The Advantages And Disadvantages Of Hot Chamber Die Casting Machine
The Advantages Of Hot Chamber Die Casting Machine
Compared with other casting methods, die casting has the following three advantages:
1. Dimensional accuracy, surface accuracy, thin wall
The dimensional accuracy of castings is high, generally equivalent to 6~7, even up to 4; the surface finish is good, generally equivalent to 5~8; the strength and hardness are higher, and the strength is generally 25~30% higher than sand casting, but it is extended The rate is reduced by about 70%; the size is stable, and the interchangeability is good; it can die-cast thin-walled complex castings. For example, the current minimum wall thickness of zinc alloy die castings can reach 0.3 mm; aluminum alloy castings can reach 0.5 mm; the minimum casting aperture is 0.7 mm; and the minimum pitch is 0.75 mm.
2. Mass production
The machine has high productivity and can be multi-cavity in one mold. For example, the domestic JⅢ3 horizontal cold-air die-casting machine can die-cast 600-700 times in an average of eight hours, and the small hot-chamber die-casting machine can die-cast 3000-7000 times in an average of eight hours. , A pair of die-casting molds, die-casting alloys, life can reach hundreds of thousands of times, even millions of times; easy to achieve mechanization and automation.
3. Economic benefits
Due to the precise dimensions of the die-casting parts, the surface is smooth and clean. Generally, it is used directly without mechanical processing, or the processing volume is small, so it not only improves the metal utilization rate, but also reduces a large number of processing equipment and man-hours; the price of castings is easy; it can be combined die-casting with other metal or non-metal materials . It saves not only assembly man-hours but also metal.
4. Surface treatment
Easy to do various surface treatments, such as electroplating, spraying, etc.
Disadvantages of hot chamber die casting machine:
- Due to the high speed of liquid metal filling the cavity during die-casting, the fluid state is unstable, so the general die-casting method is used, and the casting is prone to pores and cannot be heat treated.
- Die-casting is more difficult for castings with complex recesses.
- High melting point alloys (such as copper, ferrous metals), die-casting molds have a lower life.
- It is not suitable for small batch production. The main reasons are the high manufacturing cost of die-casting molds, the high production efficiency of die-casting machines and the uneconomical production of small batches.
- Materials are limited: The current die-casting alloys only have six types of zinc, tin, lead, copper, magnesium, and aluminum, among which copper alloys have the highest melting point.
Please keep the source and address of this article for reprinting: The Advantages And Disadvantages Of Hot Chamber Die Casting Machine
Minghe Die Casting Company are dedicated to manufacture and provide quality and high performance Casting Parts(metal die casting parts range mainly include Thin-Wall Die Casting,Hot Chamber Die Casting,Cold Chamber Die Casting),Round Service(Die Casting Service,Cnc Machining,Mold Making,Surface Treatment).Any custom Aluminum die casting, magnesium or Zamak/zinc die casting and other castings requirements are welcome to contact us.
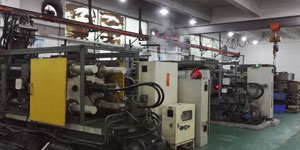
Under the control of ISO9001 and TS 16949,All processes are carried out through hundreds of advanced die casting machines, 5-axis machines, and other facilities, ranging from blasters to Ultra Sonic washing machines.Minghe not only has advanced equipment but also have professional team of experienced engineers,operators and inspectors to make the customer’s design come true.
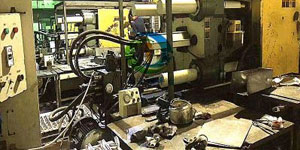
Contract manufacturer of die castings. Capabilities include cold chamber aluminum die casting parts from 0.15 lbs. to 6 lbs., quick change set up, and machining. Value-added services include polishing, vibrating, deburring, shot blasting, painting, plating, coating, assembly, and tooling. Materials worked with include alloys such as 360, 380, 383, and 413.
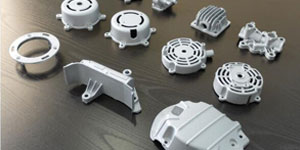
Zinc die casting design assistance/concurrent engineering services. Custom manufacturer of precision zinc die castings. Miniature castings, high pressure die castings, multi-slide mold castings, conventional mold castings, unit die and independent die castings and cavity sealed castings can be manufactured. Castings can be manufactured in lengths and widths up to 24 in. in +/-0.0005 in. tolerance.
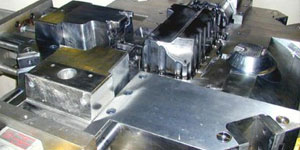
ISO 9001: 2015 certified manufacturer of die cast magnesium, Capabilities include high-pressure magnesium die casting up to 200 ton hot chamber & 3000 ton cold chamber, tooling design, polishing, molding, machining, powder & liquid painting, full QA with CMM capabilities, assembly, packaging & delivery.
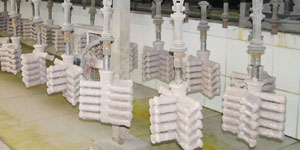
ITAF16949 certified. Additional Casting Service Include investment casting,sand casting,Gravity Casting, Lost Foam Casting,Centrifugal Casting,Vacuum Casting,Permanent Mold Casting,.Capabilities include EDI, engineering assistance, solid modeling and secondary processing.
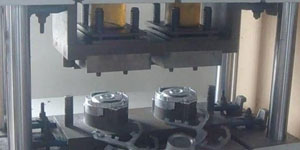
Casting Industries Parts Case Studies for: Cars, Bikes, Aircraft, Musical instruments, Watercraft, Optical devices, Sensors, Models, Electronic devices, Enclosures, Clocks, Machinery, Engines, Furniture, Jewelry, Jigs, Telecom, Lighting, Medical devices, Photographic devices, Robots, Sculptures, Sound equipment, Sporting equipment, Tooling, Toys and more.
What Can we help you do next?
∇ Go To Homepage For Die Casting China
→Casting Parts-Find out what we have done.
→Ralated Tips About Die Casting Services
By Minghe Die Casting Manufacturer |Categories: Helpful Articles |Material Tags: Aluminum Casting, Zinc Casting, Magnesium Casting, Titanium Casting, Stainless Steel Casting, Brass Casting,Bronze Casting,Casting Video,Company History,Aluminum Die Casting |Comments Off