The Application Of Impregnation Technology In Engine Manufacturing
Impregnation treatment of parts made of lightweight materials such as aluminum cylinders can effectively reduce the scrap rate of workpieces and significantly improve their quality. On the premise of ensuring product quality, they can effectively reduce manufacturing costs and improve production efficiency.
Proposal of engine lightweight and impregnation treatment
Lightweight has become a trend in the contemporary automobile industry, which is mainly determined by the worldwide attention to environmental protection and energy saving. The data shows that if a car's own weight is reduced by 10%, its fuel efficiency can be increased by 15%. The increase in fuel efficiency means that the car's fuel consumption and emissions are reduced. Therefore, reducing the weight of the car is the most effective way to improve the energy saving and environmental protection of the car. The engine is the most critical large assembly of a car, and reducing its weight is crucial to reducing the weight of the car.
From a technical point of view, there are many ways to achieve lightweight, such as the optimization of the whole machine structure, accessory modules and lightweight, but the use of lightweight materials such as plastics, aluminum alloys and magnesium alloys to replace traditional materials such as cast iron is the current reduction. The main way of engine weight. In fact, aluminum alloy has been widely used in engine cylinder heads, intake manifolds, and smaller parts such as water pump housings and oil pump housings for many years, and more and more companies have adopted aluminum alloy cylinder blocks in the past decade. However, compared with cast iron, aluminum castings are more prone to internal looseness, shrinkage and pores during the casting process due to crystal formation, shrinkage and gas absorption. These defective castings have a dense surface layer after machining. The area is removed, thereby exposing internal organizational defects. For those aluminum castings that require tightness in the engine, when passing through the leak detection process on the production line, the existence of defective micropores will cause excessive leakage and produce waste products, sometimes even in batches. Since these conditions can only be discovered after multiple machining, it will also cause serious waste of man-hours, raw materials and energy. It can be seen that in order to solve the problem of high scrap rate of aluminum castings, certain treatment measures must be taken in production. At present, the most commonly used technology is impregnation treatment, that is, leak plugging. The so-called "impregnation" is to infiltrate the infiltrant into the micro pores of the aluminum casting under certain conditions, and after solidification, the filler infiltrated into the pore and the inner wall of the pore of the casting are connected as a whole to block the micropores so that the parts can satisfy A process technology required for pressurization, anti-seepage and anti-leakage.
Vacuum pressure impregnation process
At present, in the production of aluminum castings at home and abroad, the vacuum pressure infiltration method is generally adopted. This process is mainly carried out in a vacuum pressure tank. According to the process flow, it can be divided into three stages: pre-treatment, impregnation treatment and post-treatment. Its various steps mainly include: pretreatment is also called microporous pretreatment, which mainly degreasing, cleaning, and drying the castings to prepare for the next process; the first step of impregnation treatment is to place the workpiece in a basket Then place the basket in the impregnation tank; vacuum the impregnation tank to remove the gas in the pores of the parts; transport the sealant from the storage tank to the impregnation tank, and submerge the parts that are still under vacuum; Vacuum the impregnation tank again to remove the gas in the sealant; release the vacuum and pressurize the impregnation tank with compressed air, which helps push the sealant into the pores; release the pressure and return the sealant to the storage tank; Post-processing is mainly to remove the parts, spin dry, rinse and complete the curing operations.
The main purpose of the pre-treatment is to remove oil stains, metal chips and dust on the surface of the parts, improve the quality of the impregnation, and prevent oil and mechanical impurities from being brought into the impregnation liquid to affect the penetration and adhesion. Commonly used degreasing methods include solvent degreasing, lye degreasing and electrochemical degreasing. The castings are taken out after the above-mentioned degreasing and cleaning, rinsed with hot water and then dried at 80-90 ℃. In order to improve the soaking effect and prevent a large amount of water from entering the vacuum pump, drying after cleaning is very important.
The impregnation treatment is to put the pre-processed workpieces into the impregnation tank to seal and vacuum, to fully remove the air and fine dust in the tank and the pores of the casting, and create the pressure difference dynamic conditions for the filling and infiltration of the impregnation agent. Then, the infiltrant is sucked in by the negative pressure in the tank, and the vacuum is again drawn. The purpose of the second vacuuming is to discharge the gas in the impregnation liquid in the tank to prevent the impregnation liquid containing the gas from penetrating into the micropore defects of the casting, so as to avoid the generation of pores during solidification that affect the sealing performance. Finally, pressurize, so that the infiltrant that has been filled and infiltrated into the pores of the casting further penetrates to the deepest part of each part of the defect. The impregnant is a liquid substance prepared from inorganic or organic substances. At present, the most widely used methacrylate PC504/66 sealant is cured under heating, and provides prominent micropore filling with its low shrinkage during polymerization. Ability, at the same time, its low viscosity helps the sealant penetrate quickly and deeply into the micropores. The cured sealant can function normally in the range of -50~200 ℃.
Post-treatment is to drip the workpiece, clean it, and put it in a curing oven to solidify, so that the infiltrant entering the pores of the casting changes from liquid to solid to form a solid solidified film. The curing temperature is generally set to 80~90 ℃, or placed at room temperature (above 25 ℃) for 24 hours. If the casting is used above 300 ℃, it should be cured at 80 ℃ for 2 h, and then at 110 ℃ for 1 h.
As to which part of the production process is impregnated, different production plants and different types of workpieces are very different. A small number of companies will make uniform regulations for all powertrain parts that require high manufacturing accuracy and airtightness: such parts must be impregnated before machining, that is, when they are still in the state of casting, in order to achieve improvement. The purpose of casting performance, extending tool life during machining and ensuring product quality. However, most factories still adopt different methods according to different types of parts. Generally speaking, for a few key parts, such as the aluminum cylinder block in the engine, it is usually required to impregnate all the parts when they are in the state of casting, and then send them. OEM. As for the impregnation of some workpieces according to certain criteria after a certain process in the production line of the OEM, it depends on the manufacturing process of the OEM.
For most parts, they are generally not required to be impregnated when they are in the state of castings. Instead, the impregnation process is implemented after a certain process in the production process according to the actual situation. That is, when the parts after several machining processes are confirmed that the leak detection value of some parts is within the specified interval, only this part of the rejected workpiece is impregnated. In most cases, the proportion of rejected workpieces is very low (roughly 1% to 2%), but when this proportion exceeds a certain limit (depending on the specific situation), the OEM will require the blank factory to All the castings are impregnated.
There are also some parts that require impregnation treatment are not included in the manufacturing process of the OEM due to structural reasons. For those parts whose leak detection results are out of tolerance, no matter how big the actual measured value is, they will be scrapped directly. However, if the leakage value exceeds the proportion of the workpiece to a certain extent, the main engine factory will also put forward the requirement of impregnation treatment for all the casting blanks.
So, where is the actual operation of impregnation treatment? The common practice at home and abroad is undertaken by independent and professional enterprises. This is not only efficient and easy to ensure quality, but also the cost is relatively low for the assembly plant. However, there are also a few engine factories with large batches, fast production pace and high product quality requirements. They will open up a closed area in the workshop, so that the above-mentioned professional factories engaged in impregnation treatment can build a relatively single, efficient and The impregnation production line with a higher degree of mechanization is equivalent to a section of the workshop. Of course, the operating rate of this "work section" is lower than that of a general production line.
Perform multiple definitions of impregnated workpieces
As we all know, as the main body of the engine, the cylinder block is the largest and heaviest part among them. When aluminum alloy is selected, its weight reduction by about half has the greatest significance for the lightweight of the engine. However, in view of the complex structure of the cylinder block and the number of machining processes, compared with other aluminum castings in the engine, the probability of internal defects in the aluminum cylinder block during the casting and forming process is also greater. Therefore, how to standardize and efficiently adopt immersion Infiltration process to ensure its quality is also the most concerned by enterprises. In the following, taking the aluminum cylinder as an example, the problem of defining and approving the workpieces that need to be impregnated is further explained through a representative case. A newly-built aluminum cylinder machining production line in a modern car engine factory has completed all rough machining processes before the workpiece enters the intermediate cleaning station. Before the next installation of the main bearing cap and subsequent finishing operations, a sealing test station was set up. In addition to the leak detection of the low-pressure oil passage, water passage and high-pressure oil passage of the aluminum cylinder block, this station is also equivalent to setting up a gate. According to the measured leakage value, it is necessary to determine whether this The aluminum cylinder is impregnated.
For the workpiece, there are two screening limits set: the first is the leakage rate of the inspected part, taking the low-pressure oil channel as an example, the leakage rate limit is 30 CC/min; the second screening limit is This inspected part is the object to determine whether there is a leak in the aluminum cylinder, but whether it is possible and necessary to remedy it through impregnation treatment. Taking the low-pressure oil passage as an example, the table indicates that it is 500 CC/min. In view of this, when the aluminum cylinder body after the intermediate cleaning process enters the sealing test station along the conveying raceway, if any of the measured leakage values of the workpiece is lower than the corresponding screening limit given in the table, that is, The leakage rate will be judged as qualified, and then it will flow into the next process. But as long as any one of the actual measured leakage values exceeds its leakage rate but is less than the scrap limit, take the low-pressure oil passage in the table as an example, the range is between 30 and 500CC/min. The aluminum cylinder block is treated as a workpiece that needs to be taken out for impregnation treatment, sent out by the raceway in the reverse direction, and then manually removed and sent away. As for a very small number of workpieces whose measured leakage value has reached or even exceeded the scrap limit in the table, they will flow out through the conveyor raceway. The above-mentioned detection, screening and diversion process is performed by the robot in the sealing test station.
In summary, after the impregnation treatment of aluminum cylinders and other parts, not only the scrap rate is reduced, and the quality is significantly improved, but also the manufacturing cost under the premise of ensuring quality is reduced, and the productivity is effectively improved. Therefore, in the process of the contemporary automobile engine industry becoming increasingly lightweight, the scientific and reasonable use of infiltration technology is the best solution to completely solve the inherent problems of aluminum alloy and other lightweight material castings (such as defects such as micropores) .
Please keep the source and address of this article for reprinting:The Application Of Impregnation Technology In Engine Manufacturing
Minghe Die Casting Company are dedicated to manufacture and provide quality and high performance Casting Parts(metal die casting parts range mainly include Thin-Wall Die Casting,Hot Chamber Die Casting,Cold Chamber Die Casting),Round Service(Die Casting Service,Cnc Machining,Mold Making,Surface Treatment).Any custom Aluminum die casting, magnesium or Zamak/zinc die casting and other castings requirements are welcome to contact us.
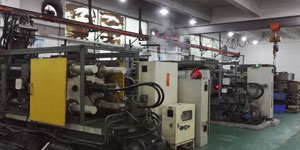
Under the control of ISO9001 and TS 16949,All processes are carried out through hundreds of advanced die casting machines, 5-axis machines, and other facilities, ranging from blasters to Ultra Sonic washing machines.Minghe not only has advanced equipment but also have professional team of experienced engineers,operators and inspectors to make the customer’s design come true.
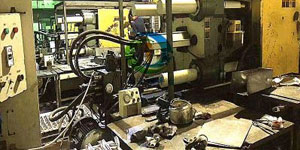
Contract manufacturer of die castings. Capabilities include cold chamber aluminum die casting parts from 0.15 lbs. to 6 lbs., quick change set up, and machining. Value-added services include polishing, vibrating, deburring, shot blasting, painting, plating, coating, assembly, and tooling. Materials worked with include alloys such as 360, 380, 383, and 413.
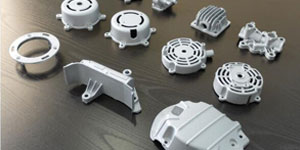
Zinc die casting design assistance/concurrent engineering services. Custom manufacturer of precision zinc die castings. Miniature castings, high pressure die castings, multi-slide mold castings, conventional mold castings, unit die and independent die castings and cavity sealed castings can be manufactured. Castings can be manufactured in lengths and widths up to 24 in. in +/-0.0005 in. tolerance.
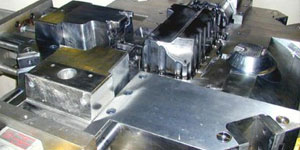
ISO 9001: 2015 certified manufacturer of die cast magnesium, Capabilities include high-pressure magnesium die casting up to 200 ton hot chamber & 3000 ton cold chamber, tooling design, polishing, molding, machining, powder & liquid painting, full QA with CMM capabilities, assembly, packaging & delivery.
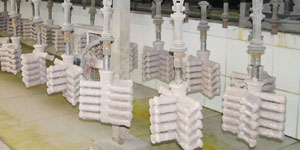
ITAF16949 certified. Additional Casting Service Include investment casting,sand casting,Gravity Casting, Lost Foam Casting,Centrifugal Casting,Vacuum Casting,Permanent Mold Casting,.Capabilities include EDI, engineering assistance, solid modeling and secondary processing.
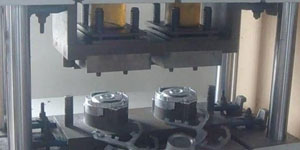
Casting Industries Parts Case Studies for: Cars, Bikes, Aircraft, Musical instruments, Watercraft, Optical devices, Sensors, Models, Electronic devices, Enclosures, Clocks, Machinery, Engines, Furniture, Jewelry, Jigs, Telecom, Lighting, Medical devices, Photographic devices, Robots, Sculptures, Sound equipment, Sporting equipment, Tooling, Toys and more.
What Can we help you do next?
∇ Go To Homepage For Die Casting China
→Casting Parts-Find out what we have done.
→Ralated Tips About Die Casting Services
By Minghe Die Casting Manufacturer |Categories: Helpful Articles |Material Tags: Aluminum Casting, Zinc Casting, Magnesium Casting, Titanium Casting, Stainless Steel Casting, Brass Casting,Bronze Casting,Casting Video,Company History,Aluminum Die Casting |Comments Off