The Combination Of Powder Coating For Foundry And High-Efficiency Flow Coating Process
Casting coatings are applied to most of the casting production process and play an important role in the surface quality of castings. There are many foundry coating manufacturers in my country, with large differences in production scale and uneven product quality. For casting manufacturers, it is very important to select high-quality coatings that suit their casting requirements.
According to the current application of foundry coatings in my country, according to the classification of solvent carriers, alcohol-based and water-based are the two most widely used solvent types. According to the original form of the coating before use, it can be divided into slurry, paste and powder coatings. Many casting manufacturers tend to use slurry coatings. The relative solid content of slurry coatings is relatively low, and the solid content is generally 70%. % Or less, it can be used without adding a large amount of thinner (alcohol or water) during use, and the operation is more convenient; the relative solid content of the paste is relatively high, before use, add more thinner to obtain the suitable Baume degree. The use cost is relatively lower; the powder form is generally divided into dry powder and wet state, each has its advantages, the wet state powder is relatively easier to stir the coating and the uniformization of the use process; the powder coating is relatively slurry in the use cost of the foundry enterprise And paste has more advantages, and it is easier to guarantee the safety of transportation and storage, but many foundry manufacturers are worried about the complexity of the operation and the stability in use.
The flow coating process is gradually getting familiar and applied by foundry companies. By comparing the coating process of the same sand mold, compared with the brushing process, flow coating can save more than 80% of the painting time. Considering that the flow coating process requires the lifting of the sand mold From the analysis of the overall time consumption, the production efficiency of the flow coating process is still much higher than that of the brush coating process. Excluding sand molds that are inconvenient for hoisting and handling, the flow coating process will become the mainstream coating process in my country in the future.
Performance Analysis Of Powder Coating
The wet state powder coating is called the wet state because it is not pure dry powder and also contains a small amount of solvent (alcohol or water). The equipment used in the coating production process is different from ordinary stirred reactors to ensure that each group of coatings Remove the excess solvent while fully homogenizing and mixing, so that the paint can be directly used in a paper packaging bag lined with a plastic bag to ensure that the paint is in a sealed state during transportation and prevent the volatilization and penetration of a small amount of alcohol solvent.
For our casting production enterprises, we first hope that the coating is easy to operate, save manpower, and is easy to homogenize and stir; then, the painting efficiency is high, the operator's labor is reduced, and the coating surface quality is good; finally the surface quality of the casting is guaranteed; on this basis The use cost of coating is relatively reduced.
Compared with paste coatings, the advantages of powder coatings may be reflected in the following aspects:
- 1) Improved transportation and storage safety, especially for alcohol-based coatings;
- 2) Loading and unloading is easier to mechanize operations, reducing manual operations;
- 3) Mixing and stirring are operated by mixing equipment, which makes it easier for the coating to be used uniformly and stably, so that the overall performance of the coating is easier to give full play;
- 4) The amount of alcohol in use is relatively increased, the amount of paint is relatively reduced, and the cost of use is significantly reduced; generally when using slurry paint, before the paint is used, it is necessary to add 0-50% of the original barrel weight of the solvent, and use powder paint When the paint reaches the use state, it needs to add 60%-100% of the solvent relative to the original barrel weight, and the use cost can be effectively reduced.
Flow Coating Process Analysis
The flow coating process has advantages but also its relative limitations. In the molding workshop of a foundry enterprise, the flow coating process should be classified as a semi-automatic mechanical operation, while the brushing or spraying process seems to be more classified as a non-mechanized manual operation. The actual situation of sand mold structure is not conducive to flow coating, sand box design is not convenient for lifting flow coating, insufficient driving capacity, and workshop design is not conducive to flow coating. Obviously, the implementation of flow coating process is restricted. However, if conditions permit, casting enterprises have It is worthwhile to transform from brush coating process to flow coating process because:
- 1) The production efficiency of the flow coating process is significantly improved, especially for sand molds with more complex structures;
- 2) With the improvement of production efficiency, the number of operators can be reduced, and the relative labor cost can be reduced. Especially when the labor costs of foundry companies increase and the willingness of workers to engage in foundry production is reduced, it is necessary for foundry companies to replace manual operations with equipment. Development trend;
- 3) The surface quality of castings is improved (of course, the prerequisite is to use flow coating that meets the requirements of flow coating quality). After flow coating, the surface of the sand mold is smooth and clean, without flow marks and brush marks. Partial brushing that often occurs in the brushless coating process, Moreover, the coating thickness is relatively more uniform, and it is easier to ensure the surface quality of the casting;
- 4) The improvement of the surface quality of castings can effectively reduce the difficulty of subsequent cleaning. The cleaning process is also a headache for foundry managers. If we can ensure excellent preliminary work (modeling, painting, process design, etc.), follow-up cleaning Naturally, the pressure will be reduced a lot;
- 5) The flow coating process can relatively reduce the consumption of paint. When a reasonable coating thickness is reached, the Baume degree of the flow coating process is smaller than that of the brushing process. Of course, the consumption of solvents will inevitably increase, but from the comprehensive Cost analysis is also more cost-effective for paint users.
Combination Process Analysis
When the brushing process is used, the bottleneck of the production cycle of the modeling workshop often occurs in the paint painting process. Generally, it is necessary to increase the labor cost to alleviate this bottleneck. We can also eliminate the bottleneck by modifying the paint painting process to remove the powder. Coating and flow coating process are combined to realize the mechanized operation of the coating process.
Powder coatings are generally packaged in paper bags and transported on pallets. After arriving at the casting site, they are mechanized and transported to the storage location. When adding materials, the operator pours the coatings into a mixing tank (volume 0.5-1t) for homogenization and mixing (if possible, advance in advance) Put the paint into the mixing tank and fully dissolve it with alcohol), the paint that meets the flow coating requirements is input into the flow coating equipment through diaphragm pumps and other equipment for flow coating operation, and the excess paint is returned to the flow coating equipment. In case of holidays, the flow coating can be applied The paint in the equipment is transported back to the mixing tank to ensure the smooth flow coating and uniformity and stability of the paint when it is used again.
The flow coating equipment needs to have good filtration to ensure that the coating is not mixed with sand and other debris scattered from the sand mold during flow coating, so as to ensure the cleanliness of the surface coating of the sand mold.
The use of flow coating technology requires certain requirements for the on-site management of the workshop. From the mold starting time to the placement of the sand mold on the workshop site, reasonable arrangements need to be made. The biggest purpose of the above operations is to ensure the continuity of the flow coating operation. Only continuous flow coating operation can reflect the high efficiency advantages of flow coating process.
The use of powder coating and flow coating technology has certain benefits for the clean management of the foundry production workshop. The powder coating is packaged in paper bags, which eliminates the packaging barrel and reduces the storage space of the packaging barrel; brushing when the brushing process is used The location is relatively scattered, while the flow coating process location is fixed, the purpose and identification are clearer.
Summary
When it comes to the foundry industry, it is often easily linked with "dirty, messy, and poor". Foundry people will have more empathy. With the development of foundry technology and equipment technology, foundry can also be mechanized throughout the process to achieve cleanliness. produce. Flow coating technology and flow coating equipment will also be the future development trend. At present, many large-scale molding lines have been equipped with advanced flow coating equipment, which uses manipulators to hold sand molds, and the operation process is semi-automatic. Similarly, in the environment of the original brushing process , It can also be transformed into a flow coating process by installing flow coating equipment to achieve efficient operation of the coating process. The application of powder coatings improves the safety of transportation and storage and reduces the cost of coatings for companies. It is also a good choice for foundry companies.
Please keep the source and address of this article for reprinting: The Combination Of Powder Coating For Foundry And High-Efficiency Flow Coating Process
Minghe Die Casting Company are dedicated to manufacture and provide quality and high performance Casting Parts(metal die casting parts range mainly include Thin-Wall Die Casting,Hot Chamber Die Casting,Cold Chamber Die Casting),Round Service(Die Casting Service,Cnc Machining,Mold Making,Surface Treatment).Any custom Aluminum die casting, magnesium or Zamak/zinc die casting and other castings requirements are welcome to contact us.
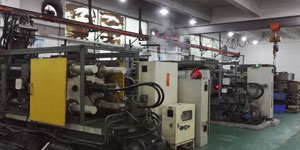
Under the control of ISO9001 and TS 16949,All processes are carried out through hundreds of advanced die casting machines, 5-axis machines, and other facilities, ranging from blasters to Ultra Sonic washing machines.Minghe not only has advanced equipment but also have professional team of experienced engineers,operators and inspectors to make the customer’s design come true.
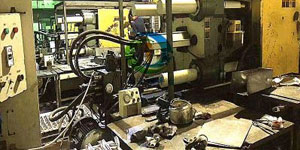
Contract manufacturer of die castings. Capabilities include cold chamber aluminum die casting parts from 0.15 lbs. to 6 lbs., quick change set up, and machining. Value-added services include polishing, vibrating, deburring, shot blasting, painting, plating, coating, assembly, and tooling. Materials worked with include alloys such as 360, 380, 383, and 413.
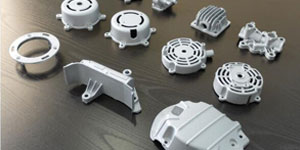
Zinc die casting design assistance/concurrent engineering services. Custom manufacturer of precision zinc die castings. Miniature castings, high pressure die castings, multi-slide mold castings, conventional mold castings, unit die and independent die castings and cavity sealed castings can be manufactured. Castings can be manufactured in lengths and widths up to 24 in. in +/-0.0005 in. tolerance.
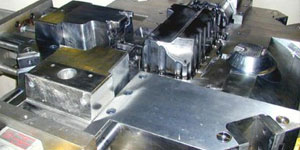
ISO 9001: 2015 certified manufacturer of die cast magnesium, Capabilities include high-pressure magnesium die casting up to 200 ton hot chamber & 3000 ton cold chamber, tooling design, polishing, molding, machining, powder & liquid painting, full QA with CMM capabilities, assembly, packaging & delivery.
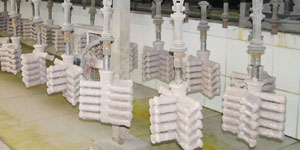
ITAF16949 certified. Additional Casting Service Include investment casting,sand casting,Gravity Casting, Lost Foam Casting,Centrifugal Casting,Vacuum Casting,Permanent Mold Casting,.Capabilities include EDI, engineering assistance, solid modeling and secondary processing.
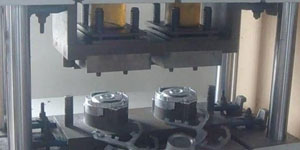
Casting Industries Parts Case Studies for: Cars, Bikes, Aircraft, Musical instruments, Watercraft, Optical devices, Sensors, Models, Electronic devices, Enclosures, Clocks, Machinery, Engines, Furniture, Jewelry, Jigs, Telecom, Lighting, Medical devices, Photographic devices, Robots, Sculptures, Sound equipment, Sporting equipment, Tooling, Toys and more.
What Can we help you do next?
∇ Go To Homepage For Die Casting China
→Casting Parts-Find out what we have done.
→Ralated Tips About Die Casting Services
By Minghe Die Casting Manufacturer |Categories: Helpful Articles |Material Tags: Aluminum Casting, Zinc Casting, Magnesium Casting, Titanium Casting, Stainless Steel Casting, Brass Casting,Bronze Casting,Casting Video,Company History,Aluminum Die Casting |Comments Off