The General Heat Treatment Of Steel
Annealing
The steel whose structure deviates from the equilibrium state is heated to an appropriate temperature, kept for a certain period of time, and then slowly cooled (usually cooled with the furnace) to obtain the structure close to the equilibrium state. The heat treatment process is called annealing.
The annealing of steel is divided into complete annealing, isothermal annealing, spheroidizing annealing, diffusion annealing and stress relief annealing.
1. Fully annealed
Complete annealing is also called recrystallization annealing, which is to heat the steel to 20℃~30℃ above Ac3, hold it for a certain period of time, and then slowly cool it (cooling in the furnace or burying in lime and sand) to obtain a heat treatment process close to the equilibrium structure. Complete annealing is generally used for hypoeutectoid steels.
The purpose of complete annealing is to homogenize and refine the coarse and uneven structure caused by hot working through complete recrystallization to improve performance; or to obtain a structure close to equilibrium for carbon steel and alloy steel above medium carbon. To reduce the hardness and improve the cutting performance. Due to the slow cooling rate, internal stress can also be eliminated.
2. Isothermal annealing
Isothermal annealing is to heat the steel to a temperature higher than Ac3 (or Ac1), and after holding for a proper time, it will be cooled to a certain temperature in the pearlite zone quickly, and maintained isothermally, so that the austenite is isothermally transformed, and then slowly cooled The heat treatment process.
The purpose of isothermal annealing is the same as that of complete annealing, which can obtain a uniform expected structure; for alloy steels with relatively stable austenite, the annealing time can be greatly shortened.
3. Spheroidizing annealing
Spheroidizing annealing is a heat treatment process to spheroidize carbides in steel. The purpose is to spheroidize the cementite in the secondary cementite and pearlite (normalizing before annealing will break the network cementite) to reduce the hardness and improve the cutting performance; and to prepare the organization for subsequent quenching. Spheroidizing annealing is mainly used for eutectoid steel and hypereutectoid steel.
The microstructure of hypereutectoid steel after spheroidizing annealing is fine and uniform spherical cementite distributed on the ferrite matrix. The heating temperature of spheroidizing annealing is slightly higher than Ac1. Spheroidizing annealing requires a longer holding time to ensure the spontaneous spheroidization of the secondary cementite. After heat preservation, it is cooled with the furnace.
4. Diffusion annealing
In order to reduce the inhomogeneity of chemical composition and structure of steel ingots, castings or forging billets, heat them to a temperature slightly lower than the solidus line (100℃~200℃ below the solidus line), and keep them for a long time (10h~15h), And a slow cooling heat treatment process is called diffusion annealing or homogenization annealing.
The grains of the steel after diffusion annealing are very coarse, so it is generally subjected to complete annealing or normalizing treatment.
5. Stress relief annealing
Low-temperature annealing to eliminate the residual internal stress in the workpiece caused by hot and cold processing such as casting, forging, welding, machining, and cold deformation is called stress relief annealing. Stress relief annealing is to heat the steel to a temperature lower than Ac1 (generally 500℃~650℃), and then cool it with the furnace after holding it. This treatment can eliminate about 50%~80% of the internal stress without causing structure Variety.
Normalizing (normalization)
The steel or steel parts are heated to 30℃~50℃ above Ac3 (for hypoeutectoid steel) and Accm (for hypereutectoid steel). After holding for a suitable time, the heat treatment of uniform cooling in free flowing air is called normalizing. Structure after normalizing: Hypoeutectoid steel is F+S, eutectoid steel is S, and hypereutectoid steel is S+Fe3CII.
The purpose of normalizing is to normalize the structure of steel, also known as normalization treatment, which is generally used in the following aspects:
- 1. As the final heat treatment, normalizing can refine the grains, homogenize the structure, reduce the ferrite content in the hypoeutectoid steel, increase and refine the pearlite content, thereby improving the strength, hardness and toughness of the steel.
- 2. As a pre-heated alloy structural steel with a large cross-section, it is often normalized before quenching or quenching and tempering (quenching and high temperature tempering) to eliminate Widmanstatten structure and band structure and obtain a fine and uniform structure. For hypereutectoid steel, the amount of secondary cementite can be reduced, and it will not form a continuous network to prepare the structure for spheroidizing annealing.
- 3. Improve cutting performance
Quenching
Heat the steel to above the phase transition temperature (hypoeutectoid steel is 30℃~50℃ above Ac3; eutectoid steel and hypereutectoid steel are 30℃~50℃ above Ac1), keep for a certain time and then quickly cool to obtain Martensite The heat treatment process of the body structure is called quenching.
Quenching temperature range of steel
Commonly used cooling media are water and oil. In order to reduce the deformation of the parts during quenching, a salt bath can be used as the medium.
Commonly used quenching methods include single-medium quenching, dual-medium quenching, graded quenching and austempering.
1. Hardenability of steel
The ability of steel to form martensite when it is quenched is called the hardenability of steel.
The hardenability of steel can be determined by the end quenching method.
Factors affecting hardenability:
- ①The eutectoid steel with carbon content has the smallest critical cooling rate and the best hardenability; as the carbon content decreases, the critical cooling rate increases, and the hardenability decreases; hypereutectoid steel increases with the carbon content , The critical cooling rate increases, and the hardenability decreases.
- ②Alloying elements except cobalt, after the other alloying elements are dissolved in austenite, the critical cooling rate is reduced, the C curve shifts to the right, and the hardenability of steel is improved. Therefore, the hardenability of alloy steel is often better than that of carbon steel.
- ③The austenitizing temperature increases the austenitizing temperature, which will make the austenite grains grow and have a uniform composition, which can reduce the nucleation rate of pearlite, reduce the critical cooling rate of steel, and increase its hardenability.
- ④ Undissolved second phase in steel. Carbides, nitrides and other non-metallic inclusions in steel that are not dissolved in austenite can become the non-spontaneous core of austenite decomposition, increasing the critical cooling rate and reducing quenching. Permeability.
After the steel is quenched and tempered, the entire section of the steel bar with good hardenability is tempered sorbite, with uniform mechanical properties, high strength, and good toughness, while the steel core with poor hardenability is flaky sorbite + iron Element body, only the surface layer is tempered sorbite, and the core has poor strength and toughness.
(a) Completely hardened; (b) Hardened to a larger thickness; (c) Hardened to a smaller thickness
Comparison of mechanical properties of steels with different hardenability after quenching and tempering
2. Hardenability of steel
The highest hardness that can be achieved after quenching is called the hardenability of steel, which is mainly determined by the carbon content of M.
Four.
After the steel is quenched, in order to eliminate the internal stress and obtain the required structure and performance, the heat treatment process of heating it to a temperature below Ac1, holding it for a certain period of time, and then cooling it to room temperature is called tempering.
Low temperature tempering
The tempering temperature is 150℃~250℃. During low temperature tempering, carbide flakes (Fe2.4C) are precipitated from the quenched martensite, and the supersaturation of martensite is reduced. Part of the retained austenite is transformed into lower bainite, but not much. Therefore, the structure after low temperature tempering is tempered martensite + retained austenite. Lower bainite can be ignored.
The purpose of low temperature tempering is to reduce the quenching stress, improve the toughness of the workpiece, and ensure the high hardness (generally 58HRC~64HRC) and high wear resistance after quenching.
Tempering
The tempering temperature is 350°C to 500°C, and a mixed structure of ferrite matrix and a large amount of dispersed fine-grained cementite is obtained, which is called tempered troostite (tempered T). Ferrite still retains the form of martensite, and cementite is coarser than carbides in tempered martensite.
Tempered troostite has a high elastic limit and yield strength, but also has a certain degree of toughness, the hardness is generally 35HRC ~ 45HRC.
High temperature tempering
The tempering temperature is 500℃~650℃, and the mixed structure of granular cementite and ferrite matrix is obtained, which is called tempered sorbite.
Tempered sorbite
Tempered sorbite (tempered S) has the best comprehensive mechanical properties, that is, the strength, plasticity and toughness are better, and the hardness is generally 25HRC~35HRC. Quenching and high temperature tempering are usually called quenching and tempering treatment.
Tempering brittleness occurs when steel is tempered, that is, after tempering in the two temperature ranges of 250℃~400℃ and 450℃~650℃, the impact toughness of steel will decrease significantly.
Changes in performance of steel during tempering:
The hardness of steel changes with tempering temperature The relationship between mechanical properties of steel and tempering temperature
The relationship between martensite carbon content, retained austenite content, internal stress, carbide particle size and tempering temperature in quenched steel.
Please keep the source and address of this article for reprinting:The General Heat Treatment Of Steel
Minghe Die Casting Company are dedicated to manufacture and provide quality and high performance Casting Parts(metal die casting parts range mainly include Thin-Wall Die Casting,Hot Chamber Die Casting,Cold Chamber Die Casting),Round Service(Die Casting Service,Cnc Machining,Mold Making,Surface Treatment).Any custom Aluminum die casting, magnesium or Zamak/zinc die casting and other castings requirements are welcome to contact us.
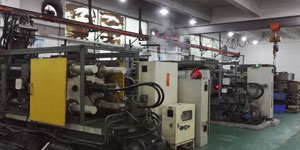
Under the control of ISO9001 and TS 16949,All processes are carried out through hundreds of advanced die casting machines, 5-axis machines, and other facilities, ranging from blasters to Ultra Sonic washing machines.Minghe not only has advanced equipment but also have professional team of experienced engineers,operators and inspectors to make the customer’s design come true.
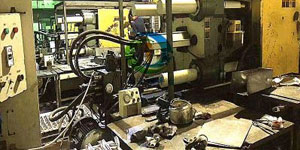
Contract manufacturer of die castings. Capabilities include cold chamber aluminum die casting parts from 0.15 lbs. to 6 lbs., quick change set up, and machining. Value-added services include polishing, vibrating, deburring, shot blasting, painting, plating, coating, assembly, and tooling. Materials worked with include alloys such as 360, 380, 383, and 413.
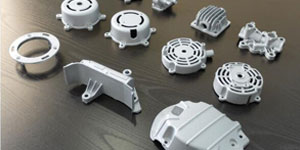
Zinc die casting design assistance/concurrent engineering services. Custom manufacturer of precision zinc die castings. Miniature castings, high pressure die castings, multi-slide mold castings, conventional mold castings, unit die and independent die castings and cavity sealed castings can be manufactured. Castings can be manufactured in lengths and widths up to 24 in. in +/-0.0005 in. tolerance.
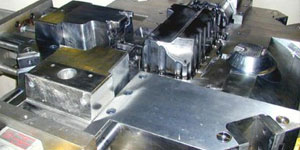
ISO 9001: 2015 certified manufacturer of die cast magnesium, Capabilities include high-pressure magnesium die casting up to 200 ton hot chamber & 3000 ton cold chamber, tooling design, polishing, molding, machining, powder & liquid painting, full QA with CMM capabilities, assembly, packaging & delivery.
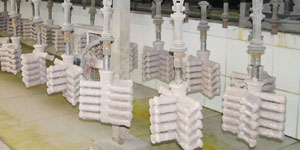
ITAF16949 certified. Additional Casting Service Include investment casting,sand casting,Gravity Casting, Lost Foam Casting,Centrifugal Casting,Vacuum Casting,Permanent Mold Casting,.Capabilities include EDI, engineering assistance, solid modeling and secondary processing.
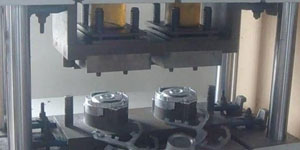
Casting Industries Parts Case Studies for: Cars, Bikes, Aircraft, Musical instruments, Watercraft, Optical devices, Sensors, Models, Electronic devices, Enclosures, Clocks, Machinery, Engines, Furniture, Jewelry, Jigs, Telecom, Lighting, Medical devices, Photographic devices, Robots, Sculptures, Sound equipment, Sporting equipment, Tooling, Toys and more.
What Can we help you do next?
∇ Go To Homepage For Die Casting China
→Casting Parts-Find out what we have done.
→Ralated Tips About Die Casting Services
By Minghe Die Casting Manufacturer |Categories: Helpful Articles |Material Tags: Aluminum Casting, Zinc Casting, Magnesium Casting, Titanium Casting, Stainless Steel Casting, Brass Casting,Bronze Casting,Casting Video,Company History,Aluminum Die Casting |Comments Off