The Calculation Method Of Mold Making Price
1. Empirical Calculation Method
- Mold price = material cost + design fee + processing fee and profit + value-added tax + mold trial fee + packaging and transportation fee
- The ratios are usually:
- Material cost: materials and standard parts account for 15%-30% of the total cost of the mold;
- Processing fee and profit: 30%-50%;
- Design fee: 10%-15% of the total mold cost;
- Trial mold: large and medium-sized molds can be controlled within 3%, and precision molds can be controlled within 5%;
- Packing and transportation fee: can be calculated according to actual or 3%;
- VAT: 17%
2. Material Coefficient Method
According to the mold size and material price, the mold material cost can be calculated.
Mold price=(6~10)*material cost
Forging die, plastic die=6*material cost
Die casting mold=10*material cost
Mould quotation estimate
- 1. First of all, it depends on the customer's requirements, because the requirements determine the choice of materials and heat treatment process.
- 2. Choose the material and draw out a rough mold plan, from which calculate the weight of the mold (calculate the price of the mold core material and the mold base material) and the cost of heat treatment. (Both are raw weight)
- 3. Processing cost. According to the complexity of the mold core, the processing cost and the price of the mold core material are generally 1.5~3:1, and the processing cost of the mold base is generally 1:1.
- 4. The risk cost is 10% of the above total price.
- 5. Tax
- 6. The design cost is 10% of the total price of the mold.
Mould quotation strategy and settlement method
The quotation and settlement of the mold is the continuation and result after the evaluation of the mold. From the evaluation of the mold to the quotation of the mold, it is only the first step, and the ultimate goal of the mold is to settle the mold after the mold is manufactured and delivered, and form the final mold settlement price. In this process, people always hope that mold valuation = mold price = mold settlement price. In actual operation, these four prices are not completely equal, and fluctuation error values may occur. This is the issue to be discussed below. ?
After the mold is appraised, it needs to be processed appropriately and compiled into a mold quotation, which is the basis for signing the mold processing contract. Through repeated negotiations and discussions, a mold price recognized by both parties was finally formed and a contract was signed. Only then can the mold processing be officially started.
Mold valuation and quotation, quotation and mold price?
After the mold is evaluated, it cannot be used as a quotation immediately. Generally speaking, it is necessary to conduct a comprehensive analysis based on market conditions, customer psychology, competitors, status and other factors, to properly organize the valuation, and make the first quotation with an increase of 10-30% on the basis of the valuation. After bargaining, the quotation can be lowered according to the actual situation. However, when the negotiated quotation of the mold is less than 10% of the estimated price, it is necessary to re-improve and refine the estimation of the mold. Under the condition of guaranteeing the profit, the mold processing contract is signed, and the mold price is finally determined. The price of the mold is the price approved by both parties and signed in the contract.
The mold price formed at this time may be higher or lower than the estimated price. When the negotiated mold price is lower than the guaranteed cost of the mold, the mold requirements, conditions, plans, etc. need to be revised to reduce some requirements in order to reduce the mold cost. After re-estimation, the mold price contract can be signed. It should be pointed out that molds are specialized products with high technological content and should not be used at low prices or even at a loss to cater to customers. Instead, it should be high-quality at a better price, and the quality, precision, and life of the mold should be the first priority, and the price of the mold should not be overemphasized, otherwise it will easily cause misleading actions. It is more difficult to guarantee the quality, precision and life of the mold when it is pursued at a low price. Cheap is generally not what the mold industry does. However, when mold manufacturing and product development and production are in the same accounting unit or there is an economic interest relationship, in this case, the price of the mold should be quoted at its cost price.
Please keep the source and address of this article for reprinting:The Calculation Method Of Mold Making Price
Minghe Die Casting Company are dedicated to manufacture and provide quality and high performance Casting Parts(metal die casting parts range mainly include Thin-Wall Die Casting,Hot Chamber Die Casting,Cold Chamber Die Casting),Round Service(Die Casting Service,Cnc Machining,Mold Making,Surface Treatment).Any custom Aluminum die casting, magnesium or Zamak/zinc die casting and other castings requirements are welcome to contact us.
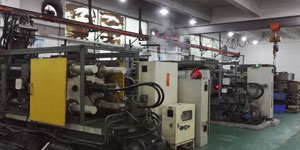
Under the control of ISO9001 and TS 16949,All processes are carried out through hundreds of advanced die casting machines, 5-axis machines, and other facilities, ranging from blasters to Ultra Sonic washing machines.Minghe not only has advanced equipment but also have professional team of experienced engineers,operators and inspectors to make the customer’s design come true.
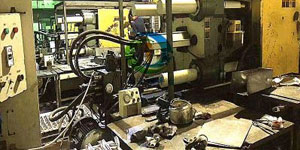
Contract manufacturer of die castings. Capabilities include cold chamber aluminum die casting parts from 0.15 lbs. to 6 lbs., quick change set up, and machining. Value-added services include polishing, vibrating, deburring, shot blasting, painting, plating, coating, assembly, and tooling. Materials worked with include alloys such as 360, 380, 383, and 413.
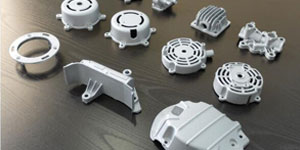
Zinc die casting design assistance/concurrent engineering services. Custom manufacturer of precision zinc die castings. Miniature castings, high pressure die castings, multi-slide mold castings, conventional mold castings, unit die and independent die castings and cavity sealed castings can be manufactured. Castings can be manufactured in lengths and widths up to 24 in. in +/-0.0005 in. tolerance.
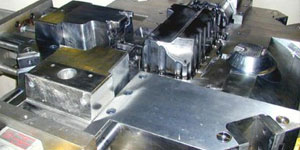
ISO 9001: 2015 certified manufacturer of die cast magnesium, Capabilities include high-pressure magnesium die casting up to 200 ton hot chamber & 3000 ton cold chamber, tooling design, polishing, molding, machining, powder & liquid painting, full QA with CMM capabilities, assembly, packaging & delivery.
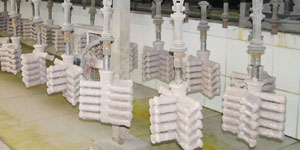
ITAF16949 certified. Additional Casting Service Include investment casting,sand casting,Gravity Casting, Lost Foam Casting,Centrifugal Casting,Vacuum Casting,Permanent Mold Casting,.Capabilities include EDI, engineering assistance, solid modeling and secondary processing.
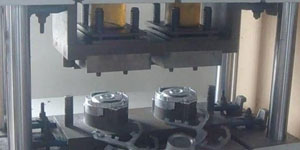
Casting Industries Parts Case Studies for: Cars, Bikes, Aircraft, Musical instruments, Watercraft, Optical devices, Sensors, Models, Electronic devices, Enclosures, Clocks, Machinery, Engines, Furniture, Jewelry, Jigs, Telecom, Lighting, Medical devices, Photographic devices, Robots, Sculptures, Sound equipment, Sporting equipment, Tooling, Toys and more.
What Can we help you do next?
∇ Go To Homepage For Die Casting China
→Casting Parts-Find out what we have done.
→Ralated Tips About Die Casting Services
By Minghe Die Casting Manufacturer |Categories: Helpful Articles |Material Tags: Aluminum Casting, Zinc Casting, Magnesium Casting, Titanium Casting, Stainless Steel Casting, Brass Casting,Bronze Casting,Casting Video,Company History,Aluminum Die Casting |Comments Off