The Development Of Electric Arc Furnace Steelmaking Clean Production Technology
The clean technology includes two aspects: improving the cleanliness of steel and reducing the load on the external environment. It is a production technology that consumes waste iron and steel materials from the society and recycles them. It does not consume non-renewable resources and uses the cleanest energy-electricity. The development of electric arc furnace steelmaking itself is the development of clean production.
In addition, the clean development of electric arc furnace steelmaking technology is as follows.
(1) Clean steel production.
- ① Increase the proportion of pure iron sources in the raw materials (such as direct reduced iron and molten iron);
- ② Low-oxygen smelting, control the terminal molten steel Wr0≤450×10;
- ③ Slag modification;
- ④ Clean steel refining process;
- ⑤ Molten steel protection pouring;
- ⑥ Electromagnetic braking and large inclusion control technology.
(2) Reduce environmental load.
- ① Electric arc furnace steelmaking uses clean energy;
- ② The si removal process is adopted to reduce the amount of slag;
- ③ Promote gas recovery technology;
- ④ Development of preheating technology for electric arc furnace scrap steel;
- ⑤ Refined slag and steelmaking recycling technology;
- ⑥ Dust recovery and treatment technology.
Significant technological progress in recent years
Electric arc furnace steelmaking production technology has made great progress in recent years. Following the surging of compact small steel mills in the 1960s, it has changed the unique situation of joint enterprises. In recent years, some electric arc furnace short-flow steel mills using cutting-edge technology integration have been produced.
- (1) Cremona ESP endless rolling strip mill of Alvidi, Italy. The company has built the world's first ArvediESP endless rolling strip steel plant, including a 250t electric arc furnace, two 250t ladle refining furnaces and an ESP endless strip rolling production line. The designed annual production capacity is 2 million tons, which can produce strip steel with a thickness of 0.8-12.0mm and a width of 1590mm.
- (2) The Crawfordsville plant of Nucor Corporation, USA. In the electric arc furnace steelmaking workshop after the company’s transformation, there is no heating device between the casting machine and the hot rolling stand. The strip passes through the hot rolling stand. 50,000 tons. Using the Casttrip process, due to the high cooling rate, short solidification time, and high drawing speed (generally 80-1500m/min), it has high productivity and can obtain extremely fine microstructures.
- (3) MesabiNuggetITmk3 factory of Kobe Steel, Japan. ITmk3 (IronTeChnologyMarkm) is known as the third-generation ironmaking method. It is a coal-based direct reduction technology that uses rotary hearth furnaces to produce high-quality pig iron jointly developed by Kobe Steel Corporation of Japan and Midland Corporation of the United States. Pulverized coal directly obtains molten iron. Using this technology, iron ore powder can be smelted into slag-free, symmetrical and nearly pure granular iron within 10 minutes.
Please keep the source and address of this article for reprinting: The Development Of Electric Arc Furnace Steelmaking Clean Production Technology
Minghe Die Casting Company are dedicated to manufacture and provide quality and high performance Casting Parts(metal die casting parts range mainly include Thin-Wall Die Casting,Hot Chamber Die Casting,Cold Chamber Die Casting),Round Service(Die Casting Service,Cnc Machining,Mold Making,Surface Treatment).Any custom Aluminum die casting, magnesium or Zamak/zinc die casting and other castings requirements are welcome to contact us.
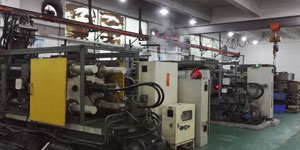
Under the control of ISO9001 and TS 16949,All processes are carried out through hundreds of advanced die casting machines, 5-axis machines, and other facilities, ranging from blasters to Ultra Sonic washing machines.Minghe not only has advanced equipment but also have professional team of experienced engineers,operators and inspectors to make the customer’s design come true.
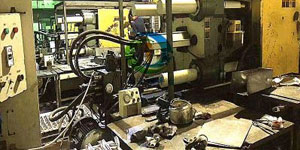
Contract manufacturer of die castings. Capabilities include cold chamber aluminum die casting parts from 0.15 lbs. to 6 lbs., quick change set up, and machining. Value-added services include polishing, vibrating, deburring, shot blasting, painting, plating, coating, assembly, and tooling. Materials worked with include alloys such as 360, 380, 383, and 413.
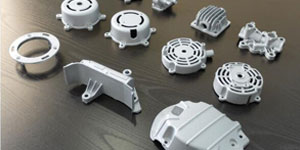
Zinc die casting design assistance/concurrent engineering services. Custom manufacturer of precision zinc die castings. Miniature castings, high pressure die castings, multi-slide mold castings, conventional mold castings, unit die and independent die castings and cavity sealed castings can be manufactured. Castings can be manufactured in lengths and widths up to 24 in. in +/-0.0005 in. tolerance.
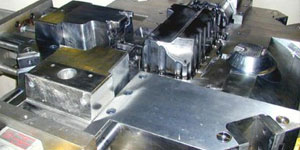
ISO 9001: 2015 certified manufacturer of die cast magnesium, Capabilities include high-pressure magnesium die casting up to 200 ton hot chamber & 3000 ton cold chamber, tooling design, polishing, molding, machining, powder & liquid painting, full QA with CMM capabilities, assembly, packaging & delivery.
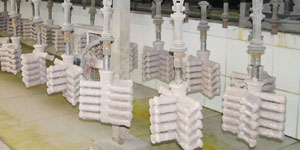
ITAF16949 certified. Additional Casting Service Include investment casting,sand casting,Gravity Casting, Lost Foam Casting,Centrifugal Casting,Vacuum Casting,Permanent Mold Casting,.Capabilities include EDI, engineering assistance, solid modeling and secondary processing.
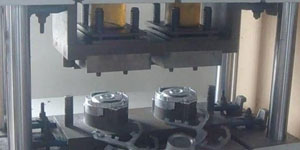
Casting Industries Parts Case Studies for: Cars, Bikes, Aircraft, Musical instruments, Watercraft, Optical devices, Sensors, Models, Electronic devices, Enclosures, Clocks, Machinery, Engines, Furniture, Jewelry, Jigs, Telecom, Lighting, Medical devices, Photographic devices, Robots, Sculptures, Sound equipment, Sporting equipment, Tooling, Toys and more.
What Can we help you do next?
∇ Go To Homepage For Die Casting China
→Casting Parts-Find out what we have done.
→Ralated Tips About Die Casting Services
By Minghe Die Casting Manufacturer |Categories: Helpful Articles |Material Tags: Aluminum Casting, Zinc Casting, Magnesium Casting, Titanium Casting, Stainless Steel Casting, Brass Casting,Bronze Casting,Casting Video,Company History,Aluminum Die Casting |Comments Off