The Defects Often Caused By Improper Forging Process
1. Large grains
Large grains are usually caused by excessively high initial forging temperature and insufficient deformation, or excessively high final forging temperature, or the degree of deformation falling into the critical deformation zone. The deformation of aluminum alloy is too large to form texture; the deformation temperature of superalloy is too low, and the formation of mixed deformation structure may also cause coarse grains. Coarse grains will reduce the plasticity and toughness of forgings, and the fatigue performance will be significantly reduced.
2. Uneven grains
Uneven grains means that the grains in some parts of the forging are particularly coarse, but some parts are smaller. The main reason for the uneven grain is that the uneven deformation of the billet makes the degree of grain breakage different, or the deformation degree of the local area falls into the critical deformation zone, or the local work hardening of the superalloy, or the local grain during quenching and heating Gross.
3. Chilling phenomenon
Due to low temperature or too fast deformation speed during deformation, and too fast cooling after forging, it is possible that the softening caused by recrystallization cannot keep up with the strengthening (hardening) caused by deformation, so that part of the forging remains cold deformation after hot forging. organization. The existence of this structure improves the strength and hardness of the forging, but reduces the plasticity and toughness. Severe cold and hard phenomena may cause forging cracks.
4. Crack
Cracks are usually caused by large tensile stress, shear stress or additional tensile stress during forging. The place where the crack occurs is usually the place where the billet has the largest stress and the thinnest thickness. If there are micro-cracks on the surface and inside of the blank, or there are structural defects in the blank, or the plasticity of the material is reduced due to improper hot working temperature, or the deformation speed is too fast, the degree of deformation is too large, and the plasticity index of the material is exceeded, then the roughing, Cracks may occur in processes such as drawing, punching, reaming, bending and extrusion.
5. Cracking
Cracks are shallow turtle-like cracks on the surface of forgings. In the forming of forgings, the surface subjected to tensile stress is most prone to such defects.
The internal factors that cause the cracks may be various:
- ①The raw materials contain too much fusible elements such as Cu and Sn.
- ② When heated at high temperature for a long time, there will be copper precipitation on the surface of the steel material, coarse surface grains, decarburization, or the surface after repeated heating.
- ③The sulfur content of the fuel is too high, and there is sulfur infiltrating the surface of the steel material.
6. Flash cracks
Flash cracks are cracks generated at the parting surface during die forging and trimming. The causes of flash cracks may be:
- ①In the die forging operation, due to the heavy blow, the metal flows strongly to produce the phenomenon of penetrating ribs.
- ②The trimming temperature of magnesium alloy die forgings is too low; the trimming temperature of copper alloy die forgings is too high.
7. Parting surface crack
Parting surface cracks refer to cracks that occur along the parting surface of forgings. There are many non-metallic inclusions in the raw materials, which flow and concentrate to the parting surface during die forging, or the residue of shrinking tube often forms parting surface cracks after squeezing the flash during die forging.
8. Fold
Folds are formed by the fusion of surface metals that have been oxidized during metal deformation. It can be formed by the confluence of two (or more) metal convections; it can also be formed by the rapid and large flow of a metal that brings the surface metal of the adjacent part to flow, and the two converge; it can also be formed by deformation The metal is formed by bending and reflowing; it can also be formed by partial deformation of part of the metal and being pressed into another part of the metal. Folding not only reduces the bearing area of the part, but also tends to become a source of fatigue due to the stress concentration here during work.
9. Flow through
Flow through is a form of improper distribution of streamlines. In the flow-through area, the streamlines originally distributed at a certain angle merge together to form a flow-through, and the grain size in the flow-through area and outside may be quite different. The cause of flow through is similar to folding. It is formed by the confluence of two strands of metal or one strand of metal with another strand of metal, but the metal in the through portion is still a whole, and the through flow reduces the mechanical properties of the forging, especially When the crystal grains on both sides of the flow zone are quite different, the performance degradation is more obvious.
10. Irregular distribution of forging streamlines
The streamline distribution of forgings is not smoothly refers to the occurrence of streamline turbulence, such as streamline cutting, backflow, and eddy current, on the forging at low power. If the mold design is improper or the forging method is unreasonably selected, the flow lines of the prefabricated blanks will be disordered; the uneven flow of the metal caused by the improper operation of the workers and the wear of the mold can make the flow lines of the forgings unevenly distributed. Irregular streamlines will reduce various mechanical properties, so for important forgings, there are requirements for streamline distribution.
11. Casting structure residue
Casting structure residues mainly appear in forgings using ingots as billets. The as-cast structure mainly remains in the difficult deformation zone of the forging. Insufficient forging ratio and improper forging method are the main reasons for the residual casting structure. The residual casting structure will reduce the performance of the forging, especially the impact toughness and fatigue performance.
12. The level of carbide segregation does not meet the requirements
The level of carbide segregation does not meet the requirements mainly in the ledeburite tool steel. The main reason is the uneven distribution of carbides in the forgings, which are distributed in large blocks or in a network. The main reason for this defect is the poor level of carbide segregation in the raw material, and the insufficient forging ratio or improper forging method during forging. Forgings with such defects are prone to local overheating and quenching during heat treatment and quenching. The finished cutting tools and molds Easy to break when used.
13. Ribbon tissue
Banded structure is a kind of organization in which ferrite and pearlite, ferrite and austenite, ferrite and bainite, and ferrite and martensite are distributed in bands in forgings. This organization, It is the band structure produced during forging deformation under the condition of two phases coexisting that can reduce the material's transverse plasticity index, especially the impact toughness. It is often easy to crack along the ferrite band or the junction of the two phases during forging or parts work
14. Insufficient local filling
Local insufficient filling mainly occurs in ribs, lobes, corners, and rounded corners, and the size does not meet the requirements of the drawing.
The reasons may be:
- ①Low forging temperature and poor metal fluidity;
- ②Insufficient equipment tonnage or insufficient hammering force;
- ③Unreasonable design of blanking die, unqualified blank volume or cross-sectional size;
- ④Oximum accumulation or welding in the mold cavity He deformed metal.
15. Undervoltage
Undervoltage refers to the general increase in the size perpendicular to the parting surface.
The reasons may be:
- ①The forging temperature is low.
- ②Insufficient equipment tonnage, insufficient hammering force or insufficient hammering times.
16. Misshift
Misalignment is the displacement of the upper half of the forging relative to the lower half along the parting surface.
The reasons may be:
- ①The gap between the slider (hammer head) and the guide rail is too large;
- ②The forging die design is unreasonable, and the lock or guide post to eliminate the misalignment force is missing;
- ③The mold is poorly installed.
Please keep the source and address of this article for reprinting:The Defects Often Caused By Improper Forging Process
Minghe Die Casting Company are dedicated to manufacture and provide quality and high performance Casting Parts(metal die casting parts range mainly include Thin-Wall Die Casting,Hot Chamber Die Casting,Cold Chamber Die Casting),Round Service(Die Casting Service,Cnc Machining,Mold Making,Surface Treatment).Any custom Aluminum die casting, magnesium or Zamak/zinc die casting and other castings requirements are welcome to contact us.
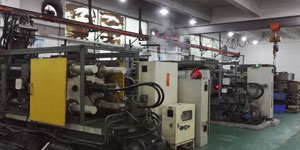
Under the control of ISO9001 and TS 16949,All processes are carried out through hundreds of advanced die casting machines, 5-axis machines, and other facilities, ranging from blasters to Ultra Sonic washing machines.Minghe not only has advanced equipment but also have professional team of experienced engineers,operators and inspectors to make the customer’s design come true.
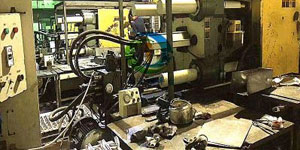
Contract manufacturer of die castings. Capabilities include cold chamber aluminum die casting parts from 0.15 lbs. to 6 lbs., quick change set up, and machining. Value-added services include polishing, vibrating, deburring, shot blasting, painting, plating, coating, assembly, and tooling. Materials worked with include alloys such as 360, 380, 383, and 413.
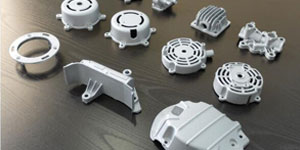
Zinc die casting design assistance/concurrent engineering services. Custom manufacturer of precision zinc die castings. Miniature castings, high pressure die castings, multi-slide mold castings, conventional mold castings, unit die and independent die castings and cavity sealed castings can be manufactured. Castings can be manufactured in lengths and widths up to 24 in. in +/-0.0005 in. tolerance.
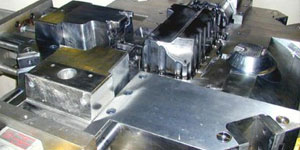
ISO 9001: 2015 certified manufacturer of die cast magnesium, Capabilities include high-pressure magnesium die casting up to 200 ton hot chamber & 3000 ton cold chamber, tooling design, polishing, molding, machining, powder & liquid painting, full QA with CMM capabilities, assembly, packaging & delivery.
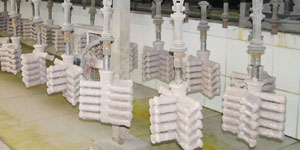
ITAF16949 certified. Additional Casting Service Include investment casting,sand casting,Gravity Casting, Lost Foam Casting,Centrifugal Casting,Vacuum Casting,Permanent Mold Casting,.Capabilities include EDI, engineering assistance, solid modeling and secondary processing.
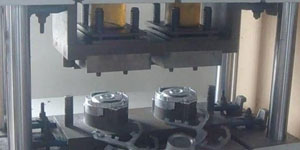
Casting Industries Parts Case Studies for: Cars, Bikes, Aircraft, Musical instruments, Watercraft, Optical devices, Sensors, Models, Electronic devices, Enclosures, Clocks, Machinery, Engines, Furniture, Jewelry, Jigs, Telecom, Lighting, Medical devices, Photographic devices, Robots, Sculptures, Sound equipment, Sporting equipment, Tooling, Toys and more.
What Can we help you do next?
∇ Go To Homepage For Die Casting China
→Casting Parts-Find out what we have done.
→Ralated Tips About Die Casting Services
By Minghe Die Casting Manufacturer |Categories: Helpful Articles |Material Tags: Aluminum Casting, Zinc Casting, Magnesium Casting, Titanium Casting, Stainless Steel Casting, Brass Casting,Bronze Casting,Casting Video,Company History,Aluminum Die Casting |Comments Off