The Causes Of Common Defects In Gray Cast Iron Cylinder Blocks
The emergence of water glass has a history of more than 300 years, but as a binder for casting and core making, it was not until 1947 that the water glass sand process with CO2 as a hardening agent was developed by Dr. L. Petrzela of the Czech Republic. of.
For more than half a century, people have gone through four major turning processes in understanding the hardening mechanism of sodium silicate sand in continuous research and exploration, namely:
- 1) The theory of CO2 pure chemical hardening by Professor Lias (Лясс A.M.) of the former Soviet Union in the 1950s. He divided the hardening process into the decomposition of silicate, the formation of silica gel, and the partial loss of water from the silica gel. He mistakenly believed that the precipitation of silicic acid and the formation of silica gel were the strength of CO2 hardened sodium silicate sand. Sole source
- 2) By the 1960s, the hardening process of CO2 water glass sand by Worthington R was considered to be a combination of chemical and physical hardening methods, that is, sodium silicate decomposed into free silicic acid under the catalysis of CO2, and then condensed into silicon gel. The dehydration of silicone gel will lead to "silicone gel bonding", which is a kind of "chemical hardening"; the dehydration of unreacted water glass will lead to "vitreous bonding", which belongs to "physical hardening". But he mistakenly believes that chemical hardening is an efficient and rapid hardening measure, while ignoring the important role of physical hardening;
- 3) By the early 1990s, the CO2 hardened water glass made by Zhu Chunxi and others in my country was essentially the theory of "physical hardening". He believes that the water glass sand blowing CO2 hardening must be under a very special condition, that is, the water glass is coated on the surface of the sand particles to form a film with a thickness of only a few microns, which can create good dehydration conditions and promote the rapid solidification of the water glass. , So it is said that "the hardening of water glass is essentially physical hardening." The disadvantage of this view is that it still follows the erroneous view that free silicic acid is precipitated when sodium silicate reacts with CO2.
- 4) By the end of the 1990s, Zhu Chunxi and others based on the theory that CO2 hardening belongs to physical hard chemistry, after further in-depth research, they proposed that hardened water glass is a kind of "dehydrated high modulus water glass". The theory, that is, the silicic acid generated by the reaction cannot be precipitated in a free state, but is re-dissolved in the unreacted water glass, increasing the modulus of the latter to realize the hardening of the water glass. For example, when organic vinegar is used to harden sodium silicate sand, a hardened high-modulus sodium silicate film with uniform modulus from the surface and the inside can be obtained, which is close to M=3.45. When CO2 is used to harden the water glass, a hardened high modulus water glass film with a gradually decreasing modulus from the surface and the inside, with an average M close to 3.79 is obtained.
Therefore, hardened water glass is a kind of dehydrated high modulus water glass, which can be solidified through loss of alkali and water.
By 2008, German C. Wallenhorst et al. believed that the hardening reaction mode of sodium silicate sand can be divided into the following two types, as shown in Figure 1.
1.1 Mode A
In the presence of acidic solution or curing agent (CO2 or organic ester), the growth rate of colloidal particles in water glass is extremely slow, but directly aggregates into a three-dimensional network gel.
1.2 Mode B
Under the condition of an alkaline solution without curing agent (under heating), the colloidal particles first grow up and form a sol structure; and the individual sol particles can form a three-dimensional network structure only under the crosslinking action of the accelerator.
Individual silicic acid particles can grow into large colloidal particles (mode B), or they can aggregate into chain and network gel structures (mode A). In these two hardening reaction modes, the chemical reaction mechanism is the same-through the condensation reaction between single silanol functional groups, dehydration and connection to a new siloxane compound.
"It can be seen that the hardening reaction mode of water glass mainly depends on the pH value of the binder solution. In the low PH value (in the presence of CO2 or organic ester curing agent) silicic acid aqueous solution, it is beneficial to the hardening reaction mode A. At this time, the hardening reaction speed is very slow, and the colloidal particles aggregate with each other to form a branched, porous gel structure.
When the pH value of the silicic acid aqueous solution>7 (no CO2 or organic esters and heat-initiated), the hardening reaction mode B proceeds to form a large-particle sol structure. In the case of a solution with a high pH value, the molecules grow so fast that the hardening reaction is mainly due to the continuous growth of colloidal particles in addition to the formation of a gel structure. In fact, the phenomenon of aggregation into a network structure is inhibited.
When the water glass sand with accelerator is heated and hardened, the hardening reaction mechanism is as follows:
After the core sand water glass is heated and stimulated, it proceeds according to the hardening reaction mode B (see Figure 1), and the colloidal particles grow up and form a sol structure. At this time, as the hardening reaction progresses, either a substantially uniform granular structure or a structure with some defects may be formed. The number of defects will directly affect its subsequent use performance, such as the moisture resistance of the sand core.
When the water glass sand core is hardened by CO2 gas, or when the organic ester is hardened, a single sol ion will proceed according to the hardening reaction mode A, and the colloidal particles will aggregate and bond to each other to form a gel structure. If there is no curing agent in the silicic acid alkaline solution, the silica gel particles can stably exist in the alkaline solution. This is because the surface of the colloidal particles has the electrical effect of the electric double layer of positively charged sodium ions. The result of colloidal particles repelling each other and not being combined. If there is an inorganic accelerator in the hardening process of sodium silicate sand, it can act as a cross-linking agent between colloidal particles, that is, the inorganic accelerator can connect individual sol particles to each other through the active reactive groups on its surface. Together, a three-dimensional network of silicate skeleton is formed, so that the binder is quickly solidified and the sand particles are bonded and formed.
If no inorganic accelerator is added, the formation of the silicate skeleton of the network structure is very slow during the secondary hardening process, and the prepared sand core exhibits shortcomings such as low instantaneous strength and poor moisture resistance.
Through the analysis of the above water glass hardening mechanism, it can be seen that although there are various hardening methods for sodium silicate sand, they can be conventionally divided into physical hardening and chemical hardening, and the hardening mechanism is consistent and unified. of. That is to say, the organic ester hardening method of sodium silicate sand has exactly the same hardening mechanism as the CO2 hardening method, which is mainly based on the physical hardening of unreacted water glass dehydration, which is the main reason for the strength of the mold (core) sand; to generate silicon The chemical hardening of the gel is supplemented by the rapid solidification of the sodium silicate sand, the establishment of initial strength, the improvement of the moisture resistance and storage stability of the sand, and the synergistic process of chemical hardening and physical hardening.
Based on the in-depth analysis of the hardening mechanism of the above sodium silicate sand with different hardening methods (CO2 method, organic ester method and heating + accelerator method, etc.), and explore the influence of the water glass bonding strength and moisture resistance from the molecular structure level The main influencing factors between water glass and collapsible performance, so as to change the structure and morphology of water glass from a molecular perspective, and develop a new heating hardening + accelerator water glass sand new process, so as to improve the bonding strength of water glass sand. The purpose of increasing its moisture resistance and improving its collapsing performance is to continuously improve and improve the process performance of sodium silicate sand while continuously overcoming its inherent shortcomings, thus becoming the most promising green casting in the 21st century. Clean the adhesive.
2 Process performance of new inorganic binder sand
2.1 Bond strength performance
By preparing amorphous phosphate and using it to modify the water glass, the bonding strength of the inorganic binder is improved.
In order to further improve the bonding strength of sodium silicate sand, an organic accelerator has been developed. Through chemical cross-linking and hardening, the instant strength of sodium silicate sand can be greatly improved. When the organic accelerator is added at 1.5%, the instant tensile strength The strength can reach 1.8MPa.
2.2 Moisture resistance of core sand
Generally speaking, the strength of water glass sand hardened by hot air will gradually decrease in a humid environment. In order to improve the moisture resistance of sodium silicate sand, on the one hand, the residual moisture content in the sand is completely removed after hardening, and on the other hand, the method of chemical cross-linking and hardening is used. When the accelerator is added to 1.5%, the tensile strength of sodium silicate sand will not decrease, but will increase slightly after being placed at 20°C and 80% relative humidity for 24 hours
2.3 Flow properties of core sand
The surface tension of the water glass itself is relatively large, which makes the wettability between the water glass and the silica sand poor, and the viscosity of the water glass for casting is generally too large, so that the viscosity of the water glass sand after mixing is very large, and the sand particles adhere to the water glass. The movement resistance is very large, resulting in poor fluidity of the sodium silicate sand, and ultimately greatly reducing the compactness of the shot core. In this experiment, surfactants and solid lubricants were added to greatly improve the fluidity of molding sand.
Based on the use of surfactants and solid lubricants, this experiment developed a spherical accelerator, which greatly improved the fluidity of water glass sand.
Please keep the source and address of this article for reprinting:The Causes Of Common Defects In Gray Cast Iron Cylinder Blocks
Minghe Die Casting Company are dedicated to manufacture and provide quality and high performance Casting Parts(metal die casting parts range mainly include Thin-Wall Die Casting,Hot Chamber Die Casting,Cold Chamber Die Casting),Round Service(Die Casting Service,Cnc Machining,Mold Making,Surface Treatment).Any custom Aluminum die casting, magnesium or Zamak/zinc die casting and other castings requirements are welcome to contact us.
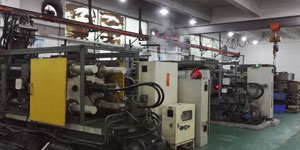
Under the control of ISO9001 and TS 16949,All processes are carried out through hundreds of advanced die casting machines, 5-axis machines, and other facilities, ranging from blasters to Ultra Sonic washing machines.Minghe not only has advanced equipment but also have professional team of experienced engineers,operators and inspectors to make the customer’s design come true.
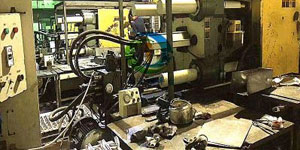
Contract manufacturer of die castings. Capabilities include cold chamber aluminum die casting parts from 0.15 lbs. to 6 lbs., quick change set up, and machining. Value-added services include polishing, vibrating, deburring, shot blasting, painting, plating, coating, assembly, and tooling. Materials worked with include alloys such as 360, 380, 383, and 413.
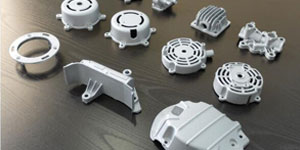
Zinc die casting design assistance/concurrent engineering services. Custom manufacturer of precision zinc die castings. Miniature castings, high pressure die castings, multi-slide mold castings, conventional mold castings, unit die and independent die castings and cavity sealed castings can be manufactured. Castings can be manufactured in lengths and widths up to 24 in. in +/-0.0005 in. tolerance.
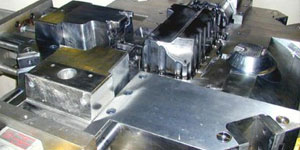
ISO 9001: 2015 certified manufacturer of die cast magnesium, Capabilities include high-pressure magnesium die casting up to 200 ton hot chamber & 3000 ton cold chamber, tooling design, polishing, molding, machining, powder & liquid painting, full QA with CMM capabilities, assembly, packaging & delivery.
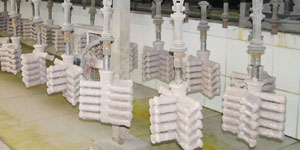
ITAF16949 certified. Additional Casting Service Include investment casting,sand casting,Gravity Casting, Lost Foam Casting,Centrifugal Casting,Vacuum Casting,Permanent Mold Casting,.Capabilities include EDI, engineering assistance, solid modeling and secondary processing.
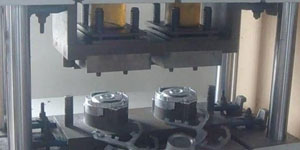
Casting Industries Parts Case Studies for: Cars, Bikes, Aircraft, Musical instruments, Watercraft, Optical devices, Sensors, Models, Electronic devices, Enclosures, Clocks, Machinery, Engines, Furniture, Jewelry, Jigs, Telecom, Lighting, Medical devices, Photographic devices, Robots, Sculptures, Sound equipment, Sporting equipment, Tooling, Toys and more.
What Can we help you do next?
∇ Go To Homepage For Die Casting China
→Casting Parts-Find out what we have done.
→Ralated Tips About Die Casting Services
By Minghe Die Casting Manufacturer |Categories: Helpful Articles |Material Tags: Aluminum Casting, Zinc Casting, Magnesium Casting, Titanium Casting, Stainless Steel Casting, Brass Casting,Bronze Casting,Casting Video,Company History,Aluminum Die Casting |Comments Off