The Anticorrosion Of Ductile Iron Pipe Zinc Layer
With the rapid and widespread use of ductile iron pipes in the water and gas industry, China’s annual output increased from 100,000 tons in 1990 to 900,000 tons in 2001, accounting for more than 50% of the total annual output of cast iron pipes. The anti-corrosion of ductile iron pipe is directly related to the long-term usability and safety of the pipeline, so it is an important indicator to measure the technology and operating conditions of the pipe network. According to the survey results of 10 typical cities, the static leakage rate of China's urban water supply pipe network reached 12 ~ 13%, which far exceeded the national standard that the urban leakage rate should be controlled below 6%. Therefore, pipeline anti-corrosion has always been a hot topic for us. Subject.
At present, nodular cast iron pipes use cement lining as the internal anti-corrosion form, and zinc plus asphalt as the external anti-corrosion form, and have been manufactured in the production process, without the need for anti-corrosion treatment after construction and installation. This has become a common practice for ductile iron pipe manufacturers at home and abroad, and the anti-corrosion effect is also very obvious.
In Article 4.4.2.2 of "Pipe Fittings" and in Article 4.4 of the international standard ISO 8179-1:1995(E) "Nodular cast iron pipes-Outer coating-Part I", it is clearly stipulated that the density of the zinc layer shall not be low At 130g/m2, the local minimum density shall not be lower than 110g/m2. In the Chinese national standard GB/T17456-1998, the international standard ISO 8179-1:1995 is equivalently adopted.
There are relatively few studies on the anti-corrosion of zinc coatings in China, but abroad, especially the Saint-Gobain Musong Bridge, the anti-corrosion research of zinc coatings has a history of over 60 years. In the internal standards of the Saint-Gobain Musong Bridge, the zinc + asphalt external anti-corrosion form is determined as the basic standard external anti-corrosion layer of ductile iron pipes, and it is suitable for most soil types. At the same time, this is also the ductile iron pipe of developed countries such as Europe. The standard external anti-corrosion mode.
Corrosion Of Soil To Ductile Iron Pipe
1. Electrochemical corrosion
The contact between the metal and the electrolyte solution will produce an electrochemical effect, and there will be a potential difference between the surface and the solution, that is, the electrode potential. The metal surface may have different phases due to different grain boundaries, crystal defects, inclusions, stress and surface damage. These electrochemical inhomogeneities make the electrode potentials of various microscopic parts of the metal surface different, which constitutes a corrosion cell. The electrons lost in the low-potential part become metal ions and enter the solution, which is called the anode; the electrons flow to the high-potential part and become the cathode. As a result of this galvanic reaction, a large amount of rust is formed on the surface of the metal.
Oxygen concentration difference battery for ductile iron pipe: When the ductile iron pipe is buried in the wet ground, the backfill at the top is relatively loose and close to the ground, while the bottom is basically the original soil, the soil is dense and far from the ground. When oxygen penetrates from the top, it will cause a difference in oxygen concentration above and below the pipe, and the pipe itself is both the electrode and the electrode connecting wire; water is the electrolyte, so an "oxygen concentration difference battery" is formed. Iron loses electrons and enters the water film, and oxygen gets electrons to become hydroxide ions.
2. Microbial corrosion
Microbial corrosion is also a kind of electrochemical corrosion. The difference is that the medium changes some physical and chemical properties of the material interface in contact with it due to the reproduction and metabolism of corrosive microorganisms. Traditionally, it can be divided into anaerobic corrosion and aerobic corrosion.
Sulfate-reducing bacteria SBR is the most researched anaerobic corrosion-induced root cause among microorganisms. Von Wogozen Kuhr et al. proposed the classic depolarization theory in 1974. They believed that the pitting corrosion of buried cast iron pipes was due to the activity of SBR to deoxidize the metal surface through hydrogenase. The general reaction formula is as follows:
4Fe + SO42- + 4H2O 3Fe(OH)2 + FeS + 2OH-
Aerobic bacteria are iron oxidizing bacteria, sulfide bacteria and iron bacteria. The sulfuric acid produced by the action of sulfur bacteria can cause aerobic corrosion. These bacteria can survive when the sulfuric acid concentration reaches 10-12%, and can cause severe corrosion to cast iron. Another reason is that bacteria multiply on the metal surface under aerobic conditions to form an irregular biofilm. The activities of microorganisms cause changes in the environment within the biofilm, such as oxygen concentration, PH value, pH, etc., forming a yin and yang zone on the metal surface, leading to a galvanic cell reaction.
Please keep the source and address of this article for reprinting:The Anticorrosion Of Ductile Iron Pipe Zinc Layer
Minghe Die Casting Company are dedicated to manufacture and provide quality and high performance Casting Parts(metal die casting parts range mainly include Thin-Wall Die Casting,Hot Chamber Die Casting,Cold Chamber Die Casting),Round Service(Die Casting Service,Cnc Machining,Mold Making,Surface Treatment).Any custom Aluminum die casting, magnesium or Zamak/zinc die casting and other castings requirements are welcome to contact us.
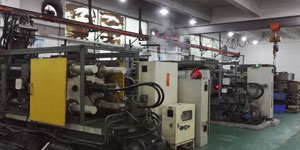
Under the control of ISO9001 and TS 16949,All processes are carried out through hundreds of advanced die casting machines, 5-axis machines, and other facilities, ranging from blasters to Ultra Sonic washing machines.Minghe not only has advanced equipment but also have professional team of experienced engineers,operators and inspectors to make the customer’s design come true.
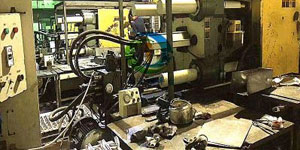
Contract manufacturer of die castings. Capabilities include cold chamber aluminum die casting parts from 0.15 lbs. to 6 lbs., quick change set up, and machining. Value-added services include polishing, vibrating, deburring, shot blasting, painting, plating, coating, assembly, and tooling. Materials worked with include alloys such as 360, 380, 383, and 413.
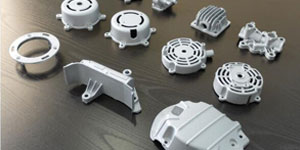
Zinc die casting design assistance/concurrent engineering services. Custom manufacturer of precision zinc die castings. Miniature castings, high pressure die castings, multi-slide mold castings, conventional mold castings, unit die and independent die castings and cavity sealed castings can be manufactured. Castings can be manufactured in lengths and widths up to 24 in. in +/-0.0005 in. tolerance.
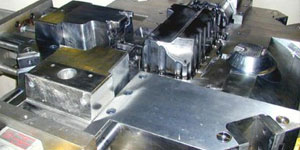
ISO 9001: 2015 certified manufacturer of die cast magnesium, Capabilities include high-pressure magnesium die casting up to 200 ton hot chamber & 3000 ton cold chamber, tooling design, polishing, molding, machining, powder & liquid painting, full QA with CMM capabilities, assembly, packaging & delivery.
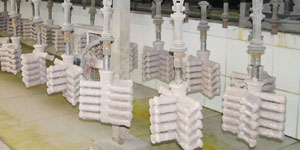
ITAF16949 certified. Additional Casting Service Include investment casting,sand casting,Gravity Casting, Lost Foam Casting,Centrifugal Casting,Vacuum Casting,Permanent Mold Casting,.Capabilities include EDI, engineering assistance, solid modeling and secondary processing.
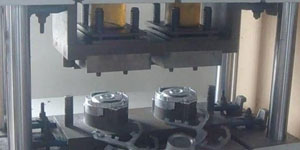
Casting Industries Parts Case Studies for: Cars, Bikes, Aircraft, Musical instruments, Watercraft, Optical devices, Sensors, Models, Electronic devices, Enclosures, Clocks, Machinery, Engines, Furniture, Jewelry, Jigs, Telecom, Lighting, Medical devices, Photographic devices, Robots, Sculptures, Sound equipment, Sporting equipment, Tooling, Toys and more.
What Can we help you do next?
∇ Go To Homepage For Die Casting China
→Casting Parts-Find out what we have done.
→Ralated Tips About Die Casting Services
By Minghe Die Casting Manufacturer |Categories: Helpful Articles |Material Tags: Aluminum Casting, Zinc Casting, Magnesium Casting, Titanium Casting, Stainless Steel Casting, Brass Casting,Bronze Casting,Casting Video,Company History,Aluminum Die Casting |Comments Off