The Cost Analysis Of Precision Castings
Based on the characteristics of all silica sol investment casting process and cost distribution, this paper discusses the components and influencing factors of investment casting cost, analyzes casting manufacturing cost by process method and establishes cost accounting model, so as to provide reference for casting suppliers and casting purchasers to evaluate casting price.
The accounting of casting cost is usually based on the weight of the cost allocation, and the allocation of production costs, especially to be apportioned and accrued expenses and the cost of work in process, may also need to take into account the balance of various economic indicators.
Therefore, the comprehensive kilogram cost calculated by accountants alone can not represent the actual cost of castings, and can not accurately reflect the influence of different castings due to the differences in structure and technology on the cost. Casting pricing can only be determined by multiplying the average price per kilogram by the corresponding floating factor. The floating coefficient is usually determined by comparing with typical castings, or even by feeling. In fact, it is difficult to accurately evaluate the cost and profit and loss of specific castings.
Casting cost can be divided into direct cost and period cost. Direct manufacturing costs can be divided into direct materials, direct labor, fuel and power, manufacturing costs, etc. In order to analyze the cost according to the manufacturing process, the furnace charge (including scrap and ferroalloy) directly forming the casting entity is collected as the direct material, and the wax and shell materials consumed in the manufacturing process are used as the auxiliary materials. The wage, fuel, power and auxiliary materials consumed in the manufacturing process are counted as process cost, which is different from the concept of manufacturing cost in accounting. The depreciation, house rent and financial expenses are incorporated into the enterprise management expenses (the depreciation and rent of production facilities are usually accounted as manufacturing expenses in cost accounting). In this way, direct material and process costs constitute the direct cost of casting, which is also the variable cost of casting. The period cost such as management expense is the fixed cost of an enterprise. The fixed cost shared by casting is actually a part of casting marginal profit, which is affected by enterprise scale, operation mode and product structure. Direct material cost depends on the type of alloy and ingredient cost, which is a relatively transparent cost item in the society. Therefore, this paper focuses on the process cost.
Composition of investment casting process cost
The process of all silica sol investment casting can be divided into four stages: wax mold manufacturing, shell making, melting and pouring, and post-treatment. The cost of inspection and equipment maintenance for these four stages is classified as auxiliary production cost. In the four production processes, the cost in the three stages of wax mold manufacturing, shell making, melting and pouring is closely related to the process yield. It is more accurate to calculate the cost by pouring weight than by casting weight directly.
For example, if the wax mold manufacturing cost is calculated according to the casting weight, the cost relationship between small and large parts is obviously not in line with the reality. Therefore, the more reasonable method is that the cost of wax mold manufacturing, shell making, melting and pouring process (referred to as the front section cost in this paper) is calculated according to the weight of molten steel pouring (referred to as the pouring weight in this paper), and the cost of post-treatment and auxiliary production (referred to as the back section cost in this paper) is calculated according to the weight of casting. The manufacturing cost and its composition calculated according to the weight of molten steel and casting are shown in Table 1, and the proportion of its distribution structure is shown in Figure 1 and Figure 2. It can be seen that the cost of shell making and smelting phase accounts for more than 60% of the process cost.
Main factors affecting cost difference of investment castings
Strictly speaking, the manufacturing cost of different castings in each process is not exactly the same, but the difference in some links is very small, which can be calculated according to the average level. We should pay attention to the factors that have a greater impact on the casting cost. The main factors leading to the difference of casting process cost are as follows:
1. Process yield
Process yield, also known as yield, is the percentage of the actual casting weight in the pouring weight. For a specific casting, the process yield is equal to the percentage of the total casting weight in the same tree. It is related to the casting structure and group plan. It may vary from 30% to 60%, generally between 40-50%. The relationship between the former cost and the process yield is as follows
Front cost per kg casting=Process yield per kg casting weight
The former cost per kilogram of casting is inversely proportional to the process yield. The lower the process yield is, the higher the former cost per unit weight of casting is, and the lower the process yield is, the more significant the influence is. The first stage cost of pouring molten steel per kilogram is 6 yuan. When the process yield is 45%, the first stage cost of casting per kilogram is 13.33 yuan; When the process yield is 30%, the front cost of casting is 20 yuan / kg, which is 6.7 yuan higher than the average level, and the process cost increases by 37.6%. The influence on the total cost of 304 stainless steel casting is about 17%; When the process yield is 60%, the front cost of casting is 10 yuan / kg, which is 3.3 yuan lower than the average level, and the process cost is reduced by 18.5%. For 304 stainless steel casting, the total cost is reduced by about 7%;
When the process yield is 45%, the front cost per kilogram of casting will increase by 0.3 yuan per percentage point, and when the process yield is 30%, For each percentage point reduction, the front cost per kilogram of castings will increase by about 0.67 yuan
It can be seen that the effect of process yield on cost is very significant. Like the power factor in Electrotechnics, reducing the process yield is equivalent to increasing the reactive power consumption. Of course, the higher the process yield is, the better it is, and it is not high to want to be. Too high process yield will reduce the feeding capacity of the gating system, resulting in insufficient feeding and shrinkage porosity or shrinkage defects; On the other hand, some castings, especially thin-walled castings with irregular shape, are difficult to improve the process yield due to the limitation of casting structure and group plan. This important factor should be considered when determining the casting price.
2. Shell layers
Due to the different shape and structure of castings, the number of shell layers will be different. For example, castings with long and thin holes or slots need to be faced twice or even three times; Generally, two backing layers are enough for castings, while three or more backing layers may be required for larger castings. The cost of shell making per kilogram of casting is about 5.9 yuan, of which 67.8% is material cost, 23.9% is fuel and power cost, and 13.3% is salary cost. Among the 4 yuan / kg shell material cost, the consumption of zirconium sand and zirconium powder accounts for about 63%, 42.7% of the whole shell cost, and the cost of silica sol accounts for about 12.2% of the shell cost. Although zirconium sand zirconium powder is only used for surface shell making, it becomes the main item of shell making cost because of its high price.
It can be seen from the table that the cost of the surface layer is about 4.4 times that of the back layer. Moreover, the materials used for the second surface course are more than those used for the first one. According to an increase of 10%, the cost of making an additional surface course is about 6.2 yuan. The average cost per kilogram of casting is increased by 2.7 yuan, and the cost per kilogram of pouring weight is increased by 1.21 yuan. That is to say, the shell making cost per kilogram of casting increases by 45.8% and the process cost per kilogram of casting increases by 15.1%. For 304 stainless steel, the impact on the total cost and price is about 7%. The cost per kilogram of casting increased by 0.56 yuan, and the cost per kilogram of pouring weight increased by 0.25 yuan. The shell making cost per kilogram of casting increases by 9.4%, the process cost per kilogram of casting increases by 3.1%, and the impact on the total cost of 304 casting is only about 1.4%.
2.Difficulty of post-processing
After casting pouring, the qualified castings can only be obtained through the post-treatment processes such as shell crushing and sand cleaning, cutting, grinding, shot blasting, pickling, shaping, repair welding and repair. The average cost of post-treatment can be determined according to the weight of castings. As shown in Table 1, the average cost of post-treatment per kilogram of castings is 3.33 yuan.
The cost of pickling for stainless steel castings is about 0.3 yuan / kg. Although the carbon steel parts do not need pickling, considering that the box needs to be buckled after pouring, and it is difficult to remove sand after bucking, and the finished products need rust prevention and other factors, the cost difference can not be distinguished.
When the structure of castings is different, the process content and difficulty of post-treatment are also different. Generally, after casting, the process of shell crushing, cutting, grinding, shot blasting and so on is OK, while some castings need to increase the process. When the customer requests to add heat treatment, surface treatment, machining and other work content to the casting blank, the cost should be accounted separately and included in the total price, which is not within the scope of this paper. The cost difference of post-treatment mainly comes from sand cleaning, deformation correction and renovation. The cost depends on the casting structure and technical requirements. The cost difference should be considered when determining the price.
- Sand cleaning: it is difficult to clean some castings with long and narrow slots or holes, which can only be cleaned by sand drilling, acid biting, sand blasting or alkali blasting. Such castings require a separate estimate of the cost of sand cleaning.
- Shaping: it is necessary to correct the deformation of the castings which are easy to deform. The difficulty of shaping depends on the casting structure, deformation degree and customer's requirements for dimension and form and position tolerance. The cost of plastic surgery should be calculated separately.
- Renovation: the casting process is a special process, and there are many factors affecting the casting quality. Objectively speaking, surface defects of castings are hard to avoid. Different customers or castings for different purposes have different requirements for surface quality. Before receiving orders, it is very important for the supplier and demander to determine a reasonable quality acceptance standard according to the characteristics of castings and possible surface defects. If the customer's requirements for surface quality are relatively high, the renovation cost will be relatively high. The repair cost is mainly affected by the casting quality requirements and the first pass rate of castings. The former needs to be considered in the pricing, while the latter depends on the internal quality control. The renovation cost can be adjusted by multiplying the average cost of post-processing by an appropriate quality grade coefficient.
Apportionment of administrative expenses
Enterprise management fee is an integral part of the sales cost of product factory, which can be apportioned to specific castings by weight. The pre evaluation of quotation can first determine an expected breakeven Output or average output, and then calculate the management cost per kilogram of castings according to this output. The post evaluation should be distributed according to the actual amount.
Management fee is related to enterprise scale and product structure. Factories with simple and stable product structure need lower management fee, while enterprises with more varieties and high technology content need higher management fee. The management fee level of medium-sized hardware investment casting factory is about 5 yuan per kilogram of castings.
Cost accounting model of investment castings
1. Average product per kg of casting
- Factory sales cost = manufacturing cost + management fee
- Casting manufacturing cost = direct material cost + process cost
- Process cost = front cost + back cost, direct material cost = batching cost × Loss compensation coefficient front cost per kg casting = average cost per kg molten steel pouring + shell making cost
- difference process yield shell making cost difference = secondary surface layer cost ×( Times of surface layer - 1) + cost of back layer ×( Back layer times - 2) post processing cost = average post-processing cost per kg casting × Quality grade coefficientThe raw material loss compensation coefficient is used to compensate the loss caused in the process of smelting, cutting and grinding, which is about 1.1. The difference of shell making cost is calculated by pouring weight. The quality grade coefficient is mainly determined according to the customer's requirements for dimensional accuracy and surface quality, and the value range can be 0.8-1.5.
- By substituting the statistical data into the formula, the casting manufacturing cost = batching cost can be obtained × 1.1+6+1.21 ×( Surface layer number - 1) + 0.25 ×( Back layer number - 2) process yield +4.45 × Quality grade system
- Factory cost of sales = cost of ingredients × 1.1+6+1.21 ×( Surface layer number - 1) + 0.25 ×( Back layer number - 2) process yield + 4.45 × Quality grade coefficient + 5
According to the above method, the process cost and factory cost (yuan / kg) per kg of 304 stainless steel conventional casting with different process yield and different shell making scheme are calculated
2. Single casting cost
Casting in the production process, regardless of size, should be carried out one by one according to the specified process. Therefore, the actual cost of the casting is not completely proportional to its weight, especially for very small castings, the cost deviation calculated by weight is large. We calculate the casting unit cost according to the weighted average of the average kilogram cost and the unit cost by 9:1. Expressed as
- Cost of sales of casting factory = (cost of batching kg) × 1.1 + management fee per kg of casting) × Casting weight + process cost per kg ×( Casting weight × 0.9 + combined average weight × 1) + supplementary process cost
- Substituting the measured data, we get the following results:
- Cost of sales of casting factory = (cost of batching kg) × 1.1 + management fee per kg of casting) × Casting weight+
- (6+1.21 ×( Surface layer number - 1) + 0.25 ×( Back layer number - 2) process yield + 4.45 × Quality grade coefficient) ×( Casting weight × 0.9 + 0.012) + supplementary process cost
Supplementary process cost refers to the cost of sand cleaning (such as sand drilling, acid biting, sand blasting, alkali blasting, etc.) and shaping and other additional processes. The cost of heat treatment, surface treatment, welding and machining outside the casting process should be calculated separately, which is not in the scope of this paper.
The Price evaluation of castings
After the cost of the casting is clear, the evaluation of the price of the casting is easy. Casting price evaluation is divided into pre-evaluation and post-evaluation. The purpose of pre-assessment is to quote, and the purpose of post-assessment is to analyze profit and loss. There are unknown factors in the pre-assessment. The standard cost can be estimated based on the statistical analysis of historical data. During the post-assessment, the various expenses are known, and the expenses can be collected according to the specific product. The allocation of expenses should be as consistent as possible with the actual situation.
The basis of casting price evaluation is the cost of sales of the factory, in addition to the expected profit, sales tax, sales expenses, etc. Expressed by the formula as
Casting price = factory sales cost + expected profit + sales tax + sales expense
Among them, there are many factors that need to be considered in determining the expected profit, and the range of change is also relatively large, generally around 15%. In summary, the main factors that need to be considered for expected profits are as follows:
- Market factors: including average profit levels in the same industry, market competition conditions, etc. Because in the buyer's market conditions, prices are ultimately determined by the market. It should be said that the final price is the result of reaching a balance in market competition. Therefore, pricing that is out of the market can only be the same idea.
- Casting characteristics: mainly including casting technical content, material, batch size, etc. The market for castings with small technical difficulties, large batches, and strong material versatility is often fierce, and the expected profit of castings cannot be too high; on the contrary, the expected profit of castings with high technical difficulty, long development cycle or small batches and not commonly used materials is expected to be profitable. It can be more demanding.
- Settlement method: The main consideration in the settlement method is the payback period. The production and operation process of an enterprise is actually a process of capital flow and value-added. The invested capital is transformed into a product through the production process, and then the payment is recovered through the sales process to complete a capital cycle. In such a cycle, the capital gains value and the company gains profits. The shorter the cycle, the faster the capital turnover, the more profits will be accumulated. Taking into account the cost of capital operation, the time value of capital, and the role of capital appreciation, the impact of the payment recovery period on profits cannot be ignored.
- Production capacity utilization rate: An important factor that needs to be considered in determining the expected profit is the company's production capacity utilization rate. If the factory has surplus production capacity and is not fully utilized, it is actually a waste of resources. In this case, the expected profit rate can be lower, or even zero or negative. A negative expected profit does not necessarily increase the loss. As long as the price excludes direct costs, taxes, and sales expenses, there is a remaining part that can share part of the management fee, and it can provide a marginal contribution to the growth of the company's total profit. This is the concept of marginal profit in management accounting. On the contrary, if the production capacity is insufficient, some castings will not lose money according to the conventional calculation. If its marginal profit rate is not high and consume more resources, it will actually reduce the production capacity of high-margin profit castings. This opportunity loss can also be As the cost of the product, it is called opportunity cost in management accounting. In this case, it is necessary to increase the expected profit margin and optimize the product structure.
Postscript: It should be pointed out that the purpose of this article is to explore the factors affecting the cost of investment castings and to scientifically evaluate the cost of investment castings. Since the actual cost levels of various investment casting plants are not the same, the statistics cited in this article are for reference only. The cost collection method adopted in this article is not completely consistent with the conventional industrial accounting practices, and needs to be identified when data collection.
Please keep the source and address of this article for reprinting:The Cost Analysis Of Precision Castings
Minghe Die Casting Company are dedicated to manufacture and provide quality and high performance Casting Parts(metal die casting parts range mainly include Thin-Wall Die Casting,Hot Chamber Die Casting,Cold Chamber Die Casting),Round Service(Die Casting Service,Cnc Machining,Mold Making,Surface Treatment).Any custom Aluminum die casting, magnesium or Zamak/zinc die casting and other castings requirements are welcome to contact us.
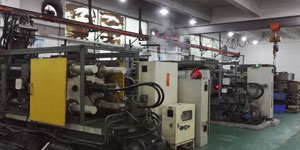
Under the control of ISO9001 and TS 16949,All processes are carried out through hundreds of advanced die casting machines, 5-axis machines, and other facilities, ranging from blasters to Ultra Sonic washing machines.Minghe not only has advanced equipment but also have professional team of experienced engineers,operators and inspectors to make the customer’s design come true.
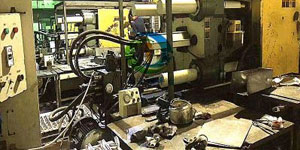
Contract manufacturer of die castings. Capabilities include cold chamber aluminum die casting parts from 0.15 lbs. to 6 lbs., quick change set up, and machining. Value-added services include polishing, vibrating, deburring, shot blasting, painting, plating, coating, assembly, and tooling. Materials worked with include alloys such as 360, 380, 383, and 413.
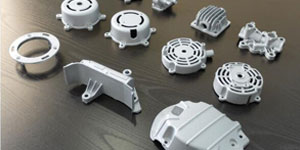
Zinc die casting design assistance/concurrent engineering services. Custom manufacturer of precision zinc die castings. Miniature castings, high pressure die castings, multi-slide mold castings, conventional mold castings, unit die and independent die castings and cavity sealed castings can be manufactured. Castings can be manufactured in lengths and widths up to 24 in. in +/-0.0005 in. tolerance.
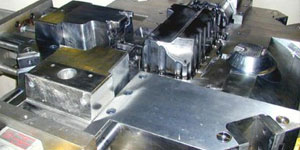
ISO 9001: 2015 certified manufacturer of die cast magnesium, Capabilities include high-pressure magnesium die casting up to 200 ton hot chamber & 3000 ton cold chamber, tooling design, polishing, molding, machining, powder & liquid painting, full QA with CMM capabilities, assembly, packaging & delivery.
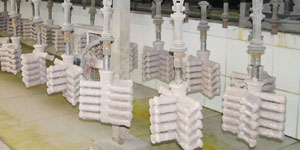
ITAF16949 certified. Additional Casting Service Include investment casting,sand casting,Gravity Casting, Lost Foam Casting,Centrifugal Casting,Vacuum Casting,Permanent Mold Casting,.Capabilities include EDI, engineering assistance, solid modeling and secondary processing.
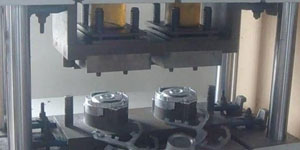
Casting Industries Parts Case Studies for: Cars, Bikes, Aircraft, Musical instruments, Watercraft, Optical devices, Sensors, Models, Electronic devices, Enclosures, Clocks, Machinery, Engines, Furniture, Jewelry, Jigs, Telecom, Lighting, Medical devices, Photographic devices, Robots, Sculptures, Sound equipment, Sporting equipment, Tooling, Toys and more.
What Can we help you do next?
∇ Go To Homepage For Die Casting China
→Casting Parts-Find out what we have done.
→Ralated Tips About Die Casting Services
By Minghe Die Casting Manufacturer |Categories: Helpful Articles |Material Tags: Aluminum Casting, Zinc Casting, Magnesium Casting, Titanium Casting, Stainless Steel Casting, Brass Casting,Bronze Casting,Casting Video,Company History,Aluminum Die Casting |Comments Off