Strengthening Theory Of AlSi10MgMn Die Casting Alloy
In our country, die casting began in the middle and late 1940s. After the 1990s, technological progress and the rapid development of domestic automobile, communications, electronics, and real estate industries have provided a steady stream of development momentum for my country's die-casting industry, and it has rapidly grown into an emerging industry. The annual output of die castings in my country rose rapidly from 266,000 tons to 870,000 tons in just ten years from 1995 to 2005, with an average annual growth rate of up to 20%, and aluminum alloy die castings accounted for more than 3/4 of all die casting output. Especially after entering the 21st century, the leapfrogging of the automotive industry
Development has become the main driving force for the development of the die-casting industry at this stage. However, the increasingly serious environmental problems brought about by the popularization of automobiles have also attracted people's attention. According to reports, automobiles emit more than 4 billion tons of carbon dioxide into the atmosphere each year, accounting for a quarter of the total global carbon dioxide emissions, and with the increase in car ownership, it is increasing year by year. At the same time, vehicle fuel consumption is also an important part of global fuel consumption.
A large number of tests have proved that the lightweight of automobiles is an important means of energy saving and emission reduction. The literature,pointed out that for every 1kg of aluminum added to the automobile, approximately 19kg of carbon dioxide can be reduced during the life cycle of the automobile, and the weight of the automobile can be reduced by 10%. It can reduce energy consumption by 5% to 7%, and fuel consumption can be reduced by 0.7L/100km. The lightweight requirements of automobiles require the use of high-strength materials on the one hand and lightweight materials on the other. Aluminum alloy is a lightweight material with a density of only 1/3 of that of steel.
The use of aluminum alloy can achieve significant weight reduction. For example, the weight reduction effect of typical aluminum parts can reach 30%-40% at the first time, and the second weight reduction effect can even reach 50%. Therefore, the amount of aluminum used in automobiles is increasing year by year. In 2006, the average amount of aluminum used in cars in Europe, America and Japan It has reached 127Kg/vehicle, and it is predicted that before 2015, the average aluminum consumption of European cars can reach 300 Kg/vehicle. Therefore, under the pressure of environmental protection and energy saving, the trend of replacing steel with aluminum is more obvious. Aluminum alloy die-casting parts for automobiles have been used in automobile engine cylinder blocks, automobile wheels, automobile chassis suspension systems and other parts. With the development and application of new die-casting technologies and new die-casting alloys, die-casting parts will be more and more widely used in the production of automobiles in the future.
However, when traditional high-pressure casting is casting parts such as automobile clutch housings, gearboxes, engine blocks, suspension system parts of car chassis, etc., due to the high pressure and high speed in the injection process, it is easy to cause entrainment during the forming process. Defects such as pores are formed inside the casting, which reduces the effective load area and the density of the casting, and cannot meet the high tensile strength, high yield strength, high elongation and other high mechanical performance index requirements of such parts. For such high-mechanical load parts or structural parts, researchers have developed vacuum die-casting technology on the basis of traditional pressure casting (that is, the gas in the mold cavity is extracted before die-casting, and the molten metal fills the mold under a certain vacuum.
Mold cavity, the casting solidifies into a dense casting under pressure), oxygen-filled die-casting (that is, oxygen is filled into the mold cavity instead of air before die-casting. When the metal liquid is filled, part of the oxygen filled in overflows, and the rest is mixed with the metal melt. Reaction occurs and 2 forms fine dispersed solid particles, which stay inside the casting), semi-solid die casting (that is, the metal melt is stirred when the liquid solidifies, and at a certain cooling rate, about 50% or even Slurry with a higher solid phase component, and then die-casting technology with the slurry ), extrusion die-casting technology and so on. Among them, high vacuum die casting not only has the advantages of high material utilization rate, good surface quality, and high production efficiency of traditional die casting, but also adopts means such as vacuuming inside the mold cavity, which is easy to realize, greatly reduces the porosity inside the casting, and can meet the high requirements. High-vacuum die-casting has gained considerable application and development in industrial production due to the requirements of performance castings . Die-casting AlSi10MgMn alloy is Al-Si-Mg-Mn series high-strength, heat-treatable cast aluminum alloy with good air tightness and fluidity. Die-casting parts have high density and strength, strong corrosion resistance, and excellent The cutting processing and welding performance of the product has a wide range of applications in the production of thin-walled, complex-structured, and high-load products, such as transmission casings, cylinder blocks, pulleys, cover plates, automobile chassis parts, cylinder head valves, etc. Ship and aircraft parts.
High-vacuum die-casting AlSi10MgMn alloy castings have low gas content, no bubbling occurs on the surface of the casting during high temperature heat treatment, and the size of the casting will not undergo macroscopic deformation. During the heat treatment process, strengthening phases such as Mg 2 Si can be precipitated, and at the same time, eutectic during solution treatment The morphology of silicon will also be granulated and spheroidized, which can improve the mechanical properties of the casting, especially the elongation. At the same time, this subject has extremely strict requirements on the high vacuum die casting process, because
The basis of high-temperature and long-term heat treatment of castings is to ensure that the gas content of the castings is 1-3ml/100g, so this subject is a research project that integrates high-vacuum die-casting process, die-casting alloy and die-casting heat treatment. The strengthening theory and industrial production have important guiding significance.
Please keep the source and address of this article for reprinting:Strengthening Theory Of AlSi10MgMn Die Casting Alloy
Minghe Die Casting Company are dedicated to manufacture and provide quality and high performance Casting Parts(metal die casting parts range mainly include Thin-Wall Die Casting,Hot Chamber Die Casting,Cold Chamber Die Casting),Round Service(Die Casting Service,Cnc Machining,Mold Making,Surface Treatment).Any custom Aluminum die casting, magnesium or Zamak/zinc die casting and other castings requirements are welcome to contact us.
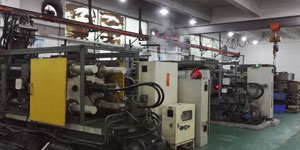
Under the control of ISO9001 and TS 16949,All processes are carried out through hundreds of advanced die casting machines, 5-axis machines, and other facilities, ranging from blasters to Ultra Sonic washing machines.Minghe not only has advanced equipment but also have professional team of experienced engineers,operators and inspectors to make the customer’s design come true.
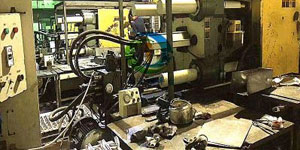
Contract manufacturer of die castings. Capabilities include cold chamber aluminum die casting parts from 0.15 lbs. to 6 lbs., quick change set up, and machining. Value-added services include polishing, vibrating, deburring, shot blasting, painting, plating, coating, assembly, and tooling. Materials worked with include alloys such as 360, 380, 383, and 413.
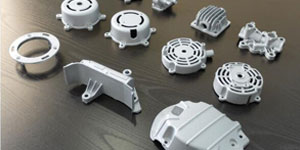
Zinc die casting design assistance/concurrent engineering services. Custom manufacturer of precision zinc die castings. Miniature castings, high pressure die castings, multi-slide mold castings, conventional mold castings, unit die and independent die castings and cavity sealed castings can be manufactured. Castings can be manufactured in lengths and widths up to 24 in. in +/-0.0005 in. tolerance.
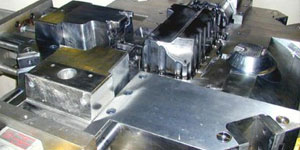
ISO 9001: 2015 certified manufacturer of die cast magnesium, Capabilities include high-pressure magnesium die casting up to 200 ton hot chamber & 3000 ton cold chamber, tooling design, polishing, molding, machining, powder & liquid painting, full QA with CMM capabilities, assembly, packaging & delivery.
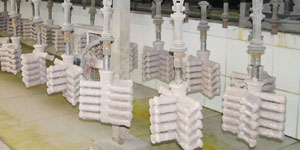
ITAF16949 certified. Additional Casting Service Include investment casting,sand casting,Gravity Casting, Lost Foam Casting,Centrifugal Casting,Vacuum Casting,Permanent Mold Casting,.Capabilities include EDI, engineering assistance, solid modeling and secondary processing.
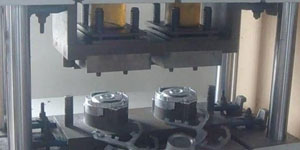
Casting Industries Parts Case Studies for: Cars, Bikes, Aircraft, Musical instruments, Watercraft, Optical devices, Sensors, Models, Electronic devices, Enclosures, Clocks, Machinery, Engines, Furniture, Jewelry, Jigs, Telecom, Lighting, Medical devices, Photographic devices, Robots, Sculptures, Sound equipment, Sporting equipment, Tooling, Toys and more.
What Can we help you do next?
∇ Go To Homepage For Die Casting China
→Casting Parts-Find out what we have done.
→Ralated Tips About Die Casting Services
By Minghe Die Casting Manufacturer |Categories: Helpful Articles |Material Tags: Aluminum Casting, Zinc Casting, Magnesium Casting, Titanium Casting, Stainless Steel Casting, Brass Casting,Bronze Casting,Casting Video,Company History,Aluminum Die Casting |Comments Off