The Common Failure Types And Causes Of Die Casting Tooling
The mold is cast during use, and some failures and damages often occur, and the use of very serious defects affects the mold. Below the standard parts, you can understand the most common failure modes of die-casting molds in the production process: fracture failure, failure and dissolution.
And three kinds of thermal fatigue crack damage and failure reasons are introduced in detail.
1. Fracture failure
Under the action of injection pressure, the mold will initiate cracks in the most fragile place, especially the surface where the traces of the molding line or the traces of electrical machining are not completed, or the place where a clear angle is formed will be the first small crack. The presence of brittle phases or coarse grain boundaries is easy to fracture. The rapid growth of cracks, brittle fracture, and mold fracture are the risk factors for failure. Therefore, on the one hand, scratches on the surface of the mold, electrical machining marks must be polished, even if it is in the pouring system, it must be illuminated. It also requires high strength, good plasticity using advanced materials, and good impact toughness and fracture toughness.
2. Corrosion failure
Commonly used molds and zinc alloys, casting alloys, aluminum alloys, magnesium alloys and copper alloys, there are also pure aluminum alloy die-casting, zinc metal elements, aluminum and magnesium are a kind of lively, they have a good affinity, mold materials, Especially aluminum sheet. When the mold hardness is high, it has good corrosion resistance. If there are soft spots on the molding surface, it is anti-corrosion.
3.Thermal fatigue crack damage failure
In the process of die casting mold production, the quenching effect of the hot forming surface and its internal deformation occur repeatedly, and the repeated thermal stress interacts, resulting in structural damage and elastic loss, leading to the appearance of micro-cracks, and causing the surface structure and internal structure of the casting to occur fracture. When the crack propagates, stagnation and melting of the fluid and repeated mechanical stress accelerate the crack propagation. Therefore, on the one hand, the die casting mold must be fully preheated before it can start. In addition, in order to avoid early cracking and failure during the production of die-casting molds, a certain operating temperature range must be maintained. At the same time, it is not a problem to ensure the production and internal reasons before the mold is put into production. In actual production, mold failure is the most common failure of thermal fatigue cracks.
Please keep the source and address of this article for reprinting:The Common Failure Types And Causes Of Die Casting Tooling
Minghe Die Casting Company are dedicated to manufacture and provide quality and high performance Casting Parts(metal die casting parts range mainly include Thin-Wall Die Casting,Hot Chamber Die Casting,Cold Chamber Die Casting),Round Service(Die Casting Service,Cnc Machining,Mold Making,Surface Treatment).Any custom Aluminum die casting, magnesium or Zamak/zinc die casting and other castings requirements are welcome to contact us.
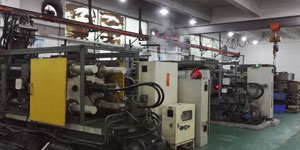
Under the control of ISO9001 and TS 16949,All processes are carried out through hundreds of advanced die casting machines, 5-axis machines, and other facilities, ranging from blasters to Ultra Sonic washing machines.Minghe not only has advanced equipment but also have professional team of experienced engineers,operators and inspectors to make the customer’s design come true.
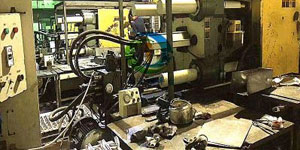
Contract manufacturer of die castings. Capabilities include cold chamber aluminum die casting parts from 0.15 lbs. to 6 lbs., quick change set up, and machining. Value-added services include polishing, vibrating, deburring, shot blasting, painting, plating, coating, assembly, and tooling. Materials worked with include alloys such as 360, 380, 383, and 413.
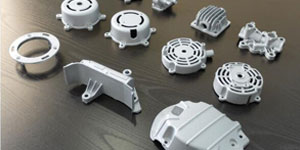
Zinc die casting design assistance/concurrent engineering services. Custom manufacturer of precision zinc die castings. Miniature castings, high pressure die castings, multi-slide mold castings, conventional mold castings, unit die and independent die castings and cavity sealed castings can be manufactured. Castings can be manufactured in lengths and widths up to 24 in. in +/-0.0005 in. tolerance.
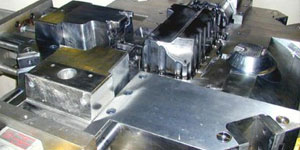
ISO 9001: 2015 certified manufacturer of die cast magnesium, Capabilities include high-pressure magnesium die casting up to 200 ton hot chamber & 3000 ton cold chamber, tooling design, polishing, molding, machining, powder & liquid painting, full QA with CMM capabilities, assembly, packaging & delivery.
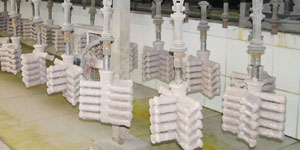
ITAF16949 certified. Additional Casting Service Include investment casting,sand casting,Gravity Casting, Lost Foam Casting,Centrifugal Casting,Vacuum Casting,Permanent Mold Casting,.Capabilities include EDI, engineering assistance, solid modeling and secondary processing.
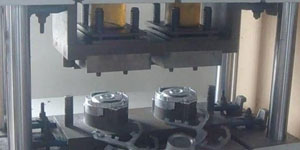
Casting Industries Parts Case Studies for: Cars, Bikes, Aircraft, Musical instruments, Watercraft, Optical devices, Sensors, Models, Electronic devices, Enclosures, Clocks, Machinery, Engines, Furniture, Jewelry, Jigs, Telecom, Lighting, Medical devices, Photographic devices, Robots, Sculptures, Sound equipment, Sporting equipment, Tooling, Toys and more.
What Can we help you do next?
∇ Go To Homepage For Die Casting China
→Casting Parts-Find out what we have done.
→Ralated Tips About Die Casting Services
By Minghe Die Casting Manufacturer |Categories: Helpful Articles |Material Tags: Aluminum Casting, Zinc Casting, Magnesium Casting, Titanium Casting, Stainless Steel Casting, Brass Casting,Bronze Casting,Casting Video,Company History,Aluminum Die Casting |Comments Off