Scientifically Resolve The Steelmaking Capacity Of Intermediate Frequency Furnaces
The original "strip steel" produced by the "small workshop" type intermediate frequency furnace is recognized as a fake and inferior product and should be banned. However, now that some small companies have expanded their furnace capacity and installed continuous casters and rolling mills, "small workshops" have become intermediate frequency furnace steel plants. Should such capacity be removed by administrative means, or should it be dealt with by laws and regulations?
Understanding and Definition of Steel Produced by Intermediate Frequency Furnace
Intermediate frequency furnace steelmaking uses the eddy current of an intermediate frequency magnetic field to melt scrap steel through a continuous casting machine and a continuous rolling mill to produce steel. The products produced by it are no longer the "ground strip steel" of the past. According to investigations by relevant institutions, there are about 70 intermediate frequency furnace steel plants in my country, with a production capacity of about 100 million tons, and the actual output fluctuates greatly. At the beginning of February this year, due to the downturn in the construction steel market, coupled with the decline in the price of imported iron ore, and the reduction in the cost of the blast furnace-converter process, intermediate frequency furnace steel plants lost their competitiveness and almost all stopped production; but by July, as the demand for construction steel increased, Iron ore prices have risen, and the output of intermediate frequency furnace steel plants has risen rapidly, reaching the level of 50 million tons of steel per year. The output of intermediate frequency furnace steel plants is expected to be around 40 million tons this year.
Compared with converter steelmaking and electric furnace steelmaking, the most important difference between intermediate frequency furnace steelmaking and converter and electric furnace steelmaking is that it cannot remove the harmful elements such as phosphorus and sulfur in molten steel, and especially cannot reduce the phosphorus content. The steel produced is very easy to produce. Brittle. This kind of steel can only meet the "strength" requirement, but not the "toughness" requirement. It can only be used for cement blocks for sea reclamation, cement isolation piers for highways, brackets for vegetable greenhouses, etc. It has a limited scope of application and cannot be widely used in the construction field.
Analysis and selection of government administration measures to reduce the production capacity of intermediate frequency furnaces
In accordance with the spirit of comprehensively deepening reforms, the government uses administrative means to remove the steelmaking capacity of intermediate frequency furnaces in accordance with the law, which should mainly be reflected in the treatment in accordance with the standards of environmental protection, energy consumption, and product quality. The author now makes a brief analysis on the feasibility of these aspects:
One is environmental protection. Intermediate frequency furnace steelmaking does not blow oxygen and does not create slag, and emits less smoke and pollutants than converters and electric furnaces. The degree of environmental pollution is relatively light. Therefore, compliance with environmental protection indicators should not be used as a measure to eliminate the production capacity of intermediate frequency furnace steelmaking. mostly according.
The second is energy consumption. Comparing with the consumption indicators of the main production links, converted into energy consumption indicators per ton of steel (kg standard coal/ton of steel): the electricity consumption per ton of steel in the intermediate frequency furnace steelmaking is 600 kWh ~ 700 kWh, equivalent to energy consumption (per kWh Electricity equivalent to 0.404 kilograms of standard coal) is 242 kilograms to 282 kilograms of standard coal. Taking into account the quality of steel and other factors, electric furnace manufacturers generally need to add 700 kg to 800 kg of relatively pure hot molten iron per ton of steel. The electricity consumption per ton of steel is reduced from about 500 kWh to 150 kWh to 200 kWh, which is equivalent to 60 kg of standard coal. ~80 kg; but the molten iron is an energy carrier, calculated based on the energy consumption per ton of iron of 460 kg of standard coal, adding 700 kg to 800 kg of molten iron per ton of steel, equivalent to energy consumption of 322 kg to 368 kg of standard coal, the total energy of the two The consumption is 382 kg ~ 448 kg standard coal, which is higher than that of the intermediate frequency furnace. Therefore, energy consumption should not be used as the main basis for removing the capacity of the intermediate frequency furnace.
The third aspect is quality. Most of my country's construction steel enters the construction field through circulation, and the supply and demand of steel are implemented in accordance with national standards. The national standard covers a wide range, covering the lowest use and lowest grade steel, and has low requirements on the quality and performance of steel, especially the requirements for phosphorus and sulfur content. The upper limit is 0.045%, and it is beneficial to There is no lower limit for the content of manganese, silicon, etc., to improve the performance of steel, that is, according to existing standards, construction steel products can be made without alloys. This is the standard that a general intermediate frequency furnace can reach. However, this kind of steel has poor toughness and is extremely brittle, so it is not suitable for large-scale use in the construction field, and is particularly not suitable for medium- and high-rise building construction and infrastructure.
Therefore, according to the different uses of steel, formulating and improving the quality standards of construction steel, strictly restricting the entry of intermediate frequency furnace steel into the construction field, is the most important legal basis for removing its production capacity.
Opinions and suggestions on controlling the production capacity of intermediate frequency furnaces in accordance with the law
The author believes that in order to strengthen the management and control of the production capacity of intermediate frequency furnace steel plants, which is in the "gray" zone, the policy level should be strengthened from the management of intermediate frequency furnace steelmaking enterprises, refine the quality standards of construction steel, and eliminate Appropriate policy support will be given in terms of rewarding and supplementing the production capacity of intermediate frequency furnaces and strengthening the reorganization of effective assets.
One is to transfer intermediate frequency furnace steelmaking enterprises from "underground" to "above ground" and bring them into the track of legal management. According to the product quality grade and scope of use of intermediate frequency furnace steelmaking enterprises, they can be classified according to the principles of "prohibited use" and "allowed use", and managed by laws and regulations. We predict that based on the steel quality of existing intermediate frequency furnace steelmaking enterprises, most of the intermediate frequency furnace capacity will enter the "prohibited use" ranks; a small number of enterprises that choose high-quality scrap steel may enter the limited low-end market. The author suggests that in the next 5 years, the production capacity of intermediate frequency furnaces should be included in the overall arrangement for capacity reduction, and governments at all levels shall be responsible for implementation, announcement and assessment.
The second is to categorize the quality standards of construction steel according to the purpose. The author suggests that, on the basis of the current quality standards, organize the power to refine the quality standards as regulations for handling the steelmaking capacity of intermediate frequency furnaces. It is possible to consider the content of harmful elements such as phosphorus and sulfur as the main signs and establish standards. For example, the scope of use can be divided into three types:
- Class I: Phosphorus and sulfur content does not exceed 0.045%, used for general facilities for non-human residential use (such as vegetable sheds, stalls, cement blocks for reclamation, etc.) and low-rise buildings in non-seismic areas.
- Class II: Phosphorus and sulfur content does not exceed 0.03%, used for middle and high-rise buildings and general infrastructure.
- Class III: Phosphorus and sulfur content does not exceed 0.02%, used in high-rise buildings and important infrastructure.
The third is about the reward and compensation method. In view of the fact that most of the existing intermediate frequency furnace production capacity is formed under the support and acquiescence of the grassroots government, it is recommended that the local government bear the compensation for removing the intermediate frequency furnace production capacity. Where there are real difficulties, the central government will provide appropriate support.
The fourth is to reorganize effective assets. The author suggests that after removing the capacity of intermediate frequency furnaces, the government encourages companies to reorganize continuous casters, rolling mills and other effective assets with other advantageous companies, and provide policy support in terms of capacity replacement, energy consumption and environmental protection indicator adjustments, and cross-regional tax distribution. .
Please keep the source and address of this article for reprinting: Scientifically Resolve The Steelmaking Capacity Of Intermediate Frequency Furnaces
Minghe Die Casting Company are dedicated to manufacture and provide quality and high performance Casting Parts(metal die casting parts range mainly include Thin-Wall Die Casting,Hot Chamber Die Casting,Cold Chamber Die Casting),Round Service(Die Casting Service,Cnc Machining,Mold Making,Surface Treatment).Any custom Aluminum die casting, magnesium or Zamak/zinc die casting and other castings requirements are welcome to contact us.
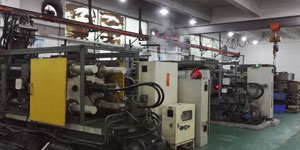
Under the control of ISO9001 and TS 16949,All processes are carried out through hundreds of advanced die casting machines, 5-axis machines, and other facilities, ranging from blasters to Ultra Sonic washing machines.Minghe not only has advanced equipment but also have professional team of experienced engineers,operators and inspectors to make the customer’s design come true.
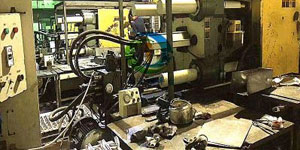
Contract manufacturer of die castings. Capabilities include cold chamber aluminum die casting parts from 0.15 lbs. to 6 lbs., quick change set up, and machining. Value-added services include polishing, vibrating, deburring, shot blasting, painting, plating, coating, assembly, and tooling. Materials worked with include alloys such as 360, 380, 383, and 413.
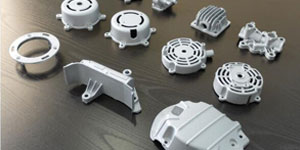
Zinc die casting design assistance/concurrent engineering services. Custom manufacturer of precision zinc die castings. Miniature castings, high pressure die castings, multi-slide mold castings, conventional mold castings, unit die and independent die castings and cavity sealed castings can be manufactured. Castings can be manufactured in lengths and widths up to 24 in. in +/-0.0005 in. tolerance.
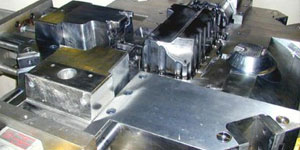
ISO 9001: 2015 certified manufacturer of die cast magnesium, Capabilities include high-pressure magnesium die casting up to 200 ton hot chamber & 3000 ton cold chamber, tooling design, polishing, molding, machining, powder & liquid painting, full QA with CMM capabilities, assembly, packaging & delivery.
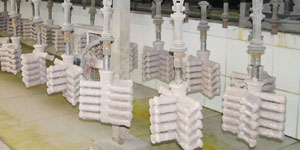
ITAF16949 certified. Additional Casting Service Include investment casting,sand casting,Gravity Casting, Lost Foam Casting,Centrifugal Casting,Vacuum Casting,Permanent Mold Casting,.Capabilities include EDI, engineering assistance, solid modeling and secondary processing.
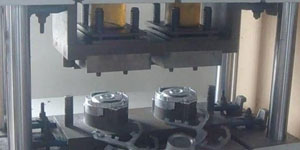
Casting Industries Parts Case Studies for: Cars, Bikes, Aircraft, Musical instruments, Watercraft, Optical devices, Sensors, Models, Electronic devices, Enclosures, Clocks, Machinery, Engines, Furniture, Jewelry, Jigs, Telecom, Lighting, Medical devices, Photographic devices, Robots, Sculptures, Sound equipment, Sporting equipment, Tooling, Toys and more.
What Can we help you do next?
∇ Go To Homepage For Die Casting China
→Casting Parts-Find out what we have done.
→Ralated Tips About Die Casting Services
By Minghe Die Casting Manufacturer |Categories: Helpful Articles |Material Tags: Aluminum Casting, Zinc Casting, Magnesium Casting, Titanium Casting, Stainless Steel Casting, Brass Casting,Bronze Casting,Casting Video,Company History,Aluminum Die Casting |Comments Off