The Design And Manufacture Of Automobile Stamping Dies
Automobile stamping dies are very important to the automobile manufacturing industry. The initial design of the dies, the production process and the later maintenance are the focal points that must be studied. This article starts with stamping die design and maintenance, summarizes the factors considered in automotive stamping die design, and lists common problems and specific solutions in the later use of stamping dies. Mold manufacturing companies should pay attention to mold design and maintenance, which is essential to prolong the service life of molds.
Factors considered in the design of automotive stamping dies
1.1 Meet the requirements of the stamping process
The following points should be paid attention to the stamping dies of automobile panels: First, whether the name of the process mathematical model and the corresponding version number are consistent and correct; second, whether the model and specifications of the used press meet the requirements of use; third, whether the external dimensions of the mold meet the requirements Technical requirements, especially whether the closing height meets the regulations; fourth, pay attention to the direction of the blank and the direction of the workpiece; fifth, the positioning requirements of the blank; sixth, the form of part of the lifting device and unloading device; seventh, the method of removing waste and Transmission direction.
1.2 Easy to install and debug
The installation and debugging of stamping dies is one of the most important tasks in all work. In order to facilitate the installation and commissioning, the commissioning equipment and structure should be installed on the mold to be commissioned. It mainly includes: the positioning structure of the die on the press; the compaction position and structure of the die on the press; the stroke limiter of the mold; the precision detection platform. Sometimes the actual pressure model and the commissioned pressure model are different. When designing these two types of presses, design parameters should be considered.
1.3 Safe and reliable operation
When the stamping die is in use, all parts must operate safely and reliably without any loose displacement. Stable tracking of moving parts requires accurate and reliable positioning. In addition to the parts that have mechanical strength to protect their functions, the assembly must also be accurately positioned and securely clamped. Safety is a problem that mold designers must pay attention to. There must be a safety gap between moving parts and fixed parts. The safety gap must not only consider personal safety, but also the safety of molds and machine tools. If necessary, a special safety facility should be set up, such as protective panels, safety barrier nets, etc.
1.4 Easy to store and keep
The size of the automobile cover stamping die is large, and the opening, overturning, lifting, hoisting and overturning during the process of mold manufacturing, transportation, use, storage and maintenance must be considered when designing. Because the volume of the mold may be relatively large, the storage device designed must carefully consider the storage method and location of the mold, and the deformation of the mold during the storage process should be minimized, and the space should be reasonably optimized. In order to facilitate the management of the mold, obvious signs should be pasted on the protruding positions of the mold. The main contents of the signs include: feeding direction signs, mold codes, etc.
Maintenance of automobile stamping dies
The cost of stamping dies is high, usually 20% to 25% of the total cost of the die. This is because in addition to the high cost of mold production, mold repair and maintenance costs are also high, and the original mold cost only accounts for about 40% of the total mold cost. Therefore, timely maintenance of molds to prevent mold damage can greatly reduce the cost of stamping production molds [1]. After the mold is damaged, there are options for repair and scrapping. Under normal circumstances, the unnatural wear and tear failure of the stamping die, such as the failure of non-critical parts, the fracture of the small punching die, the rise of the punching die, the cracking of the hollow template, the tip of the cutting edge, etc. Most of them can be restored to normal state through maintenance, and then used for stamping production. However, when the key parts of the mold are severely damaged, such as convex and concave damage on the surface of the mold, the one-time maintenance cost may exceed 70% of the cost of the stamping mold, or when the mold is nearly scrapped due to long-term use, the maintenance is of little significance If it fails, you should consider scrapping the mold. If the mold repair technology is too complicated, the cost of repairing the mold is too high, and the repair cycle is too long, which seriously affects the normal production of stamping, you should decisively choose the scrap mold and re-manufacture the mold to replace it. Under normal circumstances, the main failure mode of the mold is excessive wear. Therefore, the research on the failure mode and repair method of the mold is very important. Choosing the correct repair method and treatment method can greatly save costs.
2.1 Mold damage
The general forms of mold damage include mold cracking, breakage, and cracking. If you want to completely solve the problem of mold damage, you must find the cause from the three stages of mold design, manufacturing process, and use. It is necessary to check whether the manufacturing materials of the mold meet the requirements and whether the heating manufacturing process is reasonable. Generally speaking, the process of material heat treatment has a decisive influence on the quality of the mold. If the temperature reached by the quenching is higher than the specified value when the mold is manufactured, the method and the quenching time do not meet the requirements, and the number of tempering is not selected properly, these will cause the mold to be damaged after the stamping production. The size and depth of the hole design does not match the initial design value, which can easily cause the hole and slot to be blocked during the mold manufacturing process, which will eventually cause the drop plate to be damaged. If the design of the spring force value is too small or just reaches the limit value, it will directly cause the spring to break instantaneously, which will cause the descending plate to tilt and eventually damage the components. Insufficient cushioning parts or insufficient strength of the fixing bolts will directly cause the punch to fall or break. In the actual use of the mold, errors in the position of the parts and the installation direction of the parts, the bolts cannot be tightened, the height of the worktable is reduced, and the abnormal failure of the feeding equipment and the press will cause serious damage to the mold. If foreign matter enters the mold without being cleaned up in time, and then continue to work and produce, it is easy to damage the punching board, punch, lower template and guide rail of the mold.
2.2 Card Mode
In the mold stamping process, if the mold is inflexible or even stuck, all production activities must be stopped immediately, the cause of the failure must be found, and the failure must be cleared. Otherwise, the consequences of the failure will be immeasurable. The main reasons for card die failure are: improper adjustment of feeder distance, pressure, and loosening of feeder; variation of feeder distance during production; feeder failure; material arc, width is out of tolerance, and large burrs; die stamping abnormality, sickle bend Insufficient hole diameter of the material guide, the upper die pulls the material; the bending or tearing position is not smoothly stripped; the stripping function of the guide plate is set improperly; the material is too thin, and warping occurs during the feeding process; the mold is improperly erected, The deviation from the verticality of the feeder is large. When the above situation occurs, the mold must be readjusted and repaired in time. It is necessary to change the material regularly, control the quality of the feed, eliminate the sickle bend of the material belt and repair the convex and concave molds of the punching and guiding holes. Adjust the force of the stripping spring and modify the guide material to prevent the occurrence of the tape on the material belt. A safety switch for up and down pressing and up and down extrusion is installed between the feeder and the mold, and the mold needs to be re-erected if necessary.
2.3 Deformation of flanging plastic parts
In the process of flanging and shaping, the deformation of the part often occurs. Under normal circumstances, if the deformation occurs on a non-surface part, it will not have much impact on the quality of the part. But if it is a surface part, it will be very serious, because a little deformation will bring fatal quality defects to the appearance and affect the appearance of the whole car. When the part is formed and flanged, the sheet material is prone to deformation and rotation, and deformation will occur if the material is not tightly pressed. Even if the pressing force is large enough, if the surface of the pressing surface is uneven and there are gaps, it will cause the occurrence of the above-mentioned situation. If this happens, you need to increase the pressure of the material. If the pressing surface used is spring pressing, the solution of increasing the spring can be adopted; if it is the air cushion pressing, the solution of increasing the atmospheric pressure should be adopted. After the pressure is increased, if there is local deformation, the red Dan marked the problem points, checked whether there were dents in the part of the binder surface, and welded the binder plate.
2.4 Knife edge chipping
The phenomenon of edge chipping is also very common in the process of mold use, and it is a maintenance focus of stamping molds. There are many reasons for it, no matter which one will have an impact on the quality of the mold. Generally, it will be dealt with according to the situation of edge chipping. When the degree of chipping is small, it is necessary to use a grinder to polish the chipped edge, and then fix it by welding to prevent the occurrence of secondary chipping. Welding needs to be carried out with an electrode suitable for the mold material, and generally welding is carried out by surfacing.
2.5 Sharpening maintenance
In the stamping process, the mold can be sharpened appropriately, which can effectively improve the service life of the mold, save the cost of the mold, and greatly reduce the product cost. When the edge of the cutting edge is worn to a certain extent, the original sharp edge will become blunt, resulting in excessive burrs on the blanking part and reducing dimensional accuracy. Therefore, the mold must be sharpened to restore its sharp cutting edge, reduce the burrs of the incision and the deviation of the size and shape, and improve the surface flatness of the formed part. If you do not grind the mold in time and use a dull blade to cut, there will be burr friction in the mold during use, which greatly shortens the service life of the mold. When the burr amount of the manufactured part exceeds the allowable burr amount, production should be stopped immediately,
Automobile stamping dies occupies an important position in the automobile manufacturing industry. The quality of stamping dies is closely related to the design, production and final maintenance. Therefore, it is necessary to improve the design requirements of stamping dies and change the situation from the root cause. After all, molds are consumable equipment, and problems will inevitably occur in later use. Therefore, improving maintenance technology is essential to prolong the service life of molds.
Please keep the source and address of this article for reprinting:The Design And Manufacture Of Automobile Stamping Dies
Minghe Die Casting Company are dedicated to manufacture and provide quality and high performance Casting Parts(metal die casting parts range mainly include Thin-Wall Die Casting,Hot Chamber Die Casting,Cold Chamber Die Casting),Round Service(Die Casting Service,Cnc Machining,Mold Making,Surface Treatment).Any custom Aluminum die casting, magnesium or Zamak/zinc die casting and other castings requirements are welcome to contact us.
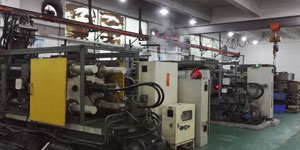
Under the control of ISO9001 and TS 16949,All processes are carried out through hundreds of advanced die casting machines, 5-axis machines, and other facilities, ranging from blasters to Ultra Sonic washing machines.Minghe not only has advanced equipment but also have professional team of experienced engineers,operators and inspectors to make the customer’s design come true.
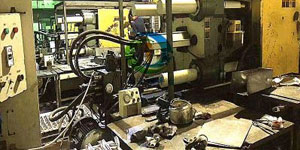
Contract manufacturer of die castings. Capabilities include cold chamber aluminum die casting parts from 0.15 lbs. to 6 lbs., quick change set up, and machining. Value-added services include polishing, vibrating, deburring, shot blasting, painting, plating, coating, assembly, and tooling. Materials worked with include alloys such as 360, 380, 383, and 413.
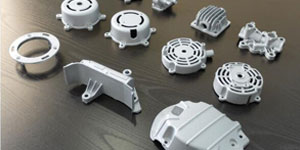
Zinc die casting design assistance/concurrent engineering services. Custom manufacturer of precision zinc die castings. Miniature castings, high pressure die castings, multi-slide mold castings, conventional mold castings, unit die and independent die castings and cavity sealed castings can be manufactured. Castings can be manufactured in lengths and widths up to 24 in. in +/-0.0005 in. tolerance.
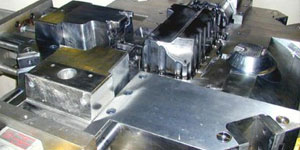
ISO 9001: 2015 certified manufacturer of die cast magnesium, Capabilities include high-pressure magnesium die casting up to 200 ton hot chamber & 3000 ton cold chamber, tooling design, polishing, molding, machining, powder & liquid painting, full QA with CMM capabilities, assembly, packaging & delivery.
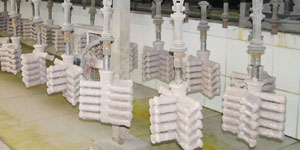
ITAF16949 certified. Additional Casting Service Include investment casting,sand casting,Gravity Casting, Lost Foam Casting,Centrifugal Casting,Vacuum Casting,Permanent Mold Casting,.Capabilities include EDI, engineering assistance, solid modeling and secondary processing.
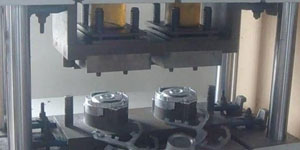
Casting Industries Parts Case Studies for: Cars, Bikes, Aircraft, Musical instruments, Watercraft, Optical devices, Sensors, Models, Electronic devices, Enclosures, Clocks, Machinery, Engines, Furniture, Jewelry, Jigs, Telecom, Lighting, Medical devices, Photographic devices, Robots, Sculptures, Sound equipment, Sporting equipment, Tooling, Toys and more.
What Can we help you do next?
∇ Go To Homepage For Die Casting China
→Casting Parts-Find out what we have done.
→Ralated Tips About Die Casting Services
By Minghe Die Casting Manufacturer |Categories: Helpful Articles |Material Tags: Aluminum Casting, Zinc Casting, Magnesium Casting, Titanium Casting, Stainless Steel Casting, Brass Casting,Bronze Casting,Casting Video,Company History,Aluminum Die Casting |Comments Off