The Improvement Method Of Mold Performance
In addition to the reasonable coordination of the matrix with sufficiently high strength and toughness, the surface properties of the mold are very important to the working performance and service life of the mold. These surface properties refer to: wear resistance, corrosion resistance, friction coefficient, fatigue performance, etc. The improvement of these properties is very limited and uneconomical by relying solely on the improvement and improvement of the base material. Surface treatment technology can often get twice the result with half the effort. This is the reason why surface treatment technology has developed rapidly.
The surface treatment technology of the mold is a systematic engineering of changing the morphology, chemical composition, structure and stress state of the mold surface through surface coating, surface modification or composite treatment technology to obtain the required surface properties. From the surface treatment method, it can be divided into: chemical method, physical method, physical chemical method and mechanical method. Although new processing technologies aimed at improving the surface performance of molds are emerging, the most common applications in mold manufacturing are nitriding, carburizing, and hardened film deposition.
The nitriding process includes gas nitriding, ion nitriding, liquid nitriding, etc. In each nitriding method, there are several nitriding technologies, which can meet the requirements of different steel types and different workpieces. Because the nitriding technology can form a surface with excellent performance, and the nitriding process and the quenching process of the die steel have good coordination, at the same time, the nitriding temperature is low, no intense cooling is required after nitriding, and the deformation of the mold is extremely small. Surface strengthening is the earlier nitriding technology, and it is also the most widely used.
The purpose of mold carburizing is mainly to improve the overall strength and toughness of the mold, that is, the working surface of the mold has high strength and wear resistance. The technical idea introduced from this is to use lower-grade materials, that is, through carburizing and quenching. To replace higher-level materials, thereby reducing manufacturing costs.
Hardened film deposition technology is currently more mature CVD, PVD. In order to increase the bonding strength of the surface of the film layer workpiece, a variety of enhanced CVD and PVD technologies have now been developed. Hardened film deposition technology was first applied to tools (knives, cutting tools, measuring tools, etc.) with excellent results. Many kinds of tools have adopted hardened film coating as a standard process. The mold has been coated with hardened film technology since the 1980s. Under the current technical conditions, the cost of hardened film deposition technology (mainly equipment) is relatively high, and it is still only applied to some precision and long-life molds. If a heat treatment center is established, the cost of coating hardened film will be greatly reduced. , If more molds adopt this technology, the overall mold manufacturing level can be improved.
Please keep the source and address of this article for reprinting:The Improvement Method Of Mold Performance
Minghe Die Casting Company are dedicated to manufacture and provide quality and high performance Casting Parts(metal die casting parts range mainly include Thin-Wall Die Casting,Hot Chamber Die Casting,Cold Chamber Die Casting),Round Service(Die Casting Service,Cnc Machining,Mold Making,Surface Treatment).Any custom Aluminum die casting, magnesium or Zamak/zinc die casting and other castings requirements are welcome to contact us.
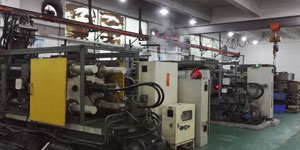
Under the control of ISO9001 and TS 16949,All processes are carried out through hundreds of advanced die casting machines, 5-axis machines, and other facilities, ranging from blasters to Ultra Sonic washing machines.Minghe not only has advanced equipment but also have professional team of experienced engineers,operators and inspectors to make the customer’s design come true.
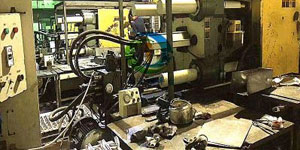
Contract manufacturer of die castings. Capabilities include cold chamber aluminum die casting parts from 0.15 lbs. to 6 lbs., quick change set up, and machining. Value-added services include polishing, vibrating, deburring, shot blasting, painting, plating, coating, assembly, and tooling. Materials worked with include alloys such as 360, 380, 383, and 413.
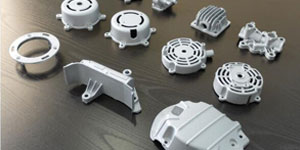
Zinc die casting design assistance/concurrent engineering services. Custom manufacturer of precision zinc die castings. Miniature castings, high pressure die castings, multi-slide mold castings, conventional mold castings, unit die and independent die castings and cavity sealed castings can be manufactured. Castings can be manufactured in lengths and widths up to 24 in. in +/-0.0005 in. tolerance.
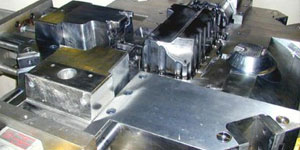
ISO 9001: 2015 certified manufacturer of die cast magnesium, Capabilities include high-pressure magnesium die casting up to 200 ton hot chamber & 3000 ton cold chamber, tooling design, polishing, molding, machining, powder & liquid painting, full QA with CMM capabilities, assembly, packaging & delivery.
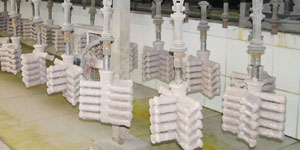
ITAF16949 certified. Additional Casting Service Include investment casting,sand casting,Gravity Casting, Lost Foam Casting,Centrifugal Casting,Vacuum Casting,Permanent Mold Casting,.Capabilities include EDI, engineering assistance, solid modeling and secondary processing.
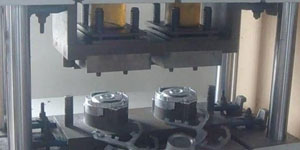
Casting Industries Parts Case Studies for: Cars, Bikes, Aircraft, Musical instruments, Watercraft, Optical devices, Sensors, Models, Electronic devices, Enclosures, Clocks, Machinery, Engines, Furniture, Jewelry, Jigs, Telecom, Lighting, Medical devices, Photographic devices, Robots, Sculptures, Sound equipment, Sporting equipment, Tooling, Toys and more.
What Can we help you do next?
∇ Go To Homepage For Die Casting China
→Casting Parts-Find out what we have done.
→Ralated Tips About Die Casting Services
By Minghe Die Casting Manufacturer |Categories: Helpful Articles |Material Tags: Aluminum Casting, Zinc Casting, Magnesium Casting, Titanium Casting, Stainless Steel Casting, Brass Casting,Bronze Casting,Casting Video,Company History,Aluminum Die Casting |Comments Off