The Causes Of Hot And Cold Cracks When Casting Wheels
Aluminum alloy wheels have many characteristics that steel wheels cannot match. Therefore, aluminum alloy wheels have been widely used in cars, motorcycles and other vehicles. By 2002, the loading rate of aluminum alloy wheels for cars in China was close to 45%. Due to the high quality requirements of automobile wheels, its structure is suitable for low-pressure precision casting, and the demand is large, it has greatly promoted the development of low-pressure casting technology. At present, low-pressure casting has become the main process method for the production of aluminum alloy wheels, and most of China's aluminum alloy wheel manufacturers use this process for production.
The cracks of the low-pressure precision casting aluminum alloy wheel hub are mainly caused by the stress concentration, or the crack caused by uneven force when the hub is ejected, or the liquid solidification at the riser pipe. Cracks are generally divided into cold cracks and hot cracks.
Cold cracking refers to the cracks formed when the alloy is below its solidus temperature. In layman's terms, cold cracking is caused when the precision casting stress acting on the casting exceeds the degree allowed by the strength or plasticity of the casting itself when the precision casting is cooled to a low temperature. Cold cracks mostly appear on the surface of castings, with slight oxidation on the surface of the cracks; while hot cracks are usually considered to be generated during the solidification of the alloy. Due to the heat transfer of the mold wall, the castings always start to solidify from the surface. When a large number of branches appear on the surface of the casting and overlap to form a complete skeleton, the casting will appear solid state shrinkage (often expressed as linear shrinkage).
However, there is still a layer of liquid metal film (liquid film) between the dendrites at this time. If the shrinkage of the casting is not hindered, the dendrite layer is not affected by force and can shrink freely, and it will not appear. stress. When the shrinkage of the dendrite layer is hindered, it cannot shrink freely or is under the action of tensile force, and tensile stress will appear. At this time, the liquid film between the dendrites will be deformed by stretching.
When the tensile stress exceeds the strength limit of the liquid film, the dendrites will be pulled apart. However, there is still some liquid metal around the cracked part. If the liquid film is pulled apart very slowly and there is enough liquid around and flows into the cracked part in time, the cracked part will be filled and "healed". Precision casting products will not show hot cracks. If the tensile cracks cannot be "healed" again, hot cracks will appear in the precision casting products. The surface of the thermal fracture is strongly oxidized, showing a dark or black color with no metallic luster.
Please keep the source and address of this article for reprinting:The Causes Of Hot And Cold Cracks When Casting Wheels
Minghe Die Casting Company are dedicated to manufacture and provide quality and high performance Casting Parts(metal die casting parts range mainly include Thin-Wall Die Casting,Hot Chamber Die Casting,Cold Chamber Die Casting),Round Service(Die Casting Service,Cnc Machining,Mold Making,Surface Treatment).Any custom Aluminum die casting, magnesium or Zamak/zinc die casting and other castings requirements are welcome to contact us.
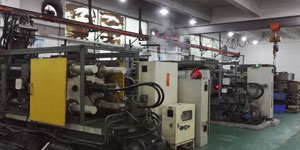
Under the control of ISO9001 and TS 16949,All processes are carried out through hundreds of advanced die casting machines, 5-axis machines, and other facilities, ranging from blasters to Ultra Sonic washing machines.Minghe not only has advanced equipment but also have professional team of experienced engineers,operators and inspectors to make the customer’s design come true.
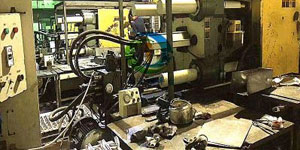
Contract manufacturer of die castings. Capabilities include cold chamber aluminum die casting parts from 0.15 lbs. to 6 lbs., quick change set up, and machining. Value-added services include polishing, vibrating, deburring, shot blasting, painting, plating, coating, assembly, and tooling. Materials worked with include alloys such as 360, 380, 383, and 413.
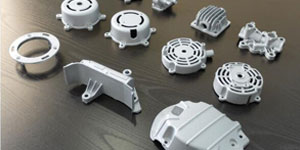
Zinc die casting design assistance/concurrent engineering services. Custom manufacturer of precision zinc die castings. Miniature castings, high pressure die castings, multi-slide mold castings, conventional mold castings, unit die and independent die castings and cavity sealed castings can be manufactured. Castings can be manufactured in lengths and widths up to 24 in. in +/-0.0005 in. tolerance.
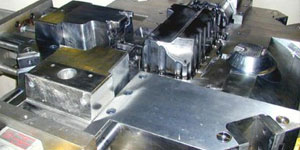
ISO 9001: 2015 certified manufacturer of die cast magnesium, Capabilities include high-pressure magnesium die casting up to 200 ton hot chamber & 3000 ton cold chamber, tooling design, polishing, molding, machining, powder & liquid painting, full QA with CMM capabilities, assembly, packaging & delivery.
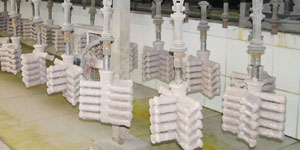
ITAF16949 certified. Additional Casting Service Include investment casting,sand casting,Gravity Casting, Lost Foam Casting,Centrifugal Casting,Vacuum Casting,Permanent Mold Casting,.Capabilities include EDI, engineering assistance, solid modeling and secondary processing.
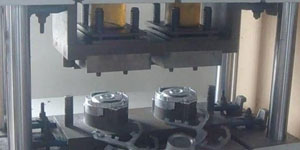
Casting Industries Parts Case Studies for: Cars, Bikes, Aircraft, Musical instruments, Watercraft, Optical devices, Sensors, Models, Electronic devices, Enclosures, Clocks, Machinery, Engines, Furniture, Jewelry, Jigs, Telecom, Lighting, Medical devices, Photographic devices, Robots, Sculptures, Sound equipment, Sporting equipment, Tooling, Toys and more.
What Can we help you do next?
∇ Go To Homepage For Die Casting China
→Casting Parts-Find out what we have done.
→Ralated Tips About Die Casting Services
By Minghe Die Casting Manufacturer |Categories: Helpful Articles |Material Tags: Aluminum Casting, Zinc Casting, Magnesium Casting, Titanium Casting, Stainless Steel Casting, Brass Casting,Bronze Casting,Casting Video,Company History,Aluminum Die Casting |Comments Off