The Analysis Of Austenitic Stainless Steel Welding Defects
Stainless steel can be divided into four categories according to the organization: austenitic stainless steel, ferritic stainless steel, martensitic stainless steel and duplex stainless steel. The production and usage of austenitic stainless steel account for about 70% of the total output of stainless steel, and it is the most important stainless steel type. Austenitic stainless steel generally contains more elements of Cr and Ni. Compared with other stainless steels, in addition to excellent corrosion resistance, austenitic stainless steel also has biocompatibility, good formability and weldability, good plasticity, toughness, and non-magnetic characteristics. It is a material with very good performance. Therefore, it is widely used in many fields such as petrochemical industry, biomedicine, food, marine and so on.
Austenitic stainless steel has many advantages, but some defects that affect material properties often appear during the welding process, such as severe intergranular corrosion of welded joints, stress corrosion, and hot cracking. Once these defects occur, they will definitely affect the service life of the equipment during use and cause safety hazards. Researchers have put forward measures to reduce or prevent defects on the basis of analyzing and discussing the defects that often occur in the welding process of austenitic stainless steel. It has important significance and reference value for improving the service life of austenitic stainless steel and expanding its application fields.
There are many factors that affect the welding quality of austenitic stainless steel, mainly including materials, processes and environments. Intergranular corrosion is the most prone problem in the welding process of stainless steel. By adjusting the percentage of C element in the welding material and base metal, and adding ferrite forming elements appropriately, under suitable welding conditions and correct welding Under treatment, the occurrence of such defects can basically be avoided. The carbon content of austenitic stainless steel is very low, and about 1% Ti is added as a stabilizer to the steel to inhibit the formation of Cr carbides, thereby eliminating the tendency of steel to intergranular corrosion.
Material stress corrosion cracking is the damage caused by the combined action of stress and corrosive environment, so measures can be taken from the environment and stress to prevent the occurrence of stress corrosion. On the one hand, changing the corrosive environment in contact with the material is an effective measure to prevent stress corrosion. On the other hand, reducing or eliminating residual stress is another effective measure to prevent stress corrosion. The occurrence of stress corrosion is mainly determined by the low thermal conductivity and large linear expansion coefficient of austenitic stainless steel. The probability of occurrence can be reduced by increasing the annealing process after welding. If annealing is not possible, you can use appropriate The welding process is improved, while avoiding contact with halogen-containing corrosive solutions and controlling the oxygen content in the solution.
The hot crack of austenitic stainless steel is mainly affected by alloy composition, metallographic structure and welding stress. Therefore, it can be controlled by adjusting the alloy composition of the welding material, controlling the existing metallographic structure and adopting a suitable welding process. The embrittlement of stainless steel can be avoided and improved by adjusting the alloy composition. Taking appropriate measures in terms of materials and processes will greatly increase the service life of austenitic stainless steel, which has important economic significance.
Please keep the source and address of this article for reprinting:The Analysis Of Austenitic Stainless Steel Welding Defects
Minghe Die Casting Company are dedicated to manufacture and provide quality and high performance Casting Parts(metal die casting parts range mainly include Thin-Wall Die Casting,Hot Chamber Die Casting,Cold Chamber Die Casting),Round Service(Die Casting Service,Cnc Machining,Mold Making,Surface Treatment).Any custom Aluminum die casting, magnesium or Zamak/zinc die casting and other castings requirements are welcome to contact us.
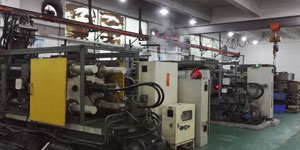
Under the control of ISO9001 and TS 16949,All processes are carried out through hundreds of advanced die casting machines, 5-axis machines, and other facilities, ranging from blasters to Ultra Sonic washing machines.Minghe not only has advanced equipment but also have professional team of experienced engineers,operators and inspectors to make the customer’s design come true.
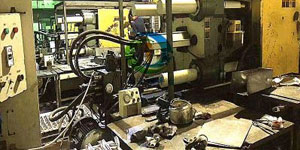
Contract manufacturer of die castings. Capabilities include cold chamber aluminum die casting parts from 0.15 lbs. to 6 lbs., quick change set up, and machining. Value-added services include polishing, vibrating, deburring, shot blasting, painting, plating, coating, assembly, and tooling. Materials worked with include alloys such as 360, 380, 383, and 413.
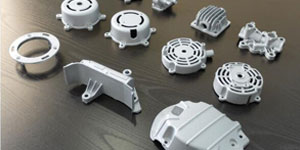
Zinc die casting design assistance/concurrent engineering services. Custom manufacturer of precision zinc die castings. Miniature castings, high pressure die castings, multi-slide mold castings, conventional mold castings, unit die and independent die castings and cavity sealed castings can be manufactured. Castings can be manufactured in lengths and widths up to 24 in. in +/-0.0005 in. tolerance.
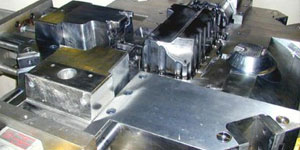
ISO 9001: 2015 certified manufacturer of die cast magnesium, Capabilities include high-pressure magnesium die casting up to 200 ton hot chamber & 3000 ton cold chamber, tooling design, polishing, molding, machining, powder & liquid painting, full QA with CMM capabilities, assembly, packaging & delivery.
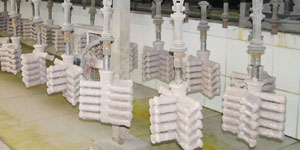
ITAF16949 certified. Additional Casting Service Include investment casting,sand casting,Gravity Casting, Lost Foam Casting,Centrifugal Casting,Vacuum Casting,Permanent Mold Casting,.Capabilities include EDI, engineering assistance, solid modeling and secondary processing.
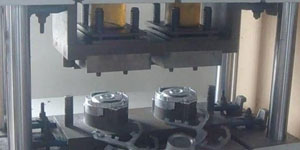
Casting Industries Parts Case Studies for: Cars, Bikes, Aircraft, Musical instruments, Watercraft, Optical devices, Sensors, Models, Electronic devices, Enclosures, Clocks, Machinery, Engines, Furniture, Jewelry, Jigs, Telecom, Lighting, Medical devices, Photographic devices, Robots, Sculptures, Sound equipment, Sporting equipment, Tooling, Toys and more.
What Can we help you do next?
∇ Go To Homepage For Die Casting China
→Casting Parts-Find out what we have done.
→Ralated Tips About Die Casting Services
By Minghe Die Casting Manufacturer |Categories: Helpful Articles |Material Tags: Aluminum Casting, Zinc Casting, Magnesium Casting, Titanium Casting, Stainless Steel Casting, Brass Casting,Bronze Casting,Casting Video,Company History,Aluminum Die Casting |Comments Off