The Control Measures of Spatter In CO2 Gas Shielded Welding
In the current ferrous metal materials, CO2 gas shielded welding is one of the most important welding methods, using carbon dioxide gas as the shielding gas for welding. During the welding process, most of the welding wire melts into molten metal and transitions into the molten pool, but a part of the welding wire flies out of the molten pool with the molten metal, which is called spatter.
When the spatter rate reaches more than 30%, normal welding cannot be performed. CO2 gas shielded welding spatter will also reduce welding efficiency and welding productivity; spatters are easy to adhere to weldments and nozzles, affecting welding quality, worsening welding labor and increasing cleaning hours; welding pool is unstable, resulting in Defects such as rough weld shape.
During the free transition of the molten droplet, the splash produced is mainly due to the flow of airflow and ejected by the arc pressure and formed by the explosion; at the same time, when the droplet and the molten pool are in contact, the short-circuit current is in the contact part after energization. Spatter caused by the heat of the dissipating resistance and the melting of the welding wire.
The preventive measures for CO2 gas shielded welding spatter are:
- When the droplet is freely transferred, reasonable welding current and welding voltage parameters should be selected to avoid the use of large droplet rejection transition form; at the same time, high-quality welding materials should be selected, such as the selection of low-C content and deoxidizing elements Mn and Si welding wire H08Mn2SiA, etc., to avoid splashing caused by gas precipitation or expansion due to the metallurgical reaction of the welding material.
- During short-circuit transition, (Ar+CO2) mixed gas can be used instead of CO to reduce splashing. Such as adding Φ(Ar)=20%~30% Ar. This is because as the argon content increases, the arc morphology and droplet transfer characteristics have changed. During arcing, the arc root of the arc expands, and the axiality of the droplet is enhanced. This aspect makes it easy for the molten droplet to meet the molten pool, and small short-circuit bridges appear between the welding wire and the molten pool. On the other hand, under the action of the axial force, the droplet obtains a more uniform short-circuit transition process, and the short-circuit peak current is not too high, which is beneficial to reduce the spatter rate.
- In a pure CO atmosphere, the welding current waveform control method is usually used to reduce the current at the initial stage of short-circuit and the current at the moment when the short-circuit bridge is broken, so as to reduce the electric explosion energy of the small bridge and achieve the purpose of reducing spatter.
- By improving the wire feeding system, pulse wire feeding is used instead of conventional constant velocity wire feeding, so that the molten droplet is short-circuited with the molten pool under the condition of pulsating feeding, so that the short-circuit transition frequency is basically the same as the frequency of pulsating wire feeding. The electrical parameters of each short-circuit cycle have good repeatability, the short-circuit peak current is also uniform, and its value is not high, thereby reducing spatter.
Please keep the source and address of this article for reprinting:The Control Measures of Spatter In CO2 Gas Shielded Welding
Minghe Die Casting Company are dedicated to manufacture and provide quality and high performance Casting Parts(metal die casting parts range mainly include Thin-Wall Die Casting,Hot Chamber Die Casting,Cold Chamber Die Casting),Round Service(Die Casting Service,Cnc Machining,Mold Making,Surface Treatment).Any custom Aluminum die casting, magnesium or Zamak/zinc die casting and other castings requirements are welcome to contact us.
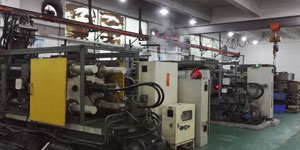
Under the control of ISO9001 and TS 16949,All processes are carried out through hundreds of advanced die casting machines, 5-axis machines, and other facilities, ranging from blasters to Ultra Sonic washing machines.Minghe not only has advanced equipment but also have professional team of experienced engineers,operators and inspectors to make the customer’s design come true.
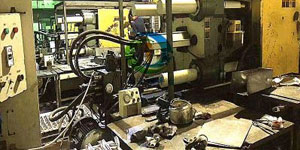
Contract manufacturer of die castings. Capabilities include cold chamber aluminum die casting parts from 0.15 lbs. to 6 lbs., quick change set up, and machining. Value-added services include polishing, vibrating, deburring, shot blasting, painting, plating, coating, assembly, and tooling. Materials worked with include alloys such as 360, 380, 383, and 413.
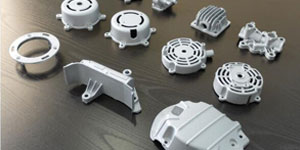
Zinc die casting design assistance/concurrent engineering services. Custom manufacturer of precision zinc die castings. Miniature castings, high pressure die castings, multi-slide mold castings, conventional mold castings, unit die and independent die castings and cavity sealed castings can be manufactured. Castings can be manufactured in lengths and widths up to 24 in. in +/-0.0005 in. tolerance.
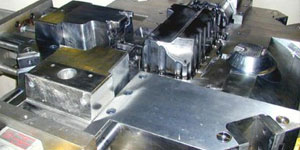
ISO 9001: 2015 certified manufacturer of die cast magnesium, Capabilities include high-pressure magnesium die casting up to 200 ton hot chamber & 3000 ton cold chamber, tooling design, polishing, molding, machining, powder & liquid painting, full QA with CMM capabilities, assembly, packaging & delivery.
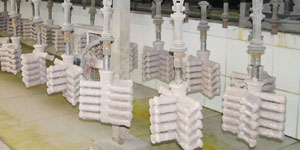
ITAF16949 certified. Additional Casting Service Include investment casting,sand casting,Gravity Casting, Lost Foam Casting,Centrifugal Casting,Vacuum Casting,Permanent Mold Casting,.Capabilities include EDI, engineering assistance, solid modeling and secondary processing.
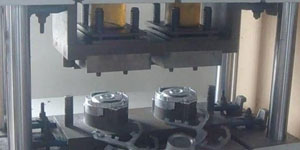
Casting Industries Parts Case Studies for: Cars, Bikes, Aircraft, Musical instruments, Watercraft, Optical devices, Sensors, Models, Electronic devices, Enclosures, Clocks, Machinery, Engines, Furniture, Jewelry, Jigs, Telecom, Lighting, Medical devices, Photographic devices, Robots, Sculptures, Sound equipment, Sporting equipment, Tooling, Toys and more.
What Can we help you do next?
∇ Go To Homepage For Die Casting China
→Casting Parts-Find out what we have done.
→Ralated Tips About Die Casting Services
By Minghe Die Casting Manufacturer |Categories: Helpful Articles |Material Tags: Aluminum Casting, Zinc Casting, Magnesium Casting, Titanium Casting, Stainless Steel Casting, Brass Casting,Bronze Casting,Casting Video,Company History,Aluminum Die Casting |Comments Off