The Control Of Die Casting Process
Due to the diversity of the factors affecting casting quality and the complexity of the production process, at present the rational organization, controlling process has an important role in promoting the process design, technical training and production control, with the ultimate goal being to realize the effective prevention and remedy of casting defects. Brief analysis about alloy melt control, mold and die-casting process control, interior and exterior inspection of products is carried out.
The design of the engine block is developing in the direction of lighter weight and complexity. Because of its low density and good casting performance, aluminum alloy is often used to produce aerospace and auto parts with complex shapes, thin walls, and medium loads. A series of engine blocks produced by Changan Automobile Jiangbei Engine Factory are formed by high-pressure casting in a mold with a high-quality aluminum alloy (similar to the domestic brand YL113). The cylinder block of this series of engines is a high-strength, thin-walled complex casting. Most of the holes on the cylinder block are pre-cast with mold cores, which not only has high requirements for hardware equipment such as molds and die-casting machines, but the control of the entire production process guarantees delivery The circulation is smooth, and the improvement of product quality is also of great significance.
Process Control
In the process management of die-casting production, it is particularly important to stabilize and improve product quality from the aspects of aluminum liquid control, mold control, die-casting process control and product inspection.
Aluminum Water Control
The solidification defects of cast aluminum alloy seriously affect the performance of the castings, and the control or elimination of solidification defects is of great significance to improve the yield of castings. As the requirements for the comprehensive properties of alloys are getting higher and higher,
The research on adding more kinds of alloying elements to improve the comprehensive properties of alloys has become more and more in-depth, and the method of alloy composition control has become more and more important. Common solidification defects in cast aluminum alloys in engineering, such as segregation, hot cracking, microporosity, shrinkage, etc., need to be controlled from the source. In response to green manufacturing, the production base of this model at Changan Automobile's Jiangbei Engine Plant adopts a direct supply of molten aluminum, so the quality of the direct supply of molten aluminum is used as the basis for whether the molten aluminum meets the requirements. A vacuum sample preparation device is used to detect the density equivalent of aluminum alloy ingots, a spectrum analyzer is used for physical and chemical analysis, and K-mode detection is performed on machine-side furnace aluminum water on a regular basis to monitor the density equivalent, chemical composition, and purity of the aluminum alloy.
Mold Control
The management, spot inspection, and maintenance of molds are a part of die-casting, and mold status is very important to product quality. The mold base is made of cast iron. During injection, the aluminum water flows through the pressure chamber, the sprue, the cross runner, and the inner runner for injection molding from bottom to top. The entire gating system is a closed design to reduce the aluminum water entrainment. The inside of the mold cavity is opened with water to balance the temperature field of the mold, and all parts of the cylinder body are solidified at the same time, and the residual gas in the aluminum water is dispersed and distributed. As far as possible, the casting holes should be pre-casted with cooling water. The high-pressure point cooling or reciprocating water cooling method can be selected according to actual needs. The cooling water can directly reach the top of the casting pin, so that the top part can also be cooled.
In the production process, the mold temperature has a great influence on the product and the life of the mold, and the high temperature is prone to mold sticking, the surface of the casting is rough, and shrinkage holes and cracks may also occur. Due to the sticking of the mold, the friction.
The increased friction force doubles the local tensile force, which makes the local movement of the mold inaccurate and damages the mold. Mold temperature control is generally set according to the wall thickness of the casting and the distribution of molten aluminum flow. The cooling water volume and cooling time of different parts of the mold can be adjusted. Cooling outside the mold is also important, and it has a lot to do with the position, direction and procedure (time) of the release agent spraying. The selection, proportion and amount of the release agent will affect the use of the mold and the quality of the product. Mold maintenance is divided into preventive maintenance, predictive maintenance and spot inspection. Determine the preventive maintenance cycle of the mold according to the accumulated experience, determine the predictive maintenance time according to the state and use of the mold, and perform daily inspections during the production process. The maintenance content covers cooling system (water, oil, gas), vacuum system, sealing, cleaning of cavity surface, etc.
Process Parameter Control
The control and optimization of die-casting process is an important part of die-casting production, which directly affects the surface and internal quality of die-casting parts. The parameters of die casting process mainly include pressure, speed and time.
The technical control parameters are quantitatively controlled to ensure that the flow, solidification, and heat exchange of the liquid metal are carried out in a set manner, so as to ensure the quality of the die-casting parts. The internal quality of the casting is very sensitive to the changes of the injection parameters. If the pressure is too low, the casting will have a lot of pores, shrinkage and other defects. If the pressure is too high, although the casting structure is dense, it will produce large flashes and burrs, which will damage the mold. . During production, it is also important to show that the change point from slow to fast injection is also very important. To change prematurely, the molten aluminum passes through the inner runner and enters the cavity at a high speed. The route is long, causing turbulent flow of the molten aluminum, involving a large amount of gas, and it is easy to form some Irregular casting defects; too late to change, the aluminum liquid stays in the pressure chamber for a long time, the temperature is low, it is easy to produce cold barriers, insufficient pouring and other defects. In fact, from anatomical point of view, the existence of pores and shrinkage holes in the casting is inevitable. The key is to adjust the injection parameters so that the gas in the aluminum liquid can be discharged as effectively as possible, and the remaining small amount of pores are dispersed and distributed in the interior. Penetration of the section causes leakage of the casting. The injection speed includes the punch speed (that is, the movement speed of the piston in the injection cylinder) and the filling speed (that is, the sprue speed).
Filling speed refers to the linear speed of molten alloy passing through the inner runner, which is an important parameter to ensure the quality of die castings. The injection time is composed of slow injection time, fast injection time, pressurization time, pressure holding time, and mold retention time. In production, the holding time and mold retention time are usually controlled and optimized together, referred to as holding pressure and mold retention time. Sufficient holding pressure and mold retention time means that the die casting does not deform or stretch during mold opening and ejection. A necessary condition for cracking. These important parameters need to be monitored on a daily basis and continuously optimized according to the status of the casting.
Product Inspection
Casting inspection includes appearance and size inspection, internal quality inspection, pre-cast hole position inspection, wall thickness inspection, cylinder liner wall thickness difference inspection, casting heat treatment offline final inspection, according to personnel arrangements and actual production requirements according to fixed frequency and standard The casting is qualified.
Sampling inspections in the production process can detect problems in time and react quickly, and will not cause batch problems due to poor timeliness of problem discovery.
Sutras
Die-casting production is a relatively complicated process, involving the quality of the molten aluminum, the state of the die-casting mold, the parameters of the die-casting machine, the die-casting process and product inspection, etc., which are closely related to the quality of the die-casting parts. In die-casting production, the process determines the result, good process management will lead to stable product quality, and controlled mass production will bring large-scale economic benefits.
Please keep the source and address of this article for reprinting: The Control Of Die Casting Process
Minghe Die Casting Company are dedicated to manufacture and provide quality and high performance Casting Parts(metal die casting parts range mainly include Thin-Wall Die Casting,Hot Chamber Die Casting,Cold Chamber Die Casting),Round Service(Die Casting Service,Cnc Machining,Mold Making,Surface Treatment).Any custom Aluminum die casting, magnesium or Zamak/zinc die casting and other castings requirements are welcome to contact us.
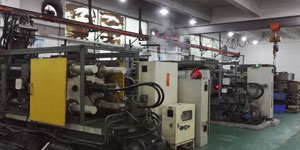
Under the control of ISO9001 and TS 16949,All processes are carried out through hundreds of advanced die casting machines, 5-axis machines, and other facilities, ranging from blasters to Ultra Sonic washing machines.Minghe not only has advanced equipment but also have professional team of experienced engineers,operators and inspectors to make the customer’s design come true.
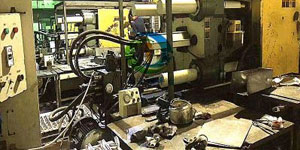
Contract manufacturer of die castings. Capabilities include cold chamber aluminum die casting parts from 0.15 lbs. to 6 lbs., quick change set up, and machining. Value-added services include polishing, vibrating, deburring, shot blasting, painting, plating, coating, assembly, and tooling. Materials worked with include alloys such as 360, 380, 383, and 413.
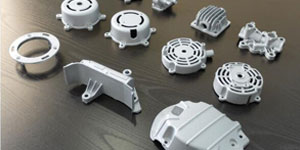
Zinc die casting design assistance/concurrent engineering services. Custom manufacturer of precision zinc die castings. Miniature castings, high pressure die castings, multi-slide mold castings, conventional mold castings, unit die and independent die castings and cavity sealed castings can be manufactured. Castings can be manufactured in lengths and widths up to 24 in. in +/-0.0005 in. tolerance.
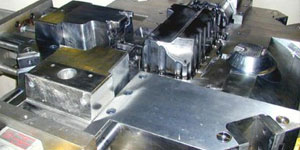
ISO 9001: 2015 certified manufacturer of die cast magnesium, Capabilities include high-pressure magnesium die casting up to 200 ton hot chamber & 3000 ton cold chamber, tooling design, polishing, molding, machining, powder & liquid painting, full QA with CMM capabilities, assembly, packaging & delivery.
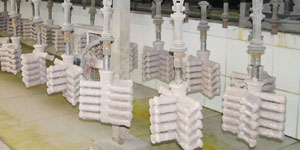
ITAF16949 certified. Additional Casting Service Include investment casting,sand casting,Gravity Casting, Lost Foam Casting,Centrifugal Casting,Vacuum Casting,Permanent Mold Casting,.Capabilities include EDI, engineering assistance, solid modeling and secondary processing.
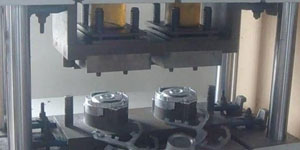
Casting Industries Parts Case Studies for: Cars, Bikes, Aircraft, Musical instruments, Watercraft, Optical devices, Sensors, Models, Electronic devices, Enclosures, Clocks, Machinery, Engines, Furniture, Jewelry, Jigs, Telecom, Lighting, Medical devices, Photographic devices, Robots, Sculptures, Sound equipment, Sporting equipment, Tooling, Toys and more.
What Can we help you do next?
∇ Go To Homepage For Die Casting China
→Casting Parts-Find out what we have done.
→Ralated Tips About Die Casting Services
By Minghe Die Casting Manufacturer |Categories: Helpful Articles |Material Tags: Aluminum Casting, Zinc Casting, Magnesium Casting, Titanium Casting, Stainless Steel Casting, Brass Casting,Bronze Casting,Casting Video,Company History,Aluminum Die Casting |Comments Off