The Factors Influencing The Fatigue Life Of Rolling Bearings
In recent years, the tribological design of general mechanical parts has received widespread attention. Rolling bearings are one of the most widely used mechanical parts. With the development of numerical calculation techniques and methods, calculation simulation and simulation tests have been widely used in the tribology of rolling bearings. Research and product design. The tribological design of rolling bearings has two ideas, forward and reverse.
The performance of the rolling bearing has a significant impact on the performance of the mechanical system. However, there are many factors that affect the fatigue life of the rolling bearing, such as operating temperature, impact load, reliability, material, use conditions, limit speed, surface roughness, inclusions, indentation, and lubrication Condition, radial clearance, deflection, fatigue crack-induced stress, tangential friction, residual stress and hoop stress, surface treatment, etc., these factors affect each other, plus the non-repeatability of the fatigue life test, the influencing factors are still difficult to be accurate Quantitative description.
The classic L-P theory of rolling bearing fatigue life is based on the assumption that the fatigue failure of rolling contact originates from the depth of the maximum orthogonal shear stress under the contact area. However, with the development of bearing manufacturing technology, fatigue failure modes originating from the surface appear more frequently than subsurface fatigue failure modes. There are three mechanisms of crack initiation: crack initiation from the surface, crack initiation from near the surface, and crack initiation in the material matrix.
The pitting originating on the surface and the spalling life originating below the surface are competing failure modes, which are predicted as a function of the film thickness ratio, the root mean square value of the roughness peak slope, and the traction coefficient in the boundary lubrication roughness peak contact.
With the development of high-speed railways and the aviation industry, there are more and more requirements for the high reliability of bearings. At the same time, the bearing application environment temperature changes greatly. It is necessary to deeply study the coupling effect of reliability and temperature. Rolling bearing materials are still under development. It is necessary to explore the relationship between the surface integrity of parts and surface fatigue pits, and reveal the influence of part surface integrity and lubrication effects on fatigue pits on a microscopic scale. On the other hand, combining load characteristics and material dynamic response to study spalling failure, analyze the dynamic response of bearing materials to external loads, study the coupling relationship between fatigue performance and material properties, and obtain the relationship between material dynamic response and surface fatigue spalling.
For other factors affecting bearing fatigue life, such as lubricants and additives, surface roughness, hoop stress and interface sliding, etc., comprehensive research is also needed, such as establishing a database and developing software packages to realize automatic analysis of lubricants and bearing materials And choice, this is also one of the future development directions.
Analyzing the factors that affect the bearing's rolling fatigue relief will help to better understand the mechanism of bearing fatigue failure. On the one hand, it can avoid the factors that reduce the bearing life as much as possible and improve the fatigue life of the bearing; on the other hand, it can provide certain guidance for the development of fatigue life theory, in order to improve the accuracy of bearing fatigue life prediction.
Please keep the source and address of this article for reprinting: The Factors Influencing The Fatigue Life Of Rolling Bearings
Minghe Die Casting Company are dedicated to manufacture and provide quality and high performance Casting Parts(metal die casting parts range mainly include Thin-Wall Die Casting,Hot Chamber Die Casting,Cold Chamber Die Casting),Round Service(Die Casting Service,Cnc Machining,Mold Making,Surface Treatment).Any custom Aluminum die casting, magnesium or Zamak/zinc die casting and other castings requirements are welcome to contact us.
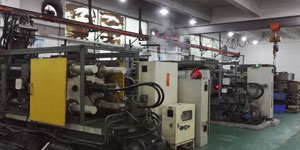
Under the control of ISO9001 and TS 16949,All processes are carried out through hundreds of advanced die casting machines, 5-axis machines, and other facilities, ranging from blasters to Ultra Sonic washing machines.Minghe not only has advanced equipment but also have professional team of experienced engineers,operators and inspectors to make the customer’s design come true.
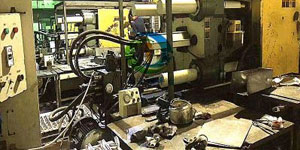
Contract manufacturer of die castings. Capabilities include cold chamber aluminum die casting parts from 0.15 lbs. to 6 lbs., quick change set up, and machining. Value-added services include polishing, vibrating, deburring, shot blasting, painting, plating, coating, assembly, and tooling. Materials worked with include alloys such as 360, 380, 383, and 413.
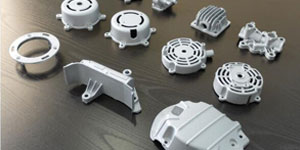
Zinc die casting design assistance/concurrent engineering services. Custom manufacturer of precision zinc die castings. Miniature castings, high pressure die castings, multi-slide mold castings, conventional mold castings, unit die and independent die castings and cavity sealed castings can be manufactured. Castings can be manufactured in lengths and widths up to 24 in. in +/-0.0005 in. tolerance.
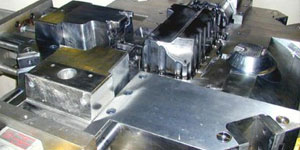
ISO 9001: 2015 certified manufacturer of die cast magnesium, Capabilities include high-pressure magnesium die casting up to 200 ton hot chamber & 3000 ton cold chamber, tooling design, polishing, molding, machining, powder & liquid painting, full QA with CMM capabilities, assembly, packaging & delivery.
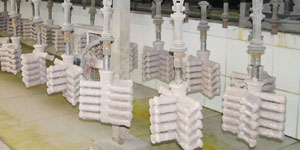
ITAF16949 certified. Additional Casting Service Include investment casting,sand casting,Gravity Casting, Lost Foam Casting,Centrifugal Casting,Vacuum Casting,Permanent Mold Casting,.Capabilities include EDI, engineering assistance, solid modeling and secondary processing.
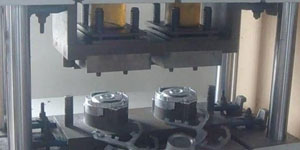
Casting Industries Parts Case Studies for: Cars, Bikes, Aircraft, Musical instruments, Watercraft, Optical devices, Sensors, Models, Electronic devices, Enclosures, Clocks, Machinery, Engines, Furniture, Jewelry, Jigs, Telecom, Lighting, Medical devices, Photographic devices, Robots, Sculptures, Sound equipment, Sporting equipment, Tooling, Toys and more.
What Can we help you do next?
∇ Go To Homepage For Die Casting China
→Casting Parts-Find out what we have done.
→Ralated Tips About Die Casting Services
By Minghe Die Casting Manufacturer |Categories: Helpful Articles |Material Tags: Aluminum Casting, Zinc Casting, Magnesium Casting, Titanium Casting, Stainless Steel Casting, Brass Casting,Bronze Casting,Casting Video,Company History,Aluminum Die Casting |Comments Off