Seven Problems And Solutions Of Surface Casting Defects
Strain
(1) Features:
- The surface of the casting is line-shaped strain along the mold opening direction, with a certain depth, and the entire surface is strained in severe cases;
- The metal liquid adheres to the surface of the mold, resulting in a lack of material on the surface of the casting.
(2) Reasons:
- The surface of the mold cavity is damaged;
- The ejection direction has no slope or the slope is too small;
- The ejection is unbalanced;
- The mold is loose:
- The casting temperature is too high or too low, and the mold temperature is too high to cause the alloy liquid to stick;
- The effect of the release agent is not good:
- The iron content of the aluminum alloy composition is less than 0.8%; the cooling time of the mesh is too long or too short.
(3) Treatment method:
- Repair mold surface damage;
- Correct the slope to improve the surface finish of the mold;
- Adjust the ejector to balance the ejection force;
- Fasten the mold;
- Control the reasonable casting temperature and mold temperature 180-250;
- Replace the release agent:
- Adjust the iron content of aluminum alloy;
- Adjust the cooling time;
- Modify the inner gate and change the direction of the molten aluminum.
Bubbles
(1) Features:
The surface of the casting has a cavity formed under the surface of a rice grain-sized bump.
(2) Cause
- The filling of the alloy liquid in the pressure chamber is too low, it is easy to generate entrainment, and the injection speed is too high;
- The mold exhaust is poor;
- The melt is not degassed, and the melting temperature is too high;
- The mold temperature is too high, and the metal solidification time is not enough , The strength is not enough, and the casting is ejected from the mold prematurely, and the pressurized gas expands;
- Too much release agent;
- The inner gate is poorly opened, and the filling direction is handed over.
(3) Treatment method
- Change the diameter of the small pressure chamber to increase the fullness of molten metal;
- Extend the injection time, reduce the injection speed in the first stage, and change the switching point between low-speed and high-speed injection;
- Reduce the mold temperature to maintain thermal balance;
- Add an exhaust groove, Overflow tank, fully exhaust, timely remove the oil and waste on the exhaust tank_;
- Adjust the smelting process and carry out degassing treatment
- Properly extend the mold retention time:
- Reduce the amount of release agent.
Crack
(1) Features:
- The casting surface has linear or wavy lines, which are narrow and long, and have a development trend under the action of external force;
- The metal in the cold crack is not oxidized;
- The hot crack-the metal in the crack is oxidized .
(2) Reasons:
- The iron content in the alloy is too high or the silicon content is too high;
- The content of harmful impurities in the retort is too high, which reduces the plasticity of the alloy;
- The aluminum-silicon-copper alloy contains too much zinc or the copper content is too low;
- Moulds, especially The overall temperature of the mold cavity is too low;
- Shrinkage is hindered where there are drastic changes in the wall thickness and thinness of the casting, and stress is formed at the sharp corners;
- The mold stays for too long and the stress is large;
- The force is uneven during ejection.
(3) Treatment method:
- Accurately control the alloy composition. In some cases, you can add pure aluminum ingots to the alloy to reduce the magnesium content in the alloy or add aluminum-silicon master alloy to the aluminum alloy to increase the silicon content;
- Change the casting structure, add angles, and change the output Mold inclination to reduce the difference in wall thickness;
- Change or increase the ejection position to make the ejection force uniform;
- Shorten the mold opening and core pulling time to increase the mold temperature and maintain the thermal balance of the mold.
Deformation
(1) Features:
- Overall deformation or partial deformation;
- Die-casting geometry drawings do not match.
(2) Reasons:
- The casting structure is poor;
- The mold is opened too early, and the rigidity of the casting is not enough.
- The ejector rod is set improperly, and the force is uneven during ejection;
- When the gate is too thick, it is easy to deform when the gate is cut off;
- By Partial surface roughness causes high resistance, and the product deforms when ejected; the local temperature of the mold is too high, the product is not completely cured, and the ejection force is large, which causes the product to deform.
(3) Solution:
- Improve the casting structure;
- Reasonably adjust the holding pressure and mold opening date
- Set the ejector position and the number of ejector pins reasonably, preferably 4, in an open place;
- Change the gate position so that the gate has a point, reduce The thickness of the gate is small to ensure the casting quality of the product, so that the product will not be easily deformed when the gate is removed;
- Strengthen the mold surface treatment to reduce the mold release resistance;
- Control the local mold temperature to maintain the mold thermal balance.
Flow Marks, Patterns
(1) Features: There are stripes on the surface of the casting that are consistent with the flow direction of the molten metal. There are obvious non-directional lines that are different from the metal matrix in color, and there is no development trend.
(2) Reasons:
- The molten metal that first enters the cavity forms a very thin and incomplete metal layer, which is made up by the later molten metal and left traces;
- The mold temperature is too low and the mold temperature is uneven:
- Inside The sprue cross-sectional area is too small and improperly positioned to cause splashing;
- The pressure acting on the molten metal is insufficient;
- The pattern: the amount of paint is too much.
(3) Treatment method:
- Increase the temperature of the molten metal by 620%~650C;
- Increase the mold temperature to maintain
- 200~C-250"(2 heat balance;
- Thicken the cross-sectional area of the inner runner to change the inlet position;
- Adjust the filling speed and injection time stroke length;
- Select the appropriate paint and adjust the contrast concentration.
Cold Barrier
(1) Features
The surface of the die-casting has obvious, irregular, and sinking linear lines (both penetrating and non-penetrating). The shape is small and narrow, and some of the junction edges are smooth, which can be developed under the action of external force.
(2) Reasons:
- The two metal streams are connected to each other, but they are not completely fused and there are no inclusions in between. The bonding force of the two metals is very weak;
- The pouring temperature or the temperature of the die-casting mold is too low;
- The alloy is improperly selected and the fluidity is poor;
- The runner position is incorrect Or the flow path is too long;
- The filling speed is low, and the injection pressure is low.
(3) Treatment method:
- Appropriately increase the pouring temperature and mold temperature;
- Increase the injection pressure and shorten the filling time;
- Increase the injection speed and increase the cross-sectional area of the gate;
- Improve the exhaust and filling conditions;
- Select the alloy correctly and increase the alloy fluidity.
Colors, Spots
(1) Features:
Different colors and spots appear on the surface of the casting.
(2) Reasons:
- Unsuitable eye cross agent in the casting, the amount of four decoupling agent is too much, the amount of stone in the production falls into the special parts table.
- Regular solidification containing graphite causes the molten metal temperature to be too high Low leads to no
(3) Treatment method:
- Replace high-quality chess remover;
- Strictly spray amount and spray operation;
- Control mold temperature and maintain thermal balance;
- Control molten metal temperature.
Reticulated Wing
(1) Features: There is a net shape on the surface of the die-casting parts, which continuously expands and extends. Just like the evolution of the bump gauge, the die-casting frequency box
(2) Reasons:
- The surface of the die-casting mold cavity is cracked.
- The material of the die-casting mold is improper or the heat treatment process is incorrect.
- The temperature difference of the die-casting mold varies greatly; Rough.
(3) Treatment method:
- The correct selection of die-casting molds and hot spots, especially high-field alloys,
- The preheating of the mold is more divided into the heat treatment process, the four-shot injection temperature is not straight and too high, and is more sufficient,
- The mold 5 is manufactured at a low temperature after being manufactured.
- The reason for the poor fluidity;
- The alloy liquid absorbs gas and oxidizes the inclusions, and the iron content is high, which makes its quality poor and reduces the fluidity;
- The pouring temperature is low or the mold temperature is low;
- The filling condition is poor;
- The specific pressure is too low;
- Too much gas is involved, the back pressure of the cavity becomes high, and the filling is blocked;
- Poor operation, excessive spraying of paint, paint accumulation, and the gas can not volatilize.
(3) Treatment method:
- D Improve the quality of alloy liquid;
- Increase the pouring temperature or mold temperature;
- Increase the specific pressure, filling speed, degree;
- Improve the metal liquid diversion method of the pouring system, add overflow grooves and exhaust grooves in the under-casting parts;
- Check whether the capacity of the die-casting machine is sufficient.
Burr Flash
(1) Feature: Metal flakes appear on the edge of the parting surface of the die casting.
(2) Reasons:
- Insufficient clamping;
- The injection speed is too high, resulting in too high pressure shock peak;
- he debris on the parting surface is not cleaned;
- The mold strength is not enough to cause deformation;
- Insert and slider wear and parting uneven.
(3) Treatment method:
- Check the clamping force and pressurization, adjust the die-casting process parameters;
- clean the cavity and parting surface;
- repair the mold;
- It is best to use a closed injection end time control system, which can achieve no Flash die casting...
Please keep the source and address of this article for reprinting:Seven Problems And Solutions Of Surface Casting Defects
Minghe Die Casting Company are dedicated to manufacture and provide quality and high performance Casting Parts(metal die casting parts range mainly include Thin-Wall Die Casting,Hot Chamber Die Casting,Cold Chamber Die Casting),Round Service(Die Casting Service,Cnc Machining,Mold Making,Surface Treatment).Any custom Aluminum die casting, magnesium or Zamak/zinc die casting and other castings requirements are welcome to contact us.
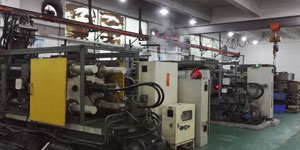
Under the control of ISO9001 and TS 16949,All processes are carried out through hundreds of advanced die casting machines, 5-axis machines, and other facilities, ranging from blasters to Ultra Sonic washing machines.Minghe not only has advanced equipment but also have professional team of experienced engineers,operators and inspectors to make the customer’s design come true.
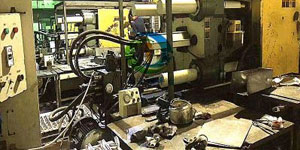
Contract manufacturer of die castings. Capabilities include cold chamber aluminum die casting parts from 0.15 lbs. to 6 lbs., quick change set up, and machining. Value-added services include polishing, vibrating, deburring, shot blasting, painting, plating, coating, assembly, and tooling. Materials worked with include alloys such as 360, 380, 383, and 413.
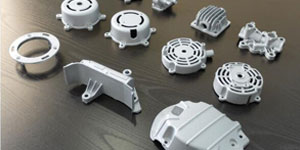
Zinc die casting design assistance/concurrent engineering services. Custom manufacturer of precision zinc die castings. Miniature castings, high pressure die castings, multi-slide mold castings, conventional mold castings, unit die and independent die castings and cavity sealed castings can be manufactured. Castings can be manufactured in lengths and widths up to 24 in. in +/-0.0005 in. tolerance.
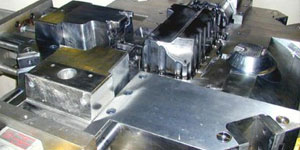
ISO 9001: 2015 certified manufacturer of die cast magnesium, Capabilities include high-pressure magnesium die casting up to 200 ton hot chamber & 3000 ton cold chamber, tooling design, polishing, molding, machining, powder & liquid painting, full QA with CMM capabilities, assembly, packaging & delivery.
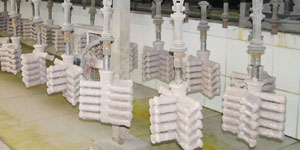
ITAF16949 certified. Additional Casting Service Include investment casting,sand casting,Gravity Casting, Lost Foam Casting,Centrifugal Casting,Vacuum Casting,Permanent Mold Casting,.Capabilities include EDI, engineering assistance, solid modeling and secondary processing.
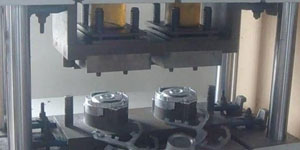
Casting Industries Parts Case Studies for: Cars, Bikes, Aircraft, Musical instruments, Watercraft, Optical devices, Sensors, Models, Electronic devices, Enclosures, Clocks, Machinery, Engines, Furniture, Jewelry, Jigs, Telecom, Lighting, Medical devices, Photographic devices, Robots, Sculptures, Sound equipment, Sporting equipment, Tooling, Toys and more.
What Can we help you do next?
∇ Go To Homepage For Die Casting China
→Casting Parts-Find out what we have done.
→Ralated Tips About Die Casting Services
By Minghe Die Casting Manufacturer |Categories: Helpful Articles |Material Tags: Aluminum Casting, Zinc Casting, Magnesium Casting, Titanium Casting, Stainless Steel Casting, Brass Casting,Bronze Casting,Casting Video,Company History,Aluminum Die Casting |Comments Off