The Advantages And Disadvantages Of Free Forging And Die Forging Methods
Free forging
Free forging refers to the processing method of forgings that use simple general-purpose tools or directly apply external force to the blank between the upper and lower anvils of the forging equipment to deform the blank to obtain the required geometric shape and internal quality. The forgings produced by the free forging method are called free forgings.
Free forging mainly produces small batches of forgings. Forging equipment such as forging hammers and hydraulic presses are used to form the blanks to obtain qualified forgings. The basic procedures of free forging include upsetting, drawing, punching, cutting, bending, twisting, shifting and forging. Free forging adopts hot forging method.
The free forging process includes basic processes, auxiliary processes, and finishing processes.
- The basic processes of free forging: upsetting, drawing, punching, bending, cutting, twisting, shifting and forging, etc. The most commonly used in actual production are the three processes of upsetting, drawing and punching.
- Auxiliary process: pre-deformation process, such as pressing jaws, pressing steel ingot edges, cutting shoulders, etc.
- Finishing process: the process of reducing the surface defects of the forging, such as removing the uneven surface of the forging and shaping.
The advantages of free forging: large forging flexibility, small parts less than 100kg can be produced, and heavy parts up to 300t or more can be produced; the tools used are simple general tools; forging forming is to gradually deform the blank in different regions, therefore, forging Similarly, the tonnage of forging equipment required for forgings is much smaller than that of model forging; the accuracy requirements for equipment are low; and the production cycle is short.
Disadvantages and limitations of free forging: production efficiency is much lower than model forging; forgings have simple shapes, low dimensional accuracy, and rough surfaces; workers have high labor intensity and require high technical levels; it is not easy to achieve mechanization and automation.
Die forging
Die forging refers to a forging method that uses a mold to form a blank on a dedicated die forging equipment to obtain a forging. The forgings produced by this method have precise dimensions, small machining allowances, and complex structures and productivity.
According to the different equipment used: hammer die forging, crank press die forging, flat forging machine die forging and friction press die forging, etc.
The most commonly used equipment for hammer die forging is steam-air die forging hammer, non-anvil hammer and high-speed hammer.It can be divided into two categories: die forging die cavity and blank making die cavity according to their different functions.
1) Forging die bore.
- Pre-forging die bore. The function of the pre-forging die cavity is to deform the blank to be close to the shape and size of the forging, so that during the final forging, the metal can easily fill the die cavity to obtain the required size of the forging. For forgings with simple shapes or when the batch is not large, the pre-forging die cavity may not be provided. The fillet and slope of the pre-forging die cavity are much larger than those of the final forging die cavity, and there is no flash groove.
- Final forging die bore. The function of the final forging die cavity is to finally deform the blank to the required shape and size of the forging. Therefore, its shape should be the same as that of the forging; but because the forging will shrink when it is cooled, the size of the final forging die cavity should be larger than that of the forging. The size is enlarged by a shrinkage amount. The shrinkage of steel forgings is taken as 1.5%. In addition, there are flash grooves along the periphery of the mold cavity to increase the resistance of metal flowing out of the mold cavity, to promote the metal to fill the mold cavity, and at the same time to accommodate excess metal.
2) Blank making mold cavity.
For forgings with complex shapes, in order to make the shape of the blank basically conform to the shape of the forging, so that the metal can be distributed reasonably and fill the cavity well, it is necessary to preform the blank in the blanking cavity.
- Drawing a long mold bore. It is used to reduce the cross-sectional area of a certain part of the blank to increase the length of the part. The drawing bore is divided into two types: open type and closed type.
- Rolling die cavity. It is used to reduce the cross-sectional area of one part of the blank to increase the cross-sectional area of another part, so that the metal is distributed according to the shape of the forging. The rolling cavity is divided into two types: open type and closed type.
- Bending the mold cavity. For bent rod die forgings, a bending die cavity is required to bend the blank.
- Cut off the cavity. It forms a pair of knife edges on the corners of the upper mold and the lower mold to cut the metal.
The advantages of die forging: higher production efficiency. When die forging, the deformation of the metal is carried out in the die cavity, so the required shape can be obtained quickly; it can forge complex forgings, and can make the metal streamline distribution more reasonable, and improve the service life of the parts; the size of the die forgings More accurate, better surface quality, smaller machining allowance; save metal materials and reduce the workload of cutting processing. Under the condition of sufficient quantity, the cost of parts can be reduced.
Disadvantages and limitations of die forging: the weight of die forgings is limited by the capacity of general die forging equipment, mostly below 7OKg; the manufacturing cycle of forging dies is long and the cost is high; the investment cost of die forging equipment is larger than that of free forging.
Please keep the source and address of this article for reprinting: The Advantages And Disadvantages Of Free Forging And Die Forging Methods
Minghe Die Casting Company are dedicated to manufacture and provide quality and high performance Casting Parts(metal die casting parts range mainly include Thin-Wall Die Casting,Hot Chamber Die Casting,Cold Chamber Die Casting),Round Service(Die Casting Service,Cnc Machining,Mold Making,Surface Treatment).Any custom Aluminum die casting, magnesium or Zamak/zinc die casting and other castings requirements are welcome to contact us.
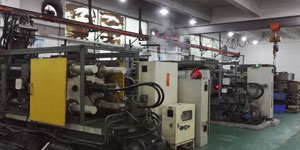
Under the control of ISO9001 and TS 16949,All processes are carried out through hundreds of advanced die casting machines, 5-axis machines, and other facilities, ranging from blasters to Ultra Sonic washing machines.Minghe not only has advanced equipment but also have professional team of experienced engineers,operators and inspectors to make the customer’s design come true.
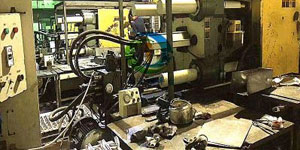
Contract manufacturer of die castings. Capabilities include cold chamber aluminum die casting parts from 0.15 lbs. to 6 lbs., quick change set up, and machining. Value-added services include polishing, vibrating, deburring, shot blasting, painting, plating, coating, assembly, and tooling. Materials worked with include alloys such as 360, 380, 383, and 413.
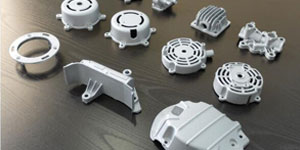
Zinc die casting design assistance/concurrent engineering services. Custom manufacturer of precision zinc die castings. Miniature castings, high pressure die castings, multi-slide mold castings, conventional mold castings, unit die and independent die castings and cavity sealed castings can be manufactured. Castings can be manufactured in lengths and widths up to 24 in. in +/-0.0005 in. tolerance.
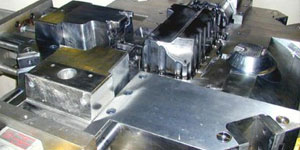
ISO 9001: 2015 certified manufacturer of die cast magnesium, Capabilities include high-pressure magnesium die casting up to 200 ton hot chamber & 3000 ton cold chamber, tooling design, polishing, molding, machining, powder & liquid painting, full QA with CMM capabilities, assembly, packaging & delivery.
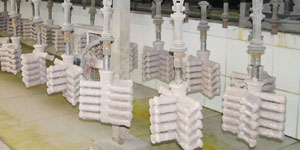
ITAF16949 certified. Additional Casting Service Include investment casting,sand casting,Gravity Casting, Lost Foam Casting,Centrifugal Casting,Vacuum Casting,Permanent Mold Casting,.Capabilities include EDI, engineering assistance, solid modeling and secondary processing.
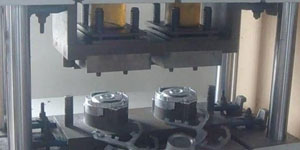
Casting Industries Parts Case Studies for: Cars, Bikes, Aircraft, Musical instruments, Watercraft, Optical devices, Sensors, Models, Electronic devices, Enclosures, Clocks, Machinery, Engines, Furniture, Jewelry, Jigs, Telecom, Lighting, Medical devices, Photographic devices, Robots, Sculptures, Sound equipment, Sporting equipment, Tooling, Toys and more.
What Can we help you do next?
∇ Go To Homepage For Die Casting China
→Casting Parts-Find out what we have done.
→Ralated Tips About Die Casting Services
By Minghe Die Casting Manufacturer |Categories: Helpful Articles |Material Tags: Aluminum Casting, Zinc Casting, Magnesium Casting, Titanium Casting, Stainless Steel Casting, Brass Casting,Bronze Casting,Casting Video,Company History,Aluminum Die Casting |Comments Off