The Analysis of Aluminum Alloy Die Casting Key Technology
Overview Of Aluminum Alloy Shell Castings
Aluminum alloy shell castings are commonly used in the modern automobile industry. Due to their irregular shapes, it is difficult for some structures to meet the quality standards through mechanical processing. Therefore, some aluminum castings are only used for the rough surface structure of automobile shells. From the perspective of the safety of automobile use, the industry has very strict quality requirements for aluminum castings. All castings have strict standards for material strength. In the requirements for shell castings, surface, Double standards for internal quality. In order to ensure product quality, some manufacturers have adopted optical flaw detection technology to control the entire production process.
Mechanical Behavior | Grade |
Tensile strength Mpa(min) | 240 |
Yield strength Mpa(min) | 140 |
Elongation %(min) | <1 |
Brinell hardness HB(min) | 80 |
The aluminum alloy shell cover introduced in this article has a relatively simple structure and only two parts need to be machined. However, due to the irregular shape of the shell, the heights of the two bosses are different. Among them, the maximum outer diameter, height, The main wall thickness sections are 105mm, 40mm and 3.5mm respectively. The parts that need to be machined are the outer diameter surfaces of the large and small shells. The machining tolerances must be controlled within +/-0.1mm. Since this part does not need to process the inner cavity, the difficulty of die casting is relatively small.
In order to ensure that the performance of the casting can meet the requirements of withstanding the static crushing force above 20kN, the production process needs to be controlled in accordance with GB6414-86 CT6 to ensure that the casting is free of impurities and cracks during the die-casting process, and welding is not allowed. Repair the product by repairing or dipping.
Product Process Analysis
2.1 Production process
The production process of parts is: incoming material → melting/die casting → trimming/cleaning → machining → cleaning → assembly.
2.2 Defect analysis
Although the aluminum alloy shell casting introduced in this article has a simple structure, the following production defects often occur during the production process:
- (1) Variegation: The temperature difference between the metal and the mold, the filling speed during smelting, and the size of the spray amount during the shot peening process are not well controlled, which easily causes the color of the casting to become dark and black.
- (2) Porosity defects: This type of problem can hardly be completely avoided in the production process of aluminum alloy castings. The control requirement for the porosity problem of the casting is to ensure the overall strength of the shell, and it is necessary to ensure that the critical area does not produce porosity that exceeds the ASTME505 level 2 standard. The acceptable diameter range of the pores in the casting is ≤∉1.6mm, the pore rate should be controlled within 6.2%, and the diameter of the pores on the machined surface should not be greater than 2.0mm.
In terms of production quality control, visual inspection is mainly responsible for the inspection of castings' appearance defects, and X-ray inspection is responsible for the control of the internal quality of castings. However, in mass production, from the perspective of accelerating production speed and controlling production costs, these two methods have certain defects. Therefore, the aluminum alloy die-casting process is analyzed and referenced with CAE and other auxiliary technologies in order to improve the inherent quality of the castings. Problem control is handled in the rough stage.
2.3 Process parameters and equipment selection
According to the structural characteristics and production requirements of the casting, the casting pressure is set at 350T. According to the production experience of similar products in the past, such as unreasonable mold combination and improper selection of process parameters, the problem of excessive liquid metal filling speed will occur during the die casting process. , Resulting in the obstruction of gas discharge in the cavity, and eventually forming quality defects such as pores or excessive oxide impurities in the finished product, which affects the pass rate of the casting.
According to the design requirements of the casting, the thickness of the dense surface layer of the thin-walled shell casting is only 0.8mm. If it is processed properly, the center structure will be loose, which will lead to the reduction of shell performance and pressure resistance. Therefore, when designing the mold, the positioning pin is used to coordinate the positioning, and the processing volume is controlled within 0.5mm. This saves machining time and is more conducive to the improvement of the inherent quality of the casting.
2.3.1 Selection of mold program
According to the design requirements of the aluminum alloy shell casting, virtual design was carried out using AnyCast-ing software, and three different inlet design schemes were obtained. Through comparison, the flow channel with smoother flow filling was finally determined. Design plan C is to produce molds, and it is found in actual production that this plan has a better effect on improving the internal defects of the shell castings and increasing the yield of the shell.
2.3.2 Setting of melting temperature
Combined with the structural weight of the casting shell, a 350T cold press chamber die-casting machine is used for the die-casting of the castings, and the temperature is set within the range of 640℃+/-20℃. In order to ensure the pressure of the metal liquid filling process is stable, try to avoid Turbulent flow, splashing and other problems caused by secondary oxidation slag entrainment or erosion of the core, the pressure rise rate is set to 1.3kPa/s.
2.3.3 Purification of alloy liquid
In order to enhance the quality of aluminum alloy shell castings and reduce the impact of pores, pinholes, and slag inclusions on the product qualification rate, a secondary refining step is used in the casting process, that is, the alloy is refined once before and after the furnace is released. At the same time, a fiber filter screen is used at the riser nozzle, a ceramic filter screen is used at the horizontal gate, and a double-layer fiber filter screen is placed at the end of the horizontal gate and the gap opening to perform three-time filtration to control the occurrence of product slag defects. rate.
Actual Production Situation And Effect
According to the above scheme and process, 6 shell samples were randomly selected for inspection in actual production, and it was found that scheme C has a better effect on improving the internal defects of the shell castings and increasing the yield of the shell. Through X-ray inspection, it was found that the internal control pass rate reached 100%; and then the precision turning test found that the porosity index of the machined surface reached the ASTM E505 level 2 level; through the destructive crush test, it was found that all samples could reach Withstand the pressure above 25kN. It can be seen that the aluminum alloy shell casting design and process selection introduced in this article are relatively reasonable, and certain effects have been achieved in controlling product quality.
Conclusion
With the continuous improvement of science and technology and related processes, the die-casting process of aluminum alloy parts has been continuously improved. The traditional related process flow is long, which is not conducive to quality control in the casting process. In order to ensure the improvement of production quality, it is necessary to start quality management from the material stage. The production process and key technologies of the above aluminum alloy shell castings have reached reasonable and feasible standards through scientific design and program selection, which proves that the relevant technologies and processes can meet the quality requirements of mass production for related casting products, and also verify the aluminum alloy The role of key parts die-casting technologies in improving the overall quality of related products.
Please keep the source and address of this article for reprinting:The Analysis of Aluminum Alloy Die Casting Key Technology
Minghe Die Casting Company are dedicated to manufacture and provide quality and high performance Casting Parts(metal die casting parts range mainly include Thin-Wall Die Casting,Hot Chamber Die Casting,Cold Chamber Die Casting),Round Service(Die Casting Service,Cnc Machining,Mold Making,Surface Treatment).Any custom Aluminum die casting, magnesium or Zamak/zinc die casting and other castings requirements are welcome to contact us.
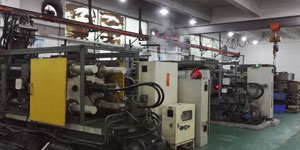
Under the control of ISO9001 and TS 16949,All processes are carried out through hundreds of advanced die casting machines, 5-axis machines, and other facilities, ranging from blasters to Ultra Sonic washing machines.Minghe not only has advanced equipment but also have professional team of experienced engineers,operators and inspectors to make the customer’s design come true.
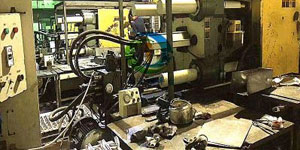
Contract manufacturer of die castings. Capabilities include cold chamber aluminum die casting parts from 0.15 lbs. to 6 lbs., quick change set up, and machining. Value-added services include polishing, vibrating, deburring, shot blasting, painting, plating, coating, assembly, and tooling. Materials worked with include alloys such as 360, 380, 383, and 413.
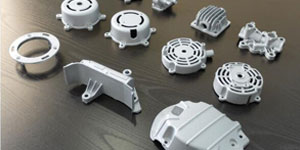
Zinc die casting design assistance/concurrent engineering services. Custom manufacturer of precision zinc die castings. Miniature castings, high pressure die castings, multi-slide mold castings, conventional mold castings, unit die and independent die castings and cavity sealed castings can be manufactured. Castings can be manufactured in lengths and widths up to 24 in. in +/-0.0005 in. tolerance.
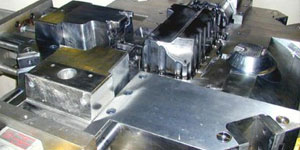
ISO 9001: 2015 certified manufacturer of die cast magnesium, Capabilities include high-pressure magnesium die casting up to 200 ton hot chamber & 3000 ton cold chamber, tooling design, polishing, molding, machining, powder & liquid painting, full QA with CMM capabilities, assembly, packaging & delivery.
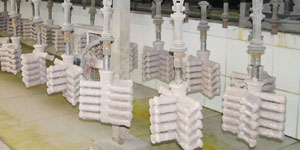
ITAF16949 certified. Additional Casting Service Include investment casting,sand casting,Gravity Casting, Lost Foam Casting,Centrifugal Casting,Vacuum Casting,Permanent Mold Casting,.Capabilities include EDI, engineering assistance, solid modeling and secondary processing.
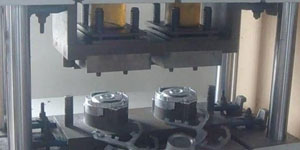
Casting Industries Parts Case Studies for: Cars, Bikes, Aircraft, Musical instruments, Watercraft, Optical devices, Sensors, Models, Electronic devices, Enclosures, Clocks, Machinery, Engines, Furniture, Jewelry, Jigs, Telecom, Lighting, Medical devices, Photographic devices, Robots, Sculptures, Sound equipment, Sporting equipment, Tooling, Toys and more.
What Can we help you do next?
∇ Go To Homepage For Die Casting China
→Casting Parts-Find out what we have done.
→Ralated Tips About Die Casting Services
By Minghe Die Casting Manufacturer |Categories: Helpful Articles |Material Tags: Aluminum Casting, Zinc Casting, Magnesium Casting, Titanium Casting, Stainless Steel Casting, Brass Casting,Bronze Casting,Casting Video,Company History,Aluminum Die Casting |Comments Off