The Diagnosis Of Die Casting Product Defects
The die casting process is a complex process. The pass rate of die-casting products is generally between 70% and 90%. The factors that affect die-casting products are as follows: the performance of the machine itself; various working parameters of the machine; the structure and performance of the die-casting mold (mold); the quality of the die-casting alloy And the skill of the operator. In order to improve die-casting production efficiency and product qualification rate, operators must have a certain ability to prevent and eliminate product defects.
The Case analysis of defect diagnosis of die-casting products
When castings have defects, the reasons for the defects should be analyzed, and generally considered from the following aspects:
- Adjust the machine (adjust the die casting process parameters);
- Material change (change to another material or change the ratio of new material to recycled material);
- Modified type (mold) with structure (inner gate, overflow groove, exhaust groove).
1. Analyze Ideas
- First, analyze the alloy composition to determine the quality of the alloy material and the degree of influence on the defect.
- Defect parts can be cut open, metallographic analysis can be carried out to judge the influence of die casting process factors.
- Re-analyze the model (mold) tool plan.
- Inspection of the smelting process.
2. Take Measures
- Adjust process parameters: filling speed, filling time, mold temperature, etc.
- Refueling: changing to another brand of material; the ratio of new material to recycled material.
- Modified (mold) tools: internal gate, water jet angle, overflow groove, exhaust groove.
Case Analysis
1. Preliminary Understanding
- Casting name: car carburetor body;
- Die casting alloy: ADC12;
- Defects: air leaks after processing, and the scrap rate is over 40%.
2. Analysis Process And Solution
*Conduct chemical analysis of alloy composition, and list the analysis table, see Table 1.
Analysis result: Zn content is 2%, Fe content is about 3%, which greatly exceeds the specified value.
Impurity Zn: High temperature brittleness, so that the casting has a tendency to crack.
Impurity Fe: When Fe content is less than 0.7%, welding with die-casting mold (die) will occur; the content of 0.8-1.0% is better for die-casting, but if the content exceeds 1.3%, metal compounds will be produced and physical properties will be reduced. It is one of the causes of shrinkage cavities and shrinkage cracks.
Solution: Control the impurity content in the alloy raw materials.
*Metallographic Analysis
Analysis result: It is found that the basic structure has coarse crystals, iron-zinc-silicon compounds, pores and shrinkage cavities.
Solution: Control the impurity content in the alloy composition and adjust the die-casting process.
*Take Measures To The Alloy Smelting Process
It is estimated that the gas content in the molten metal is relatively high. In the holding furnace, degassing with argon is used for 15 minutes.
*Re-Analyze The Model (Mold) Tool Plan
- When the exhaust is insufficient, the size of the exhaust slot can be increased, and more exhaust ports can be added.
- Use chilled exhaust block or vacuum die-casting method to increase the air discharge in the large cavity.
- The auxiliary gate is added at the shrinkage cavity (leakage) to improve the transmission effect of casting pressure.
*Die casting process parameters
- Reasonably setting the start point of slow injection and fast injection can reduce the phenomenon of molten metal entrapment gas. Modify the position of rapid switching in the original process, and select the position of rapid switching before the thick part of the side wall of the casting (where the shrinkage cavity is generated).
- The gate speed is increased to 40-50m/s.
- Lower molten metal pouring temperature: 680℃-690℃ down to 670℃±5℃
- Lower mold temperature: 200℃ down 160℃
*Effect: The scrap rate after processing is reduced to below 5%.
Die casting product defect types, causes and solutions
1. The causes of flow marks are as follows, which should be corrected in time after the cause is found out.
- The mold temperature is too low.
- Poor runner design and poor position of the inner gate.
- The material temperature is too low.
- The filling speed is low and the filling time is short.
- The pouring system is unreasonable.
- Poor exhaust.
- The spray is unreasonable.
2. The pattern is caused by too much paint in the cavity or poor paint quality. The solutions and prevention methods are as follows:
- Adjust the cross-sectional area or position of the inner runner.
- Increase the mold temperature.
- Adjust the speed and pressure of the inner runner.
- Appropriate selection of paint and adjustment of dosage.
Net-like hairy wings (cracked turtle)
Appearance inspection: The surface of the die-casting part has bulging or depressed traces like net-like hair, which will expand and extend as the number of die-casting increases, as shown in Figure 2.
The reasons are as follows:
- There are cracks on the surface of the die-casting mold (mold) cavity;
- The preheating of the die-casting mold (mold) is uneven.
The solutions and prevention methods are:
- The die-casting mold (mold) should be annealed regularly or after a certain number of die-casting to eliminate the stress in the cavity.
- If tortoise cracks have appeared on the surface of the cavity, the molding surface should be polished to remove the cracked layer.
- The preheating of the mold (mold) must be even.
Cold Partition
Appearance inspection: The surface of the die casting has obvious, irregular, and sinking linear lines (both penetrating and non-penetrating). The shape is small and long, sometimes the junction edge is smooth, and there is a possibility of disconnection under the action of external force, such as As shown in Figure 3.
The reasons are as follows:
- The two metal streams are connected to each other, but they are not completely fused and there are no inclusions in between, and the bonding force of the two metals is very weak;
- Pouring temperature or die-casting mold (mold) temperature is too low;
- The runner position is wrong or the flow path is too long;
- The filling speed is low.
The solutions and prevention methods are:
- Properly increase the pouring temperature;
- Improve the injection ratio and shorten the filling time and increase the injection speed.
- Improve exhaust and filling conditions.
Shrinkage (Dents)
Visual inspection: There are smooth dents (like discs) on the most thick surface of the die casting.
The reasons are as follows:
1. Caused by contraction
- Improper design of die-casting parts with too large wall thickness difference;
- Improper runner position;
- The injection pressure is low and the pressure holding time is short;
- The local temperature of the die-casting mold (mold) is too high.
2. The cooling system design is unreasonable;
3. Opening (mold) is too early;
4. The pouring temperature is too high.
The solutions and prevention methods are:
- The wall thickness should be uniform;
- The thickness transition should be eased;
- Correctly select the alloy liquid introduction position and increase the cross-sectional area of the inner runner;
- Increase injection pressure
Please keep the source and address of this article for reprinting: The Diagnosis Of Die Casting Product Defects
Minghe Die Casting Company are dedicated to manufacture and provide quality and high performance Casting Parts(metal die casting parts range mainly include Thin-Wall Die Casting,Hot Chamber Die Casting,Cold Chamber Die Casting),Round Service(Die Casting Service,Cnc Machining,Mold Making,Surface Treatment).Any custom Aluminum die casting, magnesium or Zamak/zinc die casting and other castings requirements are welcome to contact us.
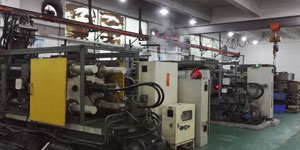
Under the control of ISO9001 and TS 16949,All processes are carried out through hundreds of advanced die casting machines, 5-axis machines, and other facilities, ranging from blasters to Ultra Sonic washing machines.Minghe not only has advanced equipment but also have professional team of experienced engineers,operators and inspectors to make the customer’s design come true.
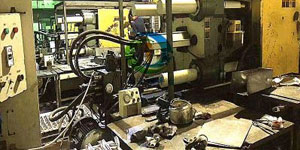
Contract manufacturer of die castings. Capabilities include cold chamber aluminum die casting parts from 0.15 lbs. to 6 lbs., quick change set up, and machining. Value-added services include polishing, vibrating, deburring, shot blasting, painting, plating, coating, assembly, and tooling. Materials worked with include alloys such as 360, 380, 383, and 413.
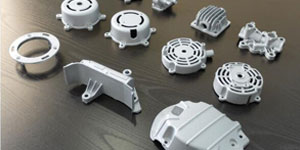
Zinc die casting design assistance/concurrent engineering services. Custom manufacturer of precision zinc die castings. Miniature castings, high pressure die castings, multi-slide mold castings, conventional mold castings, unit die and independent die castings and cavity sealed castings can be manufactured. Castings can be manufactured in lengths and widths up to 24 in. in +/-0.0005 in. tolerance.
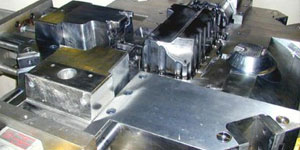
ISO 9001: 2015 certified manufacturer of die cast magnesium, Capabilities include high-pressure magnesium die casting up to 200 ton hot chamber & 3000 ton cold chamber, tooling design, polishing, molding, machining, powder & liquid painting, full QA with CMM capabilities, assembly, packaging & delivery.
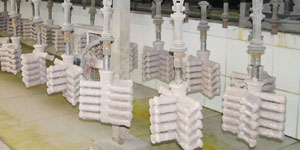
ITAF16949 certified. Additional Casting Service Include investment casting,sand casting,Gravity Casting, Lost Foam Casting,Centrifugal Casting,Vacuum Casting,Permanent Mold Casting,.Capabilities include EDI, engineering assistance, solid modeling and secondary processing.
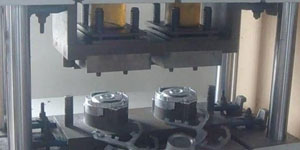
Casting Industries Parts Case Studies for: Cars, Bikes, Aircraft, Musical instruments, Watercraft, Optical devices, Sensors, Models, Electronic devices, Enclosures, Clocks, Machinery, Engines, Furniture, Jewelry, Jigs, Telecom, Lighting, Medical devices, Photographic devices, Robots, Sculptures, Sound equipment, Sporting equipment, Tooling, Toys and more.
What Can we help you do next?
∇ Go To Homepage For Die Casting China
→Casting Parts-Find out what we have done.
→Ralated Tips About Die Casting Services
By Minghe Die Casting Manufacturer |Categories: Helpful Articles |Material Tags: Aluminum Casting, Zinc Casting, Magnesium Casting, Titanium Casting, Stainless Steel Casting, Brass Casting,Bronze Casting,Casting Video,Company History,Aluminum Die Casting |Comments Off