The Atmosphere Control During Sintering Process Of Sintered Steel And Its Performance
Sintering atmosphere and its selection
If only the sintering of carbon-containing steel is considered, the sintering atmosphere used in the powder metallurgy industry is hydrogen, nitrogen, nitrogen + hydrogen (carbon potential or no carbon potential), decomposition of ammonia, endothermic gas, endothermic gas + nitrogen, synthesis For gas and vacuum, the correct selection of sintering atmosphere requires understanding of the characteristics and performance of various sintering atmospheres, and selection in accordance with the principles of ensuring quality and reducing costs.
Hydrogen is a strong reducing atmosphere. Many people believe that hydrogen has a certain decarburization effect, but this depends largely on the purity of the hydrogen used rather than the hydrogen itself. Generally, the hydrogen after electrolysis or catalytic conversion contains a certain amount of impurity gas, such as H2O, O2, CO and CH4, etc., sometimes the total amount can reach about 0.5%. Therefore, it is best to dry and purify it before use to reduce its oxygen content and dew point. However, due to the high price of hydrogen, pure hydrogen is rarely used as a sintering atmosphere unless there are special reasons.
Nitrogen is a safe and cheap inert gas, but because pure nitrogen does not have reducibility at the sintering temperature, pure nitrogen is rarely used as a sintering atmosphere in the production of traditional powder metallurgy steel. In recent years, as the cost of nitrogen purification has decreased and the airtightness of the sintering furnace has improved, nitrogen has also begun to be used as a sintering atmosphere for sintering carbon-containing steel.
In recent years, the nitrogen-hydrogen mixture has been increasingly used in the sintering of carbon steel. Nitrogen/hydrogen is usually used between 95/5-50/50. This mixture has a certain degree of reducibility and the dew point can reach Below -60℃, generally speaking, a certain amount of CH4 or C3H8 must be added to maintain a certain carbon potential when using this gas at 1050-1150℃, while sintering carbon steel above 1250℃ does not need to control the carbon potential. This mixture can be used to sinter chromium-containing iron-based alloys below 1120°C without oxidation.
Decomposed ammonia is made by decomposing ammonia gas through a heated catalyst, including 75% H2 and 25% N2. But generally speaking, a small amount of undecomposed ammonia molecules always remain in the decomposed ammonia. When they are in contact with hot metal at high temperatures, they will decompose into highly active hydrogen and nitrogen atoms, thereby nitriding the metal. Recent studies have shown that if properly controlled, sintering AstaloyCrM at 1120°C will decompose and ammoniate the 90N2/10H2 mixture with stronger reducibility. The main reason is that these active hydrogen atoms that have just been decomposed during the sintering process are more effective than 90N2/ The hydrogen in the 10H2 mixed gas has stronger reducibility and can effectively reduce the oxide layer outside the AstaloyCrM particles. To purify and decompose the ammonia, you can pass it through water and dry it, or use activated alumina or molecular sieve to remove the remaining All ammonia is removed.
Endothermic gas is a kind of mixed gas obtained by mixing hydrocarbon gas (CH4 or C3H8) with air in a certain proportion, preheating at 900-1000°C, and catalytically converting by nickel oxide catalyst. Depending on the ratio of air to coal gas, the conversion process is accompanied by endothermic or exothermic reactions. The resulting mixed gas is called endothermic gas or exothermic gas, and the reaction may be as follows:
CmHn+m(O2+3.774N2)—mCO+n/H2+1.887mN2
If the above reaction is to be carried out completely, that is, all the C in CmHm has just reacted with O2 in the air, the required air/gas should be m/2 (1+3.774), which is 2.387m. For example, if the hydrocarbon gas used is CH4, the required air/gas should be 2.387, and the mixed gas produced at this time includes 40.9% H2, 38.6% N2 and 20.5% CO. After the reaction, the mixed gas contains H2 The content of CO and CO decreases with the increase of air/gas, but the content of H2O and CO2 increases. It also shows that the carbon potential in the mixed gas after the reaction decreases with the increase of air/gas, and the oxidation performance increases. This is also the main reason why exothermic gas is rarely used when sintering carbon-containing steel, and most endothermic gas is used.
Generally speaking, the mixed gas produced by air/gas between 2.0-3.0 is called absorption Hot gas, and the mixed gas produced when the ratio is greater than 5.0 is called exothermic gas. The relationship between the dew point of the endothermic gas produced with CH4 as the raw material and air/gas shows that the air/gas only rises from 2.4 to 2.5, and the dew point of the mixed gas produced rises from -25°C to above 0°C. Therefore, if users produce endothermic gas by themselves, they should pay special attention to controlling the ratio of air to gas in the raw materials (preferably not more than 2.4) to obtain endothermic gas with a sufficiently low dew point. In the mixed gas after the reaction, the ratio of the different gases corresponds to the ratio at the end of the reaction, which is generally (1000-1100°C).
After the reaction, if the temperature of the gas changes, the carbon potential of the mixed gas, The dew point and the ratio of different gases will change. Many powder metallurgy manufacturers use one exothermic gas generator to supply the required sintering atmosphere for several sintering furnaces at the same time through the pipeline. The temperature of the atmosphere has been lowered before reaching the sintering furnace. . If the insulation of the pipeline is not good, and the temperature of the pipeline wall is lower than 800°C, then a part of the carbon in the mixed gas will be deposited on the pipeline wall in the form of carbon black. In other words, when the mixed gas is reheated to the sintering temperature in the sintering furnace, its carbon heat is much lower than the carbon potential that the endothermic gas generator can provide.
In this case, an appropriate amount of methane or propane should be added to the sintering furnace to ensure the carbon potential in the furnace. Now some foreign powder metallurgy manufacturers have begun to install a small endothermic gas generator beside each sintering furnace, and use the endothermic gas that has just been produced directly into the sintering furnace without cooling, so as to avoid affecting the sintering atmosphere due to temperature changes. . Another point to be reminded is that even with the catalytic effect of nickel oxide catalyst, a small amount of hydrocarbon gas (CH4 or C3H8, etc.) remains in the mixed gas obtained after conveying. In addition, between the gases at 900-1100℃ After the reaction reaches equilibrium, a small amount of CO2 and H2O (gaseous) will be produced, which need to be dried before use.
The addition of nitrogen to the endothermic gas can reduce the relative content of CO, CO2 and H2O in the endothermic gas, so as to buffer the sensitivity of the atmosphere to carbon potential and dew point, and make some correlation coefficients in the sintering atmosphere easier to control.
Synthetic gas is a method proposed by foreign sintering furnace manufacturers in recent years to directly generate (dilute) endothermic gas in the sintering furnace (without the need for an endothermic gas generator outside the furnace). It mixes gaseous methyl alcohol and nitrogen in a certain proportion and then directly passes it into the sintering furnace. The following reactions will occur in the high-temperature sintering zone:
CH3OH—CO+2H2
Because the ratio of CO and H2 in the decomposed gas is equal to the ratio of the endothermic gas produced by the usual method with CH4, and the mixed nitrogen can be combined to synthesize a mixed atmosphere with the same composition as the endothermic gas (1L The methane corresponds to 1.05nm3 nitrogen). Its biggest advantage is that it does not require an endothermic gas generator outside the furnace. In addition, users can mix different amounts of nitrogen gas to produce diluted endothermic gas according to their own requirements.
Vacuum is also a kind of sintering atmosphere, which is mostly used for sintering stainless steel and other materials, but not commonly used for sintering carbon steel.
Physical properties of sintering atmosphere
Most of the sintering atmosphere papers and reports mainly discuss the chemical behavior between different sintering atmospheres and the sintered body during the sintering process, but rarely discuss the influence of the physical properties of different atmospheres on sintering, although this effect is in many cases It cannot be ignored. For example, the difference in gas viscosity will cause the chemical concentration gradient of the sintered body from the surface to the inside along the opening, thereby affecting the surface properties of the sintered body. For another example, the heat capacity and thermal conductivity of different gases have a great influence on the sintering time and cooling rate. This section lists the main physical properties of some sintering atmospheres at different temperatures (around the sintering temperature) for readers' reference.
Examples of problems related to atmosphere during sintering
1 Examples of cracking on the surface of parts during dewaxing
When a mesh belt sintering furnace is used and endothermic gas is used as the sintering atmosphere, if the temperature rise rate and atmosphere in the dewaxing zone are not well controlled, surface cracking will occur. Many people think that this phenomenon is due to the rapid decomposition of the lubricant It is caused, but it is not the case. The real reason is that the carbon monoxide in the endothermic gas is decomposed into solid carbon and carbon dioxide in the temperature range of 450-700℃ under the catalysis of iron, nickel and other metals. It is the newly deposited solid carbon in the pores of the sintered body that expands its volume and causes the above-mentioned surface cracking phenomenon.
The quality of the parts varies with temperature during the sintering process in different atmospheres. Among them, atmosphere 3 is dry endothermic coal gas, and atmospheres 4 and 5 are endothermic coal gas added with different amounts of water vapor. It can be seen that during the sintering process, the quality of the parts begins to decline at about 200°C, which means that the solid lubricant inside it is continuously decomposed and overflows the sintering body, reducing its quality. Of course, if there is no solid lubricant in the mixed powder, the above phenomenon does not exist. If the above three atmospheres are used, the drier the atmosphere from the quality of the sintered body at about 450°C, the more serious this phenomenon will be.
But what’s interesting is that when gas 3 (dry endothermic gas) is used, surface cracking occurs regardless of the presence of solid lubricants, indicating that it is not directly related to dewaxing, and carbon-rich gas is found in the cracks. Phenomenon, we can affirm the correctness of the above explanation.
There are several ways to avoid the occurrence of the above-mentioned cracking phenomenon. The most direct thing is to change the sintering atmosphere from endothermic gas to hydrogen-nitrogen mixture without cracking broken lines. If the sintering atmosphere cannot be changed, there are two methods. One is to blow part of the endothermic gas containing water vapor into the dewaxing zone of the sintering furnace. However, this method is difficult to obtain stable control in actual operation.
The airflow control of the sintering furnace is not good, and the phenomenon of high dew point atmosphere entering the sintering zone may affect the sintering quality. The second and best method is to increase the heating rate of the parts in the dewaxing zone of the sintering furnace to make it pass 450 as soon as possible. In the area where cracking occurs at -600°C, the so-called fast dewaxing is usually designed for this phenomenon.
2 AstaloyCrM sintering example
Metal chromium is widely used in alloy steel because of its low price and good strengthening effect. However, chromium-containing sintered steel will encounter many problems in its production process. One is the production of chromium-containing iron powder, which must undergo a strict atomization and annealing reduction process to obtain raw material powder with lower oxygen and carbon content. .
Honganas AB of Sweden is currently the only manufacturer in the world that can produce this raw material powder at low cost. The second is that even if high-quality chromium-containing iron powder can be obtained, if the sintering and medium temperature, especially the sintering atmosphere, cannot be well controlled, it will be more likely to be oxidized during sintering and oxidation, and the sintering performance will be reduced.
Thermodynamic calculations and a large number of experiments have proved that if the endothermic gas is used as the sintering atmosphere of AsaloyCrM, the sintering requirements cannot be met even if the dew point is very low.
In other words, only pure hydrogen or hydrogen-nitrogen mixture can be used for sintering AsaloyCrM. At present, most of the latter are used. , The proportion of hydrogen accounts for 5%-20%. The reader should be reminded not only to ensure the composition of the sintering atmosphere, but also to ensure the quality of the sintering atmosphere.
The so-called quality here refers to the degree of oxidation in the sintering atmosphere, which is generally calibrated by the partial pressure of oxygen in the atmosphere. When sintering at 1120℃, if the oxygen partial pressure in the atmosphere is lower than 1×10-14Pa, oxidation will not occur during the sintering process.
When the temperature is lowered, in order to prevent oxidation, the oxygen partial pressure in the atmosphere is required to be even low It can also ensure that AsaloyCrM sintered at 1125℃ will not oxidize at 1×10-14Pa. The above calculation has been confirmed by experimental data.
Please keep the source and address of this article for reprinting: The Atmosphere Control During Sintering Process Of Sintered Steel And Its Performance
Minghe Die Casting Company are dedicated to manufacture and provide quality and high performance Casting Parts(metal die casting parts range mainly include Thin-Wall Die Casting,Hot Chamber Die Casting,Cold Chamber Die Casting),Round Service(Die Casting Service,Cnc Machining,Mold Making,Surface Treatment).Any custom Aluminum die casting, magnesium or Zamak/zinc die casting and other castings requirements are welcome to contact us.
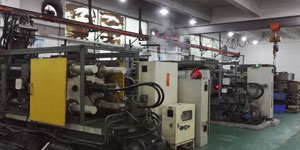
Under the control of ISO9001 and TS 16949,All processes are carried out through hundreds of advanced die casting machines, 5-axis machines, and other facilities, ranging from blasters to Ultra Sonic washing machines.Minghe not only has advanced equipment but also have professional team of experienced engineers,operators and inspectors to make the customer’s design come true.
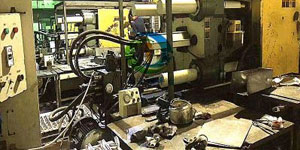
Contract manufacturer of die castings. Capabilities include cold chamber aluminum die casting parts from 0.15 lbs. to 6 lbs., quick change set up, and machining. Value-added services include polishing, vibrating, deburring, shot blasting, painting, plating, coating, assembly, and tooling. Materials worked with include alloys such as 360, 380, 383, and 413.
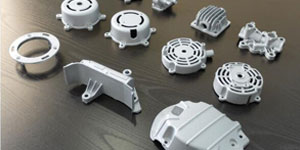
Zinc die casting design assistance/concurrent engineering services. Custom manufacturer of precision zinc die castings. Miniature castings, high pressure die castings, multi-slide mold castings, conventional mold castings, unit die and independent die castings and cavity sealed castings can be manufactured. Castings can be manufactured in lengths and widths up to 24 in. in +/-0.0005 in. tolerance.
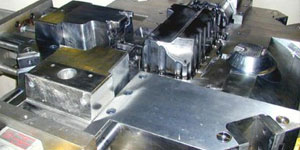
ISO 9001: 2015 certified manufacturer of die cast magnesium, Capabilities include high-pressure magnesium die casting up to 200 ton hot chamber & 3000 ton cold chamber, tooling design, polishing, molding, machining, powder & liquid painting, full QA with CMM capabilities, assembly, packaging & delivery.
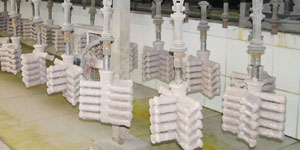
ITAF16949 certified. Additional Casting Service Include investment casting,sand casting,Gravity Casting, Lost Foam Casting,Centrifugal Casting,Vacuum Casting,Permanent Mold Casting,.Capabilities include EDI, engineering assistance, solid modeling and secondary processing.
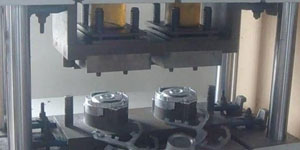
Casting Industries Parts Case Studies for: Cars, Bikes, Aircraft, Musical instruments, Watercraft, Optical devices, Sensors, Models, Electronic devices, Enclosures, Clocks, Machinery, Engines, Furniture, Jewelry, Jigs, Telecom, Lighting, Medical devices, Photographic devices, Robots, Sculptures, Sound equipment, Sporting equipment, Tooling, Toys and more.
What Can we help you do next?
∇ Go To Homepage For Die Casting China
→Casting Parts-Find out what we have done.
→Ralated Tips About Die Casting Services
By Minghe Die Casting Manufacturer |Categories: Helpful Articles |Material Tags: Aluminum Casting, Zinc Casting, Magnesium Casting, Titanium Casting, Stainless Steel Casting, Brass Casting,Bronze Casting,Casting Video,Company History,Aluminum Die Casting |Comments Off