The Application Skills Of Ultrasonic Flaw Detection For Forgings And Castings
Ultrasonic flaw detection of castings
Due to the coarse grains, poor sound permeability and low signal-to-noise ratio of castings, it is difficult to detect flaws. It uses sound beams with high-frequency sound energy to propagate inside the castings, and when they encounter internal surfaces or defects, they reflect and find defects.
The magnitude of the reflected sound energy is a function of the directivity and nature of the inner surface or defect and the acoustic impedance of this reflector. Therefore, various defects or sound energy reflected by the inner surface can be used to detect the location, wall thickness or surface of the defect.
The depth of the next defect. Ultrasonic testing is a widely used non-destructive testing method. Its main advantages are: high detection sensitivity, which can detect small cracks; it has large penetrating ability and can detect thick section castings. Its main limitations are: it is difficult to explain the reflected waveform of the disconnected defect with complex outline size and poor directivity; for undesirable internal structures, such as grain size, structure, porosity, inclusion content or fine dispersion Precipitates, etc., also hinder the interpretation of the waveform; in addition, the standard test block should be referenced when testing.
Ultrasonic flaw detection of forgings
(1) Forging processing and common defects
Forgings are formed by forging and pressing hot steel ingots. The forging process includes heating, deformation and cooling. Forging defects can be divided into casting defects, forging defects and heat treatment defects. Casting defects mainly include: residual shrinkage cavity, looseness, inclusions, cracks, etc. Forging defects mainly include: folding, white spots, cracks, etc. The heat treatment defects are mainly cracks.
The shrinkage cavity residue is the residual shrinkage cavity in the ingot when the cutting head is insufficient during forging, and it is more common at the end of the forging.
Porosity is the lack of compactness and cavities formed during the solidification and shrinkage of the steel ingot. During forging, it is not fully fused due to insufficient forging ratio, and mainly exists in the center and head of the steel ingot.
Inclusions include internal inclusions, foreign non-metallic inclusions and metal inclusions. The internal inclusions are mainly concentrated in the center and head of the ingot.
Cracks include casting cracks, forging cracks and heat treatment cracks. Austenitic steel axis intergranular cracks are cracks caused by casting. Improper forging and heat treatment will form cracks on the surface or core of the forging.
The white spot is the high hydrogen content of the forging, and the cooling is too fast after forging, and the hydrogen dissolved in the steel is too late to escape, causing cracking caused by excessive stress. The white spots are mainly concentrated in the center of the large section of the forging. White spots always appear in groups in steel.
(2) Overview of flaw detection methods
According to the classification of inspection time, forging inspection can be divided into raw material inspection and inspection in the manufacturing process, product inspection and in-service inspection.
The purpose of raw material flaw detection and flaw detection in the manufacturing process is to find defects as early as possible, so as to take timely measures to avoid the development and expansion of defects and cause scrapping. The purpose of product inspection is to ensure product quality. The purpose of in-service inspection is to monitor defects that may occur or develop after operation, mainly fatigue cracks.
1. Flaw detection of shaft forgings
The forging process of shaft forgings is mainly based on lengthening, so the orientation of most of the defects is parallel to the axis, and the detection of such defects is best with a longitudinal wave straight probe from the radial direction. Considering that the defects will have other distribution and orientation, the flaw detection of shaft forgings should also be supplemented with straight probe axial detection and oblique probe circumferential detection and axial detection.
2. Flaw detection of cake and bowl forgings
The forging process of cake and bowl forgings is mainly based on upsetting, and the distribution of defects is mainly parallel to the end surface. Therefore, detecting the defects on the end surface with a straight probe is the best method to detect defects.
3. Flaw detection of tube forgings
The forging process of barrel forgings is first upsetting, then punching, and then rolling. Therefore, the orientation of defects is more complicated than the orientation of defects in shaft forgings and cake forgings. However, since the central part of the ingot with the worst quality has been removed during punching, the quality of cylindrical forgings is generally better. The main orientation of the defects is still parallel to the outer surface of the cylinder, so the detection of the cylindrical forgings is still based on the detection of the outer cylindrical surface of the straight probe, but for the thicker wall of the cylindrical forgings, an oblique probe must be used for detection.
(3) Selection of detection conditions
Probe selection
In ultrasonic inspection of forgings, longitudinal wave straight probes are mainly used. The size of the chip is Φ14~Φ28mm, and Φ20mm is commonly used. For smaller forgings, considering the near-field area and coupling loss reasons, small chip probes are generally used. Sometimes in order to detect defects that are inclined at a certain angle with the detection surface, an oblique probe with a certain K value can also be used for detection. For short-distance defects, due to the influence of the blind area and near-field area of the straight probe, the double crystal straight probe is often used for detection.
The grains of forgings are generally finer, so a higher frequency of flaw detection can be selected, usually 2.5~5.0MHz. For a few forgings with coarse grains and severe attenuation, in order to avoid "forest echo" and improve the signal-to-noise ratio, a lower frequency should be selected, generally 1.0-2.5MHz.
Please keep the source and address of this article for reprinting: The Application Skills Of Ultrasonic Flaw Detection For Forgings And Castings
Minghe Die Casting Company are dedicated to manufacture and provide quality and high performance Casting Parts(metal die casting parts range mainly include Thin-Wall Die Casting,Hot Chamber Die Casting,Cold Chamber Die Casting),Round Service(Die Casting Service,Cnc Machining,Mold Making,Surface Treatment).Any custom Aluminum die casting, magnesium or Zamak/zinc die casting and other castings requirements are welcome to contact us.
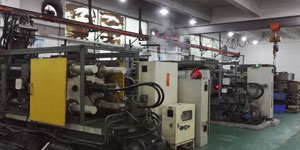
Under the control of ISO9001 and TS 16949,All processes are carried out through hundreds of advanced die casting machines, 5-axis machines, and other facilities, ranging from blasters to Ultra Sonic washing machines.Minghe not only has advanced equipment but also have professional team of experienced engineers,operators and inspectors to make the customer’s design come true.
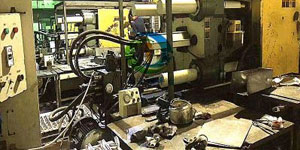
Contract manufacturer of die castings. Capabilities include cold chamber aluminum die casting parts from 0.15 lbs. to 6 lbs., quick change set up, and machining. Value-added services include polishing, vibrating, deburring, shot blasting, painting, plating, coating, assembly, and tooling. Materials worked with include alloys such as 360, 380, 383, and 413.
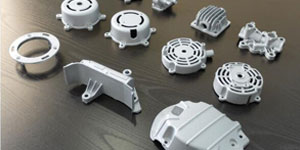
Zinc die casting design assistance/concurrent engineering services. Custom manufacturer of precision zinc die castings. Miniature castings, high pressure die castings, multi-slide mold castings, conventional mold castings, unit die and independent die castings and cavity sealed castings can be manufactured. Castings can be manufactured in lengths and widths up to 24 in. in +/-0.0005 in. tolerance.
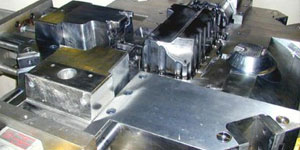
ISO 9001: 2015 certified manufacturer of die cast magnesium, Capabilities include high-pressure magnesium die casting up to 200 ton hot chamber & 3000 ton cold chamber, tooling design, polishing, molding, machining, powder & liquid painting, full QA with CMM capabilities, assembly, packaging & delivery.
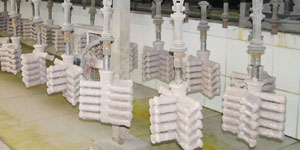
ITAF16949 certified. Additional Casting Service Include investment casting,sand casting,Gravity Casting, Lost Foam Casting,Centrifugal Casting,Vacuum Casting,Permanent Mold Casting,.Capabilities include EDI, engineering assistance, solid modeling and secondary processing.
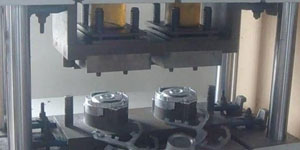
Casting Industries Parts Case Studies for: Cars, Bikes, Aircraft, Musical instruments, Watercraft, Optical devices, Sensors, Models, Electronic devices, Enclosures, Clocks, Machinery, Engines, Furniture, Jewelry, Jigs, Telecom, Lighting, Medical devices, Photographic devices, Robots, Sculptures, Sound equipment, Sporting equipment, Tooling, Toys and more.
What Can we help you do next?
∇ Go To Homepage For Die Casting China
→Casting Parts-Find out what we have done.
→Ralated Tips About Die Casting Services
By Minghe Die Casting Manufacturer |Categories: Helpful Articles |Material Tags: Aluminum Casting, Zinc Casting, Magnesium Casting, Titanium Casting, Stainless Steel Casting, Brass Casting,Bronze Casting,Casting Video,Company History,Aluminum Die Casting |Comments Off