The Difference Between Die Casting And Stamping
Stamping processing is the processing technology that makes the stamping parts directly receive force and deform in the mold with the help of the power of conventional or special stamping equipment to obtain a certain shape. The mold used for stamping is called a stamping die, which is Special tools for batch processing of metal raw materials or non-metallic materials, punching dies are very important in the processing of stamping parts;
Stamping processing has many unique advantages in terms of technology and economy; the main advantages are high production efficiency, convenient operation, and easy realization of mechanization and automation.
Die casting is a method of casting die forging. The die-casting die forging process is a dedicated process performed on a die-casting die forging machine. It is a method of pouring the fusion gold liquid into the press chamber to fill the cavity of the steel mold at high speed. And make the alloy liquid solidify under pressure to form a casting method;
The basic process of die-casting is that the molten metal is first filled into the cavity of the mold at low or high speed. The mold has a movable cavity surface. It is pressurized forged with the cooling process of the molten metal, which eliminates the shrinkage of the blank. Shrinkage defects also make the internal structure of the blank reach broken grains in the forged state, and the comprehensive mechanical properties of the blank have been significantly improved. In addition, the rough produced by this process has a surface finish of 7 (Ra1.6), which is like the surface produced by cold extrusion or machining, with metallic luster. Therefore, we call the die-casting die forging process "Ultimate Forming Process"
The Difference Between Die Casting Parts And Stamping
Although they are all metal processing techniques, there are big differences between them:
Metal stamping is a process that uses punches and molds to deform or break stainless steel, iron, aluminum, copper and other plates and other materials to achieve a certain shape and size.
Die-casting is a kind of pressure-casting parts. It uses a pressure-casting mechanical die-casting machine equipped with a casting mold to pour the heated liquid copper, zinc, aluminum or aluminum alloy into the inlet of the die-casting machine, and pass it through the die-casting machine. Die casting is to cast copper, zinc, aluminum parts or aluminum alloy parts of the shape and size restricted by the mold. Such parts are usually called die-casting parts.
Die casting and stamping are both the processing and forming methods of parts, but die casting uses pressure to fill the mold with liquid metal to obtain the same parts as the mold; stamping uses the function of the mold to remove some parts of the solid metal to obtain the required parts .
The Difference Between Die Casting Mold And Stamping Mold
Stamping is divided into cold stamping and hot stamping. Compared with cold stamping, the hot stamping process can effectively take into account the issues of lightweight and collision safety, and high-strength stamping parts springback and die wear. Hot stamping is realized through its forming die. Whether the design of the die is reasonable or not will directly affect the efficiency of hot stamping.
The design and manufacturing methods of hot stamping dies are mainly divided into four types: drilling type, layered type, shower type and casting type.
1. Drilling type
The drilling type realizes the arrangement of the insert cooling system by arranging the pipes as follows to the maximum extent under the convex-concave model surface. The advantages are easy processing, easy replacement of molds, and good versatility;
The disadvantages are: inability to follow the shape processing, and poor mold cooling uniformity.
2. Hierarchical
The layered type is designed and processed through the layered design and processing of the mold surface and other parts of the mold with the cooling pipe as the interface. The advantages are good conformability, large heat exchange area and simple sealing;
The disadvantage is that high-precision processing equipment is required, the cooling pipeline is complicated, and the heat transfer performance is poor.
3. Shower type
In the shower type, a series of small holes are opened on the mold surface, and nozzles are arranged in the holes. After the mold is closed, the nozzle is used to spray high-pressure coolant onto the hot steel plate in mist to achieve quenching and cooling. The advantage is that the cooling effect is good, the machining material phase change is sufficient, and the mechanical properties of the parts are excellent;
The disadvantage is that it is difficult to process, and the residual water droplets on the mold cause serious damage to the mold surface and reduce the life of the mold.
4. Casting type
The melt-casting type is entirely pre-embedded into the sand mold through a fixed cooling pipe, and the mold blank is obtained by casting, and an integrated mold is obtained after machining. The advantages are the flexible arrangement of cooling pipes, good conformability, simple and reliable pipe sealing, and easy processing;
The disadvantage is that the mold strength is poor, the melting and casting process is complex, the metallurgical combination between the pipe and the substrate is required, the position accuracy is high, and it is difficult to achieve partial mold repair.
Among the four hot stamping die design and manufacturing methods, the drilling type and the layered type are the most widely used.
Please keep the source and address of this article for reprinting: The Difference Between Die Casting And Stamping
Minghe Casting Company are dedicated to manufacture and provide quality and high performance Casting Parts(metal die casting parts range mainly include Thin-Wall Die Casting,Hot Chamber Die Casting,Cold Chamber Die Casting),Round Service(Die Casting Service,Cnc Machining,Mold Making,Surface Treatment).Any custom Aluminum die casting, magnesium or Zamak/zinc die casting and other castings requirements are welcome to contact us.
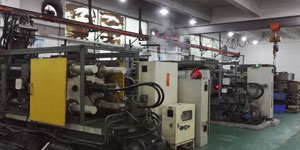
Under the control of ISO9001 and TS 16949,All processes are carried out through hundreds of advanced die casting machines, 5-axis machines, and other facilities, ranging from blasters to Ultra Sonic washing machines.Minghe not only has advanced equipment but also have professional team of experienced engineers,operators and inspectors to make the customer’s design come true.
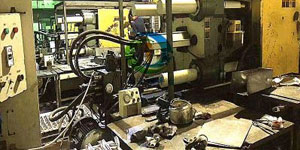
Contract manufacturer of die castings. Capabilities include cold chamber aluminum die casting parts from 0.15 lbs. to 6 lbs., quick change set up, and machining. Value-added services include polishing, vibrating, deburring, shot blasting, painting, plating, coating, assembly, and tooling. Materials worked with include alloys such as 360, 380, 383, and 413.
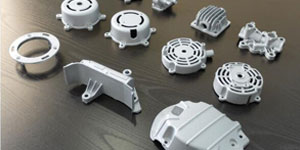
Zinc die casting design assistance/concurrent engineering services. Custom manufacturer of precision zinc die castings. Miniature castings, high pressure die castings, multi-slide mold castings, conventional mold castings, unit die and independent die castings and cavity sealed castings can be manufactured. Castings can be manufactured in lengths and widths up to 24 in. in +/-0.0005 in. tolerance.
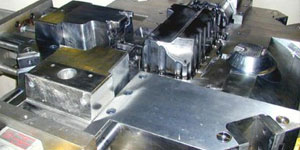
ISO 9001: 2015 certified manufacturer of die cast magnesium, Capabilities include high-pressure magnesium die casting up to 200 ton hot chamber & 3000 ton cold chamber, tooling design, polishing, molding, machining, powder & liquid painting, full QA with CMM capabilities, assembly, packaging & delivery.
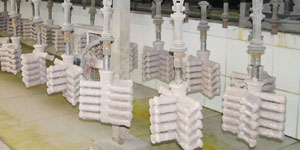
ITAF16949 certified. Additional Casting Service Include investment casting,sand casting,Gravity Casting, Lost Foam Casting,Centrifugal Casting,Vacuum Casting,Permanent Mold Casting,.Capabilities include EDI, engineering assistance, solid modeling and secondary processing.
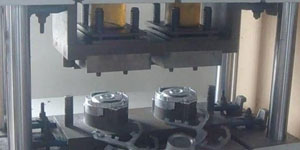
Casting Industries Parts Case Studies for: Cars, Bikes, Aircraft, Musical instruments, Watercraft, Optical devices, Sensors, Models, Electronic devices, Enclosures, Clocks, Machinery, Engines, Furniture, Jewelry, Jigs, Telecom, Lighting, Medical devices, Photographic devices, Robots, Sculptures, Sound equipment, Sporting equipment, Tooling, Toys and more.
What Can we help you do next?
∇ Go To Homepage For Die Casting China
→Casting Parts-Find out what we have done.
→Ralated Tips About Die Casting Services
By Minghe Die Casting Manufacturer |Categories: Helpful Articles |Material Tags: Aluminum Casting, Zinc Casting, Magnesium Casting, Titanium Casting, Stainless Steel Casting, Brass Casting,Bronze Casting,Casting Video,Company History,Aluminum Die Casting |Comments Off