The Composition And Function Of Precision Stamping Die
Everyone knows that the processing of precision stamping parts is inseparable from stamping dies. Stamping dies are a special process equipment for processing materials (metal or non-metal) into parts (or semi-finished products), and are widely used in the metal processing industry. However, the structure and composition of precision stamping parts molds are relatively complicated, and many people don't know much about it. Below, Shiyunjia Industry will introduce the composition and function of precision stamping parts molds in detail.
Everyone knows that the processing of precision stamping parts is inseparable from stamping dies. Stamping dies are a special process equipment for processing materials (metal or non-metal) into parts (or semi-finished products), and are widely used in the metal processing industry. However, the structure and composition of precision stamping parts molds are relatively complicated, and many people don't know much about it. Below, Shiyunjia Industry will introduce the composition and function of precision stamping parts molds in detail.
The mold is an important part of the processing of metal stamping parts, and the quality of the mold determines the quality of the metal stamping parts. Therefore, there are high requirements for the manufacture of molds, and the thermal processing of the mold has a great impact on the performance and service life of the mold. In order to ensure the quality of the mold, it is necessary to understand the thermal processing technology and precautions of the metal stamping mold
Precision stamping die
Precision stamping parts molds are mainly composed of the following parts:
- Working parts: punches, dies, etc., mainly to complete the separation or formation of precision stamping parts/precision terminal materials.
- Positioning parts: stopper pins, positioning pins, positioning baffles, etc., are mainly used to locate the correct position of precision stamping parts/precision terminal blanks in the mold.
- Guide parts: guide posts, guide sleeves, guide plates, etc., mainly to ensure the correct movement of the upper and lower molds.
- Supporting parts: upper and lower templates and fixed plates of concave and convex molds, etc., which are mainly used to connect and fix working parts.
- Fastening parts: hexagon socket screws, stripper screws, pull pins, etc., which are mainly used to connect and fasten various parts to make them integrated.
- Cushioning parts: steel wire springs, polyurethane rubber springs, etc., mainly use its elastic force to unload and return materials.
- Pressing, unloading and ejecting parts: press plate, unloading plate, ejector, blank holder, etc., mainly play the role of separating parts and waste from the mold, and press in the drawing die. The edge force ring also prevents instability and wrinkles.
Regarding the composition and function of precision stamping die, I will introduce it here today. The quality of the precision stamping parts mold affects the forming quality of the stamping parts, so the reasonable design and manufacture of the mold is very important.
Please keep the source and address of this article for reprinting:The Composition And Function Of Precision Stamping Die
Minghe Die Casting Company are dedicated to manufacture and provide quality and high performance Casting Parts(metal die casting parts range mainly include Thin-Wall Die Casting,Hot Chamber Die Casting,Cold Chamber Die Casting),Round Service(Die Casting Service,Cnc Machining,Mold Making,Surface Treatment).Any custom Aluminum die casting, magnesium or Zamak/zinc die casting and other castings requirements are welcome to contact us.
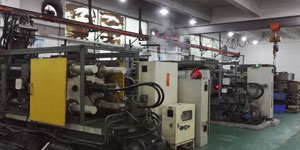
Under the control of ISO9001 and TS 16949,All processes are carried out through hundreds of advanced die casting machines, 5-axis machines, and other facilities, ranging from blasters to Ultra Sonic washing machines.Minghe not only has advanced equipment but also have professional team of experienced engineers,operators and inspectors to make the customer’s design come true.
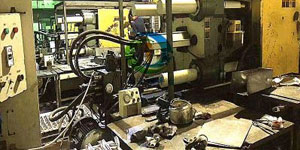
Contract manufacturer of die castings. Capabilities include cold chamber aluminum die casting parts from 0.15 lbs. to 6 lbs., quick change set up, and machining. Value-added services include polishing, vibrating, deburring, shot blasting, painting, plating, coating, assembly, and tooling. Materials worked with include alloys such as 360, 380, 383, and 413.
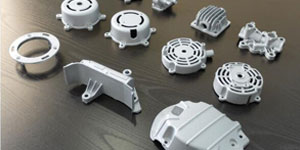
Zinc die casting design assistance/concurrent engineering services. Custom manufacturer of precision zinc die castings. Miniature castings, high pressure die castings, multi-slide mold castings, conventional mold castings, unit die and independent die castings and cavity sealed castings can be manufactured. Castings can be manufactured in lengths and widths up to 24 in. in +/-0.0005 in. tolerance.
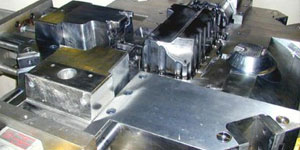
ISO 9001: 2015 certified manufacturer of die cast magnesium, Capabilities include high-pressure magnesium die casting up to 200 ton hot chamber & 3000 ton cold chamber, tooling design, polishing, molding, machining, powder & liquid painting, full QA with CMM capabilities, assembly, packaging & delivery.
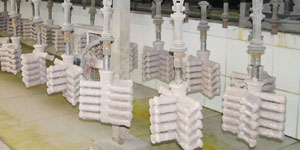
ITAF16949 certified. Additional Casting Service Include investment casting,sand casting,Gravity Casting, Lost Foam Casting,Centrifugal Casting,Vacuum Casting,Permanent Mold Casting,.Capabilities include EDI, engineering assistance, solid modeling and secondary processing.
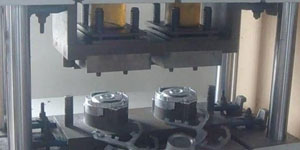
Casting Industries Parts Case Studies for: Cars, Bikes, Aircraft, Musical instruments, Watercraft, Optical devices, Sensors, Models, Electronic devices, Enclosures, Clocks, Machinery, Engines, Furniture, Jewelry, Jigs, Telecom, Lighting, Medical devices, Photographic devices, Robots, Sculptures, Sound equipment, Sporting equipment, Tooling, Toys and more.
What Can we help you do next?
∇ Go To Homepage For Die Casting China
→Casting Parts-Find out what we have done.
→Ralated Tips About Die Casting Services
By Minghe Die Casting Manufacturer |Categories: Helpful Articles |Material Tags: Aluminum Casting, Zinc Casting, Magnesium Casting, Titanium Casting, Stainless Steel Casting, Brass Casting,Bronze Casting,Casting Video,Company History,Aluminum Die Casting |Comments Off