The Analysis Of Measures For Blast Furnace Hearth Longevity
The blast furnace is forced to take measures to protect the furnace due to problems with the longevity of the hearth, which will increase the difficulty of blast furnace operation and deteriorate the economic and technical indicators of the blast furnace, which will have a significant impact on the overall production order and economic benefits of the enterprise. In recent years, domestic blast furnace hearth burn-through accidents have occurred frequently, and most large blast furnaces have a life span of only about 10 years, and some are even lower.
Therefore, the longevity of the blast furnace hearth is still an important link restricting my country's ironmaking production.
Hearth erosion is diverse and the reasons are different
Blast furnace hearth erosion types are mainly divided into mushroom erosion, elephant foot erosion, pot bottom erosion, wide face erosion and partial funnel erosion. Among them, mushroom erosion, elephant foot erosion and funnel erosion belong to the abnormal erosion of the hearth, and the hearth with longevity problem is mainly manifested in these three types of erosion shapes. The hearth of a long-lived blast furnace usually shows erosion in the shape of a pot bottom or a wide face. Mushroom and elephant foot erosion are generally relatively light on the bottom of the furnace, while erosion on the side walls of the hearth is relatively heavy. Pot-shaped and wide-faced erosion is generally relatively heavy on the bottom of the furnace, and relatively light on the side walls of the hearth. Funnel erosion is local abnormal erosion of the hearth, and blast furnaces that have longevity of the hearth soon after they are put into production are mostly manifested by this kind of erosion. Under normal circumstances, the erosion shape of the hearth is related to the cooling intensity, the quality of the raw fuel entering the furnace, the kinetic energy of the blast, the liquid permeability of the dead coke pile in the hearth center, and the smelting strength of the blast furnace.
The main reasons for the abnormal erosion of the hearth of the blast furnace include: unreasonable design of the hearth structure, substandard refractory quality, poor construction quality, poor quality of raw materials and fuels, and serious excess of harmful elements (zinc, alkali metals, lead, etc.) into the furnace. The basic system is unreasonable, the oven time is insufficient and the furnace is opened too quickly, and the routine inspection, maintenance and furnace protection measures are not in place. If there are one or more of these factors, the blast furnace hearth will have a longevity problem.
To extend the life of the hearth must be fully regulated
The longevity of the blast furnace hearth is mainly due to the combined effect of three factors: one is the design and construction, which is the basis of longevity; the second is the operation during the production period; the third is the monitoring and maintenance. Moreover, the longevity of the blast furnace hearth is a systematic project, involving many links, any problem in any link may cause fatal damage to the longevity of the hearth. Therefore, the longevity of the blast furnace hearth should be based on the basics and be fully regulated.
Hearth design with dead iron layer. The small blast furnace has a small hearth diameter, lower pressure on the upper material column, large blast kinetic energy, dead coke piles easily floating, and weak slag-iron circulation; large blast furnaces are the opposite of small blast furnaces, and the hearth activity is relatively poor. The dead coke pile is easy to settle at the bottom of the furnace, and the slag-iron circulation is strong. Therefore, the depth of the dead iron layer of large and small blast furnaces is different. The depth of the dead iron layer of a small blast furnace is generally designed according to 20% of the hearth diameter, and a large blast furnace is designed according to 25% to 30% of the hearth diameter. If the quality of raw materials and fuel is poor, it can be designed to be deeper. See the attached table for the depth of the dead iron layer of some large blast furnaces at home and abroad. There is a view that as the depth of the dead iron layer increases, the static pressure of the molten iron on the carbon bricks at the junction of the ring carbon and the bottom carbon bricks will increase, which will intensify the foot-like and mushroom-like erosion. But the impact of static pressure increase is much smaller than that of molten iron circulation. Therefore, reducing molten iron circulation is the basis for controlling the erosion of elephant feet and mushrooms.
Hearth structure design and refractory material selection. The bottom of domestic blast furnaces is generally built with large carbon bricks, the bottom layer is made of graphite carbon bricks, and one layer of semi-graphite bricks + 2 layers of ultra-microporous carbon bricks or 1 layer of semi-graphite bricks + 1 layer of microporous carbon bricks are used upwards. 1 layer of ultra-microporous carbon bricks and other structural forms. Domestic blast furnace hearth ring carbon mainly adopts two structural forms: large carbon bricks and small carbon bricks, both of which have good longevity performance. UCAR carbon brick is a design concept with high thermal conductivity. However, in recent years, many domestic blast furnaces using UCAR carbon bricks have suffered from longevity of the hearth. The reason is that they do not have a deep understanding of the design concept, the design of the hearth structure is unreasonable, and the related supporting facilities do not match. Ignore the quality of construction. For the bottom of a large blast furnace, the thickness can be appropriately reduced. The total thickness of the bottom carbon bricks of the large blast furnace should be controlled between 1.2m and 1.6m. The thickness of the bottom carbon bricks should also refer to factors such as raw fuel conditions and hearth diameter.
The 25mm~30mm gap between the hearth cooling wall and the furnace shell is generally filled with anhydrous heat-insulating castable according to the traditional design to facilitate the heat preservation of the hearth. In fact, most of the heat lost in the hearth is taken away by the hearth cooling water, and very little heat is dissipated through the furnace shell. From the perspective of the longevity of the blast furnace, anhydrous high thermal conductivity castables are used instead of anhydrous heat insulating materials to prepare for abnormal corrosion of the hearth, adding water to the furnace shell to increase the cooling intensity.
Hearth cooling system design. The cooling capacity of the cooling system should match the hearth refractory material, and the overall thermal conductivity of the cooling stave should be greater than that of the hearth refractory masonry. For large carbon brick hearths, the use of high-quality smooth gray cast iron cooling stave (substrate thermal conductivity 34W/(m·K)) can meet the requirements. And if the NMD bricks with UCAR carbon bricks are built in the cooling stave (thermal conductivity 40W/(m·K)~60W/(m·K)), choose the cooling stave at the 2nd and 3rd sections of the hearth where the molten iron circulation is more severe. Rolled copper (thermal conductivity of 360W/(m·K)) or cast copper (matrix thermal conductivity of 300W/(m·K)) cooling stave with higher thermal conductivity is more reasonable.
The design of the hearth stave should meet the requirement that the stave cooling specific surface area (the cooling stave specific surface area = the sum of the outer diameter of the cooling water pipe/the stave width) is greater than 1. Baosteel and some foreign long-life blast furnace hearth stave cooling The specific surface area often reaches more than 1.20. The design of the cooling water pipe should be as close as possible to the thin pipes, which will not only improve the cooling effect, but also greatly save water under the same cooling intensity.
Use soft water or pure water to cool the hearth cooling wall of a large blast furnace. The difference between the wall temperature and the temperature of the cooling water should be kept within 5°C. The amount of cooling water in the hearth is mainly adjusted based on the cooling water speed, as long as the cooling water speed of the hearth and furnace bottom can be above 2.0m/s.;quality of work. In order to ensure the quality of construction, winter construction should be avoided as far as possible for hearth masonry; winter construction is really unavoidable, refractory materials and construction sites should be temperature-raising measures. For hearths with large carbon brick structures, the lifting of carbon bricks should use suction cups as far as possible, and do not use card holes; the temperature measuring galvanic holes on the surface of the carbon bricks should be as small as possible, and the ramming should be solid; the carbon ramming layer should be strictly in accordance with Ramming should be carried out in the construction specification. The circumferential seams should be cleaned before paving. The thickness of the paving should be uniform. The thickness of the paving should be leveled. The thickness of the paving should not exceed 100mm each time. % Above, the density sampling should reach above 1.65g/cm3. There are many brick joints in the UCAR ring charcoal hearth structure, and the masonry should be built in strict accordance with UCAR brick construction specifications.
Oven quality. When drying the furnace, the water volume of the cooling wall should be reduced, and the temperature of the cooling wall should reach 60℃. The ramming layer between the cooling wall of the large ring charcoal hearth and the carbon bricks uses tar and asphalt as the binding agent. Because the solidification temperature of tar is high, the ramming layer will not solidify in the production of a first-generation blast furnace and can maintain good softness It can absorb the expansion pressure of carbon bricks, so the ramming layer does not have to reach too high temperature during the oven. The UCAR bricks are combined into a whole by the carbon bonds formed after the carbon cement is cured by heating. The curing of carbon mortar needs to be heated to 100°C for 4 hours, and then at 120°C to 130°C for 16 hours.
Reduce slag-iron circulation erosion. Slag-iron circulation erosion is the main cause of abnormal foot-shaped and mushroom-shaped hearth erosion. The following measures should be taken: First, the blast furnace should control the appropriate smelting intensity. Practice has shown that there is an obvious positive correlation between smelting intensity and hearth erosion. The second is to activate the hearth and reduce the center dead coke pile. The third is to maintain a regular furnace type, avoid hearth accumulation, and carefully use fluorite and manganese ore to wash the furnace. The fourth is to control a reasonable slag iron flow rate and tap depth to achieve a balanced and stable tapping.
Control the cyclic enrichment of alkali metals, zinc, etc. in the blast furnace. The alkali metal in the blast furnace is mainly discharged out of the furnace through slag. By appropriately increasing the amount of slag, reducing the alkalinity of the slag and the furnace temperature, effective alkali removal can be achieved. Zinc is mainly discharged out of the furnace through blast furnace gas. By appropriately developing the central air flow, controlling the addition of high-zinc materials such as blast furnace bag ash and converter sludge can effectively reduce the cyclic enrichment of zinc in the blast furnace.
Strengthen hearth monitoring and take timely measures to protect the furnace. Establish a comprehensive hearth longevity monitoring system to dynamically track and monitor hearth carbon brick temperature, hearth cooling wall temperature, furnace shell temperature, hearth water temperature difference, etc. When the hearth has a longevity problem, the following measures are taken to protect the furnace: First, it is more reasonable to use high-titanium balls to protect the furnace with titanium-containing minerals such as titanium ore, and the titanium content of the molten iron is controlled at 0.100%~0.200%. The second is to strengthen the cooling of the hearth. When the temperature of the furnace shell or the cooling stave rises, external water spray cooling is adopted. The third is to adjust the lower air supply system. The fourth is to carry out hearth grouting to reduce the thermal resistance of the air gap. The grouting maintenance should be started within half a year or one year after the furnace is opened. The pressure at the grouting hole is generally controlled to be no more than 10kg/cm2. The fifth is to cool the furnace with air off. The cooling time of the furnace should be based on the principle that the heat flow intensity returns below the warning value, and the part of the tuyere corresponding to the dangerous part should be blocked when the air is restored.
In short, hearth longevity is the integration of comprehensive technology, and it is a system engineering involving multiple links including design, procurement, construction, oven, operation, inspection, and maintenance. The design of the hearth must follow the heat transfer theory, and it is a trend to increase the depth of the dead iron layer. The purchase of refractory materials should not blindly pursue low cost, but should put quality first, and do a good job in the inspection and acceptance of the factory. The construction must be carried out in strict accordance with the specifications to ensure that the inspection is in place. The quality of the raw fuel and the furnace capacity must be effectively matched, and the quality of the coke must be highly valued. The lower part of the blast furnace operation must blow the center, and the upper part must control a smaller amount of center coke. In addition, it is necessary to regularly inspect the content of harmful elements and strictly control the amount of entering the furnace. The hearth must form a dynamic erosion model to effectively monitor and protect the furnace in time.
Please keep the source and address of this article for reprinting:The Analysis Of Measures For Blast Furnace Hearth Longevity
Minghe Die Casting Company are dedicated to manufacture and provide quality and high performance Casting Parts(metal die casting parts range mainly include Thin-Wall Die Casting,Hot Chamber Die Casting,Cold Chamber Die Casting),Round Service(Die Casting Service,Cnc Machining,Mold Making,Surface Treatment).Any custom Aluminum die casting, magnesium or Zamak/zinc die casting and other castings requirements are welcome to contact us.
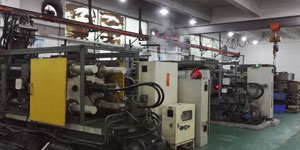
Under the control of ISO9001 and TS 16949,All processes are carried out through hundreds of advanced die casting machines, 5-axis machines, and other facilities, ranging from blasters to Ultra Sonic washing machines.Minghe not only has advanced equipment but also have professional team of experienced engineers,operators and inspectors to make the customer’s design come true.
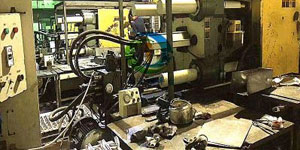
Contract manufacturer of die castings. Capabilities include cold chamber aluminum die casting parts from 0.15 lbs. to 6 lbs., quick change set up, and machining. Value-added services include polishing, vibrating, deburring, shot blasting, painting, plating, coating, assembly, and tooling. Materials worked with include alloys such as 360, 380, 383, and 413.
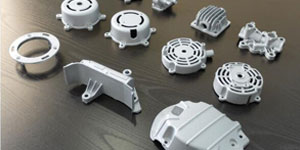
Zinc die casting design assistance/concurrent engineering services. Custom manufacturer of precision zinc die castings. Miniature castings, high pressure die castings, multi-slide mold castings, conventional mold castings, unit die and independent die castings and cavity sealed castings can be manufactured. Castings can be manufactured in lengths and widths up to 24 in. in +/-0.0005 in. tolerance.
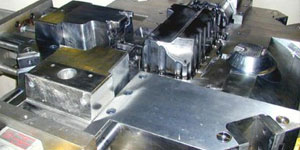
ISO 9001: 2015 certified manufacturer of die cast magnesium, Capabilities include high-pressure magnesium die casting up to 200 ton hot chamber & 3000 ton cold chamber, tooling design, polishing, molding, machining, powder & liquid painting, full QA with CMM capabilities, assembly, packaging & delivery.
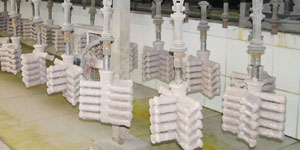
ITAF16949 certified. Additional Casting Service Include investment casting,sand casting,Gravity Casting, Lost Foam Casting,Centrifugal Casting,Vacuum Casting,Permanent Mold Casting,.Capabilities include EDI, engineering assistance, solid modeling and secondary processing.
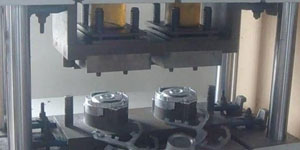
Casting Industries Parts Case Studies for: Cars, Bikes, Aircraft, Musical instruments, Watercraft, Optical devices, Sensors, Models, Electronic devices, Enclosures, Clocks, Machinery, Engines, Furniture, Jewelry, Jigs, Telecom, Lighting, Medical devices, Photographic devices, Robots, Sculptures, Sound equipment, Sporting equipment, Tooling, Toys and more.
What Can we help you do next?
∇ Go To Homepage For Die Casting China
→Casting Parts-Find out what we have done.
→Ralated Tips About Die Casting Services
By Minghe Die Casting Manufacturer |Categories: Helpful Articles |Material Tags: Aluminum Casting, Zinc Casting, Magnesium Casting, Titanium Casting, Stainless Steel Casting, Brass Casting,Bronze Casting,Casting Video,Company History,Aluminum Die Casting |Comments Off