The Forging Effect Of Tool Steel
Under certain conditions, it is reasonable to use rolled profiles to directly process products. The tool steel that needs to be forged in the manufacturing plant still accounts for a considerable proportion.
In addition to hot forging forming can reduce cutting processing and make full use of steel and other reasons, the reform forging of tool steel is conducive to improving the inherent quality of steel, and its effects are mainly reflected in the following aspects.
- Generally, the smaller the cross-section of steel, the larger the forging ratio, the better the metallurgical quality itself. Out of this, for all tool blanks that need to be modified first and then added, the seats should be forged as much as possible from steel with smaller cross-sections to blanks with larger cross-sections, which will help ensure that the tool steel has a better metallurgical quality.
- The forging is changed to make the streamline distribution inside the tool steel more reasonable. For example, if a disk milling cutter is directly machined with steel with a slightly larger outer diameter after blanking, it is reasonable in terms of steel utilization and reducing processing costs. However, the direction of the arrangement of impurities in the steel and the segregation of carbides The arrangement direction is parallel to the cutting edge, that is, it is in the direction of the greatest force, which is not good for the performance. If a small size material is used for reforming (upsetting and flattening), the streamlines are distributed radially (radial) , Improve the performance of the milling cutter.
- It is possible to improve the material of key parts by changing the forger, so that the material of the most severely stressed parts can be improved, and the effect of greatly improving the life of tool steel can be achieved.
- The heating process of forging considers the effect of diffusion annealing. The heating temperature of tool steel for forging can be slightly higher than the heating temperature of steel ingot breaking, because after the billet and rolling, the segregation in the product and the product has been significantly improved. When the steel is changed to silver, the tendency to locally melt when heated is reduced. The higher the heating temperature, the longer the length of the heat preservation, the more significant the effect of eliminating segregation. Obviously, the austenite grains of the die steel grow during the high temperature heating process. It seems that the pressure processing is performed immediately after the high temperature heating, and the English grains can be refined. If the final forging temperature is well controlled, the cooling method after forging Reasonable, it can suppress the appearance of network carbides. It is very important to ensure the RJ workability of the steel and the final use of the parts. Therefore, the final forging temperature of the tool steel is controlled, and should generally be controlled within the range of Table 3.2. .
Please keep the source and address of this article for reprinting: The Forging Effect Of Tool Steel
Minghe Die Casting Company are dedicated to manufacture and provide quality and high performance Casting Parts(metal die casting parts range mainly include Thin-Wall Die Casting,Hot Chamber Die Casting,Cold Chamber Die Casting),Round Service(Die Casting Service,Cnc Machining,Mold Making,Surface Treatment).Any custom Aluminum die casting, magnesium or Zamak/zinc die casting and other castings requirements are welcome to contact us.
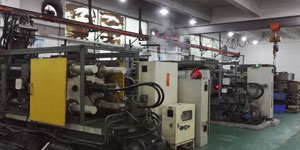
Under the control of ISO9001 and TS 16949,All processes are carried out through hundreds of advanced die casting machines, 5-axis machines, and other facilities, ranging from blasters to Ultra Sonic washing machines.Minghe not only has advanced equipment but also have professional team of experienced engineers,operators and inspectors to make the customer’s design come true.
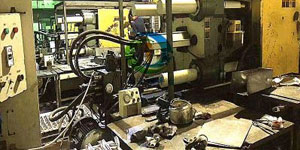
Contract manufacturer of die castings. Capabilities include cold chamber aluminum die casting parts from 0.15 lbs. to 6 lbs., quick change set up, and machining. Value-added services include polishing, vibrating, deburring, shot blasting, painting, plating, coating, assembly, and tooling. Materials worked with include alloys such as 360, 380, 383, and 413.
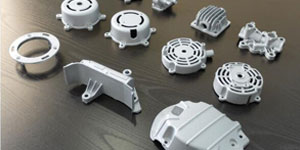
Zinc die casting design assistance/concurrent engineering services. Custom manufacturer of precision zinc die castings. Miniature castings, high pressure die castings, multi-slide mold castings, conventional mold castings, unit die and independent die castings and cavity sealed castings can be manufactured. Castings can be manufactured in lengths and widths up to 24 in. in +/-0.0005 in. tolerance.
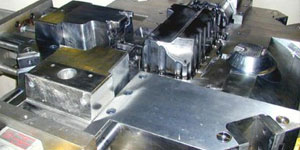
ISO 9001: 2015 certified manufacturer of die cast magnesium, Capabilities include high-pressure magnesium die casting up to 200 ton hot chamber & 3000 ton cold chamber, tooling design, polishing, molding, machining, powder & liquid painting, full QA with CMM capabilities, assembly, packaging & delivery.
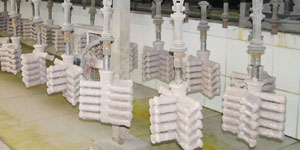
ITAF16949 certified. Additional Casting Service Include investment casting,sand casting,Gravity Casting, Lost Foam Casting,Centrifugal Casting,Vacuum Casting,Permanent Mold Casting,.Capabilities include EDI, engineering assistance, solid modeling and secondary processing.
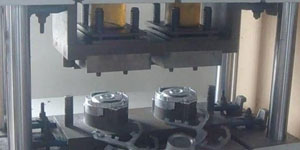
Casting Industries Parts Case Studies for: Cars, Bikes, Aircraft, Musical instruments, Watercraft, Optical devices, Sensors, Models, Electronic devices, Enclosures, Clocks, Machinery, Engines, Furniture, Jewelry, Jigs, Telecom, Lighting, Medical devices, Photographic devices, Robots, Sculptures, Sound equipment, Sporting equipment, Tooling, Toys and more.
What Can we help you do next?
∇ Go To Homepage For Die Casting China
→Casting Parts-Find out what we have done.
→Ralated Tips About Die Casting Services
By Minghe Die Casting Manufacturer |Categories: Helpful Articles |Material Tags: Aluminum Casting, Zinc Casting, Magnesium Casting, Titanium Casting, Stainless Steel Casting, Brass Casting,Bronze Casting,Casting Video,Company History,Aluminum Die Casting |Comments Off