The Design Of Multi-Station Progressive Die
Multi-station progressive die is a high-precision, high-efficiency, and long-life die developed on the basis of ordinary progressive die. It is an important representative of technology-intensive die and one of the development directions of die.
In addition to punching and blanking, this kind of mold can also complete forming processes such as beading, punching, bending, and deep drawing according to the characteristics and forming properties of the part structure. It can even complete the assembly process in the mold. When stamping, after the strip or strip is fed from the entrance end of the mold, under the condition of strictly controlling the step accuracy, in accordance with the order of the forming process, through the continuous stamping of each station, the final station is punched or punched. After cutting, stamping parts that meet product requirements can be punched out. In order to ensure the normal operation of the multi-station progressive die, the die must have a high-precision guidance and an accurate distance system, equipped with automatic feeding, automatic discharging, safety detection and other devices.
Therefore, the multi-station progressive die is more complicated than the ordinary die, and has the following characteristics:
- In one mold, multiple stamping processes including punching, bending, drawing and forming can be completed; the turnover and repeated positioning process of using multiple molds are reduced, and labor productivity and equipment utilization are significantly improved.
- Since the processes in the progressive die can be dispersed on different stations, there is no problem of the "minimum wall thickness" of the composite die.
- Question, when designing, you can also leave an empty station according to the strength of the mold and the assembly needs of the mold, so as to ensure the strength of the mold and the assembly space.
- Multi-station progressive dies usually have high-precision internal and external guidance (in addition to the high precision of mold base guidance, internal guidance protection must be implemented for small punches) and an accurate distance system to ensure product parts The machining accuracy and mold life.
- Multi-station progressive molds often use high-speed punches to produce stamping parts. The molds use automatic feeding, automatic part ejection, safety inspection and other automatic devices, which are safe to operate and have high production efficiency. At present, the world's most advanced multi-station progressive die has more than 50 stations, and the punching speed is more than 1000 times per minute.
- The structure of the multi-station progressive die is complex, there are many inserts, and the precision of die manufacturing is very high, which brings certain difficulties to the manufacture, debugging and maintenance of the die. At the same time, the mold parts are required to be interchangeable, and the mold parts are required to be replaced quickly, conveniently and reliably after they are worn or damaged. Therefore, the material selection of mold working parts must be good (high-strength high-alloy tool steel, high-speed steel or cemented carbide materials are often used), and advanced cnc machining methods such as slow-moving wire cutting, forming grinding, coordinate boring, and coordinate grinding must be used. Mold.
- Multi-station progressive die is mainly used for punching small and medium-sized parts with thin thickness (generally no more than 2mm), large output, complex shape, and high precision requirements. The precision of parts punched with this kind of mold can reach IT10 level.
It can be seen from the above that the structure of the multi-station progressive die is relatively complex, and the mold design and manufacturing technology requirements are high. At the same time, there are corresponding requirements for stamping equipment and raw materials, and the cost of the mold is high. Therefore, it is necessary to conduct a comprehensive analysis of the workpiece before mold design, and then reasonably determine the stamping process plan of the workpiece, and correctly design the mold structure and mold parts processing procedures to obtain the best technical and economic benefits. Obviously, there are many differences in stamping process, mold structure design and mold processing between using multi-station progressive die for stamping and stamping with ordinary die. This chapter will focus on the differences in stamping process and die design. Place.
Layout Design Of Multi-station Progressive Die
Layout design is one of the keys to the design of multi-station progressive die. Whether the layout drawing is optimized or not is not only related to the use of materials
Rate, the accuracy of the workpiece, the difficulty of mold manufacturing and the die casting service life, etc., are also related to the coordination and stability of the mold stations.
The layout of stamping parts on the strip material must ensure the completion of each stamping process, accurate feeding, and progressive stamping; at the same time, it should be convenient for mold processing, assembly and maintenance. The shape of stamping parts is ever-changing. To design a reasonable layout drawing, you must learn from a large number of reference materials and accumulate practical experience in order to successfully complete the design task.
Please keep the source and address of this article for reprinting:The Design Of Multi-Station Progressive Die
Minghe Die Casting Company are dedicated to manufacture and provide quality and high performance Casting Parts(metal die casting parts range mainly include Thin-Wall Die Casting,Hot Chamber Die Casting,Cold Chamber Die Casting),Round Service(Die Casting Service,Cnc Machining,Mold Making,Surface Treatment).Any custom Aluminum die casting, magnesium or Zamak/zinc die casting and other castings requirements are welcome to contact us.
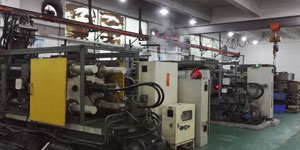
Under the control of ISO9001 and TS 16949,All processes are carried out through hundreds of advanced die casting machines, 5-axis machines, and other facilities, ranging from blasters to Ultra Sonic washing machines.Minghe not only has advanced equipment but also have professional team of experienced engineers,operators and inspectors to make the customer’s design come true.
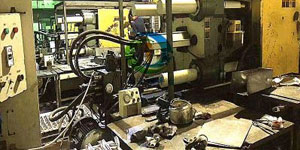
Contract manufacturer of die castings. Capabilities include cold chamber aluminum die casting parts from 0.15 lbs. to 6 lbs., quick change set up, and machining. Value-added services include polishing, vibrating, deburring, shot blasting, painting, plating, coating, assembly, and tooling. Materials worked with include alloys such as 360, 380, 383, and 413.
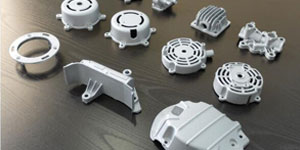
Zinc die casting design assistance/concurrent engineering services. Custom manufacturer of precision zinc die castings. Miniature castings, high pressure die castings, multi-slide mold castings, conventional mold castings, unit die and independent die castings and cavity sealed castings can be manufactured. Castings can be manufactured in lengths and widths up to 24 in. in +/-0.0005 in. tolerance.
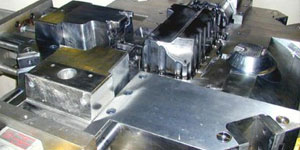
ISO 9001: 2015 certified manufacturer of die cast magnesium, Capabilities include high-pressure magnesium die casting up to 200 ton hot chamber & 3000 ton cold chamber, tooling design, polishing, molding, machining, powder & liquid painting, full QA with CMM capabilities, assembly, packaging & delivery.
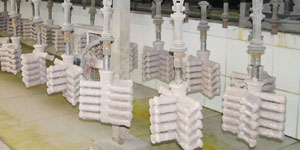
ITAF16949 certified. Additional Casting Service Include investment casting,sand casting,Gravity Casting, Lost Foam Casting,Centrifugal Casting,Vacuum Casting,Permanent Mold Casting,.Capabilities include EDI, engineering assistance, solid modeling and secondary processing.
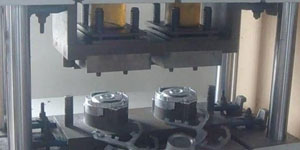
Casting Industries Parts Case Studies for: Cars, Bikes, Aircraft, Musical instruments, Watercraft, Optical devices, Sensors, Models, Electronic devices, Enclosures, Clocks, Machinery, Engines, Furniture, Jewelry, Jigs, Telecom, Lighting, Medical devices, Photographic devices, Robots, Sculptures, Sound equipment, Sporting equipment, Tooling, Toys and more.
What Can we help you do next?
∇ Go To Homepage For Die Casting China
→Casting Parts-Find out what we have done.
→Ralated Tips About Die Casting Services
By Minghe Die Casting Manufacturer |Categories: Helpful Articles |Material Tags: Aluminum Casting, Zinc Casting, Magnesium Casting, Titanium Casting, Stainless Steel Casting, Brass Casting,Bronze Casting,Casting Video,Company History,Aluminum Die Casting |Comments Off