The Features And Precautions Of CNC Lathe Machining
The machining technology of CNC lathes is similar to that of ordinary lathes, but because CNC lathes are one-time clamping and continuous automatic machining to complete all turning processes, the following aspects should be paid attention to.
1. Reasonable Choice Of Cutting Amount
For high-efficiency metal cutting machining, the material to be processed, cutting tools, and cutting conditions are the three major elements. These determine the machining time, tool life and machining quality. The economical and effective machining method must be a reasonable choice of cutting conditions.
The three elements of cutting conditions: cutting speed, feed rate and depth of cut directly cause tool damage. With the increase in cutting speed, the temperature of the tool tip will rise, which will cause mechanical, chemical, and thermal wear. Cutting speed increased by 20%, tool life will be reduced by 1/2.
The relationship between the feed condition and the wear on the back of the tool occurs in a very small range. However, the feed rate is large, the cutting temperature rises, and the back wear is large. It has less influence on the tool than cutting speed. Although the influence of cutting depth on the tool is not as large as the cutting speed and feed rate, when cutting at a small depth of cut, the material to be cut will produce a layer, which will also affect the life of the tool.
The user should select the cutting speed to be used according to the processed material, hardness, cutting state, material type, feed rate, depth of cut, etc.
The selection of suitable machining conditions is selected on the basis of these factors. Regular, stable wear and longevity are the ideal conditions.
However, in actual operations, the choice of tool life is related to tool wear, dimensional changes to be processed, surface quality, cutting noise, and machining heat. When determining the machining conditions, it is necessary to conduct research according to the actual situation. For difficult-to-process materials such as stainless steel and heat-resistant alloys, coolants or blades with good rigidity can be used.
2. Reasonable Choice Of Tools
- When roughing, choose a tool with high strength and good durability to meet the requirements of large back-grabbing and large feed when roughing.
- When finishing turning, choose high-precision and durable tools to ensure the requirements of machining accuracy.
- In order to reduce the tool change time and facilitate tool setting, machine clamped knives and machine clamped blades should be used as much as possible.
3. Reasonable Selection Of Fixtures
- Try to use general fixtures to clamp the workpiece, avoid using special fixtures;
- The part positioning datum coincides to reduce the positioning error.
4. Determine The Machining Route
The machining route is the movement track and direction of the tool relative to the part during the machining of the index-controlled lathe.
- It should be able to guarantee the machining accuracy and surface roughness requirements;
- The machining route should be shortened as much as possible to reduce the tool idle travel time.
5. The Connection Between Machining Route And Machining Allowance
At present, under the condition that the CNC lathe has not yet reached the popular use, the excess margin on the blank, especially the margin containing the forging and casting hard skin layer, should be arranged on the ordinary lathe for machining. When machining manufacturers must use CNC lathes, they need to pay attention to the flexible arrangement of the program.
6. Main Points Of Fixture Installation
At present, the connection between the hydraulic chuck and the hydraulic clamping cylinder is realized by a tie rod, as shown in Figure 1. The main points of hydraulic chuck clamping are as follows: first use a moving hand to remove the nut on the hydraulic cylinder, remove the pull tube, and pull it out from the rear of the spindle, and then use the moving hand to remove the chuck fixing screw to remove the chuck.
The wiper edge on the tool refers to a small segment of the blade parallel to the tip of the tool that is ground in the direction of the secondary deflection angle behind the blade of the tool. It is mainly used for a secondary cutting after the cutting of the blade. Improving the surface roughness of the workpiece is mostly applied to the knife for finishing.
The machining technology of CNC lathes is similar to that of ordinary lathes, but because CNC lathes are one-time clamping and continuous automatic machining to complete all turning processes, the following aspects should be paid attention to.
Please keep the source and address of this article for reprinting: The Features And Precautions Of CNC Lathe Machining
Minghe Die Casting Company are dedicated to manufacture and provide quality and high performance Casting Parts(metal die casting parts range mainly include Thin-Wall Die Casting,Hot Chamber Die Casting,Cold Chamber Die Casting),Round Service(Die Casting Service,Cnc Machining,Mold Making,Surface Treatment).Any custom Aluminum die casting, magnesium or Zamak/zinc die casting and other castings requirements are welcome to contact us.
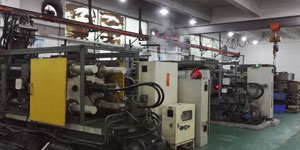
Under the control of ISO9001 and TS 16949,All processes are carried out through hundreds of advanced die casting machines, 5-axis machines, and other facilities, ranging from blasters to Ultra Sonic washing machines.Minghe not only has advanced equipment but also have professional team of experienced engineers,operators and inspectors to make the customer’s design come true.
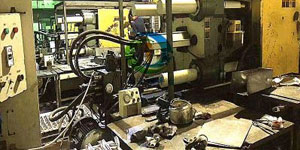
Contract manufacturer of die castings. Capabilities include cold chamber aluminum die casting parts from 0.15 lbs. to 6 lbs., quick change set up, and machining. Value-added services include polishing, vibrating, deburring, shot blasting, painting, plating, coating, assembly, and tooling. Materials worked with include alloys such as 360, 380, 383, and 413.
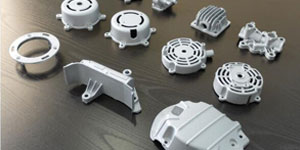
Zinc die casting design assistance/concurrent engineering services. Custom manufacturer of precision zinc die castings. Miniature castings, high pressure die castings, multi-slide mold castings, conventional mold castings, unit die and independent die castings and cavity sealed castings can be manufactured. Castings can be manufactured in lengths and widths up to 24 in. in +/-0.0005 in. tolerance.
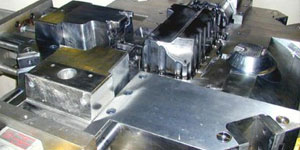
ISO 9001: 2015 certified manufacturer of die cast magnesium, Capabilities include high-pressure magnesium die casting up to 200 ton hot chamber & 3000 ton cold chamber, tooling design, polishing, molding, machining, powder & liquid painting, full QA with CMM capabilities, assembly, packaging & delivery.
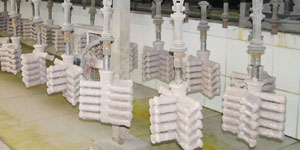
ITAF16949 certified. Additional Casting Service Include investment casting,sand casting,Gravity Casting, Lost Foam Casting,Centrifugal Casting,Vacuum Casting,Permanent Mold Casting,.Capabilities include EDI, engineering assistance, solid modeling and secondary processing.
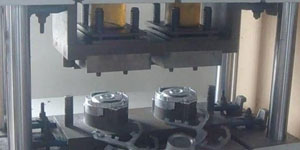
Casting Industries Parts Case Studies for: Cars, Bikes, Aircraft, Musical instruments, Watercraft, Optical devices, Sensors, Models, Electronic devices, Enclosures, Clocks, Machinery, Engines, Furniture, Jewelry, Jigs, Telecom, Lighting, Medical devices, Photographic devices, Robots, Sculptures, Sound equipment, Sporting equipment, Tooling, Toys and more.
What Can we help you do next?
∇ Go To Homepage For Die Casting China
→Casting Parts-Find out what we have done.
→Ralated Tips About Die Casting Services
By Minghe Die Casting Manufacturer |Categories: Helpful Articles |Material Tags: Aluminum Casting, Zinc Casting, Magnesium Casting, Titanium Casting, Stainless Steel Casting, Brass Casting,Bronze Casting,Casting Video,Company History,Aluminum Die Casting |Comments Off