The Current Status And Development Of Nodular Cast Iron And Spheroidizing Agent
It has been 52 years since the advent of ductile iron, and its rapid development is surprising. Even in the economic downturn, ductile iron is still developing. Some people call ductile iron a winner in inappropriate retreat, pointing out: Because of its high strength, high toughness and low price, cast iron still occupies an important position in the material market. Although the total output of steel casting has declined in the past few years, the output of ductile iron has not declined. The emergence of Ao-Bei ductile iron Enhance the competitive position of ductile iron.
The production and research status of ductile iron
3.1 Conventional Ductile Iron
At present, conventional ductile iron-that is, ductile iron based on ferrite and pearlite still accounts for most of the production of ductile iron. Therefore, attention should be paid to improving the performance and quality of conventional ductile iron to maintain the competitive position of ductile iron. Played an important role.
3.2 Strengthen the control of the elements that affect the quality of ductile iron
The structure and properties of ductile iron depend on the composition and crystallization conditions of the cast iron and the quality of the spheroidizing agent used. It is believed that in order to ensure the mechanical properties of ductile iron, the specific wall thickness, pouring temperature, spheroidizing agent used, and spheroidizing treatment of the casting must be considered. The optimization of process and cooling parameters and effective slag discharge measures are strictly controlled, and appropriate reduction of carbon equivalent, alloying and heat treatment are effective measures to improve ductile iron.
3.3 Effectively control the production of ferritic ductile iron and spheroidal ductile iron
The main elements that control the ductile iron matrix are the composition of cast iron, the type of spheroidizing agent and inoculant used, the method of adding, and the cooling conditions. The composition of as-cast ferritic ductile iron is slightly hypereutectic. The carbon is slightly higher, but no graphite floats. The silicon content is slightly lower. The silicon content of the inoculant should be less than 3%. The lower the manganese, the better. Mn<0.04%, sulfur and phosphorus should be low, so that S≦0.02%, P≦0.02%, this is because silicon can improve ductile iron structure and corresponding plasticity, Si=3.0~3.5% can obtain all ferrite structure. Some studies have pointed out that when Si=2.6~2.8%, cast iron has the highest elongation and impact toughness, but the micro segregation of silicon in iron increases with the increase of phosphorus content, the more serious the segregation, and the impact on mechanical properties.
The adverse effect, especially when the temperature is below zero, is greater, and when the sulfur content is low, low-magnesium and low-rare earth spheroidizing agents can be used to spheroidize, and reduce the generation of "black spots" defects, and the "black spots" are mainly magnesium, Aggregate of cerium sulfide and oxide, in addition, low-silica spheroidizing agent should be used to ensure multiple inoculations.
For pearlitic ductile iron, the manganese content of cast iron can be increased to 0.8-1.0% during production. If some castings are used as wear-resistant crankshafts, manganese can be increased to 1.2-1.35% to produce cast pearlite elements. Copper. When the amount of addition is greater than 1.8%, it hinders the spheroidization of graphite, but promotes the complete pearlization of the matrix. Generally, the copper content in ductile iron should be less than 1.5%. Tin is a strong pearlitizing element, and its impact on hardness is greater than that of copper. And manganese, but Sn ≥ 1.0% will cause graphite distortion, so its content should be limited to 0.08% or less.
3.4 The role of rare earth in ductile iron
Rare earth can promote the spheroidization effect of magnesium alloy (spheroidization rate and roundness of the ball). It pays attention to the effect of preventing the distortion of spheroidal graphite in the wall thick nodular iron. This is also included in the spheroidizing agent at home and abroad. One of the main reasons for rare earths. There are some elements in the casting that can destroy and hinder the spheroidization of graphite. These elements are the so-called spheroidization interference elements.
The interference elements are divided into two categories. One is the consumption of spheroidization element-type interference elements, which form MgS, MgO, MgS, MgO, and MgS with magnesium and rare earth. MgSe, RE2O3, RE2S3, RE2Te3, etc., reduce the spheroidizing elements and destroy the formation of spheroidal graphite; the other type is intergranular segregation interference elements, including tin, antimony, arsenic, copper, titanium, aluminum, etc. during eutectic crystallization These elements are enriched in the grain boundary and promote the formation of deformed dendritic graphite by carbon in the later stage of eutectic. The larger the atomic weight of the spheroidizing interference element, the stronger the interference effect. Many studies have now found interference elements in cast iron. When the content of these elements is less than the critical content, distorted graphite cannot be formed. In cast iron with interfering elements, the addition of rare earth can eliminate its interference effect.
A research report pointed out that the sum of interfering elements in cast iron should be less than 0.10%, that is, z=Ti+Cr+Sb+V+As+Pb+Zn+…<0.10 %Studies have pointed out that to neutralize Al, Sb, TI, Pb, Bi, etc. in the molten iron, as long as adding 0.005 to 0.04% Ce respectively, for example, to neutralize Ti, Pb, Sb, Al, etc., as long as adding 0.005 to 0.007% respectively. , 0.014%, 0.15% and 0.008% Ce. Interfering elements have a greater destructive effect when the casting wall is dense and the cooling rate is slow.
Interfering elements also have an effect on the matrix of ductile iron.
Te and B strongly promote the formation of white mouth, Cr, As, Sn, Sb, Pb, Bi stabilize pearlite, and Al and Zr promote ferrite. It is worth noting that some are currently being developed Spheroidizing elements and interfering elements compound spheroidizing agent to improve the treatment effect of large section ductile iron and the roundness of graphite balls.
3.5 Nodular iron detection enhancement
Ductile iron inspection is an important measure to ensure its quality. At present, the development line analysis is being studied, that is, the product is analyzed during the production process to determine its quality. Many units have used ultrasonic waves to perform the quality of castings under mass production conditions. analysis.
When measuring the structure of cast iron by ultrasonic wave, the sound velocity of flake graphite is 4500m/s, vermicular graphite cast iron is 5400m/s, and ductile cast iron is 5600m/s. In addition, the change of high-frequency attenuation rate in cast iron can also judge the type of cast iron, ductile iron The center frequency is 5MHz and the flake cast iron is only 1.5MHz. At present, there are still units using ultrasonic waves to determine the spheroidization level, and it is possible to determine the qualified spheroidization level and unqualified products (between level 3 and level 4) , But it is not yet possible to carry out a more detailed level measurement, this method is being improved.
3.6 Current status of nodulizer
Nodularizing agent is currently one of the main means to obtain nodular iron. When Zhibao Steel Rare Earth No. 1 Plant jointly completed the national research project "rare earth three-agent serialization", the research team of our school conducted more than 100 nodularizing agent production plants in the world. , The main domestic alloy production has been investigated, and product samples of more than 50 alloy production plants in more than a dozen countries such as the United Kingdom, the United States, France, Germany, Japan, the Soviet Union, and India have been obtained, as well as product samples of major domestic nodulizer manufacturers. It provides a basis for comparing the performance of spheroidizing agent at home and abroad and improving the production of spheroidizing agent in the future. 2.1 The types of spheroidizing agents are divided into the following types according to the production mode
- The types of spheroidizing agents include magnesium-silicon alloys, rare earth magnesium-silicon alloys, calcium-based alloys (mostly used in Japan), nickel-magnesium Series alloys, pure magnesium alloys, rare earth alloys. Among the above alloys, the most widely used in the world is the rare earth magnesium ferrosilicon alloy, but the RE/Mg ratio of Chinese alloys is wide (0.5~2.2), while the RE/Mg ratio of foreign alloys is small (0.1~0.3) . In Chinese alloys, the rare earth content is greater than or equal to magnesium content, and the rare earth content is less than the magnesium content. However, the content of rare earth in the nodulizer alloys in foreign countries (except for some alloys in Russia and Russia) is almost less than the content of magnesium. Therefore, the three-agent series of rare earths The research team suggested that in addition to retaining FeSlMg8E18 (this alloy is an excellent vermicularizing agent), RE/Mg≦1 in all other spheroidizing agents. This recommendation was adopted in the subsequent revised national standards. The calcium-magnesium spheroidizing agent is mainly from Japan Production and application, such as the calcium alloy NC5, NCl0, NCl5, NC20, NC25 produced by Shin-Etsu (SHIN-ETSU), the magnesium content varies from 4 to 28%, but the calcium content varies slightly, and the variation range is 20 to 31 %; This kind of alloy has a small tendency to white mouth, but requires high processing temperature and large amount of slag after processing. Nickel-magnesium alloys are used in the Americas and Europe. The nickel-magnesium alloys produced by the United States International Nickel Company are up to 82-85%, of which Mg and Ca are 13-16 and 20 respectively, and the lowest nickel-magnesium alloy is 57-61% (Mg4 .0~4.5%, Ca<2.5, Fe32~36). In the nickel-magnesium alloy produced by German Metal Chemical Company, Ni47~51%, Mgl5~17%, C1.0%Si28~32%, RE1.0% more than Fe. The advantages of these alloys are that the specificity is large, the reflection is stable, and the nickel can rise. Alloying is characterized by its high price, and this alloy is basically not used in China. Nickel-silicon alloys are basically no longer used in China. Pure magnesium alloys must be treated with a special pressure and a magnesium bag. The absorption rate of magnesium is high, but the handling safety measures must be extremely strict, and the proportion of applications in production is small. Rare earth is the spheroidizing agent used in the invention of ductile iron, and its discovery has promoted the process of industrial application of ductile iron. However, the price is high and the white mouth tends to be large. Excessive excess will make graphite metamorphose. Now it is not used as a spheroidizing agent alone, but only as an auxiliary spheroidizing element.
- The briquette spheroidizing agent is directly molded by magnesium powder and iron powder and the designed silicon content. This spheroidizing agent contains very low silicon and is usually called a low-silicon briquetting spheroidizing agent. Subsequent incubation provides a large room for the production of as-cast ductile iron, but this alloy is easy to float, and the treatment effect fluctuates greatly. It is best to mix it with a block spheroidizing agent during treatment.
- The cored wire type spheroidizing agent coats the magnesium powder and iron powder in the thin steel plate or steel plate, and sends them into the molten iron to achieve the purpose of spheroidization. This kind of spheroidizing agent is more expensive and the equipment investment is large, but The alloy has a high absorption rate during processing, so the total cost of processing ductile iron is hardly increased.
- The powdered spheroidizing agent is a Russian patent. When used, the magnesium powder and the inhibitor are mixed and put into the bag, and the molten iron flows through the surface of the alloy, layer by layer, and the alloy is reflected to achieve spheroidization. Effect, this special process is called MC. 2.2 Application of spheroidizing agent.At present, pyrometallurgical alloys are mainly used in the production of ductile iron at home and abroad, briquetting spheroidizing agent, cored wire spheroidizing agent, powdered ball The spheroidizing agent used in pyrometallurgical smelting accounts for more than 90% of the production.
At present, Ba, Ca, Cu, Ni, etc. are added to this type of alloy to achieve the purpose of controlling the matrix, and the content of magnesium oxide in the alloy There are limited indicators.
The cupola of the melting equipment accounts for 30%, the induction furnace accounts for 63%, and the spheroidizing temperature of 1482~1538°C accounts for 75%; 50% of the factories adopt the pre-desulfurization process before the spheroidizing treatment, and 90% of the factories S Less than 0.025%. In the spheroidizing treatment method, the flushing method accounts for 36% of the large American factories, while the small factory (less than 200 ton/week) the flushing method accounts for only 22%. The press-in method, the porous plug method, Type internal treatment method, Tundish cover method, pressure and magnesium method account for most of the proportions. The spheroidizing agent used contains more than% of magnesium accounted for 8.2%, Mg4~6% accounted for 63.3, and contained less than 4% magnesium. It accounts for 16.4%, pure magnesium accounts for 5%, and other magnesium alloys account for 8.2%.
The production of spheroidizing agent in my country has changed a lot from 90 years to now. The national standard of rare earth magnesium alloy has been revised, and the RE in the alloy has been greatly adjusted. Except for the retention of Mg8RE18, the Mg/Re in other alloys is greater than 1. The amount of rare earth in the alloy used in the factory has decreased, the application of Mg8RE5─7 alloy has increased greatly, and the electric furnace has also increased a lot, but the sulfur content in the raw molten iron has not changed much, and the pre-desulfurization process has not been effectively promoted. Therefore, my country The Mg and BE in the spheroidizing agent are still at a relatively high level, and the new spheroidizing process has not been promoted much in my country. For example, the Tundish capping method, which occupies a large proportion in the United States, has hardly been applied in my country. It is a problem to be solved in my country's ductile iron production plants.
3.7 Problems in the use of spheroidizing agent and quality element control indicators
The elements that affect the quality of the spheroidizing agent are: composition, particle size, shape, density, MgO content and so on. Here is only the analysis of the spheroidizing agent produced by pyrometallurgical smelting, and cite many problems reflected in the use of factories:
- (1) The composition of the spheroidizing agent is inaccurate.
- (2) The particle size of the spheroidizing agent powdered alloy does not meet the requirements.
- (3) The density of the spheroidizing agent fluctuates greatly, and some spheroidizing agents float quickly, and the response is too intense, which is not guaranteed.
- (4) The content of MgO is too high, the spheroidizing treatment is poor, and the amount of the spheroidizing agent added is too large.
- (5) Fast decline after spheroidization.
- (6) After spheroidization, the white mouth tends to be large.
To solve the above problems, we should start from two aspects:
- First, the alloy manufacturer provides products of qualified quality. it is necessary to improve the analysis of magnesium oxide;
- secondly, strictly control raw materials, control the elements that promote alloy powdering and interference elements, strengthen management;
- thirdly, strictly implement accurate smelting processes, and control the main indicators that affect the quality of nodulizers;
- fourthly It is to provide the granularity required by users. On the other hand, the production workers are trained and trained so that they understand the characteristics of the alloy and the accurate method of use.
The problems in production are directly related to the quality of the production workers. Some workers just teach what to do and cannot draw analogies. This is not feasible. The cooperation of alloy manufacturers and users is needed to popularize and improve the understanding of ductile iron and the level of production technology, so that the production of ductile iron in my country can maintain a good momentum of development.
3.8 Application of computer in the production of ductile iron
Due to its paste-like solidification characteristics, the cast iron produced by ductile iron often produces defects such as shrinkage cavity and porosity due to poor feeding. In order to predict these defects before the production of castings, the casting process was carried out at home and abroad as early as the Indian era. Numerical analogy. Numerical analogy in the casting process is to use numerical analogy technology to simulate the actual casting forming process in a computer virtual environment, including the filling process of the metal liquid, the cooling and solidification process, the stress formation process, the judgment of the influence of the main elements in the forming process, and the prediction The organization, performance and possible defects provide a basis for optimizing the process to reduce waste. In 1962, Forsund in Denmark was the first to use an electronic computer to simulate the solidification process of castings.
Since then, the United States, Britain, Germany, Japan, and France have successively carried out research in this area. Since the end of the 1970s in China, Dalian University of Technology and Shenyang Foundry Research Institute took the lead in conducting research on this technology in China, and published research reports in 1980 (Guo Keren, etc., Digital Analogy of Solidification Process of Large Castings, Dalian Institute of Technology Journal, 1980 (2) 1-16; Shenyang Foundry Research Institute, Computer Analogy of Casting Solidification Thermal Field, Foundry, Since then, a lot of manpower has been invested in Chinese universities and colleges to carry out this research. During the Sixth Five-Year Plan and the Seventh Five-Year Plan, there are key research projects for the application of computers in foundry in the central part of the national key research projects. Foundry technology CAD" organized joint research on production, education, and research, which greatly promoted the development of this technology in China. At present, Tsinghua University and Huazhong University of Science and Technology can provide FT-Star and Huazhu CAE-Inte CAST 4.0 commercial chemistry respectively. The software has been applied in Sanming Heavy Machinery Co., Ltd. and other units, and has achieved good results. The computer numerical analogy consists of three parts: pre-processing, intermediate calculation and post-processing, including the establishment of geometric models, grid division, and solution conditions (initial conditions).
And boundary conditions) determination, numerical calculation, calculation results processing and graphic display. The basic methods of numerical analogy used are mainly finite difference method, finite element method and boundary element method. At present, more fields of application in casting are :
- 1) Numerical analogy of solidification process, mainly for heat transfer analysis of casting process. Including the selection of numerical calculation method, latent heat treatment, shrinkage cavity shrinkage prediction and discrimination, and treatment of heat transfer problems at the interface of castings and molds.
- 2) The numerical analogy of the flow field involves the transfer of momentum, energy and mass, which is more difficult. The numerical solution techniques used are MAC method, SAMC method, SOLA-AOF method and SOLA-MAC method.
- 3) Casting stress analogy. This research was carried out late, mainly focusing on stress analysis in the elasto-plastic state.
At present, there are Heyn model, elasto-plastic model, Perzyna model, unified internal variable model and so on. 4) Organizational analogy is still in its infancy. Divided into macro vision, middle vision and micro vision analogy. It can calculate the number of nucleation, analyze the type of primary crystal, the growth rate of dendrite, the transformation of analogy structure, and predict the mechanical properties. At present, there are deterministic models, such as Monte, Cellular, Automaton and other statistical methods, and phase field models. Computers and their applications are currently rapidly developing technical fields. As one of the important industrial fields, foundry should increase investment.
The research and development of the application of computers in the field of casting research and production has completely changed the state of "open eyes, closed eyes pouring" in the past, and the application of computers will definitely promote the application and development of ductile iron. It has been 52 years since the advent of ductile iron, and its rapid development is surprising. Even in the economic downturn, ductile iron is still developing.
Some people call ductile iron a winner in inappropriate retreat, pointing out: Because of its high strength, high toughness and low price, cast iron still occupies an important position in the material market. Although the total output of steel casting has declined in the past few years, the output of ductile iron has not declined. The emergence of Ao-Bei ductile iron Enhance the competitive position of ductile iron.
Please keep the source and address of this article for reprinting: The Current Status And Development Of Nodular Cast Iron And Spheroidizing Agent
Minghe Die Casting Company are dedicated to manufacture and provide quality and high performance Casting Parts(metal die casting parts range mainly include Thin-Wall Die Casting,Hot Chamber Die Casting,Cold Chamber Die Casting),Round Service(Die Casting Service,Cnc Machining,Mold Making,Surface Treatment).Any custom Aluminum die casting, magnesium or Zamak/zinc die casting and other castings requirements are welcome to contact us.
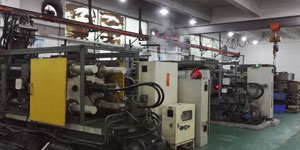
Under the control of ISO9001 and TS 16949,All processes are carried out through hundreds of advanced die casting machines, 5-axis machines, and other facilities, ranging from blasters to Ultra Sonic washing machines.Minghe not only has advanced equipment but also have professional team of experienced engineers,operators and inspectors to make the customer’s design come true.
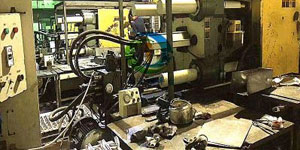
Contract manufacturer of die castings. Capabilities include cold chamber aluminum die casting parts from 0.15 lbs. to 6 lbs., quick change set up, and machining. Value-added services include polishing, vibrating, deburring, shot blasting, painting, plating, coating, assembly, and tooling. Materials worked with include alloys such as 360, 380, 383, and 413.
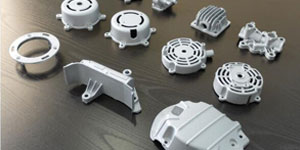
Zinc die casting design assistance/concurrent engineering services. Custom manufacturer of precision zinc die castings. Miniature castings, high pressure die castings, multi-slide mold castings, conventional mold castings, unit die and independent die castings and cavity sealed castings can be manufactured. Castings can be manufactured in lengths and widths up to 24 in. in +/-0.0005 in. tolerance.
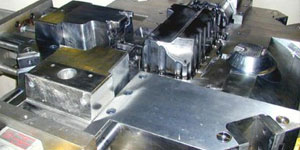
ISO 9001: 2015 certified manufacturer of die cast magnesium, Capabilities include high-pressure magnesium die casting up to 200 ton hot chamber & 3000 ton cold chamber, tooling design, polishing, molding, machining, powder & liquid painting, full QA with CMM capabilities, assembly, packaging & delivery.
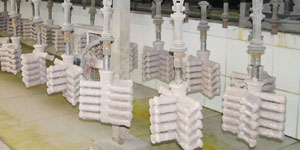
ITAF16949 certified. Additional Casting Service Include investment casting,sand casting,Gravity Casting, Lost Foam Casting,Centrifugal Casting,Vacuum Casting,Permanent Mold Casting,.Capabilities include EDI, engineering assistance, solid modeling and secondary processing.
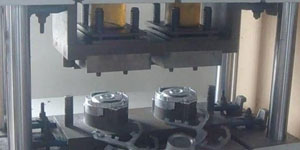
Casting Industries Parts Case Studies for: Cars, Bikes, Aircraft, Musical instruments, Watercraft, Optical devices, Sensors, Models, Electronic devices, Enclosures, Clocks, Machinery, Engines, Furniture, Jewelry, Jigs, Telecom, Lighting, Medical devices, Photographic devices, Robots, Sculptures, Sound equipment, Sporting equipment, Tooling, Toys and more.
What Can we help you do next?
∇ Go To Homepage For Die Casting China
→Casting Parts-Find out what we have done.
→Ralated Tips About Die Casting Services
By Minghe Die Casting Manufacturer |Categories: Helpful Articles |Material Tags: Aluminum Casting, Zinc Casting, Magnesium Casting, Titanium Casting, Stainless Steel Casting, Brass Casting,Bronze Casting,Casting Video,Company History,Aluminum Die Casting |Comments Off