The Forming Technology Of High-Strength Steel For Automobiles
Automobiles use high-strength steel, which can reduce the thickness of the plate due to its higher strength, making the automobile structure lighter. At the same time, the car's dent resistance, durability and large deformation impact strength are improved, and the cost is lower than that of light metals. The advantages of high-strength steel make it rapidly developed and widely used in the automotive industry, which helps to achieve the unity of automotive lightweight and safety. However, the forming range of high-strength steel is narrow, and the forming process encounters more difficult problems than traditional steel.
Therefore, advanced processing methods must be adopted according to the characteristics of high-strength steel. The forming technology of high-strength steel mainly includes cold stamping, hot forming, hydroforming and so on.
1. Cold stamping technology
The cold stamping forming technology of high-strength steel is similar to that of traditional steel cold stamping, but the forming range of high-strength steel is limited, and it is prone to springback after forming, and its springback is much larger than that of ordinary low-carbon steel stamping parts. The prediction and control of the steel have brought great difficulties. At the same time, high-strength steel faces problems such as wrinkling and cracking of the formed parts during application. These problems all lead to poor dimensional and shape accuracy of high-strength steel during forming. Japan's NKK Co., Ltd. developed a new steel plate easy stamping technology to solve the problem of cracking in the high-strength steel plate stamping process. This technology creates a gap of tens of microns between the steel plate and the die by injecting lubricating oil from the opening on the die. Therefore, the problem of steel plate cracking in the stamping process is prevented, and this method can be realized with a slight modification on the ordinary stamping machine.
2. Hot stamping technology
When the steel strength exceeds 1000 MPa, some parts with complex shapes are difficult to be formed by the conventional cold stamping process; even if the cold stamping process can be used, there are problems such as high punching force, easy cracking of the formed part, large springback, etc., so hot forming Technology came into being. The hot stamping forming technology is to heat the boron steel plate (initial strength of 500-600MPa) to austenitized state, and quickly transfer it to the mold for high-speed stamping. Under the condition of ensuring a certain pressure, the part is larger than the mold body. The cooling rate of 27℃/s is quenched, and the pressure-holding quenching is performed for a period of time. At the same time, the parts are formed with uniform martensite structure. High-strength steel hot stamping technology divides forming and strengthening into two steps to solve the contradiction between high-strength steel strength and plasticity. Its main advantages are: small deformation resistance, good plasticity, high forming limit, good stamping and chemical etching formability; easy control of springback, high precision of the formed parts; reduced tonnage requirements of the punching machine; low forming resistance of steel, low unit pressure of the die; forming parts Short production cycle, etc. However, hot stamping technology also has some shortcomings, such as large equipment investment, complex mold design and processing, and high maintenance and maintenance costs.
3. Hydroforming technology
Hydroforming technology is a plastic processing technology that relies on high-pressure liquid (water or oil) as a force transmission medium to form a workpiece. In the process of hydroforming, the sheet is formed into a convex or concave die by the pressure of a force-transmitting medium, which is a flexible processing technology. The hydroformed parts are mainly pipes, plates and shells. The required medium pressure is generally above 400MPa. The main advantages of using hydroforming technology are: it can form a hollow component that changes along the axis and cross-section of the component at one time; the cost of the mold is reduced; the precision of the formed part is improved, and the springback is also reduced; It is replaced by a single part, and the rigidity of the car body is increased at the same time, which is conducive to reducing the quality.
Please keep the source and address of this article for reprinting: The Forming Technology Of High-Strength Steel For Automobiles
Minghe Die Casting Company are dedicated to manufacture and provide quality and high performance Casting Parts(metal die casting parts range mainly include Thin-Wall Die Casting,Hot Chamber Die Casting,Cold Chamber Die Casting),Round Service(Die Casting Service,Cnc Machining,Mold Making,Surface Treatment).Any custom Aluminum die casting, magnesium or Zamak/zinc die casting and other castings requirements are welcome to contact us.
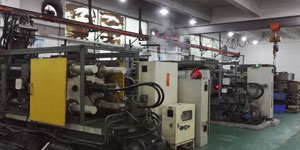
Under the control of ISO9001 and TS 16949,All processes are carried out through hundreds of advanced die casting machines, 5-axis machines, and other facilities, ranging from blasters to Ultra Sonic washing machines.Minghe not only has advanced equipment but also have professional team of experienced engineers,operators and inspectors to make the customer’s design come true.
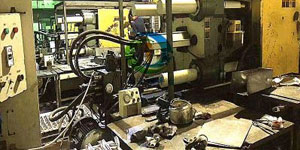
Contract manufacturer of die castings. Capabilities include cold chamber aluminum die casting parts from 0.15 lbs. to 6 lbs., quick change set up, and machining. Value-added services include polishing, vibrating, deburring, shot blasting, painting, plating, coating, assembly, and tooling. Materials worked with include alloys such as 360, 380, 383, and 413.
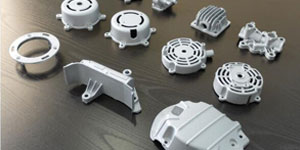
Zinc die casting design assistance/concurrent engineering services. Custom manufacturer of precision zinc die castings. Miniature castings, high pressure die castings, multi-slide mold castings, conventional mold castings, unit die and independent die castings and cavity sealed castings can be manufactured. Castings can be manufactured in lengths and widths up to 24 in. in +/-0.0005 in. tolerance.
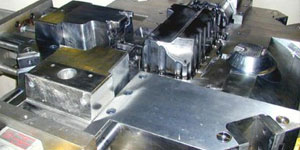
ISO 9001: 2015 certified manufacturer of die cast magnesium, Capabilities include high-pressure magnesium die casting up to 200 ton hot chamber & 3000 ton cold chamber, tooling design, polishing, molding, machining, powder & liquid painting, full QA with CMM capabilities, assembly, packaging & delivery.
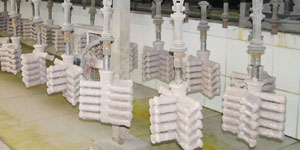
ITAF16949 certified. Additional Casting Service Include investment casting,sand casting,Gravity Casting, Lost Foam Casting,Centrifugal Casting,Vacuum Casting,Permanent Mold Casting,.Capabilities include EDI, engineering assistance, solid modeling and secondary processing.
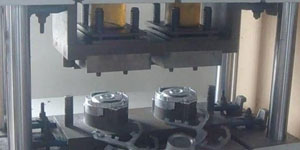
Casting Industries Parts Case Studies for: Cars, Bikes, Aircraft, Musical instruments, Watercraft, Optical devices, Sensors, Models, Electronic devices, Enclosures, Clocks, Machinery, Engines, Furniture, Jewelry, Jigs, Telecom, Lighting, Medical devices, Photographic devices, Robots, Sculptures, Sound equipment, Sporting equipment, Tooling, Toys and more.
What Can we help you do next?
∇ Go To Homepage For Die Casting China
→Casting Parts-Find out what we have done.
→Ralated Tips About Die Casting Services
By Minghe Die Casting Manufacturer |Categories: Helpful Articles |Material Tags: Aluminum Casting, Zinc Casting, Magnesium Casting, Titanium Casting, Stainless Steel Casting, Brass Casting,Bronze Casting,Casting Video,Company History,Aluminum Die Casting |Comments Off