The Heat Treatment Process Of 45 Steel Quenching And Tempering
Quenching and tempering is a double heat treatment of quenching and high temperature tempering, and its purpose is to make the workpiece have good comprehensive mechanical properties.
Quenched and tempered steel has two categories: carbon quenched and tempered steel and alloy quenched and tempered steel. Regardless of whether it is carbon steel or alloy steel, its carbon content is controlled strictly. If the carbon content is too high, the strength of the workpiece after quenching and tempering is high, but the toughness is not enough. If the carbon content is too low, the toughness will increase and the strength will be insufficient. In order to obtain good overall performance of quenched and tempered parts, the carbon content is generally controlled at 0.30~0.50%.
When quenching and tempering, the entire section of the workpiece is required to be quenched, so that the workpiece can obtain a microstructure dominated by fine needle-shaped quenched martensite. Through high temperature tempering, a microstructure dominated by uniform tempered sorbite is obtained. It is impossible for small factories to conduct metallographic analysis for each furnace, and generally only perform hardness testing. This means that the hardness after quenching must reach the quenching hardness of the material, and the hardness after tempering is checked according to the requirements of the drawing.
The operation of the quenching and tempering treatment of the workpiece must be carried out strictly in accordance with the process documents. We only provide some views on how to implement the process during the operation.
Quenched and tempered of 45 steel 45 steel is a medium carbon structural steel with good cold and hot workability, good mechanical properties, low price and wide sources, so it is widely used. Its biggest weakness is its low hardenability, large cross-sectional dimensions and high-demand workpieces.
The quenching temperature of 45 steel is A3+ (30~50) ℃. In actual operation, the upper limit is generally taken. A higher quenching temperature can speed up the heating of the workpiece, reduce surface oxidation, and improve work efficiency. In order to homogenize the austenite of the workpiece, sufficient holding time is required. If the actual amount of furnace installed is large, the holding time needs to be extended appropriately. Otherwise, there may be insufficient hardness due to uneven heating. However, if the holding time is too long, coarse grains and serious oxidative decarburization will also occur, which will affect the quenching quality. We believe that if the installed furnace volume is greater than the provisions of the process documents, the heating and holding time needs to be extended by 1/5.
Because 45 steel machining has low hardenability, a 10% saline solution with a high cooling rate should be used. After the workpiece enters the water, it should be quenched, but not cold through. If the workpiece is cooled in salt water, it may crack the workpiece. This is caused by the rapid transformation of austenite into martensite when the workpiece is cooled to about 180°C. Caused by excessive tissue stress.
Therefore, when the quenched workpiece is rapidly cooled to this temperature region, a slow cooling method should be adopted. Since the temperature of the outlet water is difficult to control, it must be operated by experience. When the shaking of the workpiece in the water stops, the outlet can be air-cooled (oil cooling is better). In addition, the workpiece should be moved but not static when it enters water, and should be moved regularly according to the geometric shape of the workpiece. The static cooling medium and the static workpiece result in uneven hardness, uneven stress and large deformation or even cracking of the workpiece.
The hardness of the 45 steel quenched and tempered parts after quenching should reach HRC56~59. The possibility of a large cross section is lower, but it cannot be lower than HRC48. Otherwise, it means that the workpiece has not been completely quenched, and sorbite or even ferrite may appear in the structure. Organization, this kind of organization is still retained in the matrix through tempering, failing to achieve the purpose of quenching and tempering.
For high temperature tempering of 45 steel after quenching, the heating temperature is usually 560~600℃, and the hardness requirement is HRC22~34. Because the purpose of quenching and tempering is to obtain comprehensive mechanical properties, the hardness range is relatively wide. However, if the drawings have hardness requirements, the tempering temperature must be adjusted according to the drawings to ensure the hardness. For example, some shaft parts require high strength, so the hardness requirements are high; and some gears and shaft parts with keyways need to be milled and inserted after quenching and tempering, so the hardness requirements are lower. Regarding the tempering and holding time, it depends on the hardness requirements and the size of the workpiece. We believe that the hardness after tempering depends on the tempering temperature, which has little to do with the tempering time, but it must be back through. Generally, the tempering and holding time of the workpiece is always More than one hour.
Please keep the source and address of this article for reprinting: The Heat Treatment Process Of 45 Steel Quenching And Tempering
Minghe Die Casting Company are dedicated to manufacture and provide quality and high performance Casting Parts(metal die casting parts range mainly include Thin-Wall Die Casting,Hot Chamber Die Casting,Cold Chamber Die Casting),Round Service(Die Casting Service,Cnc Machining,Mold Making,Surface Treatment).Any custom Aluminum die casting, magnesium or Zamak/zinc die casting and other castings requirements are welcome to contact us.
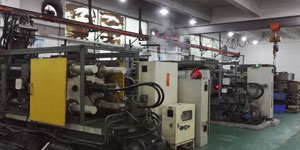
Under the control of ISO9001 and TS 16949,All processes are carried out through hundreds of advanced die casting machines, 5-axis machines, and other facilities, ranging from blasters to Ultra Sonic washing machines.Minghe not only has advanced equipment but also have professional team of experienced engineers,operators and inspectors to make the customer’s design come true.
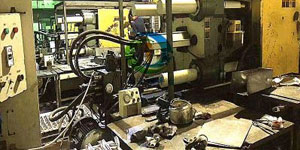
Contract manufacturer of die castings. Capabilities include cold chamber aluminum die casting parts from 0.15 lbs. to 6 lbs., quick change set up, and machining. Value-added services include polishing, vibrating, deburring, shot blasting, painting, plating, coating, assembly, and tooling. Materials worked with include alloys such as 360, 380, 383, and 413.
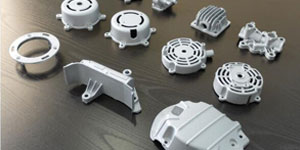
Zinc die casting design assistance/concurrent engineering services. Custom manufacturer of precision zinc die castings. Miniature castings, high pressure die castings, multi-slide mold castings, conventional mold castings, unit die and independent die castings and cavity sealed castings can be manufactured. Castings can be manufactured in lengths and widths up to 24 in. in +/-0.0005 in. tolerance.
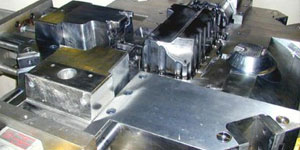
ISO 9001: 2015 certified manufacturer of die cast magnesium, Capabilities include high-pressure magnesium die casting up to 200 ton hot chamber & 3000 ton cold chamber, tooling design, polishing, molding, machining, powder & liquid painting, full QA with CMM capabilities, assembly, packaging & delivery.
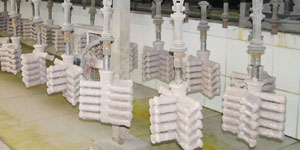
ITAF16949 certified. Additional Casting Service Include investment casting,sand casting,Gravity Casting, Lost Foam Casting,Centrifugal Casting,Vacuum Casting,Permanent Mold Casting,.Capabilities include EDI, engineering assistance, solid modeling and secondary processing.
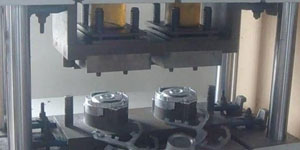
Casting Industries Parts Case Studies for: Cars, Bikes, Aircraft, Musical instruments, Watercraft, Optical devices, Sensors, Models, Electronic devices, Enclosures, Clocks, Machinery, Engines, Furniture, Jewelry, Jigs, Telecom, Lighting, Medical devices, Photographic devices, Robots, Sculptures, Sound equipment, Sporting equipment, Tooling, Toys and more.
What Can we help you do next?
∇ Go To Homepage For Die Casting China
→Casting Parts-Find out what we have done.
→Ralated Tips About Die Casting Services
By Minghe Die Casting Manufacturer |Categories: Helpful Articles |Material Tags: Aluminum Casting, Zinc Casting, Magnesium Casting, Titanium Casting, Stainless Steel Casting, Brass Casting,Bronze Casting,Casting Video,Company History,Aluminum Die Casting |Comments Off