The Advantages Of Precision Investment Casting
The biggest advantage of precision casting is that because investment castings have high dimensional accuracy and surface finish, it can reduce machining work, just leave a little machining allowance on the parts with higher requirements, even some castings Only the grinding and polishing allowance is left, and it can be used without mechanical processing. It can be seen that the use of investment precision casting methods can save a lot of machine tool equipment and processing man-hours, and greatly save metal raw materials.
Another advantage of the investment casting method is that it can precision cast complex castings of various alloys, especially high-temperature alloy castings. For example, the blade of a jet engine, its streamlined profile and cooling cavity, can hardly be formed by machining technology. Production with investment precision casting technology can not only achieve mass production, ensure the consistency of castings, but also avoid the stress concentration of residual knife marks after machining. Now known as investment casting, it is a precision casting process with little or no cutting. It is an excellent process technology in the precision casting industry and has a wide range of applications. It is not only suitable for precision casting of various types and alloys, but also the dimensional accuracy and surface quality of the produced castings are higher than other precision casting methods, and even other precision casting methods are difficult to cast, high temperature resistance, and difficult to process. All castings can be cast by investment casting.
Investment casting is developed on the basis of ancient wax casting. As an ancient civilization, China is one of the earliest countries to use this technology. As far back as hundreds of BC, the ancient working people of our country created this lost wax precision casting technology for precision casting with various fine patterns. Products such as clocks and dings and utensils with writing, such as the tomb of Zenghou Yi in the Spring and Autumn Period. The base of the tomb of Zenghou Yi is composed of multiple dragons intertwined with each other. They are connected end to end and staggered up and down to form a multi-layer moire pattern hollowed out in the middle. These patterns are difficult to produce by ordinary precision casting techniques, but the lost wax method is used. The precision casting process can take advantage of the fact that paraffin wax has no strength and is easy to engrave. You can use ordinary tools to engrave the same paraffin craftwork as the tomb of Zenghou Yi tomb, and then add a pouring system, coating, dewaxing, Pouring, you can get the exquisite tomb plate of Zenghou Yi.
The practical application of modern investment casting methods in industrial production was in the 1940s. The development of aviation jet engines at that time required the manufacture of heat-resistant alloy parts such as blades, impellers, nozzles, etc., with complex shapes, accurate dimensions, and smooth surfaces. Because heat-resistant alloy materials are difficult to machine and the shapes of parts are so complex that they cannot or are difficult to manufacture by other methods, it is necessary to find a new precision molding process. With the improvement of craftsmanship, modern investment casting methods have gained important development on the basis of ancient craftsmanship. Therefore, the development of the aviation industry has promoted the application of investment casting, and the continuous improvement and perfection of investment casting has also created favorable conditions for the aviation industry to further improve its performance.
Our country began to apply investment precision casting to industrial production in the 1950s and 1960s. Since then, this advanced precision casting process has been greatly developed, and it has been widely used in aviation, automobiles, machine tools, ships, internal combustion engines, gas turbines, telecommunications equipment, weapons, medical equipment, and cutting tools. Manufacturing of arts and crafts.
The so-called investment casting process is simply to use fusible materials (such as wax or plastic) to make a fusible model (referred to as investment or model), apply several layers of special refractory coatings on it, and dry and After being hardened to form an integral shell, use steam or hot water to melt the model from the shell, then place the shell in the sand box, fill with dry sand around it, and finally put the mold in the roasting furnace. High-temperature firing (if a high-strength mold is used, the mold shell after demolding can be directly fired without modeling). After the mold or mold is fired, molten metal is poured into it to obtain a casting.
The dimensional accuracy of investment castings is relatively high, generally up to CT4-6 (CT10~13 for sand precision casting and CT5~7 for die casting). Of course, due to the complex process of investment casting, there are many factors that affect the dimensional accuracy of castings. For example, the shrinkage of the mold material, the deformation of the investment mold, the linear change of the shell during the heating and cooling process, the shrinkage of the alloy and the deformation of the casting during the solidification process, etc., so the dimensional accuracy of ordinary investment castings is relatively high, However, its consistency still needs to be improved (the size consistency of castings using medium and high temperature waxes should be improved a lot).
When pressing the investment mold, the pressure type with high surface smoothness of the cavity is used, so the surface smoothness of the investment mold is also relatively high. In addition, the shell is made of a refractory coating made of a special high-temperature resistant adhesive and refractory material, which is coated on the investment mold, and the inner surface of the cavity that is in direct contact with the molten metal has a high smoothness. Therefore, the surface finish of investment castings is higher than that of general precision castings, generally reaching Ra.1.6~3.2μm.
Please keep the source and address of this article for reprinting:The Advantages Of Precision Investment Casting
Minghe Die Casting Company are dedicated to manufacture and provide quality and high performance Casting Parts(metal die casting parts range mainly include Thin-Wall Die Casting,Hot Chamber Die Casting,Cold Chamber Die Casting),Round Service(Die Casting Service,Cnc Machining,Mold Making,Surface Treatment).Any custom Aluminum die casting, magnesium or Zamak/zinc die casting and other castings requirements are welcome to contact us.
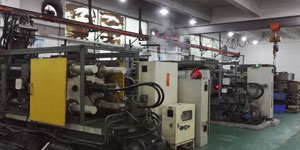
Under the control of ISO9001 and TS 16949,All processes are carried out through hundreds of advanced die casting machines, 5-axis machines, and other facilities, ranging from blasters to Ultra Sonic washing machines.Minghe not only has advanced equipment but also have professional team of experienced engineers,operators and inspectors to make the customer’s design come true.
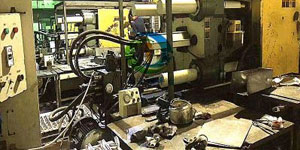
Contract manufacturer of die castings. Capabilities include cold chamber aluminum die casting parts from 0.15 lbs. to 6 lbs., quick change set up, and machining. Value-added services include polishing, vibrating, deburring, shot blasting, painting, plating, coating, assembly, and tooling. Materials worked with include alloys such as 360, 380, 383, and 413.
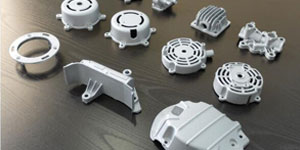
Zinc die casting design assistance/concurrent engineering services. Custom manufacturer of precision zinc die castings. Miniature castings, high pressure die castings, multi-slide mold castings, conventional mold castings, unit die and independent die castings and cavity sealed castings can be manufactured. Castings can be manufactured in lengths and widths up to 24 in. in +/-0.0005 in. tolerance.
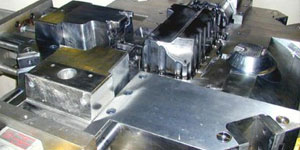
ISO 9001: 2015 certified manufacturer of die cast magnesium, Capabilities include high-pressure magnesium die casting up to 200 ton hot chamber & 3000 ton cold chamber, tooling design, polishing, molding, machining, powder & liquid painting, full QA with CMM capabilities, assembly, packaging & delivery.
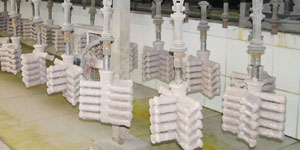
ITAF16949 certified. Additional Casting Service Include investment casting,sand casting,Gravity Casting, Lost Foam Casting,Centrifugal Casting,Vacuum Casting,Permanent Mold Casting,.Capabilities include EDI, engineering assistance, solid modeling and secondary processing.
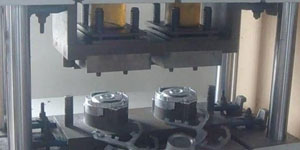
Casting Industries Parts Case Studies for: Cars, Bikes, Aircraft, Musical instruments, Watercraft, Optical devices, Sensors, Models, Electronic devices, Enclosures, Clocks, Machinery, Engines, Furniture, Jewelry, Jigs, Telecom, Lighting, Medical devices, Photographic devices, Robots, Sculptures, Sound equipment, Sporting equipment, Tooling, Toys and more.
What Can we help you do next?
∇ Go To Homepage For Die Casting China
→Casting Parts-Find out what we have done.
→Ralated Tips About Die Casting Services
By Minghe Die Casting Manufacturer |Categories: Helpful Articles |Material Tags: Aluminum Casting, Zinc Casting, Magnesium Casting, Titanium Casting, Stainless Steel Casting, Brass Casting,Bronze Casting,Casting Video,Company History,Aluminum Die Casting |Comments Off