The History And Trend Of Semi-Solid Metal Casting Process
Since 1971, DBSpencer and MCFlemings of the Massachusetts Institute of Technology in the United States invented a new process of stirring casting (stir cast), that is, the preparation of Srr15%pb rheological slurry by rotating double barrel mechanical stirring method, semi-solid metal ( SSM) Foundry technology has experienced more than 20 years of research and development.
Alloys prepared by stirring casting are generally called non-dendritic alloys or partially solidified casting alloys (Partially Solidified Casting Alloys). Because the products using this technology have the characteristics of high quality, high performance and high alloying, they have strong vitality.
In addition to the application in military equipment, it began to focus on the key components of automatic vehicles, for example, for automobile wheels, which can improve performance, reduce weight, and reduce scrap rate. Since then, it has gradually been applied in other fields, producing high-performance and near-net-shaped parts. Forming machines for semi-solid metal casting technology have also been introduced one after another.
At present, the semi-solid casting die casting machine from 600 tons to 2000 tons has been developed and produced, and the weight of the formed parts can reach more than 7kg. Currently, this process technology is widely used in the United States and Europe. The semi-solid metal casting process is considered to be one of the most promising near-net forming and new material preparation technologies in the 21st century.
Process principle
In the ordinary casting process, the primary crystals grow up in the form of dendrites. When the solid phase ratio reaches about 0.2, the dendrites form a continuous network skeleton and lose their macroscopic fluidity. If the liquid metal is stirred vigorously during the cooling process from the liquid phase to the solid phase, the dendritic network skeleton that is easily formed during ordinary casting will be broken to retain the dispersed granular structure and be suspended in the remaining liquid phase. This granular non-dendritic microstructure still has certain rheology when the solid phase ratio reaches 0.5-0.6, so that conventional forming processes such as die casting, extrusion, die forging, etc. can be used to achieve metal forming.
Alloy preparation
There are many methods for preparing semi-solid alloys. In addition to mechanical stirring methods, electromagnetic stirring methods have been developed in recent years, electromagnetic pulse loading methods, ultrasonic vibration stirring methods, forced flow of alloy liquid along curved channels under external force, and strain-induced melting activation. Method (SIMA), spray deposition method (Ospray), control alloy pouring temperature method, etc. Among them, the electromagnetic stirring method, the alloy pouring temperature control method and the SIMA method are the most promising methods for industrial applications.
1. Mechanical stirring method
Mechanical stirring is the earliest method used to prepare semi-solid alloys. Flemings et al. successfully prepared a tin-lead alloy semi-solid slurry using a set of stirring devices consisting of a concentric toothed inner and outer cylinder (the outer cylinder was rotating, and the inner cylinder was stationary); H. Lehuy et al. used a stirring paddle to prepare aluminum- Semi-solid slurry of copper alloy, zinc-aluminum alloy and aluminum-silicon alloy. Later generations improved the agitator and prepared ZA-22 alloy semi-solid slurry by using a spiral agitator. Through the improvement, the stirring effect of the slurry is improved, the overall flow strength of the molten metal in the mold is strengthened, and the molten metal generates downward pressure, which promotes pouring and improves the mechanical properties of the ingot.
2. Electromagnetic stirring method
Electromagnetic stirring is the use of a rotating electromagnetic field to generate an induced current in the molten metal. The molten metal moves under the action of Loren's magnetic force to achieve the purpose of stirring the molten metal. At present, there are mainly two methods to generate a rotating magnetic field: one is the traditional method of passing alternating current in the induction coil; the other is the rotating permanent magnet method introduced by C.Vives of France in 1993, which has the advantage of electromagnetic induction The device is composed of high-performance permanent magnet materials with high magnetic field strength. By changing the arrangement of the permanent magnets, the molten metal can produce an obvious three-dimensional flow, which improves the stirring effect and reduces the entrapment of gas during stirring.
3. Strain-induced melting activation method (SIMA)
Strain-induced melting activation method (SIMA) is to pre-deform the conventional ingots, such as extrusion, rolling and other thermal processing into semi-finished bars. At this time, the microstructure has a strongly elongated deformed structure, and then it is heated to The solid-liquid two-phase zone is isothermal for a certain period of time, and the elongated crystal grains become fine particles, which are then rapidly cooled to obtain a non-dendritic structure ingot.
The effect of the SIMA process mainly depends on the two stages of lower temperature hot working and remelting, or adding a cold working stage between the two, the process is easier to control. SIMA technology is suitable for a variety of alloys with high and low melting points, and has unique advantages in preparing non-dendritic alloys with higher melting points. It has been successfully applied to stainless steel, tool steel, copper alloy, and aluminum alloy series, and has obtained a non-dendritic structure alloy with a grain size of about 20um. It is becoming a competitive method for preparing semi-solid forming raw materials. However, its biggest disadvantage is that the size of the prepared blank is small.
4. New methods developed in recent years
In recent years, Southeast University and the Arety Research Institute in Japan have discovered that by controlling the casting temperature of the alloy, the primary dendritic structure can be transformed into a spherulitic structure. The characteristic of this method is that there is no need to add alloying elements nor stir. V. Dobatkin et al. proposed a method of adding a refiner to liquid metal and performing ultrasonic treatment to obtain a semi-solid ingot, which is called ultrasonic treatment.
Molding Method
There are many forming methods for semi-solid alloys, mainly:
1. Rheoforming (Rheocast) strongly stirs the molten metal from liquid to solid during the cooling process, and directly hydraulically casts or extrudes the obtained semi-solid metal slurry with a certain solid fraction.
For example, R. Shibata et al. once sent the semi-solid alloy slurry prepared by electromagnetic stirring method directly into the injection chamber of the die-casting machine for forming. The mechanical properties of aluminum alloy castings produced by this method are higher than those of extrusion castings, and are equivalent to those of semi-solid thixotropic castings. The problem is that the storage and transportation of semi-solid metal slurry is difficult, so there are not many practical applications.
2. Thixocasting (Thixoforming, Thixocast)
The prepared non-dendritic structure ingot is reheated to the solid-liquid two-phase zone to reach a suitable viscosity, and then die-casting or extrusion forming.
EOPCO, HPM Corp., Prince Machine, THT Presses in the United States, Buhler in Switzerland, IDRA USA, Italpresse of America in Italy, Producer USA in Canada, Toshib a Machine Corp. Special equipment for thixoforming of solid aluminum alloy. This method is easy to automate the heating and conveying of the blank, so it is the main process method of semi-solid casting today.
3. Injection Molding
The molten metal is directly cooled to a suitable temperature instead of the semi-solid slurry after treatment, and injected into the cavity to form with certain process conditions. For example, the Thixoforming Development Center in Wisconsin, USA, used this method for semi-solid casting of magnesium alloys. Professor K.K. Wang from Cornell University in the United States and others have developed a similar magnesium alloy injection molding device. The semi-solid slurry is added from the material tube and injected into the cavity after proper cooling.
4. Low temperature continuous casting
The so-called low-temperature continuous casting is a casting method in which the superheat of the molten metal is controlled at about 0°C and forced cooling is performed under the mold, as shown in Figure 4. Central segregation is a big problem in continuous casting, and breakage may occur during continuous rolling of the wire rod. Therefore, the process is of great significance.
5. Strip continuous casting
Flemings used Sn-15%pb low melting point metal to carry out strip continuous casting experiments, and analyzed heat transfer, solidification and deformation. It is believed that the thickness of the strip is related to the pressure of the roll, solid phase ratio, rheological shear speed and continuous casting speed. When the specific pressure under extrusion is large, micro segregation is promoted. In order to ensure the surface and internal quality and dimensional accuracy, it is necessary to strictly control the process parameters of semi-solid metal manufacturing such as the solid phase ratio, the size of the primary crystal shape, and the amount of discharged metal.
For high melting point metals such as phosphor bronze Cu-Sn-P alloy (Cu-8%Sn-0.1%P), the liquidus temperature is 10300℃, which is difficult to heat-process. It has obvious effect on the thin plate made of this semi-solid alloy. At present, it is possible to prepare semi-solid stainless steel ingots and high-speed tool steel ingots with excellent organization.
Technical advantages
The advantages of semi-solid die casting process can be summarized in process advantages and product advantages.
1. Process advantage
- 1) Fine grain structure can be obtained without adding any grain refiner, eliminating columnar crystals and coarse dendrites in traditional casting.
- 2) Low forming temperature (such as aluminum alloy can be lowered by more than 1200℃), which can save energy.
- 3) The life of the mold is extended. The shear stress of the semi-solid slurry at a lower solid temperature is three orders of magnitude smaller than that of the traditional dendritic slurry, so the filling is stable, the thermal load is small, and the thermal fatigue strength is reduced.
- 4) Reduce pollution and unsafe factors. Get rid of the high temperature liquid metal environment during operation.
- 5) The deformation resistance is small, and the homogeneous processing can be realized with a small force, and the forming of difficult-to-process materials is easy.
- 6) The solidification speed is accelerated, the productivity is improved, and the process cycle is shortened.
- 7) It is suitable for computer-aided design and manufacturing, which improves the degree of automation of production.
2. Product advantages
- 1) The parts are of high quality. Due to the refinement of crystal grains, uniform structure distribution, reduced body shrinkage, and reduced thermal cracking tendency, the shrinkage tendency of the matrix is eliminated, and the mechanical properties are greatly improved.
- 2) The solidification shrinkage is small, so the molded body has high dimensional accuracy, small machining allowance, and nearly net shape.
- 3) Wide range of forming alloys. Non-ferrous alloys include aluminum, magnesium, zinc, tin, copper, and nickel-based alloys; iron-based alloys include stainless steel and low-alloy steel.
- 4) Manufacturing metal matrix composite materials. Utilizing the high viscosity of semi-solid metal to make alloys with large density difference and small solid solubility, it can also effectively mix different materials to make new composite materials.
Please keep the source and address of this article for reprinting: The History And Trend Of Semi-Solid Metal Casting Process
Minghe Die Casting Company are dedicated to manufacture and provide quality and high performance Casting Parts(metal die casting parts range mainly include Thin-Wall Die Casting,Hot Chamber Die Casting,Cold Chamber Die Casting),Round Service(Die Casting Service,Cnc Machining,Mold Making,Surface Treatment).Any custom Aluminum die casting, magnesium or Zamak/zinc die casting and other castings requirements are welcome to contact us.
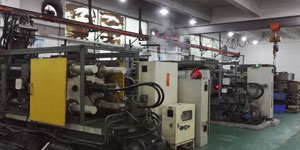
Under the control of ISO9001 and TS 16949,All processes are carried out through hundreds of advanced die casting machines, 5-axis machines, and other facilities, ranging from blasters to Ultra Sonic washing machines.Minghe not only has advanced equipment but also have professional team of experienced engineers,operators and inspectors to make the customer’s design come true.
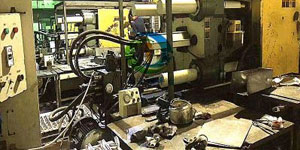
Contract manufacturer of die castings. Capabilities include cold chamber aluminum die casting parts from 0.15 lbs. to 6 lbs., quick change set up, and machining. Value-added services include polishing, vibrating, deburring, shot blasting, painting, plating, coating, assembly, and tooling. Materials worked with include alloys such as 360, 380, 383, and 413.
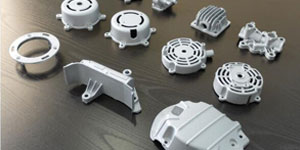
Zinc die casting design assistance/concurrent engineering services. Custom manufacturer of precision zinc die castings. Miniature castings, high pressure die castings, multi-slide mold castings, conventional mold castings, unit die and independent die castings and cavity sealed castings can be manufactured. Castings can be manufactured in lengths and widths up to 24 in. in +/-0.0005 in. tolerance.
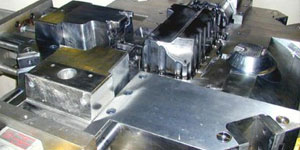
ISO 9001: 2015 certified manufacturer of die cast magnesium, Capabilities include high-pressure magnesium die casting up to 200 ton hot chamber & 3000 ton cold chamber, tooling design, polishing, molding, machining, powder & liquid painting, full QA with CMM capabilities, assembly, packaging & delivery.
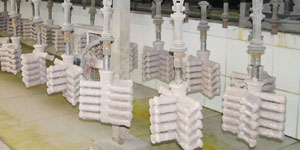
ITAF16949 certified. Additional Casting Service Include investment casting,sand casting,Gravity Casting, Lost Foam Casting,Centrifugal Casting,Vacuum Casting,Permanent Mold Casting,.Capabilities include EDI, engineering assistance, solid modeling and secondary processing.
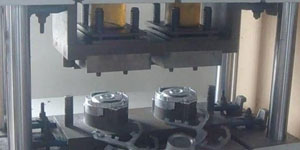
Casting Industries Parts Case Studies for: Cars, Bikes, Aircraft, Musical instruments, Watercraft, Optical devices, Sensors, Models, Electronic devices, Enclosures, Clocks, Machinery, Engines, Furniture, Jewelry, Jigs, Telecom, Lighting, Medical devices, Photographic devices, Robots, Sculptures, Sound equipment, Sporting equipment, Tooling, Toys and more.
What Can we help you do next?
∇ Go To Homepage For Die Casting China
→Casting Parts-Find out what we have done.
→Ralated Tips About Die Casting Services
By Minghe Die Casting Manufacturer |Categories: Helpful Articles |Material Tags: Aluminum Casting, Zinc Casting, Magnesium Casting, Titanium Casting, Stainless Steel Casting, Brass Casting,Bronze Casting,Casting Video,Company History,Aluminum Die Casting |Comments Off