The Flaw Detection Methods For Forged Parts, Steel Castings And Crankshafts
Magnetic particle inspection for forged steel parts
- The characteristics of flaw detection of forged steel parts: The forging process and forming methods are generally divided into two categories: free forging and die forging.The process flow is: blanking-heating-forging-(trimming)-flaw detection-machining-heat treatment-flaw detection-(surface heat treatment-flaw detection)-surface treatment-finished product delivery.Among them, the forging process is prone to defects such as cracks, folding and white spots; heat treatment will produce quenching cracks; machining will produce grinding cracks and correction cracks; surface heat treatment will also produce cracks.
- Flaw detection method selection: Generally, a fixed magnetic particle flaw detector is used for circumferential and longitudinal magnetization. If the remanence and coercivity of the material meet the requirements, it is recommended to use the remanence method for flaw detection.
- Magnetic particle inspection of crankshaftFlaw detection method: directly energize circumferential magnetization, check forging cracks, folding, grinding cracks, quenching cracks, and hair lines. The segmented coil is magnetized longitudinally, and the transverse cracks are inspected, including forging cracks, grinding cracks, correction cracks, quenching cracks, etc. Pay special attention to the observation of the corners and the edge of the oil injection hole during flaw detection.
Magnetic particle inspection of steel castings
- The characteristics of magnetic particle inspection of steel castings: steel castings are generally complex in shape, and the types and positions of defects are relatively regular. The main defects are casting cracks, porosity, shrinkage cavities, inclusions, pores and cold partitions.
- Choice of flaw detection method: Castings are generally small in size, which is convenient for flaw detection on a fixed flaw detector. All castings must undergo circumferential and longitudinal magnetization inspections. The continuous method is used for flaw detection before heat treatment, and the residual magnetic method is generally used for flaw detection after heat treatment. Check for pores and inclusions under the surface, and DC flaw detection should be used. For network cracks, it is best to use fluorescent magnetic particle inspection.
- Cam magnetic particle inspectionFlaw detection method: The blank is tested by continuous method, and after heat treatment, the residual magnetic method is used for flaw detection. The wheel part is inspected by the rod-through method, and the shaft part is magnetized circumferentially by the direct energization method, and then longitudinally magnetized by the coil. Focus on checking the cracks at the root.
Magnetic particle inspection of in-service and maintenance parts of special equipment
- The characteristics of magnetic particle inspection of in-service and repaired parts: mainly found fatigue cracks and stress corrosion cracks. The location of the crack is directly related to the force. The inspection conditions of in-service and repaired parts are poor, and the fatigue cracks are small. If conditions permit, use fluorescent magnetic particle inspection as much as possible. For bolt holes, the rod-through method should be used, and technologies such as endoscopes should be borrowed. Small bolt holes can also be inspected by rubber casting method.
- Bolt magnetic particle inspection: Bolts are fasteners, which are subjected to tensile force and are prone to transverse fatigue cracks. Therefore, longitudinal magnetization of the coil should be used. The residual magnetization method and the lower concentration of fluorescent magnetic particle inspection have the best effect.
Special workpiece magnetic particle inspection:
- Compression spring flaw detection: First, directly energize to check the longitudinal defects on the steel wire; then use the rod-through method to check the lateral flaws on the steel wire. Note: The spring should be turned continuously when demagnetizing.
- Flaw detection of the tension spring: First, pull the spring apart (use a tension machine if necessary) and support it with an insulating rod, so that the spring coils are separated from each other, and then directly energize to check the longitudinal defects on the steel wire. Then, insulate each coil of the spring (remove the support rod), and use the rod-through method to detect the lateral defects on the steel wire.
Please keep the source and address of this article for reprinting:The Flaw Detection Methods For Forged Parts, Steel Castings And Crankshafts
Minghe Die Casting Company are dedicated to manufacture and provide quality and high performance Casting Parts(metal die casting parts range mainly include Thin-Wall Die Casting,Hot Chamber Die Casting,Cold Chamber Die Casting),Round Service(Die Casting Service,Cnc Machining,Mold Making,Surface Treatment).Any custom Aluminum die casting, magnesium or Zamak/zinc die casting and other castings requirements are welcome to contact us.
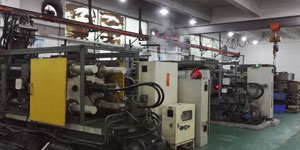
Under the control of ISO9001 and TS 16949,All processes are carried out through hundreds of advanced die casting machines, 5-axis machines, and other facilities, ranging from blasters to Ultra Sonic washing machines.Minghe not only has advanced equipment but also have professional team of experienced engineers,operators and inspectors to make the customer’s design come true.
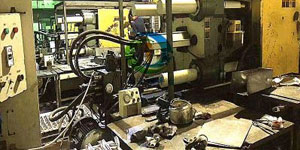
Contract manufacturer of die castings. Capabilities include cold chamber aluminum die casting parts from 0.15 lbs. to 6 lbs., quick change set up, and machining. Value-added services include polishing, vibrating, deburring, shot blasting, painting, plating, coating, assembly, and tooling. Materials worked with include alloys such as 360, 380, 383, and 413.
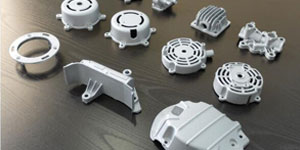
Zinc die casting design assistance/concurrent engineering services. Custom manufacturer of precision zinc die castings. Miniature castings, high pressure die castings, multi-slide mold castings, conventional mold castings, unit die and independent die castings and cavity sealed castings can be manufactured. Castings can be manufactured in lengths and widths up to 24 in. in +/-0.0005 in. tolerance.
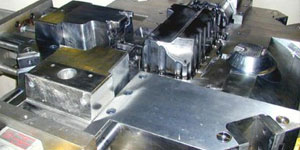
ISO 9001: 2015 certified manufacturer of die cast magnesium, Capabilities include high-pressure magnesium die casting up to 200 ton hot chamber & 3000 ton cold chamber, tooling design, polishing, molding, machining, powder & liquid painting, full QA with CMM capabilities, assembly, packaging & delivery.
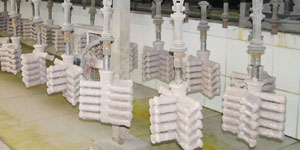
ITAF16949 certified. Additional Casting Service Include investment casting,sand casting,Gravity Casting, Lost Foam Casting,Centrifugal Casting,Vacuum Casting,Permanent Mold Casting,.Capabilities include EDI, engineering assistance, solid modeling and secondary processing.
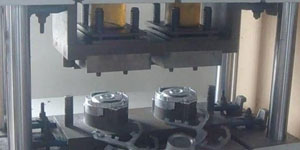
Casting Industries Parts Case Studies for: Cars, Bikes, Aircraft, Musical instruments, Watercraft, Optical devices, Sensors, Models, Electronic devices, Enclosures, Clocks, Machinery, Engines, Furniture, Jewelry, Jigs, Telecom, Lighting, Medical devices, Photographic devices, Robots, Sculptures, Sound equipment, Sporting equipment, Tooling, Toys and more.
What Can we help you do next?
∇ Go To Homepage For Die Casting China
→Casting Parts-Find out what we have done.
→Ralated Tips About Die Casting Services
By Minghe Die Casting Manufacturer |Categories: Helpful Articles |Material Tags: Aluminum Casting, Zinc Casting, Magnesium Casting, Titanium Casting, Stainless Steel Casting, Brass Casting,Bronze Casting,Casting Video,Company History,Aluminum Die Casting |Comments Off