The Effect Of Fine-Grained Band In 690 Alloy Forged Bar On The Structure Of Finished Pipe
Alloy 690 is a nickel-based corrosion-resistant alloy. It not only has excellent stress corrosion cracking resistance, but also has relatively high strength, good structure stability and excellent processing characteristics. It has become a large-scale advanced PWR nuclear power plant at home and abroad. The material of choice for heat transfer tubes of steam generators The tube making process of 690 alloy heat transfer tube is: forged bar → hot extrusion → billet cold rolling → intermediate annealing → final cold rolling → final annealing → special heat treatment (referred to as "TT").
Scholars at home and abroad have studied the effects of solution treatment and special heat treatment on the uniformity, carbide precipitation morphology, grain boundary structure and corrosion resistance of 690 alloy finished heat transfer tubes, but the structure of alloy forged bars There are relatively few reports on fine-grained bands and their effects on the structure of pipes. In view of this, the researchers analyzed the structure of the 690 alloy forged bar used in the heat transfer tube of the nuclear power steam generator, and performed the heat treatment test and the structure of the forged bar with fine-grained band structure according to the heating process in the hot extrusion process. Analyzed and analyzed its influence on the annealed intermediate tube structure and the TT state finished tube structure in the subsequent processing.
The 690 alloy forged bar for the test was provided by a domestic manufacturer. The end of the 690 alloy forged bar was cut off, and a representative sample was selected to observe the longitudinal original structure. In order to study the influence of the heating process on the structure of the forged bar during the thermal process, the 690 alloy forged bar was heat treated according to this heating process, that is, the forged bar sample (20mm×20mm×20mm) was heated at 950℃ for 2h, and water cooled , Prepare the metallographic sample to observe its longitudinal structure; then, the batch of samples are first kept at 950°C for 10 minutes, then raised to 1200°C for 5 minutes, and then water-cooled, and then the metallographic sample is prepared to observe its longitudinal structure. At the same time, annealed intermediate tubes and TT finished tubes were prepared according to the heat transfer tube process for this batch of forged bars, and longitudinal microstructure analysis was performed on them.
The test found that there is an abnormal fine-grained band structure in the form of "sandwich" in the original structure of the forged bar. The coarse and fine-grained bands are spaced apart, and the grain sizes of different fine-grained bands are basically the same. The width of the fine-grained bands of each layer is different. The width of the wider fine-crystalline band is more than 200μm, the width of the narrower fine-crystalline band is only 10μm, and the grain size in the fine-crystalline band is less than 20μm. There are many Ti(C, N) inclusions in the fine-grained band of the original forged bar, and most of them are located on the grain boundary. The grain boundary plays a role of pinning, and at the same time, it is in the grain and crystal of the fine-grained band. There are a lot of carbides in the world. Because Ti (C, N) and carbide particles have a strong pinning effect on the movement of dislocations, they hinder the growth of crystal grains, leading to the formation of fine crystal bands. The normal structure of the original forged bar (without the fine grain zone) has a large number of continuous or semi-continuous carbide precipitation on the grain boundary, and there is basically no point-like carbide precipitation in the grain, and there is no intragranular and grain boundary. A large number of Ti(C,N) particles were found.
After the forged bar is heat treated at 950℃ for 2h, the fine-grained band has been improved, but it is not obviously eliminated, and there are still a lot of band-shaped fine-grained bands. After heat treatment at 1200°C, the structure of the forged bar is a solid solution structure, but the fine-grained band structure cannot be completely removed.
Further experiments have found that there are still fine crystal bands in the longitudinal microstructure of the annealed intermediate tube, and the fine crystal bands are composed of a series of single fine crystal grains. The remaining fine crystal bands of the annealed intermediate tube will have a certain impact on the uniformity of the finished tube structure. The carbides on the longitudinal grain boundaries of the finished tube in the TT state are all continuously or semi-continuously distributed, and carbide precipitation bands are found in the structure. The carbide precipitation bands are longitudinally distributed, and the direction of the rolling deformation is the same. Analysis:
- (1) The uneven precipitation of carbides in 690 alloy forged bars is the main reason for the existence of fine crystal bands in forged bars.
- (2) The presence of fine-grained bands in the 690 alloy forged bar will adversely affect the uniformity of the 690 alloy tube during subsequent processing, resulting in uneven carbide precipitation in the finished structure of the heat transfer tube, and ultimately resulting in the local structure of the finished tube Uneven.
- (3) In order to ensure the uniformity of the structure of the finished 690 alloy heat transfer tube, the structure of the forged bar should be controlled to avoid the existence of fine-grained bands in the bar.
Please keep the source and address of this article for reprinting: The Effect Of Fine-Grained Band In 690 Alloy Forged Bar On The Structure Of Finished Pipe
Minghe Die Casting Company are dedicated to manufacture and provide quality and high performance Casting Parts(metal die casting parts range mainly include Thin-Wall Die Casting,Hot Chamber Die Casting,Cold Chamber Die Casting),Round Service(Die Casting Service,Cnc Machining,Mold Making,Surface Treatment).Any custom Aluminum die casting, magnesium or Zamak/zinc die casting and other castings requirements are welcome to contact us.
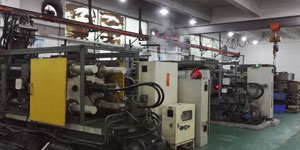
Under the control of ISO9001 and TS 16949,All processes are carried out through hundreds of advanced die casting machines, 5-axis machines, and other facilities, ranging from blasters to Ultra Sonic washing machines.Minghe not only has advanced equipment but also have professional team of experienced engineers,operators and inspectors to make the customer’s design come true.
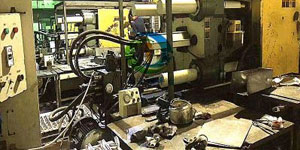
Contract manufacturer of die castings. Capabilities include cold chamber aluminum die casting parts from 0.15 lbs. to 6 lbs., quick change set up, and machining. Value-added services include polishing, vibrating, deburring, shot blasting, painting, plating, coating, assembly, and tooling. Materials worked with include alloys such as 360, 380, 383, and 413.
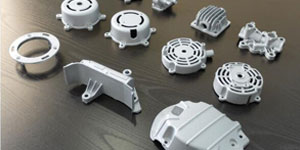
Zinc die casting design assistance/concurrent engineering services. Custom manufacturer of precision zinc die castings. Miniature castings, high pressure die castings, multi-slide mold castings, conventional mold castings, unit die and independent die castings and cavity sealed castings can be manufactured. Castings can be manufactured in lengths and widths up to 24 in. in +/-0.0005 in. tolerance.
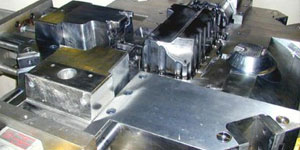
ISO 9001: 2015 certified manufacturer of die cast magnesium, Capabilities include high-pressure magnesium die casting up to 200 ton hot chamber & 3000 ton cold chamber, tooling design, polishing, molding, machining, powder & liquid painting, full QA with CMM capabilities, assembly, packaging & delivery.
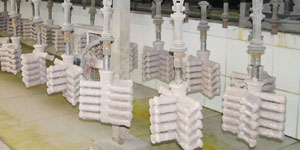
ITAF16949 certified. Additional Casting Service Include investment casting,sand casting,Gravity Casting, Lost Foam Casting,Centrifugal Casting,Vacuum Casting,Permanent Mold Casting,.Capabilities include EDI, engineering assistance, solid modeling and secondary processing.
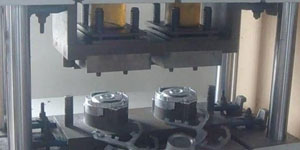
Casting Industries Parts Case Studies for: Cars, Bikes, Aircraft, Musical instruments, Watercraft, Optical devices, Sensors, Models, Electronic devices, Enclosures, Clocks, Machinery, Engines, Furniture, Jewelry, Jigs, Telecom, Lighting, Medical devices, Photographic devices, Robots, Sculptures, Sound equipment, Sporting equipment, Tooling, Toys and more.
What Can we help you do next?
∇ Go To Homepage For Die Casting China
→Casting Parts-Find out what we have done.
→Ralated Tips About Die Casting Services
By Minghe Die Casting Manufacturer |Categories: Helpful Articles |Material Tags: Aluminum Casting, Zinc Casting, Magnesium Casting, Titanium Casting, Stainless Steel Casting, Brass Casting,Bronze Casting,Casting Video,Company History,Aluminum Die Casting |Comments Off