The Improvement Of Current Shell Making Process In Investment Casting
1 Determination of fertility
The inoculation amount is generally determined according to the metallographic structure of the product. The metallographic structure to be considered mainly includes the shape and length of graphite, whether there is cementite, and the content of pearlite. Green sand is the sand mold with the fastest cooling rate among all sand molds. The water content is generally around 3.0%, and some reach 4.0%. Therefore, the production of gray iron parts from green sand is most likely to cause cementite in the thin-walled parts, and other conditions remain unchanged. Under the circumstances, this becomes the most important basis for judging how much fertility is added. Our company has encountered such a problem. The amount of the same raw iron liquid and the same inoculant in different products varies greatly, ranging from 0.15% to 0.9%, and the thin-walled part of the product with 0.9% inoculation amount is still Cementite often occurs. Even if the shape of the parts differs greatly, such a large deviation is unreasonable. For this reason, we conducted an on-site investigation.
The pouring weight of each type of product two is 13 kg less than product one. Therefore, the pouring time of the same amount of molten iron must be more than doubled. The pouring weight of each type of molten iron cannot be changed. Regardless of the inoculant, it is impossible to keep it from declining within 37 minutes. The problem lies in the amount of iron produced. If you reduce the amount of iron produced per pack and produce two more irons, the inoculation decline can be avoided; or if the inoculation is shifted back, that is, to increase the amount of inoculation with the flow, this problem can also be solved.
Since the tapping and the hoisting platform are the same crane, changing the tapping method will inevitably have a greater impact on production and logistics, so we chose the method of increasing inoculation with the flow. According to various information, generally the inoculation rate of gray cast iron is about 0.2% to ensure good inoculation. We have tried to increase the inoculation rate with the flow.
After increasing the amount of inoculation with flow, the amount of inoculant added in the iron trough is greatly reduced. Therefore, inoculation with flow is the best way to solve the decline of inoculation. However, the amount of inoculation with the flow is too large, and the inoculant may not be completely dissolved. Therefore, we finally chose the method of 0.3% for the iron trough + 0.18% for the flow. Compared with green sand, the chilling effect of resin sand on gray iron parts is much smaller, and the possibility of white mouth is much less. Therefore, the determination of the inoculation capacity should mainly consider the shape and length of graphite, and the content of pearlite.
2 About Baikou
White mouths often appear in our products. White mouths have a great impact on product processing performance. How to prevent and eliminate them has always been the focus of our daily work. There are many reasons for the white mouth. Here we put aside the influence of the shape of the part itself and the moisture content of the molding sand, and only conduct some investigations on the aspects of molten iron and inoculation.
2.1 The influence of molten iron quality
If the original iron liquid has a deep white mouth, the product has a deep white mouth, which is well known. The depth of the raw iron white mouth is related to the heredity of the pig iron white mouth, the amount of scrap added, and the level of w(S). In the production process, there was a period of time. Due to the shortage of pig iron, we could only use ductile iron pig iron to produce gray iron castings. Its w (Si) content was extremely low. The original inoculation method was adopted, and the product was white and deep. Can only use the method of increasing fertility to eliminate white mouth.
Multi-use of scrap steel will also lead to an increase in the product. The effect of S on incubation is relatively clear, w(S) in the range of 0.05% to 0.1% is good for incubation, and of course it is also beneficial for reducing white mouth; if w(S) is low, you can use iron sulfide Concentrate method is used to supplement, but is w(S) lower than 0.05%, there must be a problem? My company used to have a product of 0.02%~0.04% w(S) for a long time. There is no problem of infertility. The analysis believes that this may be related to the inoculant used by our company.
The SiBaCa inoculant used by our company has a good inoculation effect on high and low w(S) iron liquid. However, in order to ensure a good incubation, it is better to have a higher w(S) content. 2.2 The influence of inoculation The existing inoculants with strong ability to eliminate white mouth mainly include inoculants containing Sr, RE, Ca and other elements. Generally, it can ensure that the triangle test piece does not appear white mouth within 15-20 minutes. Enough for the product. However, no matter how strong the inoculant is, there is a problem of decay, so the key to preventing white mouth is how to pour the molten iron as soon as possible after inoculation, and strengthening the inoculation with the flow is undoubtedly the best way.
In our experience, as long as the amount of inoculation is about 0.15%, for most products, the white mouth problem can basically be solved.
3 About inoculants
There are many varieties of inoculants sold in the market, so you should choose the inoculant products that are high in price and suitable for you.
3.1 75SiFe
75 SiFe is the most commonly used inoculant, of which Al and Ca play an important role in the inoculation effect. However, the molten iron bred by 75 SiFe decays quickly, and it is generally not suitable for large-scale production and assembly line casting furnace production. To effectively promote the formation of A-type graphite and prevent the generation of white holes at the thin wall, the addition of 75 SiFe must be increased, sometimes reaching 1.0%, but the addition of 1.0% not only increases the cost, but may also cause shrinkage porosity of the casting. Therefore, it is not recommended as the first inoculant.
3.2 Containing Sr inoculant
The Sr-containing inoculant has a strong ability to eliminate white mouth, which is beneficial to improve the shape and distribution of graphite in thin-walled castings, so that the difference in the organization of different thicknesses is smaller, and theoretically also has the effect of preventing shrinkage [1]. Sr-containing inoculants have high requirements on the amount of aluminum w(Al) and w(Ca) because the inoculant effect of Al and Ca is just the opposite of that of Sr. Generally, w(Al) ≤0.1%, w(Ca) ≤0.3% is required. To achieve such amounts of w(Al) and w(Ca), SiFe must be refined, which will inevitably increase the production cost of inoculants containing Sr, so Inoculants containing Sr are more expensive, almost twice as much as 75SiFe. However, the addition amount of the inoculant containing Sr is about one-third of the 75SiFe, so overall, compared with 75SiFe, the inoculation effect is improved, and it is economically cost-effective.
There is information that Sr-containing inoculants can solve the problem of product shrinkage, but our company's production practice proves that this is not the case. A refrigerator compressor part produced by our company has occasional shrinkage and porosity in the thick part of the product. We have tried to modify the pouring system to increase the feeding of the product, lower the pouring temperature to reduce the liquid shrinkage of the product, but the effect is not obvious. Try the inoculant containing Sr, the addition amount is 0.25% of the iron trough + 0.15% of the flow, the graphite grade of the product is grade 5, there is no white mouth in the thin-walled parts, but there is still shrinkage in the thick and large parts of the dissection. The number of eutectic clusters in the product is about 200 pieces/mm2, which is indeed less than about 500 pieces/mm2 of SiBaCa, indicating that there is no problem with the inoculant containing Sr. At the same time, it indicates that the effect of the inoculant containing Sr in solving shrinkage is relatively limited, and it is not expected to be too much. high.
3.3 Inoculant containing Ba
The most important role of the Ba-containing inoculant is to slow down the inoculation and decay, and has a strong ability to promote graphitization, which can improve the shape and distribution of graphite in thin-walled castings, thereby reducing the hardness difference between thick and thin parts. The SiBa inoculant with w(Ba) in the range of 20%~30% can significantly reduce the white mouth tendency of cast iron, and the time to maintain the inoculation effect can be increased to about 30 min. It is especially suitable for large castings, but it may cause products when used for small pieces. The amount of pearlite is insufficient. At present, the more widely used inoculant containing Ba with w(Ba) in the range of 2% to 3%, the addition amount is about 0.3%, the iron liquid is basically not decayed within 20 minutes, and its price is only more than 1,000 yuan more expensive than 75SiFe. About one-third of 75SiFe, it is an inoculant worthy of widespread promotion.
3.4 Rare earth compound inoculant
Rare earth inoculants are generally not used alone. They are often combined with Ba and Ca to synthesize a rare earth-Ba-Ca inoculant. On the basis of retaining the advantages of Ba-containing inoculants, it has stronger deoxidizing ability and is particularly effective for high w(S) molten iron . However, the amount of this inoculant should not be too high, otherwise the amount of w (RE residue) in the product is too high, which may cause excessive cooling of the cast iron during crystallization and the appearance of cementite structure. The dosage must be strictly controlled during use, and the maximum dosage should not exceed 0.4%. The price of rare earth inoculants is not too expensive, only slightly higher than the Ba-containing inoculants, and it is an inoculant worth choosing.
4 How to control the quality of purchased inoculants
The quality of inoculants fluctuates during the production process, and suppliers often mix good and poor quality products to us. So how should we control the quality of purchased inoculants?
4.1 Chemical testing
It is possible to preliminarily determine whether the inoculant is qualified by detecting the mass fraction of Si, Al, Ca, Ba, rare earth, etc. in the inoculant, but the detection of these elements is more complicated and takes a long time. Generally, foundries do not have this ability, so , The following method is more practical.
4.2 Visual inspection
Open the bag to check whether the color of the inoculant is normal? Is there too much black slag? Are there too many particles that do not meet the particle size requirements, too coarse or too fine? These problems occur most often, and you must open the bag for inspection after each purchase. Our company once purchased a batch of inoculants and put them into use after the chemical detection elements were qualified. As a result, more than 20 furnaces had white mouth and graphite abnormalities. After inspection, it was found that there was too much black residue in the inoculant and the color of the inoculant was dark.
4.3 On-site trial
After each batch of inoculant arrives at the factory, after the above inspection is qualified, we will also try 3~5 furnaces on site. Through metallographic analysis of the graphite, white mouth, pearlite and other tissues of the product, compare it with the normal production product, and find that the abnormality is immediately Deactivation can avoid batch product scrapping.
4.4 Selection of Suppliers
When choosing a supplier, generally choose a supplier with a larger scale and a certain degree of credibility, so that the quality is more assured. Some suppliers do not have their own smelting furnaces, nor do they have chemical inspection methods for their products. They just buy large chunks of raw materials from others for shredding. Such suppliers have weak quality assurance capabilities.
5 Harm of poor pregnancy or overdose
Poor inoculation will lead to abnormal graphite, white mouths in thin-walled parts, and low mechanical properties. Excessive inoculation will cause coarse graphite, insufficient pearlite, and low mechanical properties. Excessive inoculation is generally easy to occur in the process of technological trial production, but generally does not occur under normal production conditions. In 2006, our company replaced the 75SiFe inoculant with SiBa inoculant. Although the inoculum was reduced from 1.0% to 0.6% during the process test, the customer reported that the thick and thick parts of the product still showed thick graphite after processing, until the inoculum was reduced. The product does not return to normal until 0.4%, which shows that over or under inoculation is different for different inoculants.
Under normal production conditions, poor inoculation will not occur, but when there is a problem with the equipment, especially in the assembly line production process, the process of pouring molten iron with a pouring furnace often has poor inoculation. Because in the event of equipment failure, there is still molten iron that has been conceived but not poured in the pouring furnace. With the extension of the failure time, these molten iron will cause poor gestation due to inoculation. When the amount of molten iron is not too much, we generally adopt the method of adding more inoculants to the lower ladle molten iron to re-inoculate; and if the amount of molten iron is too much, the molten iron in the casting furnace can only be returned to the furnace for processing.
6 Storage and drying of inoculants
The inoculant must be placed in a dry and ventilated place, and the regained inoculant must be dried before use. Every year from March to May, it is the rainy season in the south. The more ventilated the air, the more humid the air. Therefore, you must be more careful when using inoculants in this season. The inoculant added to the iron tapping tank or transfer bag does not need to be dried. Just put the inoculant in the iron tapping tank or transfer bag a few minutes before ironing, and use the residual heat to dry the inoculant. Special attention is paid to , Do not add the inoculant into the transfer bag too early, otherwise the inoculant may be oxidized or stick to the bottom of the bag, which will affect the inoculation effect. The flow inoculation device and the pouring machine are together, and the flow inoculant can be placed on the stove of the pouring machine to dry naturally for 1~2 h every day, and then added to the flow inoculation device. Generally, special drying is not required. Some factories use compressed air to drive the flow inoculant, so we must pay attention to the dryness of the compressed air, otherwise, the moisture of the compressed air may affect the inoculation.
7 concluding remarks
The inoculation of gray cast iron plays a vital role in product quality. Therefore, the type of inoculant must be carefully selected, and special attention must be paid to the method of use. The inoculation should be placed as far as possible to increase the inoculation effect, reduce the amount of inoculant, and stabilize product quality.
Please keep the source and address of this article for reprinting:The Improvement Of Current Shell Making Process In Investment Casting
Minghe Die Casting Company are dedicated to manufacture and provide quality and high performance Casting Parts(metal die casting parts range mainly include Thin-Wall Die Casting,Hot Chamber Die Casting,Cold Chamber Die Casting),Round Service(Die Casting Service,Cnc Machining,Mold Making,Surface Treatment).Any custom Aluminum die casting, magnesium or Zamak/zinc die casting and other castings requirements are welcome to contact us.
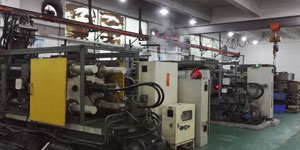
Under the control of ISO9001 and TS 16949,All processes are carried out through hundreds of advanced die casting machines, 5-axis machines, and other facilities, ranging from blasters to Ultra Sonic washing machines.Minghe not only has advanced equipment but also have professional team of experienced engineers,operators and inspectors to make the customer’s design come true.
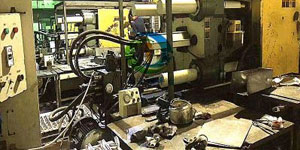
Contract manufacturer of die castings. Capabilities include cold chamber aluminum die casting parts from 0.15 lbs. to 6 lbs., quick change set up, and machining. Value-added services include polishing, vibrating, deburring, shot blasting, painting, plating, coating, assembly, and tooling. Materials worked with include alloys such as 360, 380, 383, and 413.
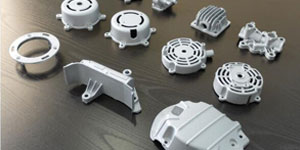
Zinc die casting design assistance/concurrent engineering services. Custom manufacturer of precision zinc die castings. Miniature castings, high pressure die castings, multi-slide mold castings, conventional mold castings, unit die and independent die castings and cavity sealed castings can be manufactured. Castings can be manufactured in lengths and widths up to 24 in. in +/-0.0005 in. tolerance.
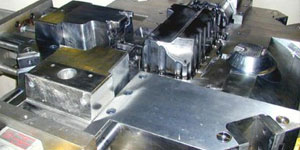
ISO 9001: 2015 certified manufacturer of die cast magnesium, Capabilities include high-pressure magnesium die casting up to 200 ton hot chamber & 3000 ton cold chamber, tooling design, polishing, molding, machining, powder & liquid painting, full QA with CMM capabilities, assembly, packaging & delivery.
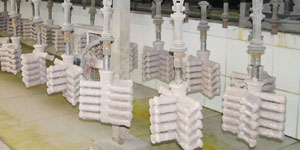
ITAF16949 certified. Additional Casting Service Include investment casting,sand casting,Gravity Casting, Lost Foam Casting,Centrifugal Casting,Vacuum Casting,Permanent Mold Casting,.Capabilities include EDI, engineering assistance, solid modeling and secondary processing.
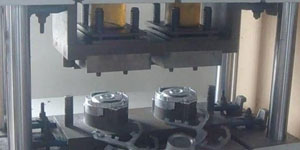
Casting Industries Parts Case Studies for: Cars, Bikes, Aircraft, Musical instruments, Watercraft, Optical devices, Sensors, Models, Electronic devices, Enclosures, Clocks, Machinery, Engines, Furniture, Jewelry, Jigs, Telecom, Lighting, Medical devices, Photographic devices, Robots, Sculptures, Sound equipment, Sporting equipment, Tooling, Toys and more.
What Can we help you do next?
∇ Go To Homepage For Die Casting China
→Casting Parts-Find out what we have done.
→Ralated Tips About Die Casting Services
By Minghe Die Casting Manufacturer |Categories: Helpful Articles |Material Tags: Aluminum Casting, Zinc Casting, Magnesium Casting, Titanium Casting, Stainless Steel Casting, Brass Casting,Bronze Casting,Casting Video,Company History,Aluminum Die Casting |Comments Off