The Causes Of Bearing Corrosion
External Manifestations Of Bearing Corrosion
- Flake Embroidered Yellow: It is characterized by large area, shallow depth, and easy to find. The main cause of this kind of rust is moisture, dust and SO2, H2S, CO2 and other gases in the atmosphere. In the hot and humid summer, especially in places with large air flow, this kind of bearing is easy to produce on the periphery of the bearing stack. Rust.
- Honeycomb pitting: It is characterized by large lumps, prominent surface, loose yellow color, yellow rust on the surface, easy to wipe off, but honeycomb black rust pits under it. The main reason for this kind of corrosion is that the residual salt is not cleaned or the parts have water droplets.
- Fingerprint rust: When holding bearings and parts with bare hands, the rust is caused by sweat on the surface. There are lactic acid, sodium chloride, moisture, etc. in hand sweat, especially in summer, and the rust is in the shape of fingerprint rust.
- Yellow seal rust: It is characterized by shallow depth and can be easily wiped off with emery cloth. There is no rust pit scar after rubbing. This kind of yellow seal rust is prone to occur on the end face of the stacking ferrule. The main working fluid has poor overlap, and the overlapped surface of the ferrule is corroded by the concentration difference caused by uneven inflation.
- Black seal rust: It can be wiped off at first, but rust pits will appear over time. This kind of rust is caused by poor neutralization after the acid is written, or the acid liquid is stained on the product, or because the packaging paper has poor rust resistance, this black rust will be produced on the contact with the packaging box after being damp.
- Black dots: There are many forms of black dots, which are characterized by small area and large depth. They are not easy to observe in sunlight and can be seen clearly under light or magnifying glass. There is a black spot that is only as big as a small needle tip, and the outer color is light, and the middle is a circular black hole. This kind of rust cannot be wiped off with general gauze. The reason for the black spot is that the surface of the part is stained with grinding wheels and cannot be cleaned, especially the rubber Grinding wheels and resin grinding wheel chips produce black spots faster. When the parts have residual magnetism or electrostatic adsorption of grinding wheel chips, black spots will be produced faster. In addition, dust and impurities stick to the metal surface and cause electrochemical corrosion to produce irregular black spots of rust.
- Corrosion caused by bumps, scratches, abrasions, and blank marks: Defects caused by the "three scratches" (bumps, scratches, and abrasions) usually seen on the bearing surface should be distinguished from rust. But the damaged part is particularly easy to cause rust, because the three wounds and the embryo print have wounds, the oxide film is destroyed and the potential is more negative to become the anode (public account: pump housekeeper), the unwound becomes the cathode, and the three wounds are easy to be damaged. Contamination accelerates electrochemical corrosion, so the wounds often turn black. For example, when working from the surface of the surface grinder disk, it is easy to cause the grinding wheel chip pad injury and produce small spots on the surface, which will become small black spots over time . When the octagonal tire card is used for the grinding ring, it is easy to produce embryo marks. At that time, it will be wiped off with a cloth. If it is not wiped for a long time, black embryo marks will occur. Automatic centerless grinder When the mold is not suitable, the end face of the ferrule is abraded to produce many small spots, which will turn black after a long time.
The Detail Causes Of Bearing Corrosion
- In the process of bearing production, some enterprises did not strictly follow the cleaning and rust prevention regulations and oil seal rust prevention packaging requirements for the bearing parts in the process of processing and the finished bearing products after assembly. If the turnover time of the ferrule is too long during the turnover process, the outer circle of the outer ring is in contact with corrosive liquid or gas, etc.
- The quality of anti-rust lubricating oil, cleaning kerosene and other products used in production by some enterprises cannot meet the requirements of process technology regulations.
- Some enterprises have poor environmental conditions, high levels of harmful substances in the air, and too small a turnover space, which makes it difficult to carry out effective anti-rust treatment. Coupled with the hot weather, there are also phenomena such as violations of anti-rust regulations by production workers.
- Bearing packaging materials such as rust-proof paper, nylon paper (bags) and plastic tubes of some companies do not meet the requirements of anti-rust packaging for rolling bearing oil seals, which is also one of the factors that cause rust.
- The turning allowance and grinding allowance of the bearing rings of some enterprises are too small. One of the reasons is that the oxide scale and decarburization layer on the outer circle cannot be completely removed.
The Main Factors Affecting Atmospheric Corrosion
1.Relative Humidity Of The Atmosphere
Absolute humidity: the weight of water vapor per unit volume of air (g/m3)
Relative humidity: The ratio of the water vapor content in the air to the saturated water vapor content of the air at the same temperature, expressed as a percentage.
The relative humidity determines whether a water film is formed on the metal, and the thickness and retention time of the water film. The higher the relative humidity and the higher the humidity in the air, the faster the metal corrosion.
The critical relative humidity of steel is 65%. Below the critical humidity, the rate of metal corrosion is very slow. Once the humidity exceeds the critical humidity, the rate of metal corrosion will rise suddenly.
2.Temperature
Generally, the speed of a chemical reaction increases when the temperature rises. The metal interacts with the oxygen and moisture in the moist air to reach above the critical temperature, and the temperature changes cause condensation on the metal surface, resulting in corrosion. When the relative humidity is lower than the critical humidity of the metal, the influence of temperature on atmospheric corrosion is small; when the relative humidity reaches the critical humidity of the metal, the influence of temperature is very obvious, the temperature increases, and the reaction speed increases.
3.The Influence Of Oxygen
The following reaction formula is usually used to simply express rust:
It can be seen from the reaction formula: Without oxygen, atmospheric corrosion of metals will not occur. In some special cases, the concentration of oxygen on the metal surface is different, which will produce a special form of differential gas battery. For example: on the overlapping surface, that is, when the metal surface is in close contact with another surface, the edge of the contact surface will not rust, but there will be cloud-like shadows or rust away from the edge. The corrosion products on steel are often gray or black (iron oxide).
4.The Influence Of Pollutants In The Atmosphere
In addition to oxygen and water vapor, the atmosphere also contains various pollutants. Such as carbon dioxide, nitrogen oxides, carbon dioxide and other gases and solid dust. These pollutants will condense on the metal surface together with the water mist in the air, and dissolve in water to produce the following results: various non-metal oxides dissolve in water and become acids, which will destroy the passivation film on the metal surface; various electrolytes increase the water film The conductivity; reduce the critical relative humidity of the metal. (For example, when the atmosphere contains 0.01% SO2, the critical humidity can be reduced from 70% to 50%. In a humid atmosphere, one SO2 molecule can turn dozens of iron atoms into oxides).
Common Methods To Prevent Bearing Corrosion
- The bearing is kept clean and isolated from the air
- Correct selection of corrosion-resistant materials
- Surface treatment
Please keep the source and address of this article for reprinting:The Causes Of Bearing Corrosion
Minghe Die Casting Company are dedicated to manufacture and provide quality and high performance Casting Parts(metal die casting parts range mainly include Thin-Wall Die Casting,Hot Chamber Die Casting,Cold Chamber Die Casting),Round Service(Die Casting Service,Cnc Machining,Mold Making,Surface Treatment).Any custom Aluminum die casting, magnesium or Zamak/zinc die casting and other castings requirements are welcome to contact us.
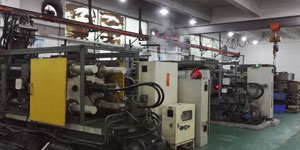
Under the control of ISO9001 and TS 16949,All processes are carried out through hundreds of advanced die casting machines, 5-axis machines, and other facilities, ranging from blasters to Ultra Sonic washing machines.Minghe not only has advanced equipment but also have professional team of experienced engineers,operators and inspectors to make the customer’s design come true.
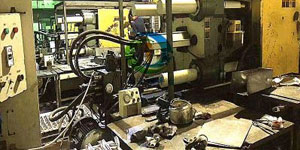
Contract manufacturer of die castings. Capabilities include cold chamber aluminum die casting parts from 0.15 lbs. to 6 lbs., quick change set up, and machining. Value-added services include polishing, vibrating, deburring, shot blasting, painting, plating, coating, assembly, and tooling. Materials worked with include alloys such as 360, 380, 383, and 413.
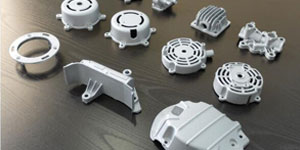
Zinc die casting design assistance/concurrent engineering services. Custom manufacturer of precision zinc die castings. Miniature castings, high pressure die castings, multi-slide mold castings, conventional mold castings, unit die and independent die castings and cavity sealed castings can be manufactured. Castings can be manufactured in lengths and widths up to 24 in. in +/-0.0005 in. tolerance.
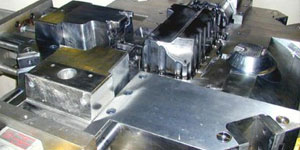
ISO 9001: 2015 certified manufacturer of die cast magnesium, Capabilities include high-pressure magnesium die casting up to 200 ton hot chamber & 3000 ton cold chamber, tooling design, polishing, molding, machining, powder & liquid painting, full QA with CMM capabilities, assembly, packaging & delivery.
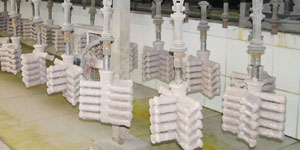
ITAF16949 certified. Additional Casting Service Include investment casting,sand casting,Gravity Casting, Lost Foam Casting,Centrifugal Casting,Vacuum Casting,Permanent Mold Casting,.Capabilities include EDI, engineering assistance, solid modeling and secondary processing.
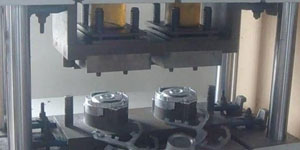
Casting Industries Parts Case Studies for: Cars, Bikes, Aircraft, Musical instruments, Watercraft, Optical devices, Sensors, Models, Electronic devices, Enclosures, Clocks, Machinery, Engines, Furniture, Jewelry, Jigs, Telecom, Lighting, Medical devices, Photographic devices, Robots, Sculptures, Sound equipment, Sporting equipment, Tooling, Toys and more.
What Can we help you do next?
∇ Go To Homepage For Die Casting China
→Casting Parts-Find out what we have done.
→Ralated Tips About Die Casting Services
By Minghe Die Casting Manufacturer |Categories: Helpful Articles |Material Tags: Aluminum Casting, Zinc Casting, Magnesium Casting, Titanium Casting, Stainless Steel Casting, Brass Casting,Bronze Casting,Casting Video,Company History,Aluminum Die Casting |Comments Off