Shell Body Die Casting Process Design
According to the structural characteristics of the shell, the die-casting process is designed. Through the numerical simulation of the two gating systems using ProCAST software, the locations and causes of shrinkage cavities and porosity were analyzed, and a better gating system was selected to optimize the die-casting process through comparison. The results show that after process optimization, the castings have no shrinkage holes or porosity defects, and have been verified by production, which meets the technical requirements
Die casting is a kind of casting technology m with a high degree of automation and capable of mass production of parts with complex shapes. The castings produced by it have the advantages of good compactness, high precision, less machining allowance, and excellent mechanical properties. It is used in automobiles and machinery. 1wl has been widely used in equipment and other fields. The casing shell is an important carrier for the installation of auto parts. Its wall thickness is relatively thin, but its mechanical properties, precision, and air tightness are required to be high, and mass production is required. Therefore, pressure casting is the best shell for manufacturing. s Choice.
This paper analyzes the structure of the casting, designs the casting system of the casting, and simulates it with PmCAST software. Through the analysis of the simulation results, the process is optimized to eliminate the defects such as shrinkage and porosity, so as to obtain A die-casting process that meets the technical requirements of the shell.
The casting under study is a casing for auto parts produced by a certain company. Its three-dimensional modeling diagram is shown in Figure I. The dark area is the machining surface of the casting, the machining allowance is 0.5 mm, and the outline size of the casting It is 103 mm x 98 mm x 89 mm, the casting volume is 234 108 mn r', the mass is 632 g, the thickest wall is 5.5 mm, the thinnest wall is 2.5 mm, and the average wall thickness is 3 mm. The casting material is Al-Si-Cu alloy YL113 with good fluidity, good air tightness, and high wear resistance. Its alloy composition is shown in Table lw. Castings are required to have a smooth surface, the draft angle should not exceed 1.5°, the casting shrinkage rate is 0.6%, and there should be no internal defects such as shrinkage holes and porosity.
In the mold design, the die casting process is the most important, which directly affects the quality of the casting, the production and Cnc machining cost, and the difficulty of mold manufacturing. The die casting process includes the selection of parting surface, the design of the gating system, the design of the overflow and exhaust system
- The shape of the casing is relatively complicated, and a core pulling mechanism is required. Therefore, it is difficult to manufacture the mold. Therefore, the casting adopts a one-mould-one-cavity casting method. According to the most basic principle of parting surface selection, select the largest area of the casting projected area. There are two parting surface setting methods for this casting. As shown in Figure 2, using parting surface a, only one core-pulling mechanism is required, but the casting has a deeper cavity and a larger core tightening force, and the casting is not easy to fall out; Secondly, the casting wall is thin, and it is not easy to install an ejection mechanism. With parting surface b, the casting needs to be equipped with multiple core pulling mechanisms, and the mold manufacturing is complicated, but the casting is basically symmetrical up and down, and the casting is filled smoothly. Secondly, it is convenient to set up the ejection mechanism, which is beneficial to the setting of the overflow groove and the exhaust groove, and is more effective To meet the requirements of die casting process, S text castings select parting surface b.
- The inner gate can be divided into: flat inner gate, end face side gate, center inner gate, annular inner gate, etc. 16]. The shell belongs to the cylindrical type. In order to avoid the direct impact of the molten metal on the core and the occurrence of adhesion, the two gating systems adopt the annular inner gate tangential feeding, that is, an annular runner is set on the side of the casting, and the molten metal is filled After the annular runner enters the cavity, the molten metal can get roughly the same speed on the annular circumference, so that the molten metal fills smoothly and the gas in the cavity is easily discharged. Secondly, it is also possible to install a push rod on the inner gate to avoid the traces of the push rod on the casting.
- The runner is the transition channel for the molten metal from the sprue to the inner gate. For different die castings, the runner has different structures, and for the cylindrical castings, the arc-contracted structure is adopted. In order to prevent the negative pressure when the molten metal flows, the cross-sectional area of the runner should be gradually reduced
- The sprue is the primary channel for the molten metal to enter the cavity from the die casting machine. Its size is related to the diameter of the pressure chamber of the die casting machine. In this study, the diameter of the pressure chamber is 60 mm, the thickness of the remaining material is set to 10 mm, and the draft angle is 10 °.
- Import the 3D modeling into the simulation software ProCAST for grid division, set the casting grid unit size to 2 mm, and the mold grid unit size to 10 mm
- In order to make the casting uniformly solidify at the wall thickness, this study set up a cooling water channel directly below the shrinkage porosity and shrinkage cavity area of the casting, and set two overflow grooves at the place where the shrinkage porosity and shrinkage cavity area are concentrated to make it fully Eliminate gas and inclusions, transfer shrinkage positions, and the optimized process plan is shown in Figure 10. After optimization, the process parameters set the heat transfer coefficient of the cold zone water channel and the mold to 2 000/ (• K ), and other parameters remain unchanged
- According to the structure of the shell, two gating systems for castings are designed, and the ProCAST software is used to perform numerical simulation on them. The results show that the castings have shrinkage holes and shrinkage defects at the wall thickness; the inner gate is set at a farther wall thickness. There are fewer shrinkage holes and shrinkage defects in the place. The analysis found that the reason for the shrinkage cavity and porosity of the casting is that the casting is unevenly solidified at the wall thickness, and part of the area is isolated and cannot be fed.
Through process optimization, the castings are made free of shrinkage holes and porosity defects, and the optimized process is used for production verification. Through inspections, it is found that there are no shrinkage holes and shrinkage porosity defects inside the castings, and meet the technical requirements, which can be used to guide similar castings die-casting process design.
Please keep the source and address of this article for reprinting: Shell Body Die Casting Process Design
Minghe Die Casting Company are dedicated to manufacture and provide quality and high performance Casting Parts(metal die casting parts range mainly include Thin-Wall Die Casting,Hot Chamber Die Casting,Cold Chamber Die Casting),Round Service(Die Casting Service,Cnc Machining,Mold Making,Surface Treatment).Any custom Aluminum die casting, magnesium or Zamak/zinc die casting and other castings requirements are welcome to contact us.
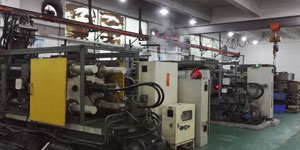
Under the control of ISO9001 and TS 16949,All processes are carried out through hundreds of advanced die casting machines, 5-axis machines, and other facilities, ranging from blasters to Ultra Sonic washing machines.Minghe not only has advanced equipment but also have professional team of experienced engineers,operators and inspectors to make the customer’s design come true.
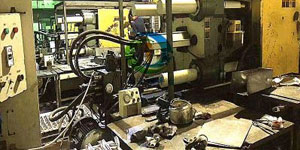
Contract manufacturer of die castings. Capabilities include cold chamber aluminum die casting parts from 0.15 lbs. to 6 lbs., quick change set up, and machining. Value-added services include polishing, vibrating, deburring, shot blasting, painting, plating, coating, assembly, and tooling. Materials worked with include alloys such as 360, 380, 383, and 413.
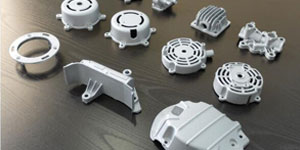
Zinc die casting design assistance/concurrent engineering services. Custom manufacturer of precision zinc die castings. Miniature castings, high pressure die castings, multi-slide mold castings, conventional mold castings, unit die and independent die castings and cavity sealed castings can be manufactured. Castings can be manufactured in lengths and widths up to 24 in. in +/-0.0005 in. tolerance.
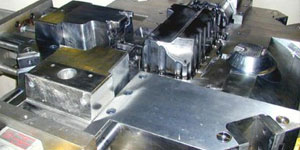
ISO 9001: 2015 certified manufacturer of die cast magnesium, Capabilities include high-pressure magnesium die casting up to 200 ton hot chamber & 3000 ton cold chamber, tooling design, polishing, molding, machining, powder & liquid painting, full QA with CMM capabilities, assembly, packaging & delivery.
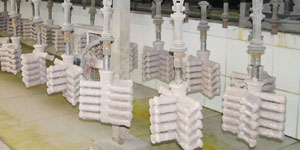
ITAF16949 certified. Additional Casting Service Include investment casting,sand casting,Gravity Casting, Lost Foam Casting,Centrifugal Casting,Vacuum Casting,Permanent Mold Casting,.Capabilities include EDI, engineering assistance, solid modeling and secondary processing.
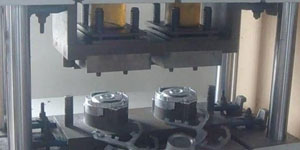
Casting Industries Parts Case Studies for: Cars, Bikes, Aircraft, Musical instruments, Watercraft, Optical devices, Sensors, Models, Electronic devices, Enclosures, Clocks, Machinery, Engines, Furniture, Jewelry, Jigs, Telecom, Lighting, Medical devices, Photographic devices, Robots, Sculptures, Sound equipment, Sporting equipment, Tooling, Toys and more.
What Can we help you do next?
∇ Go To Homepage For Die Casting China
→Casting Parts-Find out what we have done.
→Ralated Tips About Die Casting Services
By Minghe Die Casting Manufacturer |Categories: Helpful Articles |Material Tags: Aluminum Casting, Zinc Casting, Magnesium Casting, Titanium Casting, Stainless Steel Casting, Brass Casting,Bronze Casting,Casting Video,Company History,Aluminum Die Casting |Comments Off