axis machines, and other facilities, ranging from blasters to Ultra Sonic washing machines.Minghe not only has advanced equipment but also have professional team of experienced engineers,operators and inspectors to make the customer’s design come true.
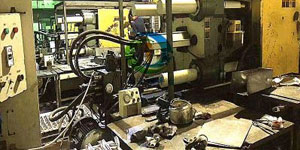
Contract manufacturer of die castings. Capabilities include cold chamber aluminum die casting parts from 0.15 lbs. to 6 lbs., quick change set up, and machining. Value-added services include polishing, vibrating, deburring, shot blasting, painting, plating, coating, assembly, and tooling. Materials worked with include alloys such as 360, 380, 383, and 413.
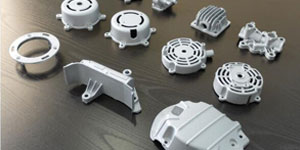
Zinc die casting design assistance/concurrent engineering services. Custom manufacturer of precision zinc die castings. Miniature castings, high pressure die castings, multi-slide mold castings, conventional mold castings, unit die and independent die castings and cavity sealed castings can be manufactured. Castings can be manufactured in lengths and widths up to 24 in. in +/-0.0005 in. tolerance.
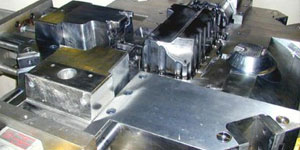
ISO 9001: 2015 certified manufacturer of die cast magnesium, Capabilities include high-pressure magnesium die casting up to 200 ton hot chamber & 3000 ton cold chamber, tooling design, polishing, molding, machining, powder & liquid painting, full QA with CMM capabilities, assembly, packaging & delivery.
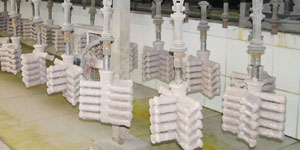
ITAF16949 certified. Additional Casting Service Include investment casting,sand casting,Gravity Casting, Lost Foam Casting,Centrifugal Casting,Vacuum Casting,Permanent Mold Casting,.Capabilities include EDI, engineering assistance, solid modeling and secondary processing.
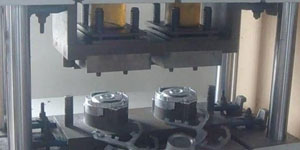
Casting Industries Parts Case Studies for: Cars, Bikes, Aircraft, Musical instruments, Watercraft, Optical devices, Sensors, Models, Electronic devices, Enclosures, Clocks, Machinery, Engines, Furniture, Jewelry, Jigs, Telecom, Lighting, Medical devices, Photographic devices, Robots, Sculptures, Sound equipment, Sporting equipment, Tooling, Toys and more.
What Can we help you do next?
∇ Go To Homepage For Die Casting China
→Casting Parts-Find out what we have done.
→Ralated Tips About Die Casting Services
By Minghe Die Casting Manufacturer |Categories: Helpful Articles |Material Tags: Aluminum Casting, Zinc Casting, Magnesium Casting, Titanium Casting, Stainless Steel Casting, Brass Casting,Bronze Casting,Casting Video,Company History,Aluminum Die Casting |Comments Off