The Forging Process Of Aluminum Alloy Wheel Industry
Forging spinning
Relatively high-end forming process, currently only about 10% of domestic enterprises adopt this process for production, and the products are mainly supplied to the domestic and foreign bus, truck and high-end car markets. The advantage is that the product has good inherent quality, high strength and lightness; the disadvantage is that the equipment is expensive. The spoke shape of the product manufactured by the traditional forging process can only be completed by milling, and the metal utilization rate is low and the production efficiency is not high. Forging is divided into traditional forging and rolling forging. Rolling forging can directly forge the shape of the spokes.
Casting spinning
Casting spinning is divided into "low pressure casting + spinning" and "gravity casting + spinning" two processes. At present, Korean car companies have a trend of fully adopting "low pressure casting + spinning" for the forming process of aluminum wheels. Other car series also have some products that require this process. This process is the mainstream process in the casting and spinning process and is used as an OEM product. Most of the companies use this process; at the same time, a small number of companies engaged in overseas retail markets use the "gravity casting + spinning" process. Theoretically speaking, this process is feasible. The advantages of the gravity casting and spinning processes are combined, and the product quality has been improved. However, because the blanks are produced by the gravity casting process, the economics of this process are very poor and the production cost is very high. In short, the cast-spinned product, because the spoke part is cast, has the same advantages and disadvantages as the product produced by the casting process; and the rim part is spun, so the air tightness is better. In theory, cast-spinning products can reduce weight, but the effect is not obvious in practical applications.
Liquid forging
At present, only two companies in the mainland are using this process for production, and the equipment and technology are from South Korea. In fact, this process is not forging, it should be classified as high-pressure casting. It is to directly pour a certain amount of aluminum alloy liquid into the mold, and continue to apply mechanical static pressure to make the metal crystallize and solidify under pressure and forcibly eliminate the formation of solidification shrinkage. The shrinkage cavity shrinks to obtain a liquid die-forged aluminum alloy wheel blank without casting defects. Compared with the forging process, its advantages are that the equipment investment is low, the rim can be directly formed, and the mechanical properties are generally higher than that of ordinary castings, close to or even reaching the level of forgings, and it does not have the anisotropy that usually exists in forgings. The disadvantage is that liquid die forging products are the same as traditional forging products, which require milling to complete the shape of the spokes.
Please keep the source and address of this article for reprinting:The Forging Process Of Aluminum Alloy Wheel Industry
Minghe Die Casting Company are dedicated to manufacture and provide quality and high performance Casting Parts(metal die casting parts range mainly include Thin-Wall Die Casting,Hot Chamber Die Casting,Cold Chamber Die Casting),Round Service(Die Casting Service,Cnc Machining,Mold Making,Surface Treatment).Any custom Aluminum die casting, magnesium or Zamak/zinc die casting and other castings requirements are welcome to contact us.
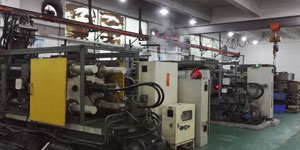
Under the control of ISO9001 and TS 16949,All processes are carried out through hundreds of advanced die casting machines, 5-axis machines, and other facilities, ranging from blasters to Ultra Sonic washing machines.Minghe not only has advanced equipment but also have professional team of experienced engineers,operators and inspectors to make the customer’s design come true.
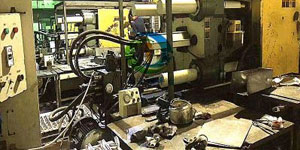
Contract manufacturer of die castings. Capabilities include cold chamber aluminum die casting parts from 0.15 lbs. to 6 lbs., quick change set up, and machining. Value-added services include polishing, vibrating, deburring, shot blasting, painting, plating, coating, assembly, and tooling. Materials worked with include alloys such as 360, 380, 383, and 413.
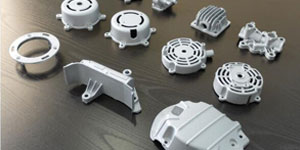
Zinc die casting design assistance/concurrent engineering services. Custom manufacturer of precision zinc die castings. Miniature castings, high pressure die castings, multi-slide mold castings, conventional mold castings, unit die and independent die castings and cavity sealed castings can be manufactured. Castings can be manufactured in lengths and widths up to 24 in. in +/-0.0005 in. tolerance.
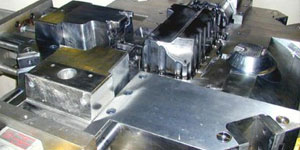
ISO 9001: 2015 certified manufacturer of die cast magnesium, Capabilities include high-pressure magnesium die casting up to 200 ton hot chamber & 3000 ton cold chamber, tooling design, polishing, molding, machining, powder & liquid painting, full QA with CMM capabilities, assembly, packaging & delivery.
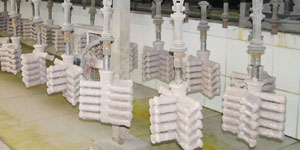
ITAF16949 certified. Additional Casting Service Include investment casting,sand casting,Gravity Casting, Lost Foam Casting,Centrifugal Casting,Vacuum Casting,Permanent Mold Casting,.Capabilities include EDI, engineering assistance, solid modeling and secondary processing.
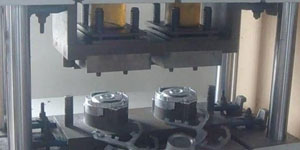
Casting Industries Parts Case Studies for: Cars, Bikes, Aircraft, Musical instruments, Watercraft, Optical devices, Sensors, Models, Electronic devices, Enclosures, Clocks, Machinery, Engines, Furniture, Jewelry, Jigs, Telecom, Lighting, Medical devices, Photographic devices, Robots, Sculptures, Sound equipment, Sporting equipment, Tooling, Toys and more.
What Can we help you do next?
∇ Go To Homepage For Die Casting China
→Casting Parts-Find out what we have done.
→Ralated Tips About Die Casting Services
By Minghe Die Casting Manufacturer |Categories: Helpful Articles |Material Tags: Aluminum Casting, Zinc Casting, Magnesium Casting, Titanium Casting, Stainless Steel Casting, Brass Casting,Bronze Casting,Casting Video,Company History,Aluminum Die Casting |Comments Off