The Deformation Control Of Carburized Gear Heat Treatment
Heat treatment deformation of carburized gear. Heat treatment deformation directly affects the accuracy, strength, noise and life of the gear. Even if the gear grinding process is added after the carburizing heat treatment, the deformation still reduces the accuracy level of the gear.
There are many factors that affect the deformation of carburizing heat treatment, and only by controlling various factors can the deformation be controlled to a small extent. Controlling the deformation of gears must also be solved in the whole process of manufacturing gears.
- The test of the influence of metallurgical factors of gear material on deformation shows that the higher the hardenability of steel. The greater the deformation. When the core hardness is higher than 40HRC, the deformation will increase significantly. Therefore, there are certain requirements for the hardenability of steel, the narrower the hardenability band. The more stable the deformation, the steel mill is required to provide "low and stable deformation" steel. The A1/N content ratio is controlled within the range of 1 to 2.5, which can narrow the hardenability band and reduce deformation. In addition, the box segregation and band structure of the material affect the uneven deformation and uneven carburization of the gear spline hole.
- The effect of preliminary heat treatment on gear deformation. Excessive normalizing hardness, mixed crystals, a large amount of sorbite or Widmanstat will increase the deformation of the inner hole, so temperature control normalizing or isothermal annealing should be used to treat forgings.
- The effect of carburizing process on deformation The uniformity of temperature. The uniformity of the carbon layer and the uniformity of the cooling medium temperature all affect the deformation of the gear. At the same time, the higher the carburizing temperature, the thicker the carburizing layer. Low oil temperature and large gear deformation. Therefore, it is necessary to improve the equipment, optimize the process, and improve the quality of gear heat treatment.
- The effect of quenching on deformation. Quenching cooling behavior is the most important factor affecting gear deformation. Hot oil quenching has less deformation than cold oil quenching, and is generally controlled at 100℃±120℃. The cooling capacity of the oil is also critical to deformation. Stirring method and intensity affect the deformation, the disk gears quenched by the upper quenching press, according to the deformation of various gears. Adjust the parameters of the flushing press to reduce the deformation, adjust the pressure of the inner and outer die and the expansion block, the size of each section of the fuel injection, and the upper work table to control the deformation.
- The clamping method and the purpose of the fixture are to make the workpiece evenly heated and cooled, and the carburized layer of each part of the workpiece is uniform to reduce the uneven thermal stress and the uneven structural stress to reduce deformation. The clamping method can be changed. The oil level is vertical, the shaft parts are installed vertically, using compensation washers, supporting washers, superimposed washers, etc., spline hole parts can be carburized mandrels, etc.
- Coordination in mechanical processing: first. Grasp the heat treatment deformation law, move the tolerance zone position, and improve the product qualification rate; second, according to the deformation law, apply anti-deformation, and shrink the end pre-expansion hole to improve the deformation qualification rate after quenching; third, for asymmetric or uneven thickness parts Using the method of reserved processing volume. Process after heat treatment. Fourth, after heat treatment, use a push knife to finish the spline hole, or electrolytically process the spline hole, or heat the mandrel after carburization for quenching, and then press out the mandrel to ensure the size of the spline hole to reduce deformation.
Please keep the source and address of this article for reprinting: The Deformation Control Of Carburized Gear Heat Treatment
Minghe Die Casting Company are dedicated to manufacture and provide quality and high performance Casting Parts(metal die casting parts range mainly include Thin-Wall Die Casting,Hot Chamber Die Casting,Cold Chamber Die Casting),Round Service(Die Casting Service,Cnc Machining,Mold Making,Surface Treatment).Any custom Aluminum die casting, magnesium or Zamak/zinc die casting and other castings requirements are welcome to contact us.
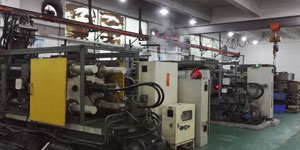
Under the control of ISO9001 and TS 16949,All processes are carried out through hundreds of advanced die casting machines, 5-axis machines, and other facilities, ranging from blasters to Ultra Sonic washing machines.Minghe not only has advanced equipment but also have professional team of experienced engineers,operators and inspectors to make the customer’s design come true.
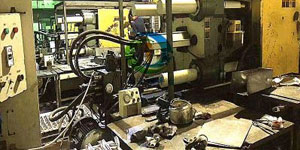
Contract manufacturer of die castings. Capabilities include cold chamber aluminum die casting parts from 0.15 lbs. to 6 lbs., quick change set up, and machining. Value-added services include polishing, vibrating, deburring, shot blasting, painting, plating, coating, assembly, and tooling. Materials worked with include alloys such as 360, 380, 383, and 413.
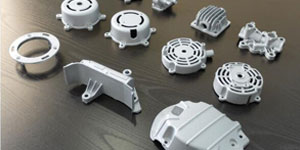
Zinc die casting design assistance/concurrent engineering services. Custom manufacturer of precision zinc die castings. Miniature castings, high pressure die castings, multi-slide mold castings, conventional mold castings, unit die and independent die castings and cavity sealed castings can be manufactured. Castings can be manufactured in lengths and widths up to 24 in. in +/-0.0005 in. tolerance.
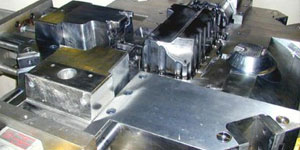
ISO 9001: 2015 certified manufacturer of die cast magnesium, Capabilities include high-pressure magnesium die casting up to 200 ton hot chamber & 3000 ton cold chamber, tooling design, polishing, molding, machining, powder & liquid painting, full QA with CMM capabilities, assembly, packaging & delivery.
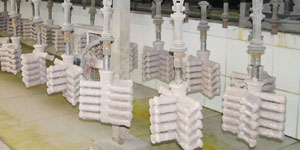
ITAF16949 certified. Additional Casting Service Include investment casting,sand casting,Gravity Casting, Lost Foam Casting,Centrifugal Casting,Vacuum Casting,Permanent Mold Casting,.Capabilities include EDI, engineering assistance, solid modeling and secondary processing.
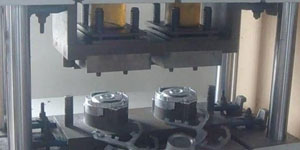
Casting Industries Parts Case Studies for: Cars, Bikes, Aircraft, Musical instruments, Watercraft, Optical devices, Sensors, Models, Electronic devices, Enclosures, Clocks, Machinery, Engines, Furniture, Jewelry, Jigs, Telecom, Lighting, Medical devices, Photographic devices, Robots, Sculptures, Sound equipment, Sporting equipment, Tooling, Toys and more.
What Can we help you do next?
∇ Go To Homepage For Die Casting China
→Casting Parts-Find out what we have done.
→Ralated Tips About Die Casting Services
By Minghe Die Casting Manufacturer |Categories: Helpful Articles |Material Tags: Aluminum Casting, Zinc Casting, Magnesium Casting, Titanium Casting, Stainless Steel Casting, Brass Casting,Bronze Casting,Casting Video,Company History,Aluminum Die Casting |Comments Off