The Difference Between Forging And Rolling
Rolling: A pressure processing method in which a metal blank is passed through a pair of rotating rolls (various shapes). Due to the compression of the rolls, the cross-section of the material is reduced and the length is increased. This is the most commonly used production method for producing steel. Production of profiles, plates and pipes.
According to the motion of the rolling piece, the rolling methods are divided into: longitudinal rolling, cross rolling, and cross rolling.
The longitudinal rolling process is a process in which metal passes between two rolls that rotate in opposite directions, and plastic deformation occurs between them.
- Cross rolling: The moving direction of the rolled piece after deformation is consistent with the direction of the roll axis.
- Skew rolling: The rolling piece moves in a spiral, and the rolling piece and the roll axis have no special angle.
The Advantage Of Rolling
It can destroy the casting structure of the steel ingot, refine the grain of the steel, and eliminate the defects of the microstructure, so that the steel structure is dense and the mechanical properties are improved. This improvement is mainly reflected in the rolling direction, so that the steel is no longer isotropic to a certain extent; bubbles, cracks and looseness formed during casting can also be welded under high temperature and pressure.
The Disadvantage Of Rolling
- After rolling, the non-metallic inclusions (mainly sulfides and oxides, as well as silicates) inside the steel are pressed into thin sheets, and delamination (interlayer) occurs. Delamination greatly deteriorates the tensile properties of the steel in the thickness direction, and it is possible that interlayer tearing may occur when the weld shrinks. The local strain induced by weld shrinkage often reaches several times the yield point strain, which is much larger than the strain caused by the load.
- Residual stress caused by uneven cooling. Residual stress is the internal self-balanced stress without external force. Hot-rolled steel sections of various cross-sections have such residual stresses. Generally, the larger the section size of the steel section, the larger the residual stress. Although the residual stress is self-balanced, it still has a certain influence on the performance of the steel member under the action of external force. For example, it may have adverse effects on deformation, stability, fatigue resistance, etc.
- Hot-rolled steel products are not easy to control in terms of thickness and edge width. We are familiar with thermal expansion and contraction. Since at the beginning, even if the length and thickness are up to the standard, there will be a certain negative difference after the final cooling. The wider the negative difference, the thicker the thickness, the more obvious the performance. Therefore, for large-sized steel, the side width, thickness, length, angle, and sideline of the steel cannot be too precise.
Forging: It is a processing method that uses forging machinery to apply pressure to metal blanks to produce plastic deformation to obtain forgings with certain mechanical properties, certain shapes and sizes, and one of the two major components of forging (forging and stamping). Forging can eliminate defects such as loose as-cast during the smelting process and optimize the microstructure. At the same time, due to the preservation of complete metal flow lines, the mechanical properties of forgings are generally better than castings of the same material. For the important parts of related machinery with high load and severe working conditions, forgings are mostly used except for simpler shapes that can be rolled, profiles or welded parts.
Forging can be divided into free forging, die forging, and closed die forging
- Free forging. Using impact or pressure to deform the metal between the upper and lower anvils (anvils) to obtain the required forgings, there are mainly manual forging and mechanical forging.
- Die forging. Die forging is divided into open die forging and closed die forging. The metal blank is compressed and deformed in the forging die with a certain shape to obtain forgings. It can be divided into cold heading, roll forging, radial forging and extrusion, etc. Wait.
- Because there is no flash in closed die forging and closed upsetting, the material utilization rate is high. It is possible to complete the finishing of complex forgings with one process or several processes. Because there is no flash, the force-bearing area of the forging is reduced, and the required load is also reduced. However, it should be noted that the blanks cannot be completely restricted. For this reason, the volume of the blanks should be strictly controlled, the relative position of the forging dies and the measurement of the forgings should be controlled, so as to reduce the wear of the forging dies.
Features:
Compared with castings, forging metal can improve its structure and mechanical properties after forging. After the casting structure is deformed by the forging method due to the deformation and recrystallization of the metal, the original coarse dendrites and columnar grains become the equiaxed recrystallized structure with finer grains and uniform size, which makes the original segregation in the steel ingot, The compaction and welding of looseness, pores, slag inclusions, etc., make the structure more compact and improve the plasticity and mechanical properties of the metal.
The mechanical properties of castings are lower than the mechanical properties of forgings of the same material. In addition, the forging process can ensure the continuity of the metal fiber structure, keep the fiber structure of the forging consistent with the shape of the forging, and the metal streamline is complete, which can ensure that the parts have good mechanical properties and long service life. Precision die forging and cold extrusion are used. Forgings produced by processes such as, warm extrusion, etc. are unmatched by castings.
Comparison Of Forging And Rolling
- The difference in axial and radial mechanical properties of forgings is smaller than that of rolled products. That is to say, the isotropy of forgings is much higher than that of rolled products. Therefore, the life of forgings is much higher than that of rolled products. Rolled pieces. The following figure shows the metallographic diagram of the morphology of eutectic carbides in different directions of Cr12MoV rolled sheet.
- In terms of the degree of transformation, the degree of deformation of the forging is much greater than that of the rolling, that is to say, the effect of breaking eutectic carbide through forging is better than that of rolling.
- In terms of processing cost, the cost of forging is much higher than the cost of rolling. For some key parts, workpieces with large loads or impacts, and workpieces with complex shapes or very strict requirements, forging must be used. Process for processing.
- Forgings have complete metal flow lines. After rolling, mechanics destroy the integrity of the metal flow lines, which greatly shortens the life of the workpiece. The following picture shows the metal flow lines of casting, machining, and forging workpieces.
Please keep the source and address of this article for reprinting: The Difference Between Forging And Rolling
Minghe Die Casting Company are dedicated to manufacture and provide quality and high performance Casting Parts(metal die casting parts range mainly include Thin-Wall Die Casting,Hot Chamber Die Casting,Cold Chamber Die Casting),Round Service(Die Casting Service,Cnc Machining,Mold Making,Surface Treatment).Any custom Aluminum die casting, magnesium or Zamak/zinc die casting and other castings requirements are welcome to contact us.
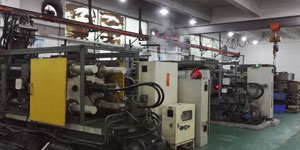
Under the control of ISO9001 and TS 16949,All processes are carried out through hundreds of advanced die casting machines, 5-axis machines, and other facilities, ranging from blasters to Ultra Sonic washing machines.Minghe not only has advanced equipment but also have professional team of experienced engineers,operators and inspectors to make the customer’s design come true.
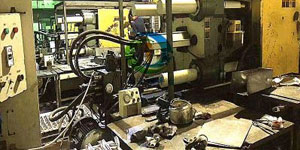
Contract manufacturer of die castings. Capabilities include cold chamber aluminum die casting parts from 0.15 lbs. to 6 lbs., quick change set up, and machining. Value-added services include polishing, vibrating, deburring, shot blasting, painting, plating, coating, assembly, and tooling. Materials worked with include alloys such as 360, 380, 383, and 413.
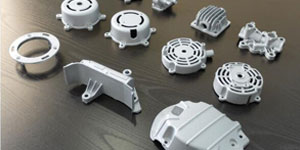
Zinc die casting design assistance/concurrent engineering services. Custom manufacturer of precision zinc die castings. Miniature castings, high pressure die castings, multi-slide mold castings, conventional mold castings, unit die and independent die castings and cavity sealed castings can be manufactured. Castings can be manufactured in lengths and widths up to 24 in. in +/-0.0005 in. tolerance.
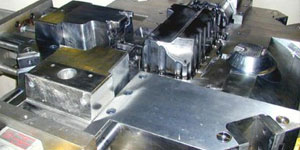
ISO 9001: 2015 certified manufacturer of die cast magnesium, Capabilities include high-pressure magnesium die casting up to 200 ton hot chamber & 3000 ton cold chamber, tooling design, polishing, molding, machining, powder & liquid painting, full QA with CMM capabilities, assembly, packaging & delivery.
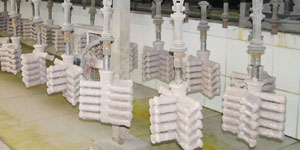
ITAF16949 certified. Additional Casting Service Include investment casting,sand casting,Gravity Casting, Lost Foam Casting,Centrifugal Casting,Vacuum Casting,Permanent Mold Casting,.Capabilities include EDI, engineering assistance, solid modeling and secondary processing.
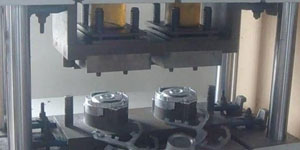
Casting Industries Parts Case Studies for: Cars, Bikes, Aircraft, Musical instruments, Watercraft, Optical devices, Sensors, Models, Electronic devices, Enclosures, Clocks, Machinery, Engines, Furniture, Jewelry, Jigs, Telecom, Lighting, Medical devices, Photographic devices, Robots, Sculptures, Sound equipment, Sporting equipment, Tooling, Toys and more.
What Can we help you do next?
∇ Go To Homepage For Die Casting China
→Casting Parts-Find out what we have done.
→Ralated Tips About Die Casting Services
By Minghe Die Casting Manufacturer |Categories: Helpful Articles |Material Tags: Aluminum Casting, Zinc Casting, Magnesium Casting, Titanium Casting, Stainless Steel Casting, Brass Casting,Bronze Casting,Casting Video,Company History,Aluminum Die Casting |Comments Off