The Causes Of Wrinkles Formed On Precision Castings Produced Surface By Lost Foam
Using lost foam to produce precision casting, the carbon content of iron castings is close to saturation, and the concentration gradient of carbon between gas phase and precision casting is very small, and free carbon in the gas phase is not easy to migrate and diffuse to the surface of the casting. Therefore, surface carburization rarely occurs when casting iron castings.
For iron castings, surface wrinkles are the most common defect. Because free carbon does not easily penetrate into the surface of the casting, but is deposited on the surface of precision casting and molds. During this pouring, the ES type is in contact with the molten metal and decomposes into three components: gaseous, liquid and P-mode solid.
The gas phase is mainly composed of CO, CO: 2, H, methane, styrene and its derivatives; the liquid phase is mainly composed of liquid hydrocarbon groups such as benzene, toluene, styrene and glassy polystyrene; the solid phase is mainly composed of polystyrene thermal Decomposition of the bright carbon and coke residue group formed.
- 1) The residual solid phase carbon between the metal surface and the mold forms a wrinkle defect. The solid high-temperature carbon accumulates locally, causing the surface of the casting to be rough, which is a wrinkle defect. The bright carbon in the phase forms a melt adhesive with the gas and liquid phase, and the liquid phase will also decompose at a certain speed to form a secondary gas and solid phase. Dimers, trimers and repolymers in the liquid tend to appear as a viscous pitch-like liquid. This liquid decomposition product remains on the inside of the coating, part of it is absorbed by the coating, and a part of a corrugated corrugated skin) b) The nodular corrugated skin forms a thin film between the casting and the coating, and this part of the thin film is reducing (O)C The formation of flakes or scaly crystalline residual carbon in the atmosphere, that is, the formation of wrinkled skin. Some of them gather on the surface of the casting and are irregularly coarse-grained, forming a drop-knob-like wrinkled skin with slag-like wrinkles, which is mainly due to the polystyrene solid product that has not been vaporized in the molten metal during the pouring process. After the precision casting is cooled and solidified, these soot-like carbon soot inclusions form irregular slag-like wrinkle defects on the surface of the casting.
- 2) In the "" part of the molten metal flow, the residual liquid phase is due to surface tension) cold end e) cold-separated corrugated skin d) slag-like corrugated skin shrinks to form a corrugated skin defect ESP produces cracked products or tar-like residue in the corrugated skin During the defect process, it softens and shrinks, thickening the thin honeycomb structure membrane in the original foam plastic thousands of times, destroying the foam structure and forming a thick dura mater. This liquid or hard-film polystyrene residue floats on the molten metal surface in a glassy state or adheres to the mold wall. Therefore, these are maintained at the boundary J: Wrinkled skin defects can be divided into corrugated corrugated skin, bead-shaped corrugated skin, cold-separated corrugated skin, and slag-like corrugated skin according to appearance. Generally, corrugated corrugated skin has a shallow depth. The latter three are deeper. Its depth is lighter than 01. ~1mm, Yanying's is about 10mm... The surface of such precision casting defects is often covered with light and shiny carbon flakes, and the recesses of the defects are filled with soot and carbon, which are surface carbon defects. The wrinkle defect often occurs in the liquid ESP from the metal. It is too late to vaporize during the condensation process of the molten iron. Because the surface tension is different from that of the molten iron, it causes shrinkage. After the molten metal is cooled and solidified, it becomes non-liquid and finally flows to the part or flow. The "cold end" part. Continuous corrugated wrinkled skin defects and cold partition wrinkled skin.
- 3) The pulsating flow process produces wrinkled skin defects ES liquid metal P and quickly vaporizes after contact, producing a large amount of gas. At the beginning of pouring. The metal indenter is large and the liquid metal is filled smoothly. But with the precision casting pouring. Because the air permeability of the coating and the mold is constant, the pressure at the air gap gradually increases. In this way, the pressure at the metal head and the air gap must be balanced at a certain moment. At this moment, the generation mechanism of the wrinkle defect is a problem. The complicated process involves the heating of the model.
Please keep the source and address of this article for reprinting:The Causes Of Wrinkles Formed On Precision Castings Produced Surface By Lost Foam
Minghe Die Casting Company are dedicated to manufacture and provide quality and high performance Casting Parts(metal die casting parts range mainly include Thin-Wall Die Casting,Hot Chamber Die Casting,Cold Chamber Die Casting),Round Service(Die Casting Service,Cnc Machining,Mold Making,Surface Treatment).Any custom Aluminum die casting, magnesium or Zamak/zinc die casting and other castings requirements are welcome to contact us.
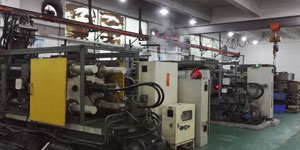
Under the control of ISO9001 and TS 16949,All processes are carried out through hundreds of advanced die casting machines, 5-axis machines, and other facilities, ranging from blasters to Ultra Sonic washing machines.Minghe not only has advanced equipment but also have professional team of experienced engineers,operators and inspectors to make the customer’s design come true.
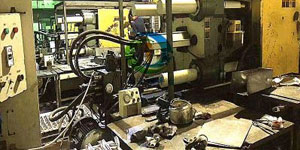
Contract manufacturer of die castings. Capabilities include cold chamber aluminum die casting parts from 0.15 lbs. to 6 lbs., quick change set up, and machining. Value-added services include polishing, vibrating, deburring, shot blasting, painting, plating, coating, assembly, and tooling. Materials worked with include alloys such as 360, 380, 383, and 413.
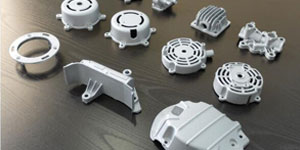
Zinc die casting design assistance/concurrent engineering services. Custom manufacturer of precision zinc die castings. Miniature castings, high pressure die castings, multi-slide mold castings, conventional mold castings, unit die and independent die castings and cavity sealed castings can be manufactured. Castings can be manufactured in lengths and widths up to 24 in. in +/-0.0005 in. tolerance.
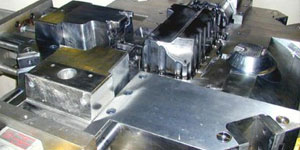
ISO 9001: 2015 certified manufacturer of die cast magnesium, Capabilities include high-pressure magnesium die casting up to 200 ton hot chamber & 3000 ton cold chamber, tooling design, polishing, molding, machining, powder & liquid painting, full QA with CMM capabilities, assembly, packaging & delivery.
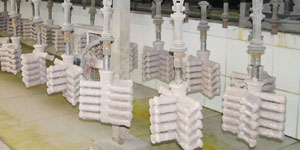
ITAF16949 certified. Additional Casting Service Include investment casting,sand casting,Gravity Casting, Lost Foam Casting,Centrifugal Casting,Vacuum Casting,Permanent Mold Casting,.Capabilities include EDI, engineering assistance, solid modeling and secondary processing.
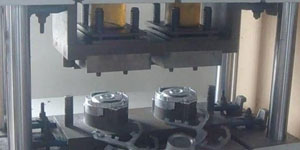
Casting Industries Parts Case Studies for: Cars, Bikes, Aircraft, Musical instruments, Watercraft, Optical devices, Sensors, Models, Electronic devices, Enclosures, Clocks, Machinery, Engines, Furniture, Jewelry, Jigs, Telecom, Lighting, Medical devices, Photographic devices, Robots, Sculptures, Sound equipment, Sporting equipment, Tooling, Toys and more.
What Can we help you do next?
∇ Go To Homepage For Die Casting China
→Casting Parts-Find out what we have done.
→Ralated Tips About Die Casting Services
By Minghe Die Casting Manufacturer |Categories: Helpful Articles |Material Tags: Aluminum Casting, Zinc Casting, Magnesium Casting, Titanium Casting, Stainless Steel Casting, Brass Casting,Bronze Casting,Casting Video,Company History,Aluminum Die Casting |Comments Off